To exploit all the benefits of new and composite materials, multiscale analysis is being employed. Laurence Marks takes a look at how this enabling technology will facilitate step changes in how components are designed, used and disposed of
Everyone doing simulation is doing multiscale analysis, but possibly without thinking in those terms. All the big stuff is boundary conditions and the small stuff comes from Matweb.
Anything in between is our model, and therefore the only bit we are really interested in. That’s probably a tiny bit unfair, but is actually a reasonable summary of where most of us are at.
But – and there was always a ‘but’ coming – as we look for increasing levels of performance, especially by using advanced materials, and combinations of materials, this simplified approach may not take us far enough.
Old new materials (I once heard aluminium described as the world’s oldest new material) and ‘properly’ new materials present many simulation challenges if we are going to exploit their potential to reduce weight, cost and environmental impact, and do it in a manner that we at least wish for with modern manufacturing processes like additive manufacturing.
Simulation is possibly our best bet for avoiding what I heard a pioneering F1 composites engineer describe as the “black metal” phase. That’s where we use a new material in the same way as the one it replaces, thereby failing to exploit many of the advantages which are there to be taken.
In fact, if we stick with the composites theme, we can see the starting point of what is generally known as multiscale analysis.
‘Traditional’ elements generally assume that they are made of a single material, and that material doesn’t vary across the element. That, honestly, is good enough for the vast majority of simulation challenges. Yet composite systems have a variation of material on a scale smaller than any mesh that you could solve. That’s how they achieve their levels of performance.
So, code developers were forced to create elements which could handle many layers of different materials; materials that are often stiffer and stronger in one direction than the others.
More advanced and creative material systems, and external drivers such as lightweighting and recyclability, forcing their adoption, have driven the simulation world to explore this process further.
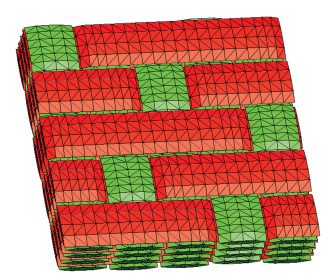
Representative volume elements (RVEs) are now quite widely employed to do this. In this approach, the material properties for the finite element model are replaced by another finite element model. However, this one is of a much smaller scale than the part being modelled – it represents the material structure and critically can include not just multiple materials but also interactions between them.
In this ‘FE2’ process, we find a two-way street: how the material properties vary as the stresses build on each element are calculated by the RVE, yet the RVE can also be used to determine how the material is responding locally to the stresses.
The multiscale approach bridges the gap between the length scales – but, it must be said, at something of a computation cost. How this computational cost is reduced and controlled, and how the data is reused, is what separates an effective commercial code from an academic prototype.
Currently, commercial codes include Multimechanics from Siemens, e-Xstream/Digimat from Hexagon and Altair Multiscale Designer, amongst numerous others.
Potential applications of this technology go way beyond the classical composites that seem to form the majority of use cases at the moment. Building an understanding of the material structures that result from the many additive manufacturing processes being developed and exploited must be an application area that is set to grow. And the fuzzy boundary between material and structure that is developing as a result is only set to drive the technology further.
It’s fair to say that the average CAD user involved in basic integrated FEA is unlikely to embark on multiscale simulations any time soon, yet in many high-performance scenarios, it’s an enabling technology that will facilitate step changes in how components are designed, used and disposed of.
I’m thinking here about replacing metals with short-fibre reinforced injection moulded parts to eke out the last few percentages of composite structural performance where that is critical. It’s not for nothing that the automotive world is at the forefront of multiscale modelling and its application.
Laurence Marks built his first FEA model in the mid-1980s and his first CFD model in the early 1990s. Since then, he’s worked in the simulation industry, in technical, support and management roles.
He is currently a visiting research fellow at Oxford Brookes University, involved in a wide range of simulation projects, some of which are focused on his two main areas of interest: life sciences and motorsports.