The struggle to repopulate Australia’s damaged coral reefs with new growth is too great for manual work alone. Stephen Holmes speaks to the team at Coral Maker about how it is using product development and manufacturing know-how to scale up the fight
The millennia it takes to form a natural wonder are thrown into sharp focus when huge swathes of it can be damaged or destroyed in only a few weeks.
This is sadly true of Australia’s Great Barrier Reef, where elevated sea water temperatures are causing unprecedented damage, including mass coral bleaching events like the one that killed between 30% and 50% of the reef’s coral in 2016 and 2017.
Bleaching occurs when environmental stressors, even a water temperature rise of just 1°C, cause corals to expel symbiotic algae living inside them, turning the corals white and often killing them.
Over the last 30 years, mass bleaching events have grown in frequency and severity, leaving biologists battling to restore coral and save their delicate ecosystems.
One method is transplanting coral from existing colonies, but it can take as long as 10 years for them to grow their own adult-sized skeletons, requiring a huge amount of manual tending and cultivating.
Seeking a better means of repopulating the reefs, Australian coral biologist Dr Taryn Foster has developed a new, large-scale method that uses the latest digital tools in conjunction with traditional masonry manufacturing.
Leaning on knowledge gained from her family’s business, which makes masonry products for the construction industry, Foster founded the company Coral Maker, in order to scale restoration efforts in the same way as you might scale manufacturing.
Coral Maker’s method aims to speed up restoration by mass producing new limestone skeletons and grafting live coral onto them. When deployed in the ocean, the groupings of coral on the structure join up and fuse, coating the manufactured skeletons much faster and giving them the potential to reach adult size within 12-18 months.
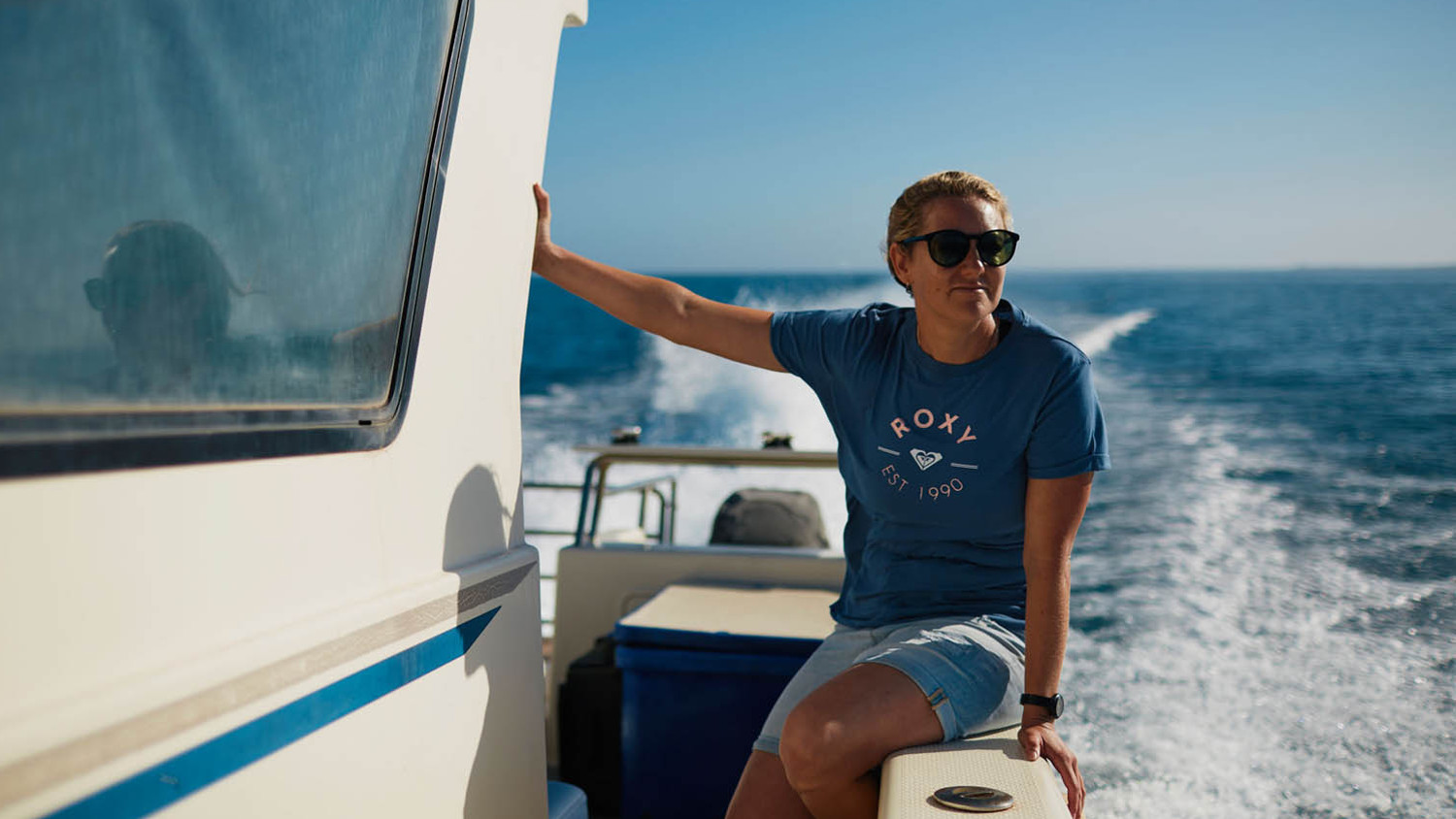
Pro bono support
Work on this method began while Foster was working at the California Academy of Sciences on a Fulbright Fellowship. With Coral Maker founded, Foster joined the Autodesk Technology Centers Outsight Network residency.
