The journey towards zero-emission vehicles starts with small components. Claudia Schergna speaks to Markforged about how its copper 3D printing technology helps car designers create parts with efficiency
The automotive market is already seeing huge growth in electric vehicles (EVs). The UK market alone grew by over 800% between 2016 and 2022, and is expected to be the driving force behind new car sales for years to come. Despite demand, automotive producers have reported that they struggle to achieve profitability due to manufacturing challenges. Even as entire supply chains are built around EVs, their components remain extremely complex to produce efficiently.
As in many other industries, using additive manufacturing (AM) in automotive to prototype components represents an opportunity to speed up time to market and save resources. NEW
New materials, better results
Pure Copper material and the Metal X system by Markforged are being used in automotive R&D to prototype components such as busbars in order to reduce costs and optimise designs.
A busbar is an electroconductive metallic bar that distributes current to subsystems in intensive electrical applications. It is therefore an essential component when it comes to achieving optimal electrical performance in EVs.
Designing the right busbar can be complex as engineers must work with multiple constraints. In particular, a viable design requires them to work within boundaries of both form factor and heat dissipation requirements.
Busbars in EVs are usually made of pure copper, due to the material’s high electrical conductivity. But despite its excellent electrical properties, copper is difficult to work with in traditional manufacturing, which translates into high price tags and long lead times. To alleviate these challenges, metal 3D printing is the perfect candidate.
Given that several iterations may be needed to create an optimised part, these high costs and long lead times can force designers to make several compromises, and time constraints may lead to less optimal designs.
By 3D printing pure copper to prototype busbar designs, electric vehicle suppliers can enjoy several competitive advantages. The ability to 3D print in pure copper allows vehicle suppliers to reduce costs on each iteration and avoid long lead times due to bottlenecks in machine centres. It also empowers engineers to quickly test more experimental designs.
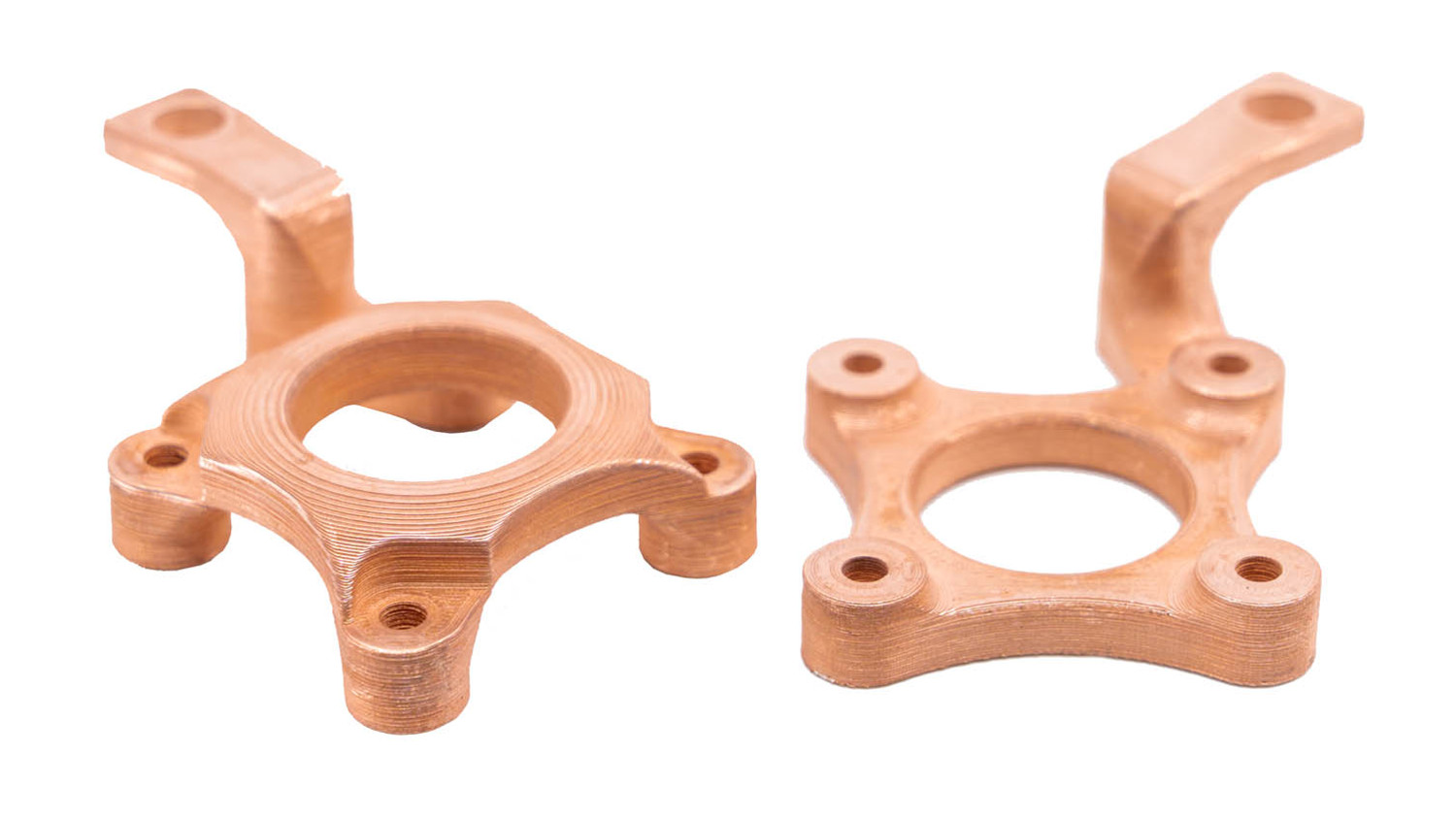
More for less
Markforged estimates that a traditional manufacturing process for creating a busbar prototype would typically cost about over £160 per iteration, with a three-week lead time. By contrast, printing a busbar prototype with the Metal X System in pure copper would cost around only £45, with a lead time of just three days.
This means the Metal X can turn around 9 iterations in the same time it would take to get just a single iteration through traditional fabrication, allowing engineers to test designs during time that would otherwise be spent waiting for parts to arrive.
Markforged Metal X is not the only technology to offer the possibility to print copper, but the company claims it is the only one that allows printing pure copper, which is required for the fabrication of busbars, since other copper alloys would not yield the same performance.
The ability to produce 3D printed prototypes is extremely valuable, with quick-turnaround fabrication having a revolutionary effect on the workflow and freeing up valuable machinist bandwidth and reducing the costs associated with using third-party services in order to get prototypes in hand.
Besides busbars, 3D-printed pure copper is also being used for EV applications such as heat sinks, exchangers and cold plates.
Faster prototyping abilities are a big boost to design cycles, making possible higher levels of optimisation compared to traditional manufacturing.
These characteristics are particularly crucial for applications where time and money optimisations are a priority, and EV development is one of the sectors where these pressures are felt the most.
This article first appeared in DEVELOP3D Magazine
DEVELOP3D is a publication dedicated to product design + development, from concept to manufacture and the technologies behind it all.
To receive the physical publication or digital issue free, as well as exclusive news and offers, subscribe to DEVELOP3D Magazine here