If something needs to be dug up, lifted, pushed, carried or positioned, whatever its size or weight, then JCB has a bright yellow machine for the job.
Founded by Joseph Cyril Bamford in Uttoxeter, UK back in 1945, the company has never stopped innovating over the 75 years of its existence.
Today, its equipment can be found on construction sites, farms, warehouse sites and military bases around the world.
But being powered by diesel, these products are vulnerable to rising fuel prices and environmental concerns over the burning of fossil fuels.
Throw lifestyle changes and population growth into the mix, too, and you’ve got an idea of the sorts of issues that play on the mind of JCB’s director of advanced engineering, Bob Womersley.
After all, he’s the person who, for the past decade, has been entrusted with guiding the company’s next great step, as a producer of zero-emissions vehicles.
Womersley is perhaps the perfect person for the task, with his enthusiasm for progressive engineering, a nearobsessive focus on powertrain efficiency and his dedication to understanding customer needs.
He describes the company’s drive to introduce new electric machines as “a pulse” in the business, conjuring up a sense of something vital and insistent.
He’s also optimistic about sales prospects for these new machines, citing as evidence the C40 Cities Climate Leadership Group, a group of 96 cities around the world that collectively represent one-twelfth of the world’s population and one-quarter of the global economy.
This group focuses on tackling climate change and driving urban action to reduce emissions and climate risks. Says Womersley: “These places are full of electric machines now and, as an engineering team, we think it’s fantastic, because we’re involved in launching product into nascent markets.”

JCB – Interest and acclaim
In 2019, JCB launched its first electric vehicle, the 1.9- ton 19C-1E mini digger, to widespread interest and acclaim.
The new model scooped one of the automotive industry’s most prestigious honours, the Dewar Trophy for outstanding technical achievement, from the Royal Automobile Club.
The trophy is only awarded in years when the judging committee deems there to be an entry of sufficient merit and JCB is one of only four companies to have ever won it twice – the last time being back in 2006, for the land-speed record-breaking JCB Dieselmax car.
As the accolade suggests, the development of the JCB 19C-1E goes way beyond a simple powertrain swap.
The initial steps began a decade earlier, with an internal concept excavator, running on a hybrid powertrain partly influenced by the Toyota Prius.
This was a functioning machine, certainly – but it turned out that a production version would end up costing customers nearly three times as much as its diesel equivalent.
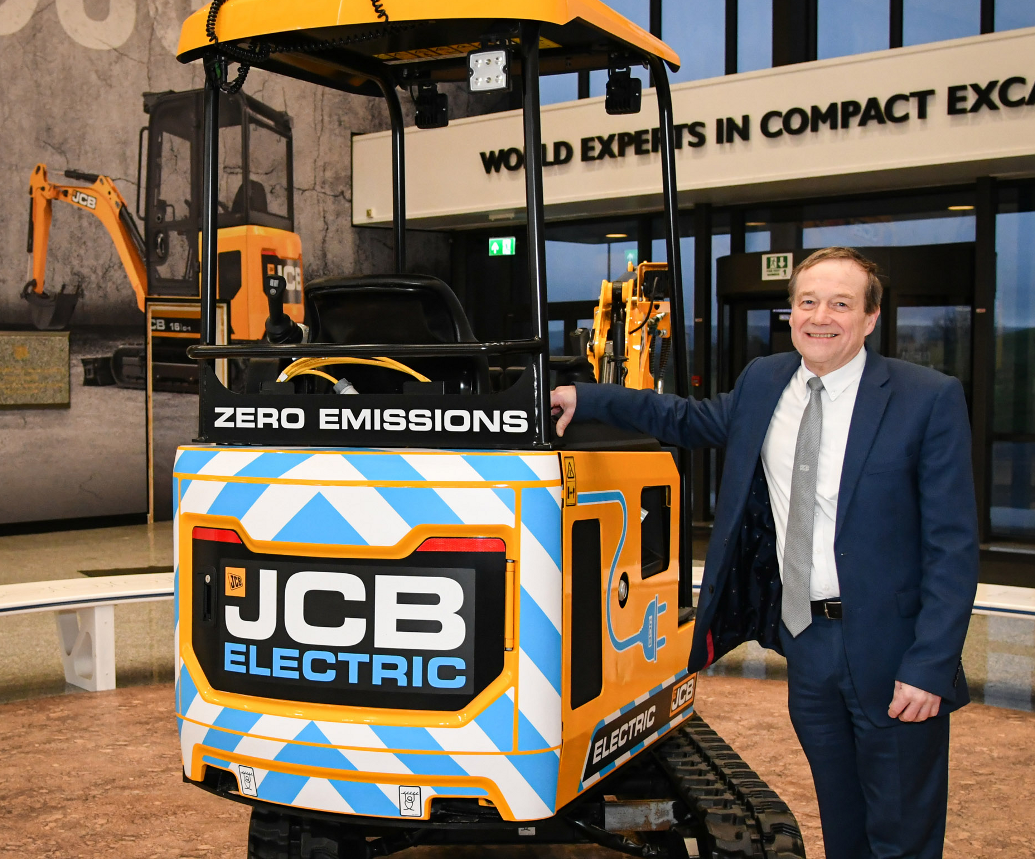
The project was shelved as commercially unviable, but the work involved had planted a seed.
