Using a simulation-led design for additive manufacturing workflow and advanced multi-laser metal 3D printing technology, Airbus is achieving 75% lightweighting, multi-part consolidation and precise geometric tolerances. Stephen Holmes speaks to the team behind hefty changes that add up to lighter designs
The team at Airbus Operations set out to redesign the fuel air separator for the company’s A330 aircraft with a good idea of all the benefits that additive manufacturing might bring to their work. They knew that the technology could be used to lightweight the part, consolidating many connecting parts within the system, and that it would enable them to make that part in a way that could be qualified to fly. All the same, they weren’t fully prepared for the striking results that they actually achieved.
The fuel air separator is a large and complex component, which removes air from the auxiliary power unit (APU) fuel feed system, ensuring that the APU can power essential aircraft systems when the main engines are off.
Typically, this part is fabricated from more than 30 individual components that require manual welding and assembly. This makes for a labour-intensive production process, as well as being prone to supply chain challenges.
However, the higher-level objective for redesigning the air separator in a prototyping project was to reduce CO2 emissions over the lifespan of an aircraft. Weighing in at 35kg, a typical system also requires a substantial mounting rack that adds further weight to the aircraft.
So it was a cause for considerable celebration that the system was able to be consolidated as a single part weighing less than 8.8kg – some 75% lighter than the original.
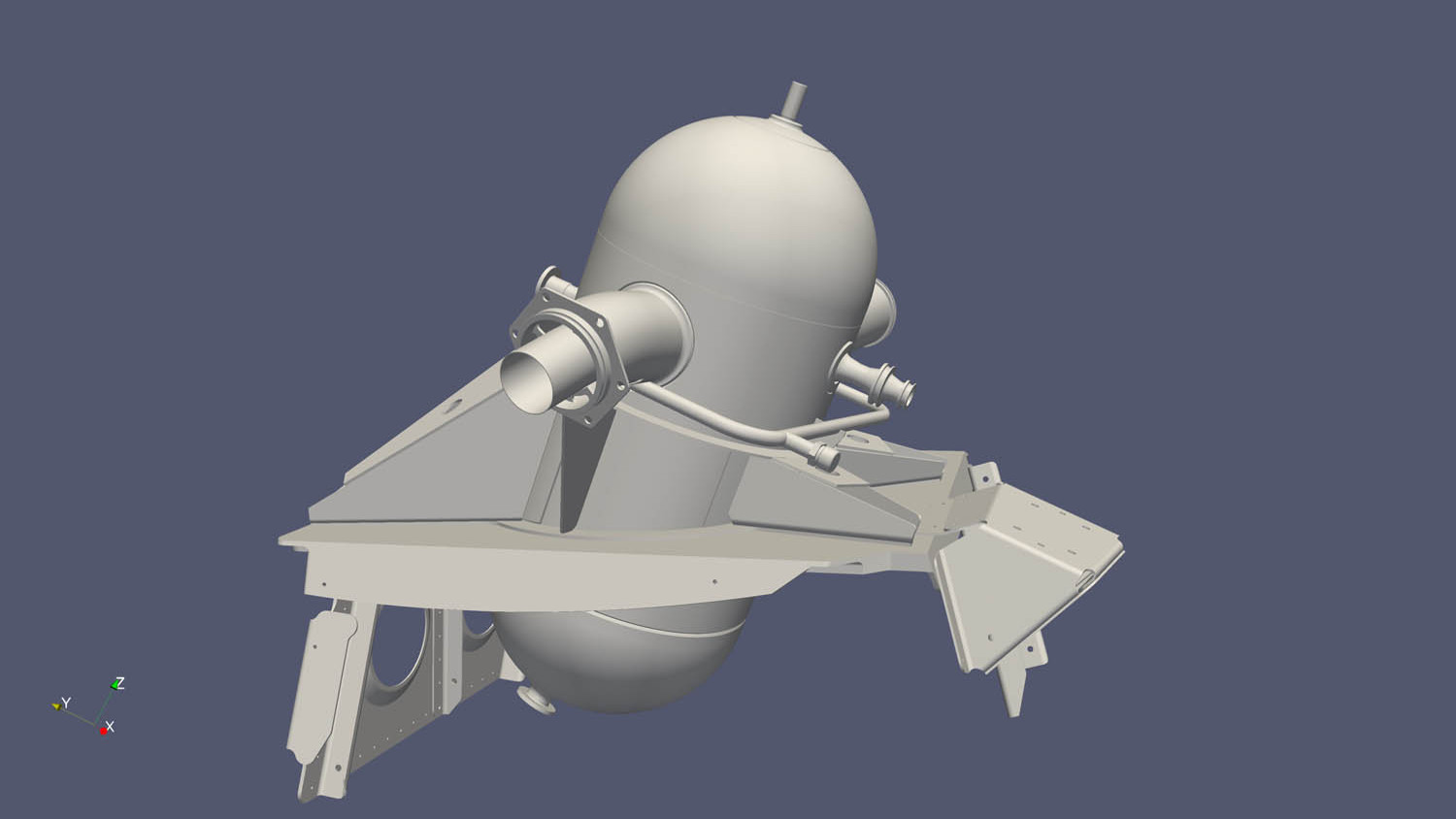
Big metal, fine margins
The new fuel air separator was built on the Nikon NXG XII 600 3D printer, a large metals SLS system boasting 12 lasers and a build area of 600 x 600 x 600mm, and capable of building the new design in 68 hours.
