Impossible Objects CBAM 25 additive manufacturing system is being hailed as a super fast means of building composite parts, some 15-times faster than existing methods.
The process works by long-fibre sheets of carbon or fibreglass being fed into the printer, where each one forms a layer for slides of the CAD model to be printed onto the sheets using a clear proprietary fluid and thermal inkjet technology.
Then, a polymer powder is applied to the fibre sheet adhering to the fluid, while excess powder is removed, being repeated for all layers. Much like typical composite layering methods, sheets are then stacked then heated to the melting point of the polymer and compressed to consolidate the part. Using a mechanical or chemical process, un-bonded portions of sheet fibres are removed, revealing the final part.
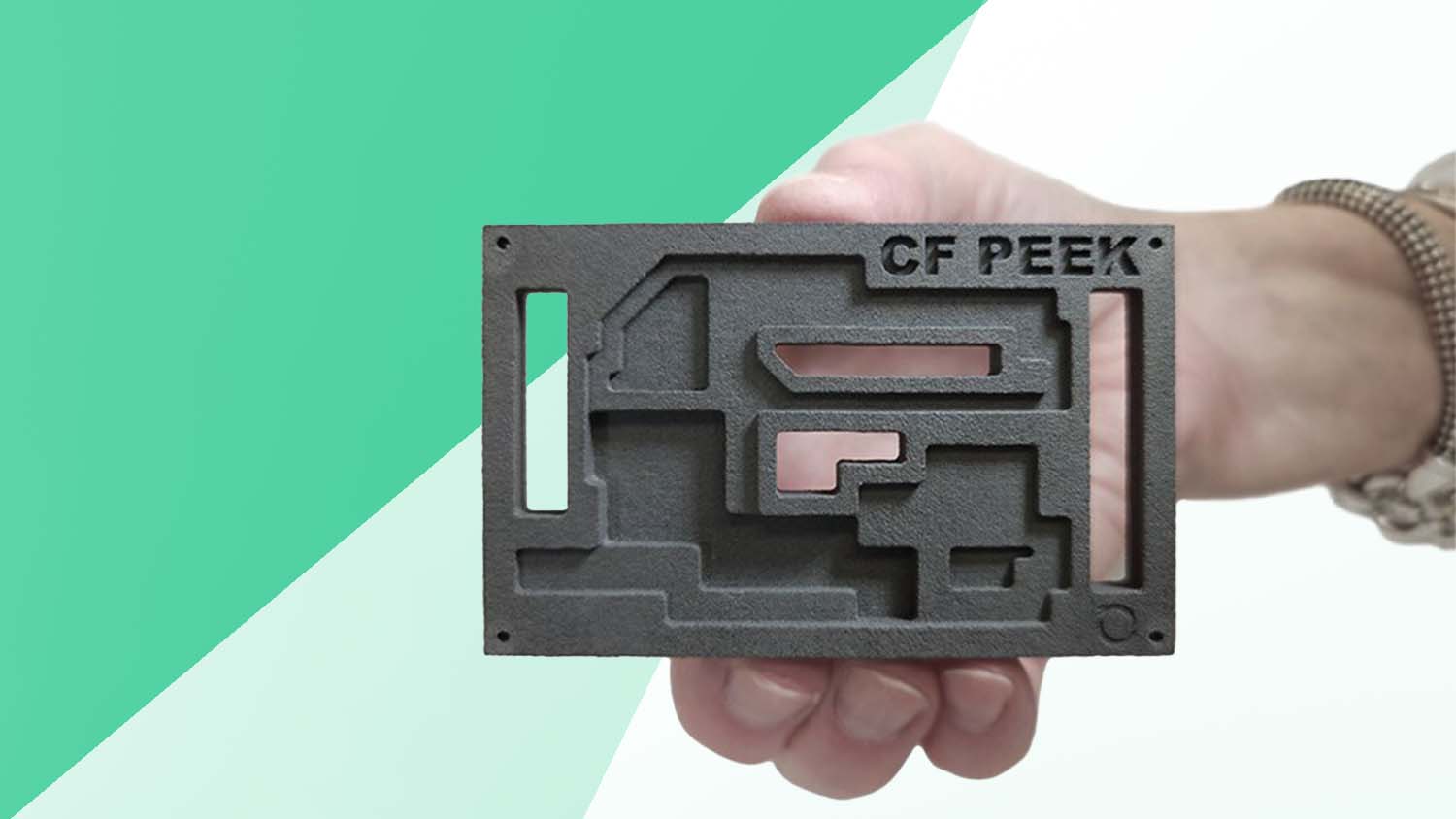
“The world is made out of things and with the CBAM 25 we are changing the way they are made,” said Impossible Objects founder Robert Swartz. “The CBAM 25 is the world’s fastest printer, and we are entering a new era of 3D printing with nearly unlimited material options at the speed of true mass production.
“This is a Moore’s law moment for 3D printing, and this is just the first step.”
The use of long fibre composites sheets and performance polymers like PEEK, mean extremely strong parts, with very high chemical and temperature resistance.
Impossible Object’s Rules-based Automated Masking Packing and Slicing (on-RAMP) software is powered by Dyndrite, and integrates a multi-threaded, GPU-accelerated, Python-based Accelerated Computation Engine to drive the process.
Offering automated CAD-to-print workflows and an easy to use GUI, benefits include faster processing of native CAD 3D data, reductions in tedious manual labour, automated labelling and nesting that optimises build space and minimises scrap, and customisable workflows that allow significantly faster time to a first part.
This software workflow helps further accelerate the process, while adding efficiencies for an improved build block use by a reported 20%.
“Dyndrite was the perfect partner for supplying software to match our new high-speed process,” continued Swartz. “Their team and software augmented our own internal team enabling us to focus on what differentiates us, and keep our IP internal while leveraging their powerful ADK toolsets. The result is a high performance hardware, software and materials solution that puts automated durable end-use AM part production in the hands of users worldwide.”
CBAM 25 machines will be available in early 2024, while customers can order test parts immediately.