Through pro bono support from the Autodesk Foundation, Autodesk employees located across North America and the UK assisted Coral Maker on the design, engineering, advanced manufacturing and robotic automation capabilities needed to help scale production.
“Taryn comes up with these great ideas and she sketches them down, but she doesn’t know how to translate that sketch into a physical product. And that’s kind of where we came in,” says Rob Bowerman, an Autodesk principal technology consultant based in its Technology Centre in Birmingham, UK.
“We would use Fusion 360 to turn that sketch into a physical model, and then as soon as we have that physical model, she could get a real feel for what that would look like, how that would work, how she would interact with that in the water, how the seeding would work, and how we could use things like robotics to automate the seeding and assembly of the skeletons.”
With the global Covid pandemic forcing Foster to leave San Francisco and return to Australia, the team was forced to work across multiple time zones. “It was almost impossible for us all to be on a call at one point, so throughout this whole project, we’ve had to collaborate remotely,” says Bowerman.
“Fusion has been amazing for that, because it’s enabled us to have this one location where we can all work on the same design data. We can all have input to the same design, but we can also have a design up on screen, we can all be commenting on it, we can be saying we want things to be changed, we can do those changes in real time and get Taryn’s feedback straight away.”
If the whole team can’t be in a meeting at the same time, he adds, “we can make some changes, she can then see the changes have happened, review the design, make comments and we can come back to it at a later date.”
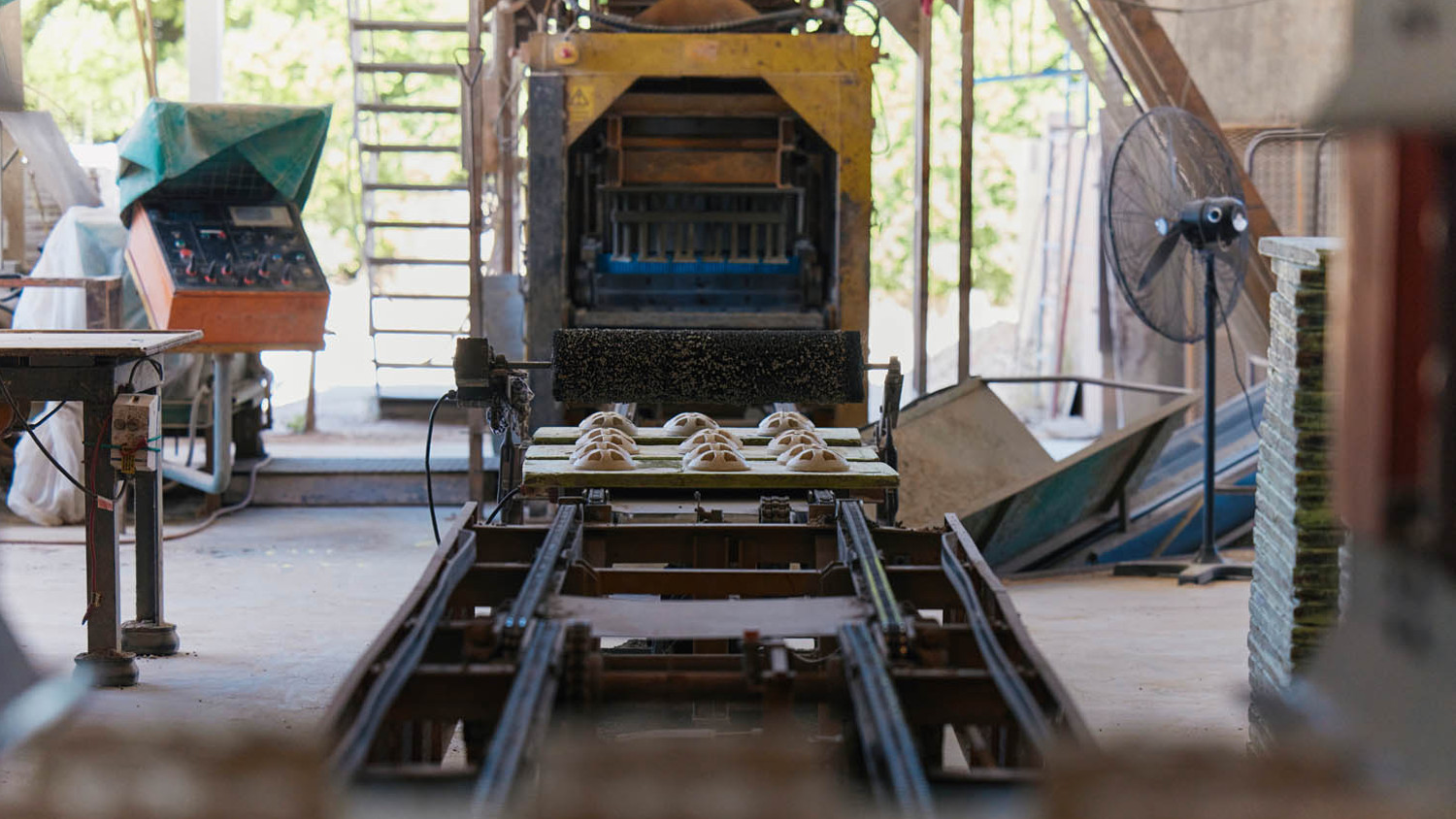
Accelerated growth
The dome-shaped skeleton, with square sockets in which to dock coral seed plugs, appears quite simple, but a lot of design iteration has gone into devising this optimal shape.
A key factor is that it enables coral to reach its adult size faster, by providing the foundation layer for the coral to start growing on. Furthermore, this skeleton can be quickly and cheaply produced using masonry manufacturing.
“It’s a process that is robust. It’s fairly crude in its method, but it’s certainly able to give us the rate that would be needed to try and solve this problem,” says Bowerman.