While still a lengthy process, which also requires several hours of post-processing and heat treatments, this method still beats the conventional approach hands-down.
“In terms of cost, we don’t have a very precise breakdown, but expect it to be cost-competitive as well, due to the complexity of the original design and the work in assembly,” adds Mathieu Pérennou, global director of additive manufacturing solutions at Hexagon’s Manufacturing Intelligence division.
Tackling a part of such scale and complexity was not straightforward. In fact, without advances in software from project partner Hexagon, the air separator could not have come close to the tolerances required.
The consolidation of elements and lightweighting of the overall form utilises topology optimisation within Hexagon Apex Generative Design, but that is only the first step.
Key to this project was developing a process to mitigate all the manufacturing risk, given that physical builds on large-scale metals 3D printing systems are costly in terms of time, resources and money.
The build process for aligning the part on the Nikon NXG XII 600 3D printer was quickly derived using Hexagon AM Studio. After that, the risk-reduction work really began, with in-depth process simulation taking into account all factors relating to the machine and the materials used.
Process simulation is used for two things, explains Perennou. First, it’s used to mitigate manufacturing issues – risks like recoater interference, supports separating, or cracks appearing due to the stress levels in the build. But once you can simulate a process with no manufacturing problems, you still need to consider the impact this simulation will have on the shape of the part.
“With titanium especially, you’re going to have distortions,” he says. “There are going to be shrinkage distortions. And then the next step is to use simulation to try to make a part within tolerance.”
Using Hexagon Simufact Additive, the team was able to virtually print the part and compare this model to the nominal, determine the differences between the two, and then morph the nominal into a distortion compensation model that, when printed, builds a part within tolerances.
Yet for large, complex aerospace parts with tight tolerances like the fuel air separator, simulation results can still lead to real-world headaches.
To take this a step further, Hexagon has developed an advanced compensation module for an approach Perennou calls ‘second time right’. Here, a simulation gets you very close to the end result. You print that first part and then 3D scan it, allowing you to compare that data capture to your nominal once more, showing you where the differences lie.
The 3D data capture measurements can be added into Simufact, compensating the printable mesh based on the measured deviations from an optical or CT scan and address localised distortions for more accurate compensation.