A company directive to move to electric power soon followed and, with subsequent technological advances, JCB began to see opportunities to sidestep the hybrid model and focus instead on Lithium-ion batteries.
For the 19C-1E’s design and engineering, battery capability would be crucial, and the JCB team settled on battery packs designed, developed and manufactured by Hyperdrive Innovation.
This Sunderland-based company is located across the road from the Nissan factory where the same cells are used in the automotive giant’s popular Leaf electric car.
JCB pushed the validation process of Hyperdrive Innovation’s battery to the limit, well beyond normal automotive use. “It had to be robust,” Womersley explains.
“There’s no suspension on these machines, so the vibration characteristic that the whole of the propulsion system has to withstand is substantial.”
Years of honing the design of the diesel mini digger for systems efficiency meant that 48v batteries, a relatively low-power source, could be used.
These proved more than a match for the digger’s diesel equivalent.



Using Siemens NX for 3D CAD modelling, all the components of the original design’s diesel powertrain were removed, giving the team a packaging envelope with which to work.
As with any excavator, the all-important need for stability means designing so that weight is located both low down and towards the rear of the vehicle.
This rule would clearly apply to the battery, if the excellent balance and poise of the original diesel version was to be maintained.
At the same time, positioning the battery this way would lend it extra protection from knocks, scrapes and potentially, theft.
“Most of the attention to detail around this machine to unlock the electric capability was the structuring [of ] the middle of the machine,” says Womersley, adding that the FEA [finite element analysis] tools in Siemens NX and other FEA software played an important role here.
“I think we’re genuinely world-class at forming a joint in metal and understanding structural performance, so we can use the minimum amount of steel to get the stiffest structure,” he says.
“In Siemens NX, we’ve got software packages that not only do the FEA, but [also] if you design a loader arm, how do you ensure that you get it right when it’s all welded?
That’s the sort of analysis we do with the big weldments, on the chassis and what have you, with all of the analysis done prior to the first prototype being made.”
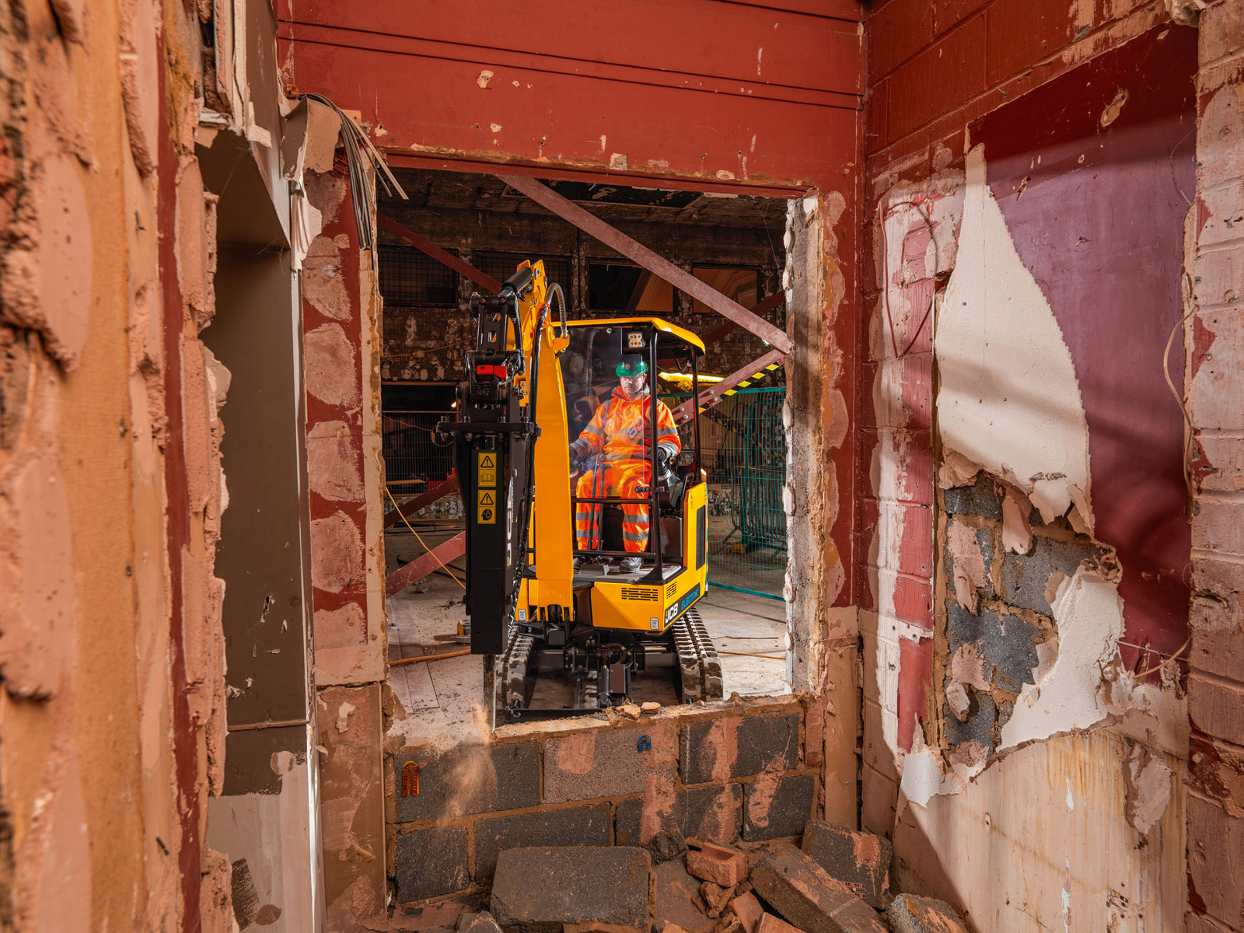
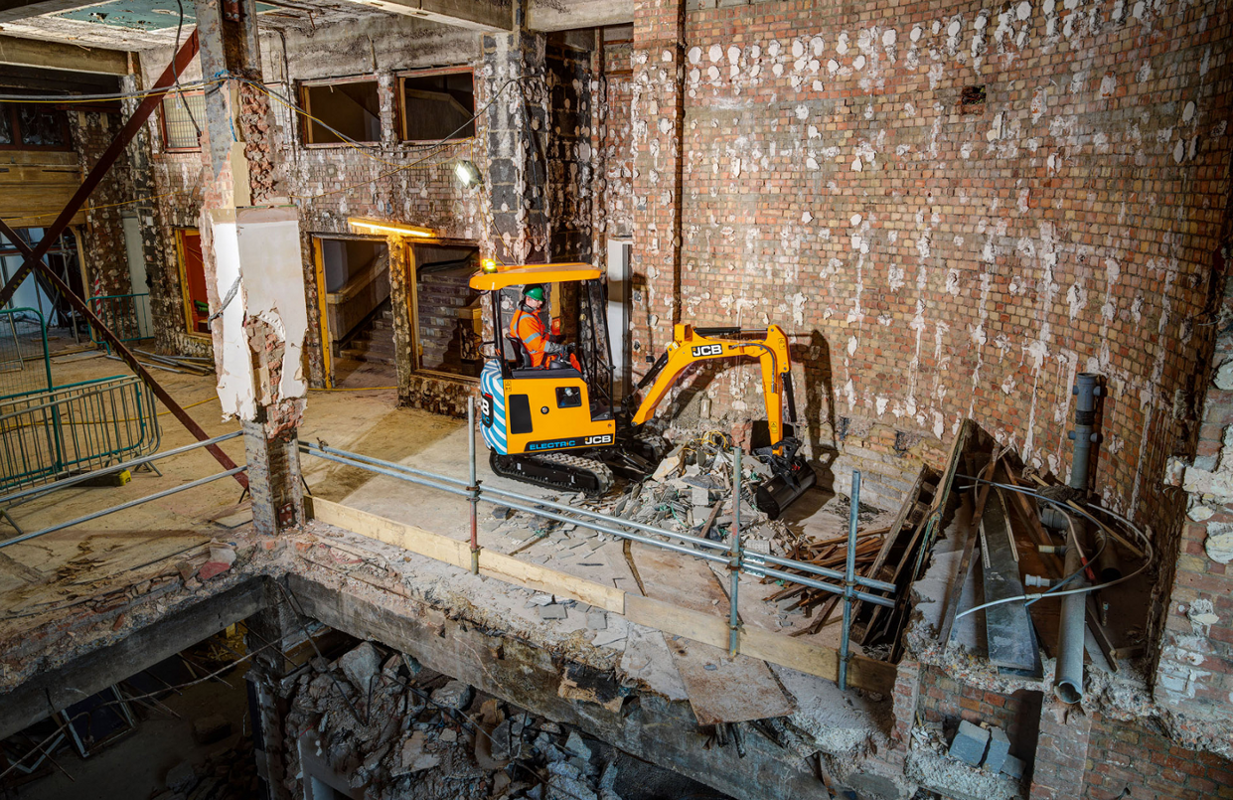
JCB – Digging deep
Once designed, the JCB engineering team was determined to test the little digger to breaking point.
