Doppelmayr/Garaventa Group’s ropeways must deliver on flawless operation, comfort and safety, and advanced simulation from Altair provides a robust way to test out the performance and strength of its designs
Doppelmayr/Garaventa Group is an international manufacturer of ropeways and innovative transportation systems for ski areas, urban transport, amusement parks and material handling systems.
Doppelmayr was founded 1893, merging with Garaventa AG in 2002 to become the world’s leading ropeway manufacturer. As of 2020, the group has realised more than 15,100 installations in 96 countries worldwide.
Since 2017, the company has been using Altair solutions, including Inspire, for the topology optimisation of design parts to reduce material usage and product weight and to increase durability.
More recently, Doppelmayr started using Altair SimSolid to explore its designs and create structurally efficient concepts for large models and complex assemblies.
In modern passenger transport systems, flawless operation, comfort and safety are key engineering criteria for design. To guarantee these key performance indicators, demanding fatigue tests are performed to ensure a component’s performance and strength. Today, advanced simulation methods help to achieve optimal designs and meet the highest safety requirements.
Using Altair Inspire, Doppelmayr built a design that passed the necessary safety tests and optimised a gondola station to be even lighter, safer and more durable than the client requested.
Challenge accepted
Doppelmayr’s engineers were set the task of optimising a bracket of a Doppelmayr lift station building. Since the seam weld of this bracket had failed a critical fatigue test, it was necessary to improve the design of the component for increased strength and fatigue-life of the connection.
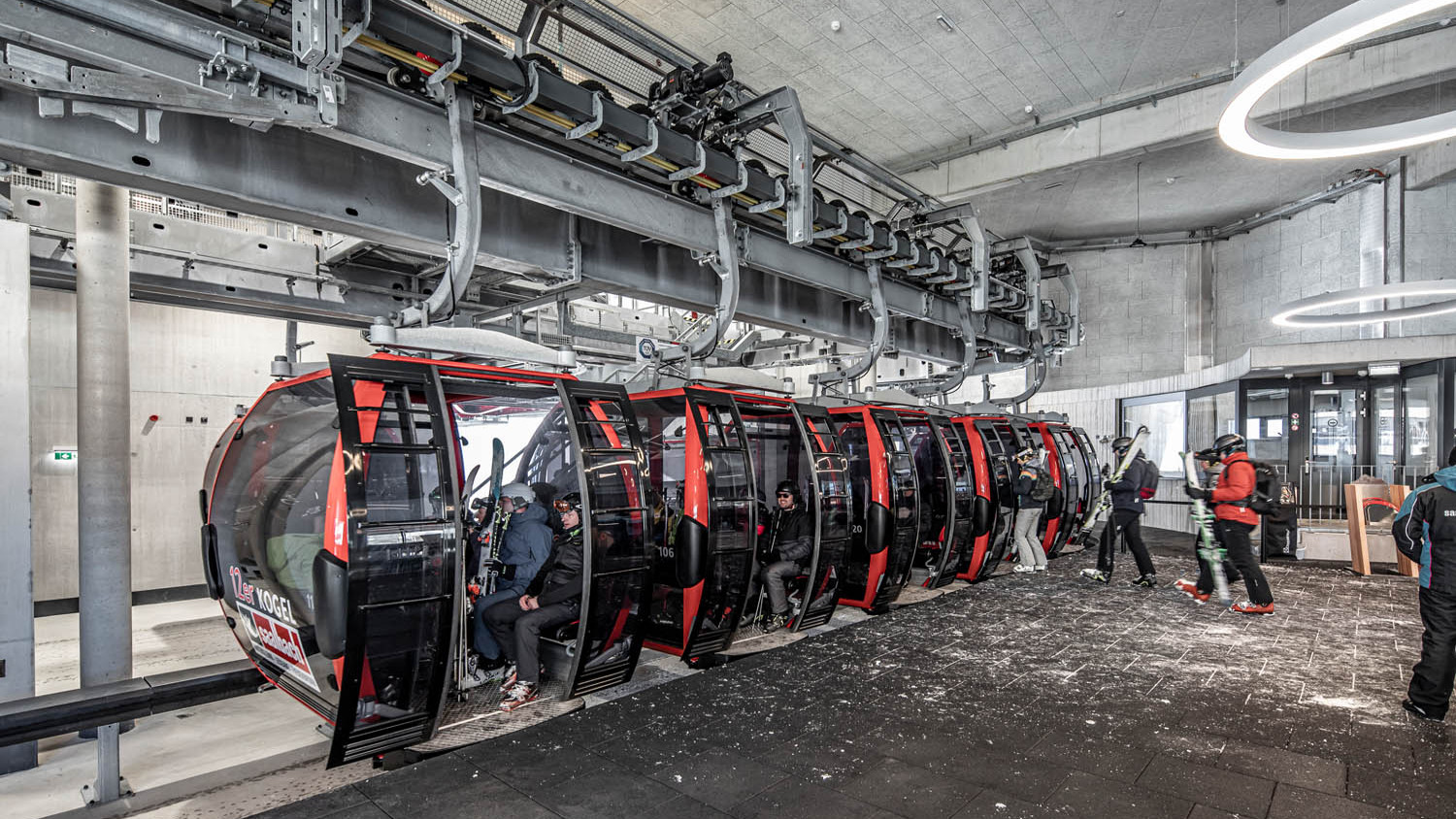