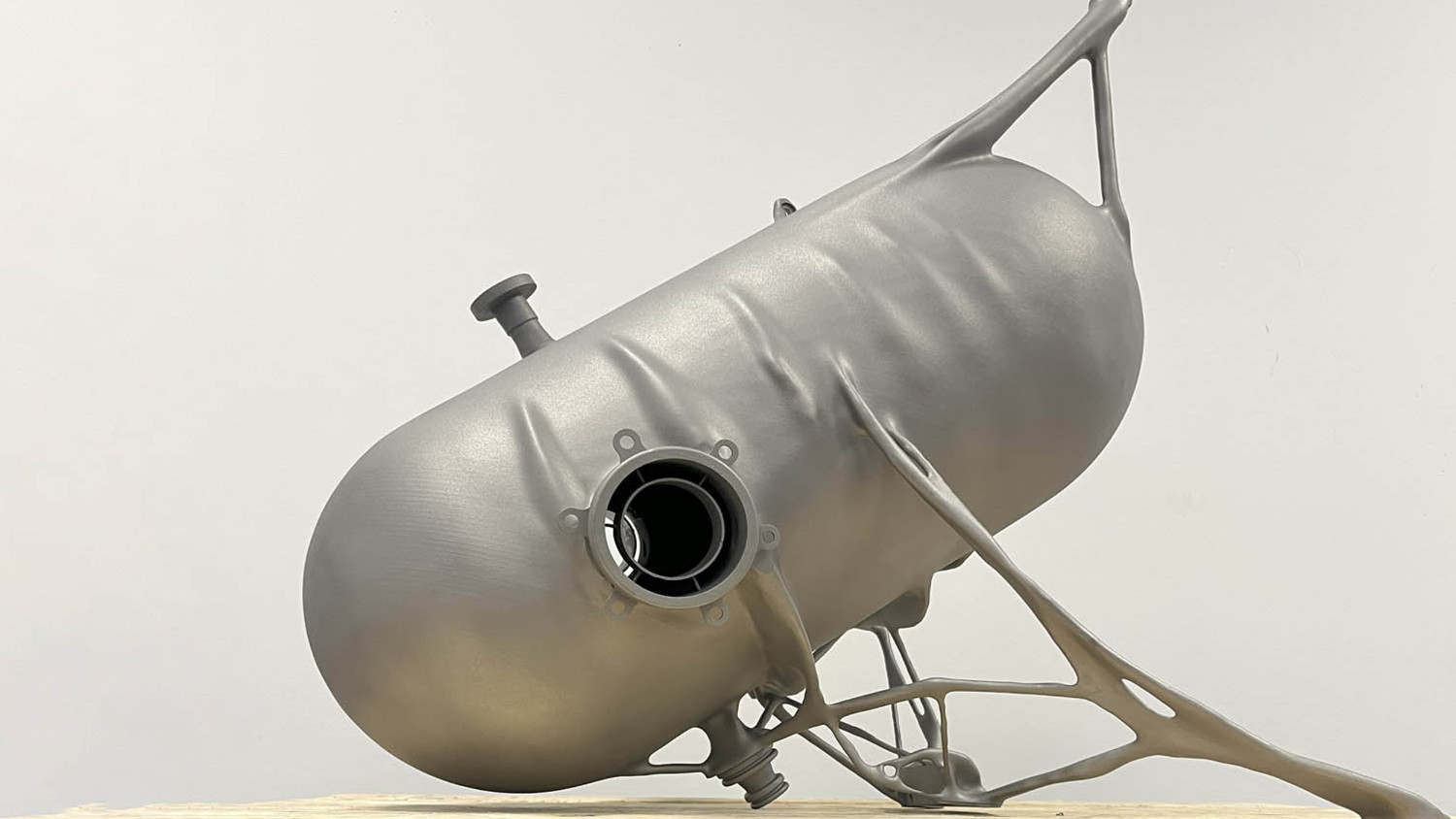
The edge of accuracy
With parts like the air separator, you’re starting to approach the edge of accuracy in terms of what simulation can achieve, says Perennou. So, you’re probably better off just printing the first part and compensating it based on its measurements.
“This hybrid approach – using the two-step approach that we’re talking about – is used in cases where you have a complex geometry that distorts a lot, and you have tight tolerances.”
Simulation alone might mean 90% of the geometry meets tolerances, but there remains a lot of trial and error to define that last 10% by tuning it via multiple physical builds.
Hexagon executives say the company is enabling this by using elements from its VG Studio Max product – better known for CT scan analysis and adding them into Simufact, making it more forgiving of gaps in scan data and letting Simufact Additive users perform metrologybased compensation with whatever data capture technology they have to hand.
“The idea is really to reduce the [physical] iterations as much as possible,” explains Perennou. Because of this new process, some Hexagon aerospace customers are taking on projects that might otherwise be deemed too risky and too expensive, with too many builds needing to be scrapped.

The next level is Hexagon’s drive to define macro scale elements of additive parts in Simufact, by looking at the quality of the part from a material standpoint and simulating potential defects – what Perennou calls ‘ virtual CT scanning’ – to fi nd where porosities and defects in a part might arise.
Having defined all the process parameters for machine and materials in Simufact, users are presented with a ‘heat map’ that flags up any potential cure risks that could cause porosity.
