Node Audio is aiming to make a big noise in the high-end audio market with its new Hylixa design. Stephen Holmes visits the UK start-up to learn how additive manufacturing is enabling it to reshape loudspeaker concepts
There’s a striking, sinuous flow to the form of Node Audio’s Hylixa loudspeaker. Almost every familiar element of a traditional loudspeaker is missing: the square edges, the boxy shape, the piano-black gloss.
Instead, Hylixa’s creators have built something far more shapely, more elegant, but with functional benefits firmly in mind.
There’s barely a flat surface in sight, all the better to allow the sounds from its passive, three-speaker set-up to flow around its surroundings unimpeded, creating the impression that the musician is right there in the room with the listener.
The 3D-printed speaker pod is perched on an aerodynamically rounded shaft. The first impression is of a product originating from the aerospace industry, rather than the acoustic field. Everything is anchored, meanwhile, by three squat stabilising feet.
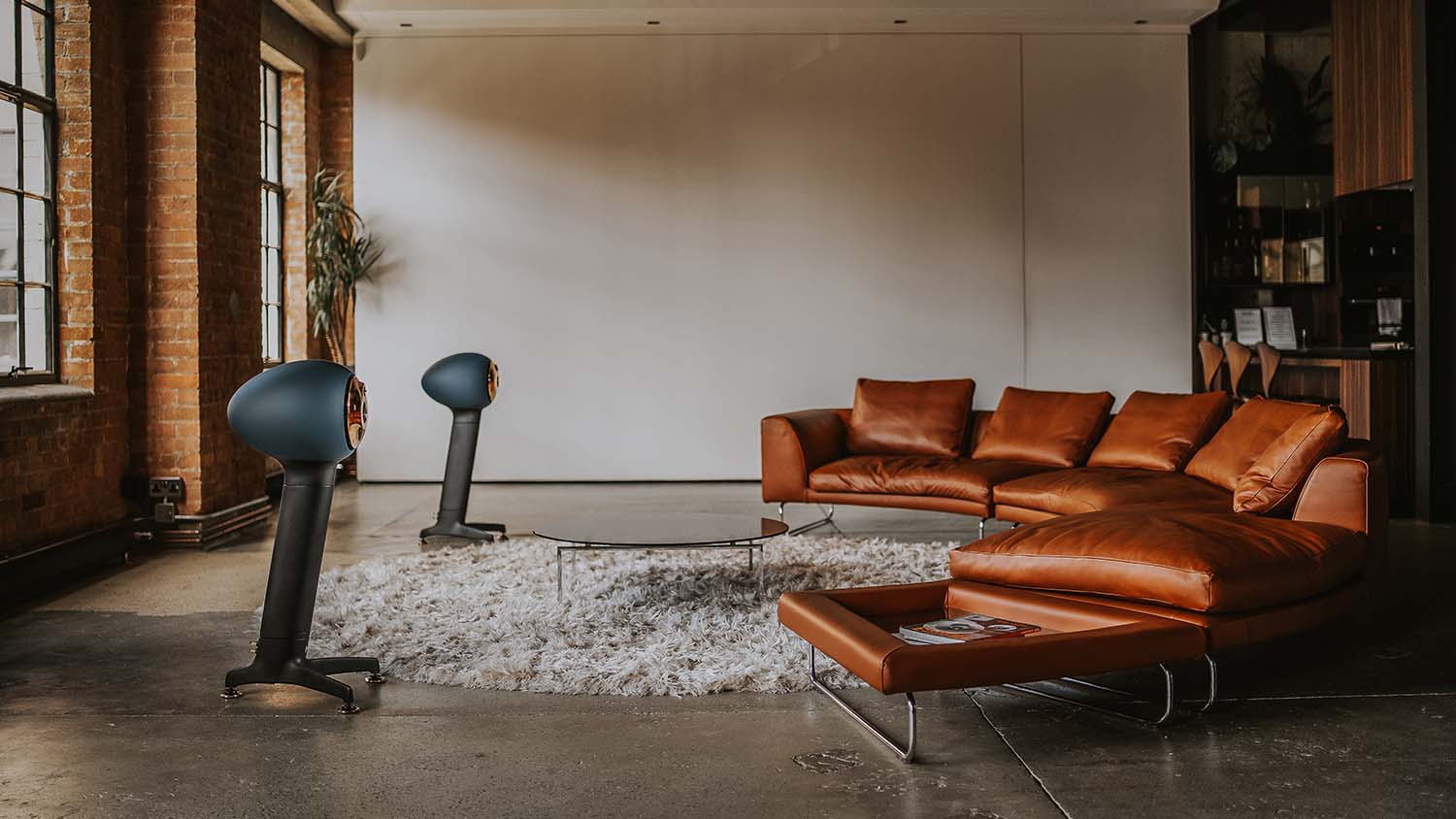
From an aesthetic point of view, a pair of these £30,000 speakers will certainly catch the eye in pretty much any room – but it’s the gargantuan sound they emit that will fill that space. That’s the result of Node Audio’s patent-pending internal design for the Hylixa, which is radically different from anything that has preceded it.