The main challenge for the new design was to pass the critical fatigue test. This tests the bracket, taking into consideration the maximum forces that can occur during ropeway operation, while also measuring defined parameters like vibration and material strain. To meet high safety standards, the construction has to withstand 100 Mio load cycles.
With that in mind, Doppelmayr engineers had to identify a solution that would enable them to build high-precision components, while considering material use, manufacturing constraints and time and budget for the project.
From previous successful projects, the team had already gained a lot of experience with Altair solutions. With Inspire, and working alongside Altair’s own expert engineers, the Doppelmayr team was confident it could achieve a weight-reduced bracket with increased lifetime and the endurance to pass the critical vibration test. Using the test parameters, they were able to create a full-scale simulation scenario.
In the first step of the optimisation process, the engineers specified the requirements of the new bracket design and generated the CAD model.
Since the initial tests revealed overstressing in one part, the aim was to redesign for better stress distribution and relocate the stress concentration outside the weld seams. The original CAD data was then imported to Inspire and the team defined both the external and internal clearance, design space and manufacturing method.
After two iterations in Inspire, the engineers were able to identify the optimal design. The final design solution was a welded insert with a flame-cut profile and weld preparations.
This ensured that the stress remained outside the weld seams, creating a better stress distribution and an increased lifetime.
Altair enabled the Doppelmayr engineers to develop a multi-step process, accurately predict the critical area of the first design that had failed the test, and find the proper design modifications. They were able to generate an optimal design, in a reasonable amount of time, that met performance targets and was lighter than the original.
