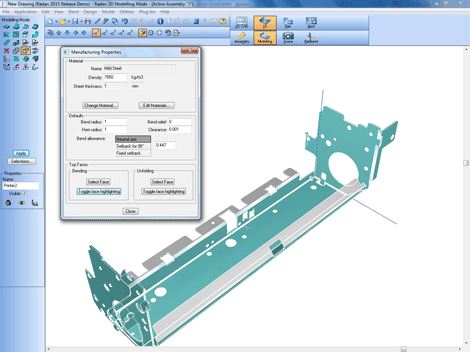
The latest edition of Vero Radan pushes on from being merely a sheet-metal CAM tool, with enhancements linking all its connected product
On a lonely winter’s night it must be hard sitting at the end of the bar with the rest of the pub’s regulars looking knowingly across at you, noting you as a one-trick pony.
As they stare at the solitary figure on his stool, they don’t know about your Grade 7 bassoon-playing ability, or your collection of lesser known Swiss postage stamps. This is, in a pseudo-psychiatry sense, how Vero’s Raydan software has been feeling: known simply as ‘that product for fixing up sheet-metal parts’. Until now.
The latest release of Radan includes additional functionality, ramping up 180 enhancements to bring all aspects of the software together – including its CAD/CAM, Radbend, Radm-ax, Radtube and logistics products.
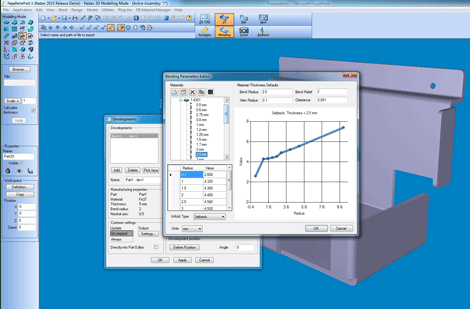
A new editor in the Unfolding Dialog tool supports bend parameters by simply sliding points on the graph to adjust the values
“When people think of Radan they think of the world’s most powerful sheetmetal CAD/CAM software, but Radan is actually a whole suite of connected products,” says product manager Olaf Körner, slapping his money down at the bar before telling everyone the equivalent of a hilarious anecdote about the time Radan ended up trapped in a lift with three nuns and a penguin.
“For example, there is a major connection between 3D in CAD/CAM and the Radbend press brake software. When manufacturers unfold a model they need to know how the bend process will be affected further down the production line.”
This is aided by an important update in Radan 2015 – strengthened 3D translation procedures, which Körner says, imports information more consistently.
The routines for automatically calculating the thickness of imported parts have also been redesigned giving faster and more accurate results. Automatic face selection now applies to unfolding, and there is a simple way to manually specify the top face much earlier in the process.
“Telling Radbend at the 3D stage which is the protected face ensures the visible face of the part is scratch-free.”
There’s a new editor in the Unfolding Dialog tool to support bend parameters by simply sliding points on the graph to adjust the values. For nesting near-rectangular parts, the user can select the true-shape option and the nester will automatically apply rectangular nesting where appropriate, ensuring a more compact nest than before, including compensating for centrifugal placement – the technique of placing parts as far removed as possible from the centre of the sheet.
New machine automation functions have been built into the software, including significant enhancements to part removal, continues Körner: “Considerable work has gone into ensuring that Radan understands the loading and removal process and what the machine is capable of.
“As well as calculating the sucker lift, we must be sure the part won’t bend and hit the machine while it’s being moved to its storage area.”
As well as a new option to use a link from Radbend to Radan 3D to create a heel tool by using the 3D boolean operations on the tool profile and heel profile, Radbend has been strengthened in its control of the hemming process, by specifying the central face as being either above or below, and in the logistics of the press brake operations.
“For example, there is now the option of re-using tool set-ups if the same type of part could share the same setup, minimising tool changes,” concludes Körner. “Users now have more control over Radbend, enabling them to change a number of settings early in the process.”
By the time Radan left the pub that night everyone was enraptured by its many skills nobody had previously known about.