The rear-firing bass woofer channels through a freeflowing ‘transmission line’, where the rotational pressure of an inner helix-shaped chamber increases the effective length, extending bass performance dramatically. It’s from this chamber, incidentally, that the name Hylixa is derived.
Coupled with an acoustically streamlined cabinet, which delivers exceptionally low diffraction, the full sound spectrum reaches your ears at the same time, without the colouration generated by those box-like cabinets.
Node Audio – Origin story
The Hylixa design originated with company founders Ashley May and David Evans, already successful directors of design consultancy, Studio17.
Having developed products for the likes of homeware specialists Joseph Joseph and Fiskars for the last decade, they began work on the Hylixa concept as a side project. It was only when they consulted an acoustic engineer about their design, and saw how enthusiastic they were about the idea, that May and Evans decided to take it further.
The initial stages of that process focused on iterating the original designs and working with the audio engineer to hone the best shape and sound possible from the transmission line.
Traditionally this is done inside a box cabinet, by creating internal walls within that form a long path. However, by 3D printing the cabinet, Node Audio’s design team figured out they could create whatever shape would give the clearest sound. The resulting helix creates a very low impedance path because of its continuous round form, so air and sound both flow very efficiently around that path.
As Ashley May puts it: “There’s no reason why you can’t design something really beautiful that actually enhances the acoustics, rather than compromises them.”
The 3D designs for Hylixa took shape in Solidworks, allowing the team to send designs back and forward to the audio engineer who analysed the form in Comsol Multiphysics, running acoustic and vibration simulations on the cabinet design, as well as other FEA analysis to ensure structural stability.
“Once we had something that was proven in simulation, that’s when we started prototyping to see if it worked in real life,” explains David Evans.
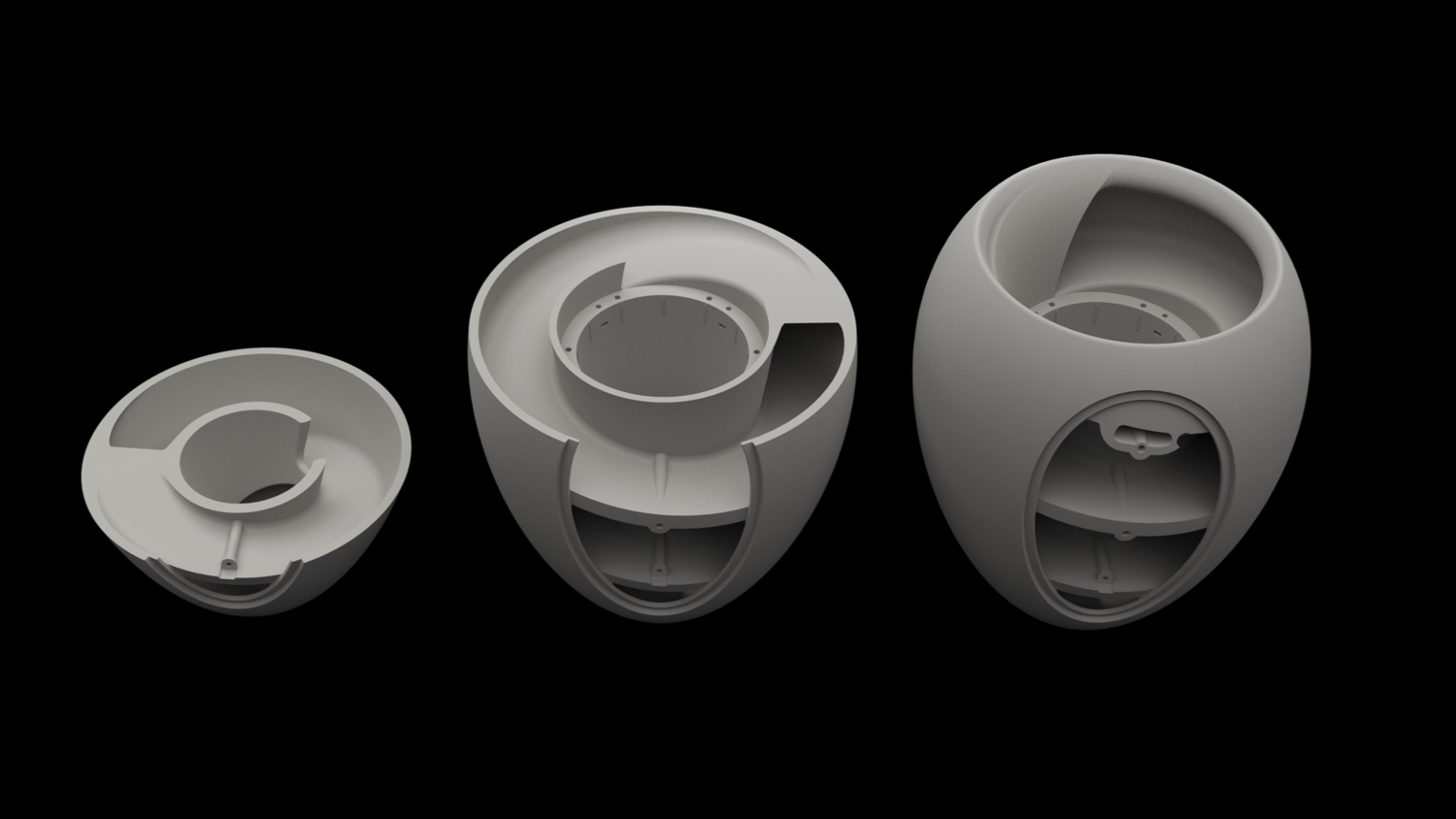
Node Audio – Innovation centre
Node Audio is headquartered on the ARCC Innovations campus, close to Cambridge. The heartland of British audio engineering, the site provides a collaborative workspace for start-ups, inventors and technologists looking to bring new products to life.