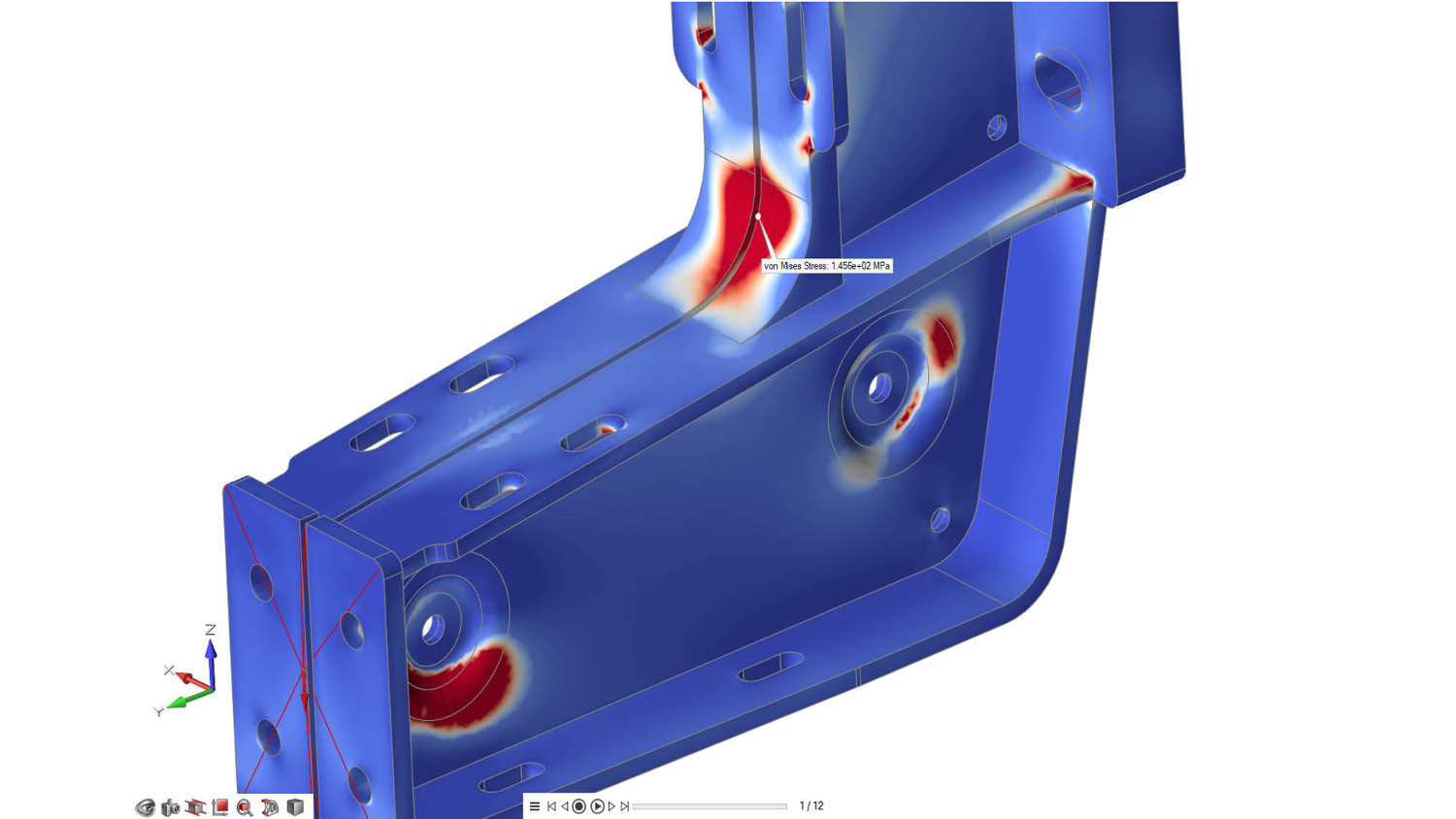
Doppelmayr – impressive results
When it comes to specific results achieved using Inspire, Doppelmayr engineers were able to increase the lifetime of the seam weld while reducing the length of each component’s weld seam by 3.5 meters.
The component passed the vibration test and the component’s fatigue-life was increased by factor 4 – from fatigue limit design to fatigue cut-off limit.
In addition to meeting safety targets, Doppelmayr also reduced manufacturing time and costs by approximately 10% for the new design. Long-term results also include reduced maintenance costs, due to the increased lifetime of the bracket.
“Thanks to working with Altair, we are now able to accurately match our components to stringent quality and safety requirements,” says Philipp Schneider, head of the structural calculation department of Doppelmayr. “The experience we have gained by working with Altair’s engineers will help us to continuously provide our customers with safe and comfortable transport solutions.”