“I was paranoid, the engineering team were paranoid, that we would let the business down if it wasn’t strong enough,” says Womersley.
He goes on to detail the rigours under which it was placed, in an accelerated programme of testing permitted by its size and zero-emissions status.
This included simulating work situations in JCB’s freezers and hot cells, in order to mimic minus 20 degree Norwegian winters and scorching summer temperatures in India, where the company derives significant revenue.
Despite being predominantly designed for urban use, the team ruggedised the product well beyond its intended habitat.
Tests run at JCB’s own private rock quarry, where it worked alongside giant earthmovers, helped validate the initial FEA analysis.
Twelve prototype machines were then sent out to key customers for beta testing, under the guidance of JCB chaperones from the firm’s Young Talent team, made up of recent graduates and apprentices.
They fed back even more information and observations from usage in the field.
Onboard, the mini-digger is almost identical to its tried-and-tested diesel twin.
Simple in design, the driver’s cab offers 270-degree visibility, perfect for working in confined areas, and can be fitted with an optional polyscreen for protection when doing demolition work.
“We want the operator to know it’s a digger.
It’s just like any other machine – but there isn’t a fuel tank indicator!” Womersley laughs.
A narrow 980mm overall width allows the mini-digger to squeeze into most buildings in order to undertake internal demolition or excavation work.
On the bottom, three single-flanged rollers on short pitch tracks ensure a quiet, smooth ride.
On top, the boom arm has its hydraulic ram positioned to reduce the risk of damage in confined spaces.
The machine is five times quieter than the diesel variant – almost eerily quiet.
This allows it to work longer hours without fear of causing disturbance, in proximity to buildings such as schools, hospitals and offices.
“There are no fumes and no diesel extraction required, crucial in indoor excavation, breaking and demolition works. It’s low-noise, perfect for urban environments,” Womersley comments.
The electric mini digger is now being used by archaeologists working undercover on an ancient burial site in London, as well as by the operators of the largest cemetery in Europe – locations where work needs to be precise and considerate.
Another customer is looking to use the JCB 19C-1E in the clean spaces of its food factory.
