A new 3D printed wind tunnel material has been launched by 3D Systems in collaboration with the Alpine F1 Team, speeding up the CAD-to-testing process.
The new Accura Composite PIV material has been designed for more efficient part production, with accurate and high resolution Particle Image Velocimetry (PIV) testing data – making it ideal for aerodynamic testing situations.
The parts built using the Accura Composite feature a high-contrast colour (Prince would approve) which is optimised for PIV testing, which removes the need for further time-consuming post processing steps when creating wind tunnel material parts.
In addition to being as purple as Ribena, the material has a high tensile and flex modulus, with a heat deflection temperature of 100° C, making it ideal to withstand the rigours of wind tunnel testing.
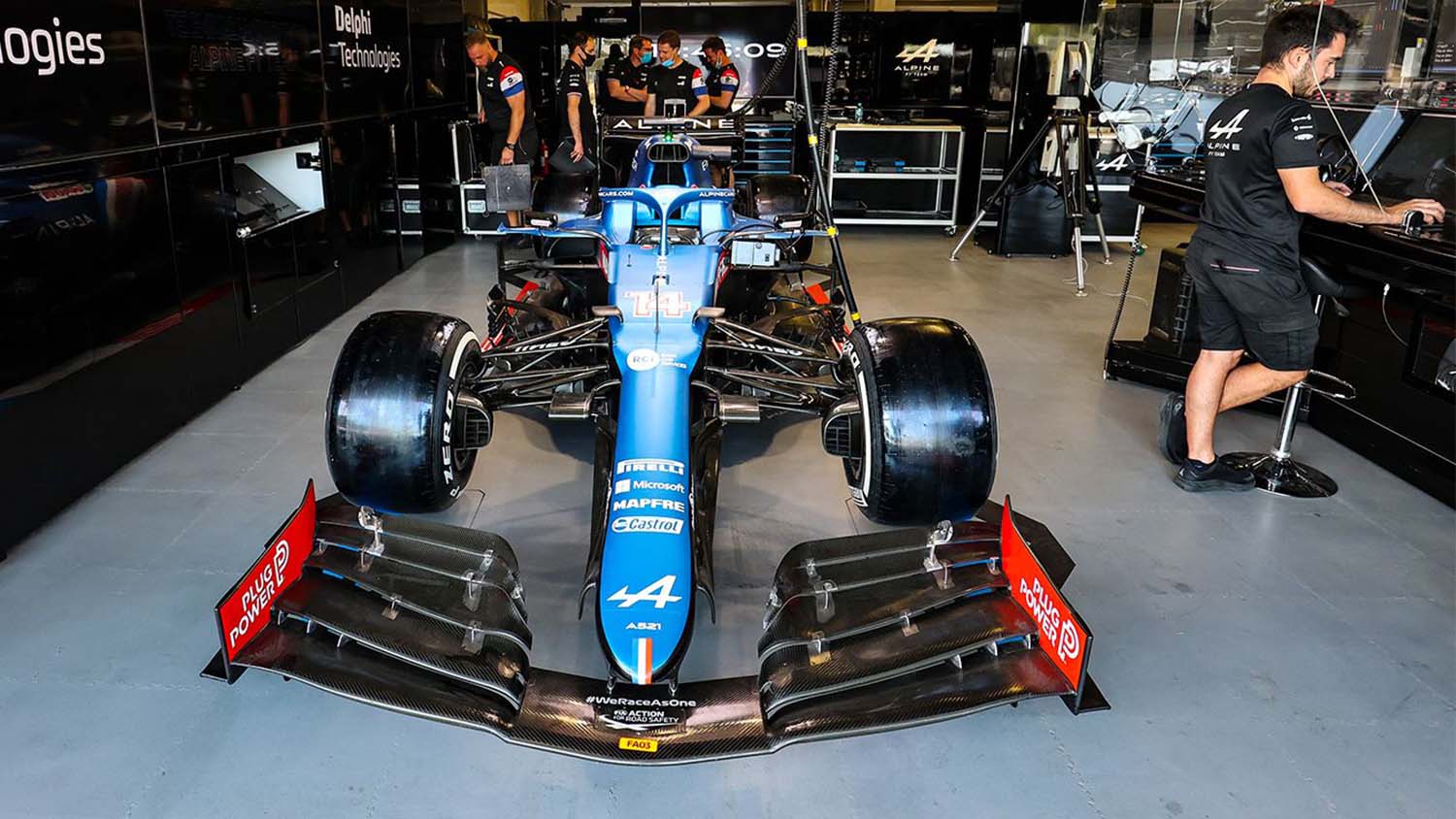
Alpine F1 have been instrumental in developing the material, stating that when used as part of its complete 3D Systems additive manufacturing solution – comprising Accura Composite PIV, the company’s SLA technology, software, and advanced application services – the team has been able to maximise its wind tunnel investment and improve its understanding of the airflow over the car.
3D printing wind tunnel parts for aerodynamic testing is an intensive part of the design process, making it virtually a 24/7 operation as the racing team constantly works to unlock new levels of performance in the car.
3D Systems explains that its SLA technology has allowed Formula 1 companies to build rigid aerodynamic parts with high productivity and leverage innovations like integrated pressure tappings.
When these parts are used in laser-based PIV testing, their reflection mitigating properties mean that the wind tunnel cameras capture more of the air particles, and less background reflection.
“We’ve proudly collaborated with 3D Systems for many years,” said Pat Warner, Alpine F1 Team’s advanced digital manufacturing manager, and the man behind producing some 500 3D printed parts each week for wind tunnel testing.
“The deep expertise of their application engineers and their industry-leading solutions have been an invaluable part of our innovation team. It’s been exciting to co-develop Accura Composite PIV and see the benefits it’s bringing to our process.”
“Customer-centric innovation is a guiding force within 3D Systems,” said Kevin Baughey, segment leader, transportation & motorsports, 3D Systems. “Working with Alpine F1 Team to develop our newest material is another example of how we’re leveraging our F1 application expertise to develop advanced solutions that give our customers a competitive edge.”
The move to develop industry specific processes and materials looks to be part of 3D Systems’ continuing policy which has seen it move away from its previous business model including the recent off-loading of its global on-demand 3D printed parts business.