The SmartPlate, newly announced by Fabrisonic, allows for the analysis of individual ‘pixels’ for sudden vector changes, which can provide tell-tale signs of many build issues, while also comparing time histories of adjacent pixels also highlights problems in the build.
Fabrisonic LLC is a manufacturing technology company most widely known for its Ultrasonic Additive Manufacturing (UAM) process, and although the SmartPlate was built with the help from the UAM technology, it has been designed to be retrofitted to existing metals 3D printers for other technologies.
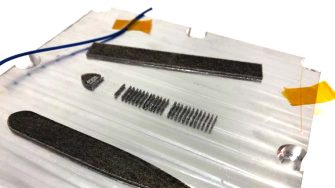
Key to the abilities is the way the SmartPlate is produced. Fabrisonic starts with a billet build plate and mills channels in locations where sensors are to be embedded. Sensors are placed in the milled cavities, and UAM is used to print solid metal over the sensor. The low-temperature process does not harm the sensors; thus, the metal has continuous, contiguous, and direct contact with these sensors.
When the product is completed, the end part has a fully consolidated metal plate with integral sensors buried within it.
The SmartPlate announced by Fabrisonic has optical strain gauges and thermal sensors built into the metal, with an demonstration build plate used on a Powder Bed Fusion (PBF) 3D printer, which allowed for the simultaneous recording of strain/time and temperature/time data.
A PBF build that included highly problematic features was tested, with Fabrisonic stating that the SmartPlate picked up significantly more information from this initial build than the bulk stress state. Among some of the additional data uncovered was the resolution and scan rate was high enough to discern the scan strategy of each layer; defects appeared as large compressive strains that formed early in the build at localised points, and low delamination of a specific feature was seen in the data even though the recoater blade never hit the build.
Fabrisonic CEO Mark Norfolk, said that the design came out of a proposal from one of Fabrisonic’s close collaborators at EWI, an Ohio based 501c(3) research organisation, who wanted to measure the loads going through the build plate during an AM process. “Fabrisonic had built a reservoir of knowledge in embedding sensors and was working on embedding strain sensors in aerospace parts,” said Norfolk.
“We suggested we build a build plate using our UAM 3D printing technology and incorporating embedded sensors. Fabrisonic proposed collaborating with EWI (PBF research) and Luna Innovations (Fiber Optic Sensors) to design and build an instrumented PBF build plate. The challenge was accepted and then solved!”
The research into the product continues, with the team recently upgrading an EOS M290 with a SmartPlate by adding various sensors, including thermocouples and vibration sensors to allow further investigations for quality monitoring.