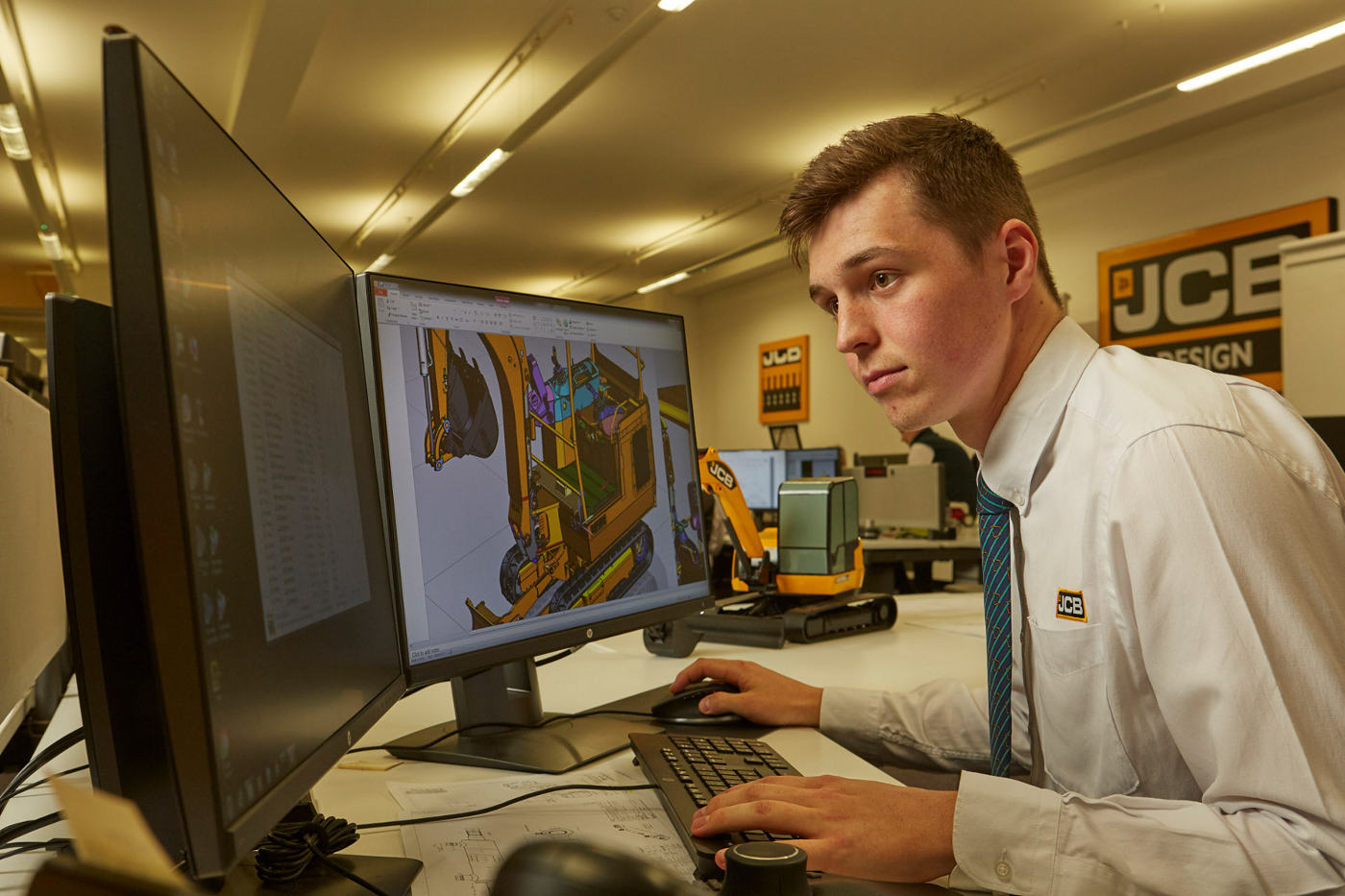
More to follow
The JCB 19C-1E has already been joined by a zeroemissions tele-handling truck, the JCB 30-19E Teletruk, and more electric vehicles are in the pipeline.
Future models are likely to push the design envelope further, Womersley suggests. Lightweighting – in particular, reducing the weight of the bucket end and simultaneously, the counter-balance needed at the back – is something that design tools could help with in the future.
More interesting still is the idea of battery energy recovery from machinery. With a lot of redundant mass being dropped down a hole when excavating, there’s the opportunity to recover some of that energy back into the power unit. This is an area that JCB is already investigating.
Womersley believes that the company is already ahead of the electric automotive crowd in the field of telematics.
All of its electric-powered machines, both those in testing and those already on sale, have JCB’s proprietary LiveLink system fitted.
This allows the company to track machine use and help it develop the next generation of vehicles according to its findings.
From the prototyping stages onwards, the engineers have used data from LiveLink to ascertain what an actual ‘day’s work’ really looks like, giving them new insight into battery usage.
This is not to say, however, that the company has given up designing traditional engines and drivetrains.
According to Womersley, there’s a bright future for ‘clean diesel’ engines, especially at what he calls “the heavy end” of JCB’s product line-up.
Through innovation and design improvements, JCB is leading the way on clean diesel technology to meet Stage V EU emissions regulations.
When vehicles go beyond a certain weight, or when they’re deployed on particular use cases, it often makes sense to rely on combustion engines.
But, he adds, “we’re working hard on making these as near to zero emissions as possible.” From Womersley’s words, it’s clear that efficiency is now a major focus across the company’s entire product line – and that the spark of electrification has lit up yet another phase of innovation at JCB.