Initial prototypes could be shared as files to be 3D printed, allowing the Australian team to test them for size and handling them underwater. Once the form had been tested, back in Birmingham, the team began to cut the tools for mass producing the skeleton using its array of 5-axis CNC machines.
Bowerman explains that the UK team is not only making prototypes, but also proving out the manufacturing process, so that when the skeletons go into production, the design can be given to a local manufacturer and it’s ready to go.
“We know there are no kinks in it, and we can even get to the point where we have the code that can run on that local manufacturer’s machine, so we know that they’re going to get a like-for-like part of what’s already been tested over here in the UK. We’re nurturing and incubating that technology here, and then we can deploy it to wherever she is locally.”
With the volumes of coral needing to be seeded already daunting, and with ocean temperatures continuing to rise, local production to ensure successful deployment of new coral will be key. As water temperatures continue to change, reef regeneration may need to be relocated from the tropics to cooler high latitude ‘fringe’ reefs. To accomplish that effectively, reef restoration needs to be mobilised as a bigger, more organised effort.
While the versatility of the design allows skeletons to be built using local aggregates, or in different shapes to better aid different species of coral, the need for millions or potentially tens of millions of structures per year has seen the team having to look further at the manufacturing process.
To overcome the challenge, Coral Maker wants to automate coral propagation using robotics and artificial intelligence for onsite deployment, with capabilities able to work collaboratively with humans and also freeing them up to do more complex work.
With many other ecological challenges to be tackled, the technology that allows designers and engineers around the world to work together to develop solutions at scale might just be the seed that helps nature regenerate elsewhere.
This article first appeared in DEVELOP3D Magazine
DEVELOP3D is a publication dedicated to product design + development, from concept to manufacture and the technologies behind it all.
To receive the physical publication or digital issue free, as well as exclusive news and offers, subscribe to DEVELOP3D Magazine here