Blending creative solutions with technical know-how, Lamp & Pencil is the go-to design firm for some of theatre’s most unique lighting and visual effects. We learn how the company’s use of in-house 3D printing has earned it rave reviews
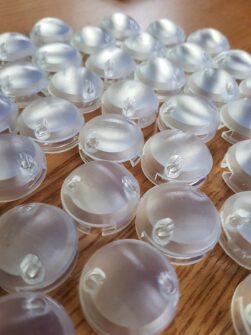
If you’ve ever sat in the audience of a theatre show in the West End or on Broadway, you’ll understand just how important a role lighting plays in shaping a story’s narrative.
It is critical for conveying the mood of a scene, helps guide the audience through an experience, and highlights the most important elements on the stage.
Although lighting and visual effects have long been an integral part of the entertainment industry, few understand the attention to detail and complex engineering work that goes into producing a first-class stage production.
This is where Lamp & Pencil fits in. The UK-based design and engineering consultancy builds bespoke installations for stage shows like Harry Potter and Les Miserables.
Founded in 2014 by engineer Robin Barton and designer Tamsin Higgins, the duo pooled their skills and love of theatre to form Lamp & Pencil. Barton had previously worked as an electrical engineer with experience in stage lighting from time at London’s Royal Opera House, while Higgins has previously worked as a product, furniture and interiors designer.
The requests they receive from productions can vary wildly. “It could be windows that glow, a chimney that smokes, a handheld prop that needs to light up or do something,” explains Higgins. “We always say it’s the type of thing nobody else wants to do. We’re the stupid people that say we’ll give it a go!”
Generally, a project will come from the lighting designer’s specs. “The lighting designer will specify an effect or a thing they want to achieve, and we will need to create the end result.”
If it’s a big West End show, Lamp & Pencil consults the stage designer’s drawings to understand the set and how an element needs to behave in a certain way. “We can’t really draw that up,” says Higgins. “So we tend to play with the technical first.”
Given the bespoke nature of most of what the company does, a lot of the work is research and development. “It isn’t a case of being able to just buy [parts] and they’ll do the job. We have to develop and design it, and I think that’s where a lot of people don’t necessarily understand the amount of work that goes into these projects.”
Critical to this is the team’s blend of creative understanding, married with the technical know-how, and its ability to balance the need to achieve an effect with how best to fit that into a production in a way that can be maintained and moved, all without impeding actors or scene changes.
Time to sparkle
One example of Lamp & Pencil’s recent work: a lighting project for a West End show, where an area of the set built from clear acrylic needed to have lights fitted to it that would twinkle, but with all the fixtures, fittings and cables invisible to the audience.
“They were quite strict on that,” recalls Higgins. “With the size of the LED, they needed to dissipate the heat, so I designed a little heatsink that then slotted into a hole in the back, and we used some cable that was clear on the outside and silver, so it disappeared into the acrylic.”
Lamp & Pencil developed a controller for the LED set-up, and things looked promising, until the lighting designer decided the lights needed to have a narrower beam angle.
“We couldn’t change the LED, because of what we were asking it to do, so we had to work out a way to bring that beam angle in,” explains Higgins. The team developed a clear lens cover for the LEDs that would blend with the set and could be produced in-house on its Formlabs Form 3 3D printer using clear resin.
“I sat down, did a bit of research, modelled up a series of lenses, printed prototypes, tested them to decide on the final one and then printed 100,” says Higgins. “From our point of view, being able to develop that inhouse is amazing!”
She believes that the better your CAD modelling skills are, the better you’ll understand what the 3D printer is doing, and the better the results will be. The team at Lamp & Pencil typically uses Vectorworks, which is widely used in the lighting industry due to Spotlight, a plug-in for stage lighting. As the company has grown, it has added Autodesk Fusion 360 and its Eagle PCB ability to its toolset.
For Lamp & Pencil, the process is less about presenting an idea on screen and more about manufacturing a physical prototype.
“We’d been talking about getting a 3D printer for a long time and I think the biggest thing was deciding what type to get,” says Higgins. “For me I decided that the resin printer was better than the filament 3D printers for what we needed. Things like the lenses, or specific things we needed to print, needed the quality of the resin.”
After consulting with UK Formlabs reseller Simply Rhino, the team took the plunge during the Covid-19 pandemic to order its Form 3, with lockdown affording the team additional time to learn and test the new 3D printer. As theatre productions slowly reopen, many with set updates and refreshes, Lamp & Pencil is ready to take on new projects without having to rely on the time schedules of suppliers. After all, the show must go on.