BCN3D has launched its Viscous Lithography Manufacturing (VLM), its new resin-based 3D printing technology that allows the resin to be laminated from both sides of the film, speeding up build times, and allowing different resins be combined for multi-material parts
Using a UV light source and an LCD screen to laminate thin layers of high viscosity resins onto a transparent transfer film, VLM looks to deliver constant time per layer, regardless of the number of parts been printed at one time, and without being constrained by the vat dimension, users should be able to scale-up by using a bigger LCD screen.
BCN3D says that its VLM technology is also designed to filter and recirculate unused resin, meaning that every drop of resin will potentially be used, helping reduce overall costs.
For these reasons, BCN3D has defined VLM as ‘the most productive additive manufacturing solution on the market’, and has priced the initial system at under €50,000.
BCN3D has claimed that, unlike other resin technologies on the market, VLS can process resins 50-times more viscous than the industry standard.
Without a strict low viscosity constraint, chemical companies should have more freedom to formulate new sets of ingredients that can be added to the resin to modify their thermal and mechanical properties.
According to BCN3D, VLM can process resins that obtain three-times the amount of impact resistance for rigid materials and a 200 per cent increment in tear strength compared to industry-standard formulations.
“If 3D printing is to be the future of manufacturing, and what leads us towards local production, customisation, control of supply chains and sustainability, all the players in the industry should be pushing in this direction,” said BCN3D CEO Xavier M. Faneca.
“At BCN3D, we think that today is the first step in achieving this goal with the new Viscous Lithography Manufacturing (VLM) technology. We want to show 3D printing in a new light so that it becomes the pivotal point of manufacturing.”
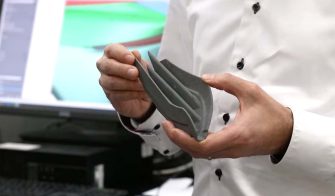
The speciality material company Arkema, with whom BCN3D has a joint development agreement, has claimed that VLM technology will open the path for thermosetting resins to further evolve mass manufacturing and the production of functional parts.
“Thanks to the proven capability of VLM to manage high viscosity resins, we envision a great prospect to develop new building blocks and enable game-changing formulations to meet applications requirements that have not yet been reached with existing photocured technologies,” said Arkema European 3D market manager Hélène Egret.
BCN3D has partnered with the motorsport and advanced technology company Prodrive, which is one of the first in the world to put VLM technology to the test, by assembling end-use parts made with VLM mounted directly on off-road vehicles.
“VLM technology seemed to combine all the best features of the different additive manufacturing technologies, and even offer some unique advantages,” said Prodrive design engineer Callum Harper.
“For Prodrive, materials are the key to making durable end-use parts. VLM allows us to continue to use the engineering materials that we know and love, but instead in significantly finer resolution in all three directions, and the material is much more homogeneous, making the finished parts behave much more like a traditional injection moulded part.”
The automotive glass manufacturer Saint Gobain, in partnership with BCN3D, has claimed that, by using VLM, it was able to fabricate 7,000 positioning fixtures in 7 days, saving up to €70,000 in a year.
“VLM technology has empowered us to see significant improvement in the future,” said Saint Gobain manufacturing manager Alberto Rodriguez Fernandez.
“Our main goal is to reduce our dependence on external mechanisation suppliers and do it internally instead with technologies such as VLM. Doing so is what would give us the power of manufacturing autonomy.”