While your initial process model could be within the right parameters, factors like heat building up over a build lasting several days means that errors could arise. Perennou explains that Simufact Additive constantly calculates parameters during the simulation, adjusting it to the thermal conditions of the path when it’s being printed, showing where the failures might occur.
“Here, we do it layer by layer, and then you can really see the scanning patterns, how the temperature evolves and the kind of results you can get.” This ability bleeds into another area of Hexagon’s expertise: quality assurance.
“Sometimes you don’t have all the freedom you want,” adds Perennou. “So at least you know where there is a risk of defects. You know where you want to scan your part, so you can save time in the quality inspection process, by not having to scan a complete part.”
With the ability to inspect CT Scans of parts in Hexagon VG Studio Max, users can complete the loop to verify their simulation data with that of the end part – feeding any further tweaks back into the process.
By taking away the guesswork and diving deep into the details before a part has even been sent to a 3D printer, Hexagon hopes that this de-risking of the process will allow more ambitious projects to see the light of day.
In industries such as aerospace, having processes defined in such detail early on will mean more pioneering builds like Airbus’ air separator, enabling more qualified and sustainable parts to take off.
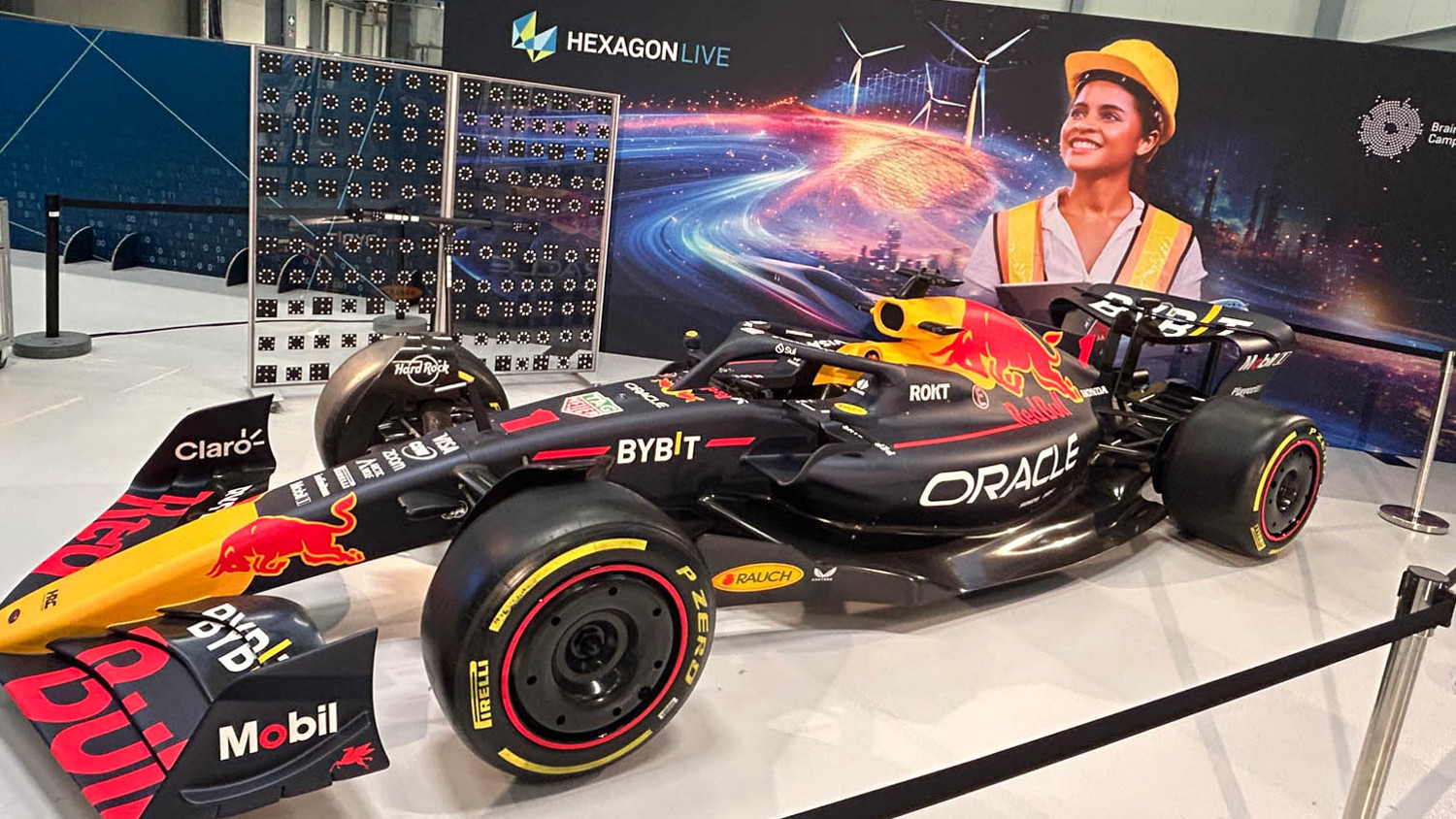
New campus, new opportunities
Emilie Eisenberg attended Hexagon Live: Manufacturing Intelligence in Eindhoven, Netherlands, to witness the opening of Hexagon’s new Experience Centre and learn how the company plans to continue successfully collaborating with customers.