As part of its tenancy agreement, Node Audio has access to design software such as Solidworks, which is maintained by reseller Innova Systems, as well as a wide range of fabrication equipment, including onsite 3D printing using a 3D Systems sPro 60 SLS printer.
“Having access to something like this, and us being designers and understanding what’s now possible with technology like this. I think that’s where the product was born, almost.” says Evans. In other words, it was a unique opportunity to explore what they could achieve with this kind of kit and set-up, which would otherwise be out of reach because of the costs involved.
Each speaker pod is built to order, with parts nested together and created from 3D Systems’ glass fibre-filled Nylon material, DuraForm GF, which feels almost ceramic to the touch when holding a part this large.
May explains that, in acoustic terms, flat surfaces are generally a bad thing, since they resonate. “We’re able to eliminate that completely by using double curves throughout the entire 3D form, and it’s manufactured as a single coalesce piece, so there’s no fixings to resonate. This process ticks a lot of boxes, it really does!”
The material boasts excellent properties for speaker cabinets. “You can feel the density,” he says, “but it has a high resonant frequency, which means that when we play the bass frequencies through it, we’re not exciting the cabinet. It’s not resonating at the crucial operating band.”
One of the things that the team realised was that designing the product was one challenge, but the manufacturing process also had to be well thought-out to achieve a product of a sufficiently high quality.
“A good example is how, when these come off the 3D printer, it’s not a bad finish, but it’s not a high-quality finish that you’d expect from a premium product,” May says, assessing a part straight out of the depowdering unit.
Because of the torturous internal geometry, the team created a QA process to be absolutely certain that no unsintered powder is left inside the helix, where it could ruin the acoustics. Each cabinet is weighed against a reference model as it goes through the depowdering process. To check the inside is clear, an endoscopic keyhole camera is used.
“It’s a really important part of the process, and it’s really the only way we can be sure that there’s nothing in there, because there are slight variances in terms of weight and density of parts, depending on the [powder] build blend in the 3D printer. But we try and keep that tolerance as tight as possible,” says May.
