MakerBot is capable of 3D printing steel, as its Method 3D Printers now support BASF Forward AM Ultrafuse 316L Stainless Steel Composite material, letting users produce lightweight, hollow metal parts with high tensile strengths.
The 316L stainless steel parts require the second generation MakerBot LABS Experimental Extruder, and once the part is 3D printed on the MakerBot Method with BASF Forward AM Ultrafuse 316L, it requires debinding and sintering, which turns the part printed with the composite material into solid stainless steel.
MakerBot is targeting the process at designers looking to produce parts in stainless steel without investing in expensive in-house debinding and sintering equipment – instead allowing them to send these parts out to local service bureau for quick turnaround.
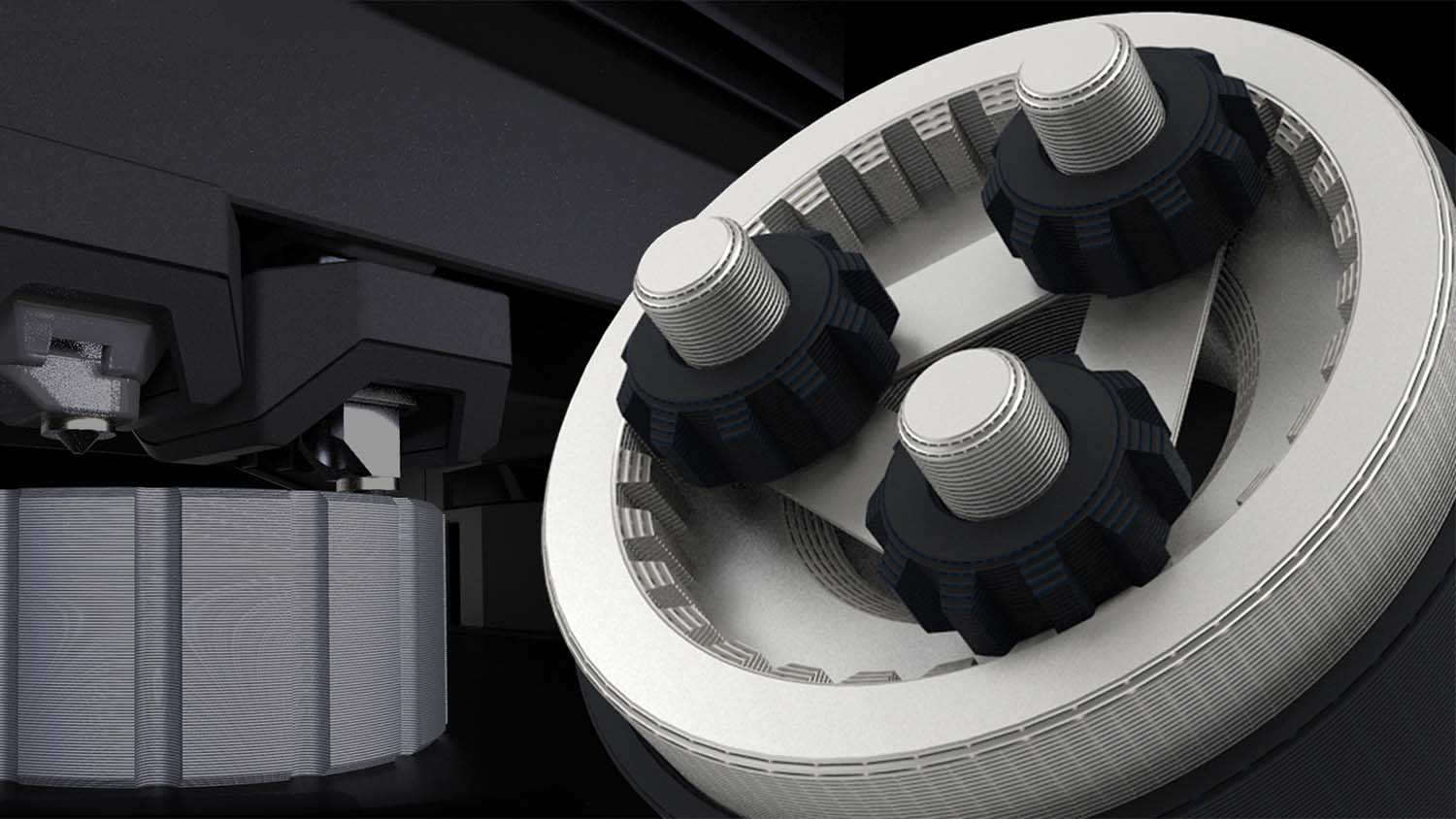
MakerBot states that the final parts can achieve up to 96 per cent of the density of pure 316L metal material, and highlights the 3D printer’s heated chamber and ability to control the speed at which a part cools down during the printing process as a benefit for reduce the risk of delamination.
“Ultrafuse Metal Filaments removed the barriers between metal 3D printing and users to make the technology more accessible to a larger audience,” said Firat Hizal, head of metal systems group, BASF 3D Printing Solutions.
“We are very excited to have our Ultrafuse 316L part of the MakerBot LABS program. We aim to add our recently launched Ultrafuse 17-4 PH filament, with the Ultrafuse 316L to make our entire portfolio accessible to MakerBot users.”
The MakerBot Method range has quickly grown since its launch in 2019, with the company targeting professional users with specific tasks including a specialist carbon fibre edition.