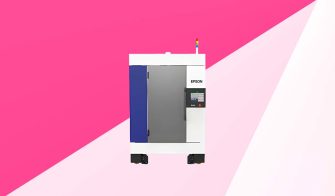
Fresh from the announcement of its development of an industrial 3D printing system, we spoke to Epson head of manufacturing solutions Volker Spanier.
Capable of using common third-party manufacturing materials using an extrusion method evolved from its existing injection moulding technology, he answered our questions about the origins of the technology, and where it will likely position the brand in the expanding world of additive manufacturing.
DEVELOP3D – Like a lot of companies, we assume that Epson has long had 3D printing technology inhouse. Can you give us an idea of the background behind the new 3D printer’s development?
Volker Spanier – At the 2017 CeBIT exhibition, Epson Group’s president at the time, Minoru Usui, explained that Epson would first observe the developments of the 3D printing landscape to better understand whether Epson could offer value in this area.
The competitive advantages of Epson’s technology portfolio derive from leveraging its own precision and digital technologies, and it was important for Epson to focus on this at the early stages of its new product development for 3D printing.
D3D – Why has Epson chosen FDM as the technology to embrace? Is it purely from the materials perspective?
VS – Epson’s flat screw method is based on the same principle as FDM, but our technology is more advanced. The flat screw (F/S) method of material extrusion is superior to inline screw (I/S) and filament-based methods in terms of material versatility, strength and precision on/off control.
D3D – What does Epson see as the key issues in this sector, and how is it looking to fix these?
VS – The top three challenges of 3D printing are a limited number of materials available for each method, needing a better balance between lot size and cost, and producing end-products that are both high quality and cost effective, which Epson’s 3D printers improve on.
Epson’s aim is to innovate in the area of manufacturing innovation by creating highly productive and flexible production systems with a low environmental impact. In this context, Epson 3D printers will contribute to mass customisation (providing customised products with the same quality, cost and delivery as mass production), using eco-friendly and environmentally friendly materials and digital technology to create mass production quality.
The combination of Epson’s own precision injection control technology based on Techforum’s technology (flat screw) ensures the use of versatile materials (injection is possible even for super engineering plastics such as PEEK (polyetheretherketone)).
Epson’s proprietary technology ensures:
- Constant injection rate technology (constant pressure control technology using a pressure sensor to feed back to the flat screw speed)
- Precise flow control technology (control of resin flow by means of a valve adapted to the build trajectory speed) ON/OFF mechanism
- High-strength layering technology (temperature control of the build surface using heaters and temperature sensors) to produce parts with the precision and strength required for industrial use.)
D3D – Is there a particular spot in the market that Epson is targeting?
We will consider the appropriate price based on the specifications and the market price, which is expected to be between ¥20-30 million per unit (roughly £120-180k).
In general, the unit purchase price of general-purpose pellet materials is about 1/10 of that of dedicated filament materials and dedicated powder materials.
Other companies’ filament 3D printers are limited in the materials they can use, which makes it difficult to produce high content materials such as cellulose, wood filler and carbon fibre, but Epson 3D printers are able to meet this challenge.