A BOA Fit System has to perform under stress, leaving its designers with a challenge to speed up their physical prototyping. We learn how a 3D printing material with thermoplastic qualities means BOA’s testing can be as tough as needed earlier in the design process
The BOA Fit System is a common thread connecting workwear, medical bracing, and sports like golf, snowboarding, and cycling.
Each integrates BOA’s patented three-part fit system into high-performance products, keeping its wearers dialled-in without a fleeting consideration that the connection might unlace or unravel at any critical stage.
One of the main components of the BOA Fit System is the dial, which is engineered to three different power levels depending on the lace tensions achieved by the internal gear they are fitted to.
This includes the high power snowboard dials with gear reductions for high torque that launched BOA’s success in 2001.
Getting prototypes on the shoe for early testing and interaction is a big plus point for BOA’s design team, even for concepts that don’t make it to production. Putting iterations through real-world abuse helps the designers gather more design and performance data on what works and what doesn’t.
This aspect of testing requires the dials to be sewn directly into fabric without molded holes. According to BOA senior design engineer Daniel Hipwood, finding conventional plastics that can be stitched is difficult enough, let alone finding a UV cured 3D printed material that will perform without cracking.

“Punching a needle through plastic is a toughness problem. You need a material that is resilient, but still maintains enough stiffness to carry out its other uses,” explains Hipwood.
“Part count reduction is key, so that stitched component may have other important functions that require a stiff plastic material.”
BOA has been using 3D printing to prototype for several years now, but according to Hipwood, it has been difficult to match BOA’s applications with the material performance needed.
The scale of BOA’s products are small and the mechanical properties needed are paramount, leaving some 3D printing processes only able to provide concept verification and aesthetic models.
“We’ve been really hamstrung by the materials available to us,” says Hipwood, explaining that the parts BOA was printing were turning brittle and not holding up over time.
“We’d have a concept and three days later, if the part fell off a desk in a meeting, it would just shatter into a million pieces. It’s been a real challenge to find thermoplastic-like performance at the resolutions we need, and to actually 3D print parts that function at our scale and can still hold those properties.”
Although BOA’s workflow will still include short runs of pre-production injection moulded parts for the foreseeable future, the company wanted to close the gap between 3D printed part durability and final injection moulded parts so it could push its designs further, faster, and with greater confidence before beginning the tooling process.
To do this, its research led BOA to 3D Systems’ Figure 4 Standalone 3D printer and materials line-up.
Rather than wait the typical three weeks for machined parts and moulded components, BOA is now able to assess the viability of its designs in the same afternoon using its Figure 4.
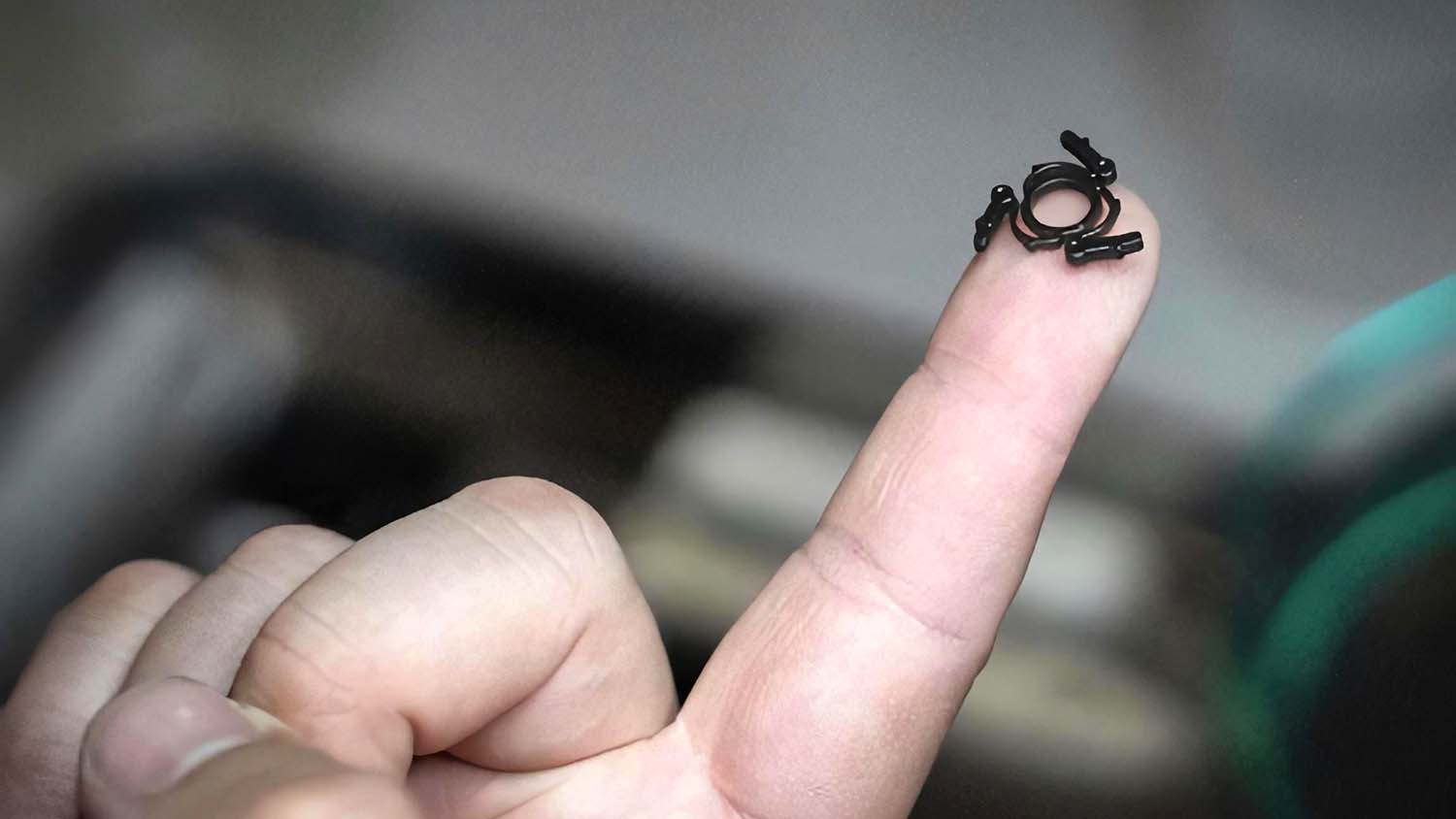
The engineering team use several of the available 3D Systems’ Figure 4 materials, and is particularly fond of Figure 4 Pro-Blk 10 and its high precision, long-term environmental stability, which acts with a thermoplastic-like behaviour.
Pro-Blk 10 is being used for ongoing correlation tests between final production parts and Figure 4 parts to understand the threshold performance requirements it needs before moving on to production. “Sometimes it’s actually one-to-one,” says Hipwood, “So they’re performing the same as our injection moulded components.”
The fact that Pro-Blk 10 can be used to prototype in this manner has been a major help to BOA, saving time and money to quickly iterate its designs for the highest performance.
“Everyone is striving to shrink and optimise their products, which makes it critical to identify the weak spots as early in the design process as possible to avoid finding problems when moulds have already been created.”
The BOA Guarantee, a lifetime warranty offered on its BOA Fit System products, means that quality out of the gate is paramount.
Having functional printed parts helps Hipwood and the team not only complete faster design cycles, but also means less redesign of components after tooling creation – meaning boots on the ground ready for action.