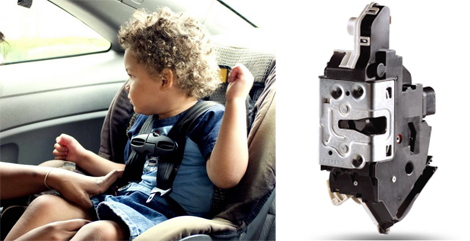
For Kiekert, designing a car child lock benefits from CAE
Designing, developing and manufacturing custom locking systems for over 150 years, Kiekert knows a thing or two about what makes car doors click.
Producing side-door latches, latch modules, rear compartment and hood latches and a broad range of actuators for side doors, sliding doors, decklids and various interiors solutions… the list goes on, but few are as important as its child safety locks that are built into the rear car doors.
When the child safety lock is engaged, the rear doors can only be opened from the outside. On newer models, this safety lock is activated or deactivated electronically utilising a small motor within the side door latch by a switch, typically located near the driver’s side door lock switch.
The side door latch is a complex system consisting of cables, cams, leverages, couplings, actuators, gears, pawls and catches. The side door latch secures the door by activating the catch and pawl so that they clamp around the striker, which is a u-shaped part that is secured to the C-pillar.
The child safety lock is just one of multiple functions that must be performed by a side door latch including; lasting the life of the vehicle, operating at a wide range of temperatures, meeting noise and vibration requirements and maintaining the integrity of the lock in the event of a crash.
In the past, Kiekert engineers used manual methods including kinematics analysis and engineering handbook formulas to produce the initial design for side door latch mechanisms.
Kinematics analysis is limited by the fact that it does not take the dynamic characteristics of the mechanism into account while handbook formulas are not capable of addressing the specific geometry of the mechanism. For these reasons, the initial mechanism design iteration usually did not meet the design requirements.
Engineers built and tested the initial design, and based on the test results, they iterated the design and built a new prototype.
The considerable expense and lead time involved in each prototyping iteration drove up the time and cost involved in designing a new latch. It took from six to 18 months to design a latch mechanism using the build and test method.
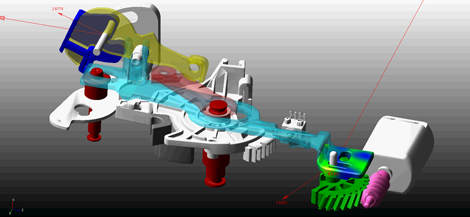
Parameters such as gears in the mechanism could be defined in Adams by selecting the gear type, location, gear ratio, materials and connections
To speed up this process Kiekert has recently implemented virtual prototyping capability, a key aspect of which being the virtual validation process to accurately simulate the performance of a mechanism including both its kinematic and dynamic characteristics while taking the full geometry of the mechanism into account.
Darius Schendzielorz, Kiekert’s simulation engineer, started by importing the initial design concept from Catia into Adams for simulation, defining the gears, bearings and electrical motor in the child lock by entering parameters.
For example, he defined the gears in the mechanism by selecting the gear type, location, gear ratio, materials, connections, and other parameters.
It was critical to accurately model the behavior of the plastic levers. With the new Adams option to create flexible bodies from solids within Adams View, Darius Schendzielorz created modal neutral files (MNF) for the aforementioned levers. The modal neutral files contain information such as the inertia matrix, the mode shapes and modal frequencies.
Stelian Borlodan, project engineer for simulation and FEA, then simulated the performance of the child safety lock mechanism under the complete range of design conditions.
Performance at different temperatures, loading in a hypothetical crash, and evaluated impact of manufacturing variation on mechanism performance were all assessed.
The simulation was used to size the electric motor used to drive the child safety lock mechanism, using an animation to help diagnose issues with the mechanism and helping engineers iterate a design that met all requirements.
Using multibody dynamics simulation, Kiekert engineers dramatically reduced the time required to design the child safety lock mechanism to only about three weeks, meaning a full new latch can be brought to market in less than 18 months.