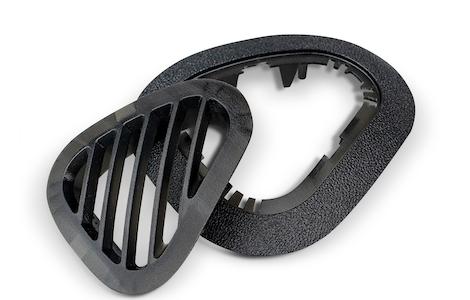
It wasn’t until we saw a Figure4 3D printer out in the wild – in the labs of Imperial College London, more on that at a later date – that we realised just what it is actually capable of, so it’s impressive to see 3D Systems launching another five materials for the machine.
Skipping the jargon about it ‘replacing injection moulding’, the printer itself is super fast, and the output is incredibly detailed (think threading and internal structures) and quick to post process, and now it has a range of materials that make it a better value option – all led by tough Pro-Blk 10.
3D Systems explains the following four materials as follows:
– Figure 4 EGGSHELL-AMB 10: A process-optimized material for the production of sacrificial tooling for casting true silicone components
-Figure 4 HI TEMP 300-AMB: Industry-leading, ultra-high temperature (300 Celsius) rigid plastic suitable for production applications such as high temperature component testing and stators and motor enclosures
– Figure 4 FLEX-BLK 20: Durable, flexible, high impact, fatigue resistant material with long term environmental stability for functional assemblies and prototypes such as automotive styling parts, consumer goods and electronic components, snap-fit assemblies, containers and enclosures
– Figure 4 RUBBER-BLK 10: High-tear strength, malleable, low durometer material for hard rubber-like parts designed for prototyping hard, rubber-like parts such as hoses and tubes
“Through collaboration with its customers, 3D Systems continues to innovate, and rethink manufacturing,” said Menno Ellis, senior VP and GM, Plastics, 3D Systems. “The release of our newest Figure 4 materials enables production of parts through additive across the entire product development and production value chain.”