The external surface underwent further work as the team strove for the highest-quality finish over several iterations. First, a protruding neck section was removed, leaving a purely circular form. The cabinet was then calibrated to be printed oversize, so that excess material could be turned back using the lathes in the ARCC facility.
The mouth of the speaker was tweaked to allow for an aluminium mandrel to be attached, allowing it to be easily mounted onto the lathe. The smoothed finish was then coated with a primer, several layers of paint, and then a lacquer that is subsequently polished back to a ‘pianograde’ finish.
“It just means that when the light falls on it, you get a nice, consistent, almost automotive quality to the surface,” reflects May. “It’s these processes that you need to go through to take SLS from a prototype process to a proper end-use part.”
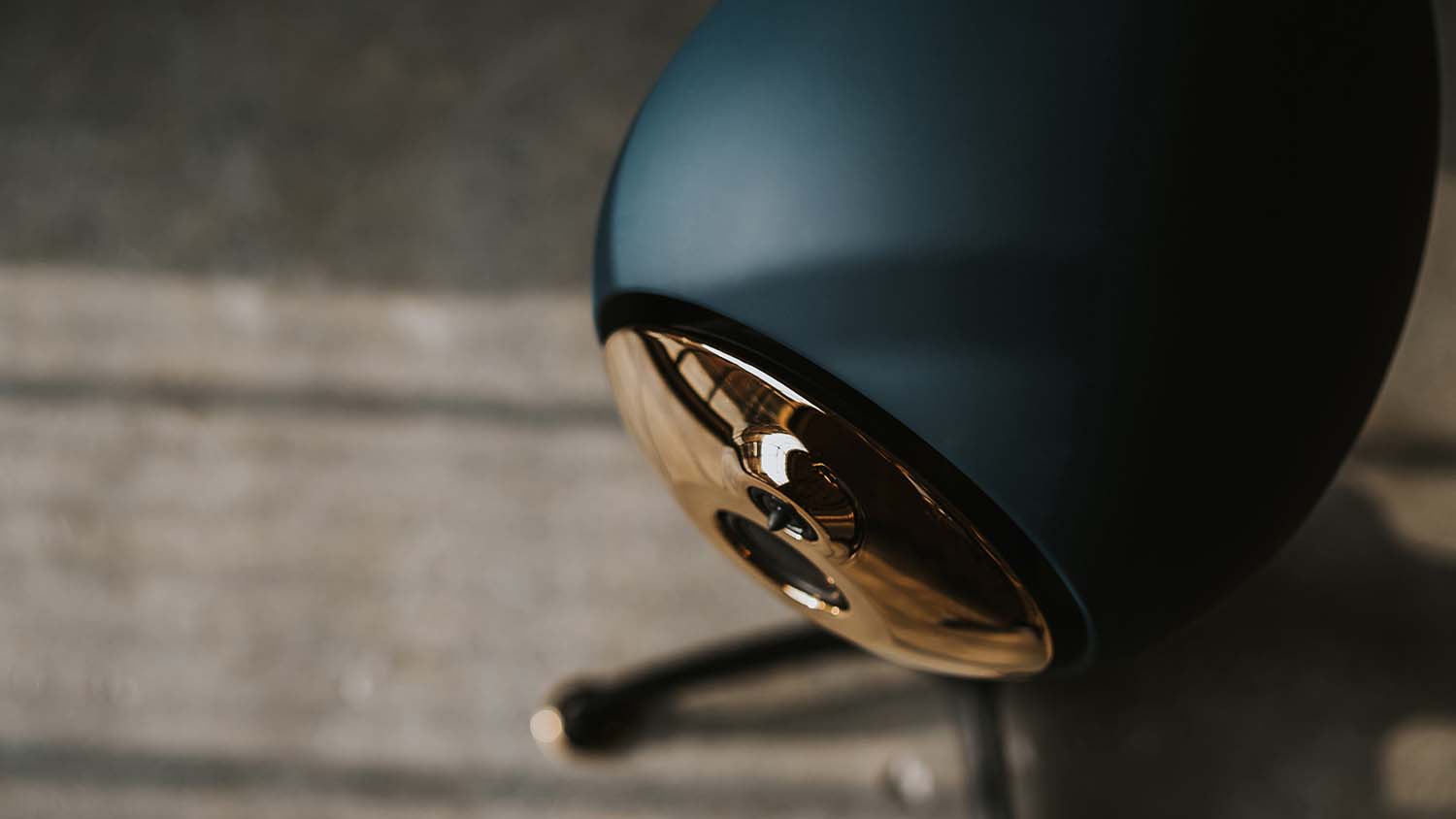
High fidelity
To push Hylixa to the highest possible level of acoustic fidelity, 3D printing is used beyond the speaker cabinet, too. Each of the speaker’s three specially sourced drivers are paired up in-house to ensure the balance of sound is close to perfect, with a custom 3D-printed surround added to help stiffen the flange, again in the interests of achieving the best possible sound.