At the opening of its new Experience Centre at the Brainport Industries Campus in Eindhoven, Hexagon ceded the floor to customers from a wide range of industries.
A number of speakers from Hexagon also highlighted how the company’s recent successes in a number of different sectors have led to the opening of the Experience Centre and means that its collaborations with several major brands will continue to flourish.
Hexagon’s vice president and president of the EMEA region Stephen Chadwick highlighted current trends in manufacturing, including those taking place at new aerospace start-ups. He also stressed the role that additive manufacturing is playing as an essential part of many workflows, especially when it comes to electrification in vehicles.
Traditional barriers between manufacturers are breaking down, he said, with electronics companies manufacturing electric cars, for example. Companies using Hexagon’s digital twin model, he claimed, are able to stay ahead of the curve by shortening the time to market from years down to months.
Hexagon’s interpretation of the digital twin concept is not a CAD file or a simulation, but a set of information and data that allow engineers and product designers to digitise and simulate components. The result is that they can better predict how a product’s manufacturing process and lifespan is likely to play out.
Stephen Graham, executive vice president and general manager of Nexus, Hexagon’s open digital reality platform, spoke on the importance of cloud-based collaboration between engineers. Nexus is currently available for Hexagon customers, and there are plans to expand it as a purchasable add-on. It can link an unlimited number of different software platforms together, including those from third parties, as well as from Hexagon.
Nexus offers real-time visual collaboration between both engineering and manufacturing, and customer and supplier. In particular, it is a powerful tool for linking the platforms used by different generations of engineers.
After all, recently graduated engineers may prefer to use different software platforms from their colleagues who have been working for several decades on another platform.
Introducing artificial intelligence (AI) into Nexus means that it can learn from data derived from multiple databases, making it possible to automate machines on the shop floor, which Graham anticipates will save 75% more time.
Despite the concerns some designers have about AI, Graham is confident that the technology should be viewed as just another update to software, rather than a radical change.
Nexus is a project developed in partnership with Microsoft Azure, and uses Microsoft’s data centres. “It was Microsoft who coined the phrase ‘copilot’ for its AI large language model (LLM), and it is just that – a co-pilot,” said Graham.
