British defence, security, and aerospace giant BAE Systems has spoken about the increase in abilities added to its Factory Of The Future initiative.
The BAE Systems Factory Of The Future underpins efforts of the UK-led Tempest programme to meet the UK’s ambition to remain at the forefront of the Combat Air sector through multi-million pound investment and collaboration with more than 40 blue chip and SME companies along with academic institutions.
Based in Warton, UK, it brings together the latest advances in technology and manufacturing – blending Additive Manufacturing, co- and robots for assembly, as it looks to make next generation fighter jet production more flexible, faster and help to reduce costs.
Technologies inside the factory are already delivering benefits. The intelligent workstation, developed in collaboration with The University of Sheffield’s Advanced Manufacturing Research Centre (AMRC) and Fairfield Control Systems, is in use on the Typhoon production line.
It uses a system which recognises operators and automatically delivers tailored instructions using ‘pick by light’ technologies.
Intelligent machines and off-the-shelf robotic technology from the automotive industry have been modified to operate at the precise tolerances required for military aircraft, which are less than a third the width of a human hair on some of our programmes.
In addition, additive manufacturing technologies are being used in the production of Typhoon aircraft parts and assemblies.
According to BAE Systems AM operations lead Greg Flanagan, FDM-based 3D printing technology in particular is providing opportunities to decrease the up-front cost of tooling for new products.
This is especially so with items such as drill tools, repair tools and other development tools that are often needed in small numbers.
As a result, the BAE Systems Factory Of The Future has installed its fourth Stratasys Fortus F900 3D printer through experts Laser Lines, as a result of witnessing ‘significant cost and lead time reductions’ against those of traditional manufacturing methods.
“Our Factory of the Future programme is all about driving the future of fighter aircraft production with disruptive technologies and we’re working closely with our suppliers and wider industry to meet the challenges the UK Government has set out to us,” said Flanagan.
“Stratasys FDM additive manufacturing plays an important role in this initiative, as it helps us meet our overall company objectives to reduce costs and time-to-market.”
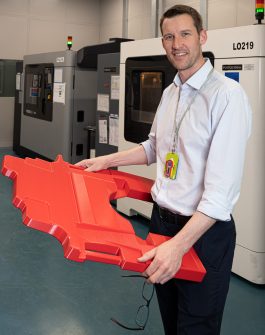
BAE Systems’ latest Fortus F900 installation will not only increase 3D printing capacity, but also help exploit new 3D printing materials for tooling applications – including carbon fibre-filled FDM Nylon 12CF.
The defence giant has found great success in identifying traditionally manufactured applications that can be enhanced, or in some cases replaced, with high-performance 3D printing materials.
This includes utilizing durable ABS and ASA materials for a range of aircraft ground equipment, such as cockpit floor covers for the Typhoon fighter aircraft.
“With our F900, the thermoplastic covers can be made much faster than traditionally manufactured versions and are a lot lighter and easier to move for the ground crew, so it improves efficiencies within the maintenance, repair and overhaul process,” added Flanagan.
“An added bonus is that they can be printed in red – the colour of all ‘remove before flight’ components.”
BAE Systems and the UK’s aerospace, defence and security sector is world leading, employing hundreds of thousands of people and supporting many more jobs through the supply chain across the country.