The crossover – the electrical filter element of the loudspeaker that divides up the signal coming in from the amplifier to each of the three drivers – is also managed in a unique way. Traditionally, a crossover is built using printed circuit boards, with each component mounted on and soldered. But with Hylixa, Node Audio has instead packaged the crossover neatly into the structure of the stand, using HP MultiJet Fusion 3D printing technology.
“We’re maximising every detail, so we’ve taken this to the nth degree,” says May. “We’re using a 3D printing process to create the chassis and that removes any micro vibrations or resonance that you get through a PCB, which degrades the performance of every one of these components.”
He continues: “It’s a pretty rigid structure and every element is hard-wired, which essentially sounds better than a PCB.”
3D-printed wire runs and bays for each inductor create consistency within the structure, with the neat array forming a magazine that is loaded into the underside of the stanchion, sitting within the slender stand.
Says May: “We take great care to space all the inductors out, so there’s no electrical coupling in between the two. So the orientation and the location is really important. There are numerous small wins that we can get from using the 3D printing process, even on hidden areas that a customer never sees.”
For the parts that the customer can see, such as the splayed base legs, meanwhile, Node Audio had the HP 3D-printed parts extensively UV-tested to simulate the effect of daylight over several years.
Although the parts are all vibro-polished and dyed, the team found that customer-facing parts would still need automotive-grade paint applied to the outside to negate colour fading over time.
3D printed wire runs continue the length of the stand, helping keep the cables separate from each other and from the extruded aluminium outer. This controls the consistency of where the wires sit and avoids any minute degradation of the signal passing through them.
Assembly is performed in-house, using further 3D printing processes to build jigs and fixtures. Final touches, including the front aluminium baffle and two sets of feet (for either carpet or hard floor), are added.
Machined and electroplated locally, the aluminium highlights, combined with the range of paint colours available, increase the level of customisation for this made-to-order product. This enables users to adapt the appearance of their speakers during their lifetime to suit their living environment.
“We’re trying to create something of real beauty, where there’s no harsh edges. It’s quite sinuous and seamless, which is great for acoustics, because it doesn’t reflect sound. It’s ‘acoustically stealth’, we like to say!” May jokes.
By contrast, the final product experience for the customer is nothing like as covert, having been extensively thought through. With each purchase comes a glamourous accessory box, containing the adjustable feet, a custom spirit level to help set the speakers up and a book detailing the design and production story behind the kit.
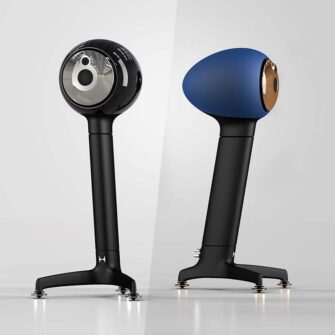
Way before they receive their product, in fact, customers are invited to visit the site, in order to see their speakers take shape and observe the production process they go through. In that respect, the experience is more akin to buying a luxury car.
If the customer is based further afield, and can’t make an in-person visit to Node Audio, they can work with the team online to assess colour and finish options. Here, the team uses Solidworks Visualize to create realistic 3D renders.
But the real end result is the sound that these speakers produce. To date, no customer has been disappointed, according to Evans.
“We’ve really impressed people. It’s been extremely different to what they’re used to seeing,” he says. The amazing sound produced often fools people into expecting to see a giant set of traditional speakers, he adds, “whereas we’re getting the same performance from something more elegant, beautiful and a lot smaller.”
The form of Hylixa was driven by the function, at the end of the day, he concludes. “But we also wanted to make something that looks as good as it sounds.” Job done.