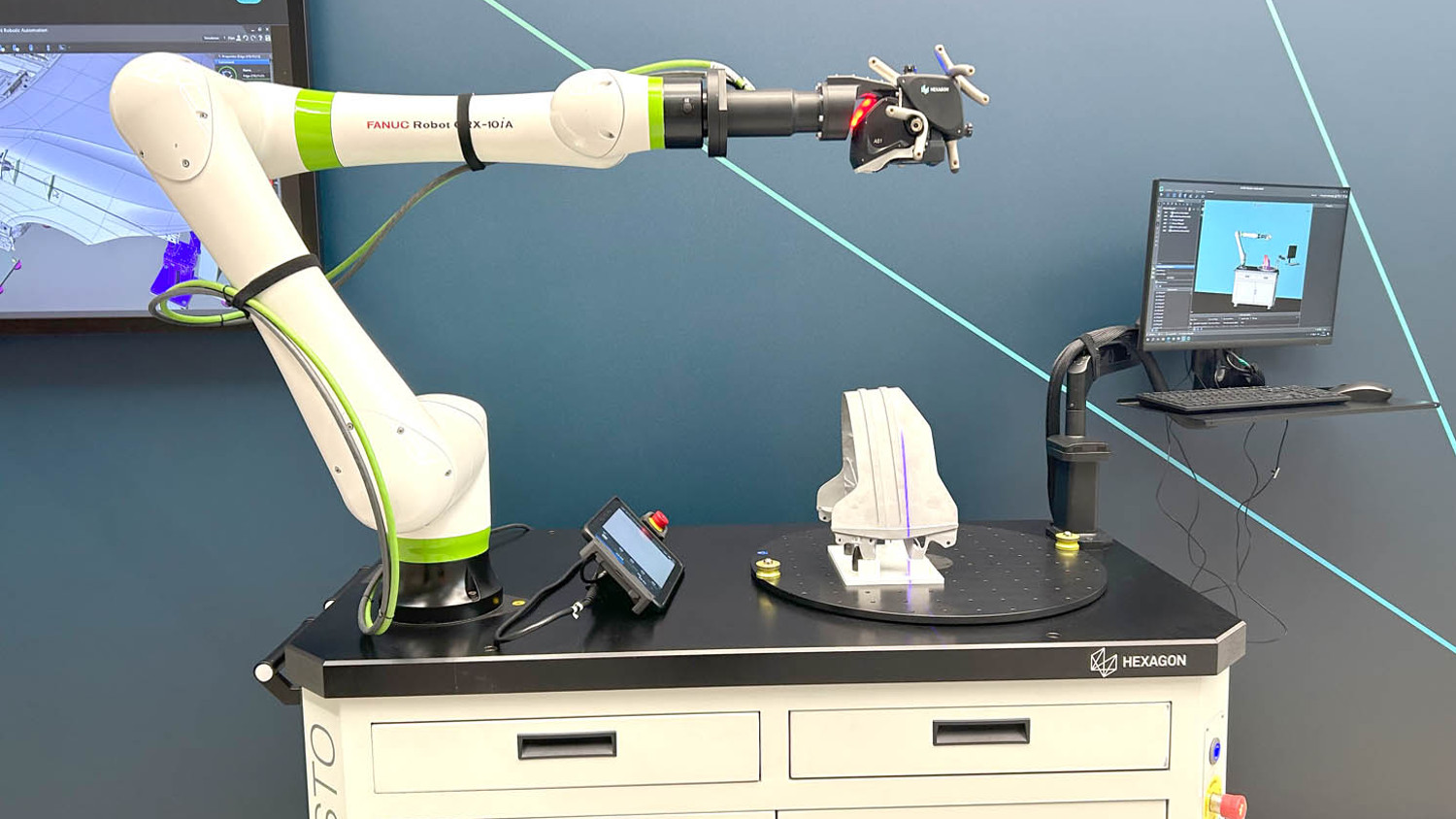
Rainforest revolution
Erik Josefsson, president of R-Evolution, demonstrated how Hexagon’s 3D scanners – typically used in the automotive and aerospace industries, among others – can be used for environmental purposes and in the important work of saving the planet.
R-Evolution has scanned 125 million cubic metres of rainforest, including the La Gamba biological corridor in Central America, using Hexagon’s Leica CountryMapper Hybrid Airborne Sensor alongside handheld scanners. These methods of scanning allow R-Evolution to scan the rainforest in layers, down to the soil, and even to scan underwater rainforests.
Morgan Maia, partnerships manager at Oracle Red Bull Racing, discussed how the team’s use of Hexagon’s technology will become more important than ever in 2026, with the release of Red Bull Powertrains. Currently, approximately one million parts are scanned and verified by Hexagon’s technology each year, ensuring that Red Bull’s cars can be verified by FIA standards. Starting in 2026, however, this quantity will rise closer to three million.
The opening of the Experience Centre places Hexagon in the centre of the EMEA area, and connects the company directly with some of its biggest customers in Eindhoven. The event provided insight into the range of companies using Hexagon software and hardware, leaving the impression that Hexagon is driving to succeed in all these markets.
This article first appeared in DEVELOP3D Magazine
DEVELOP3D is a publication dedicated to product design + development, from concept to manufacture and the technologies behind it all.
To receive the physical publication or digital issue free, as well as exclusive news and offers, subscribe to DEVELOP3D Magazine here