In October, 2008, the 59 senior motoring journalists from 23 European countries who make up the jury for the annual European Car of the Year (COTY) awards chose seven finalists from a total of 37 contenders for the latest awards.
After the points allotted by the jury during the final round of judging had been counted, the Car of the Year 2009 award went to the brand new Opel/Vauxhall Insignia from GM Europe. The Insignia gathered a total of 321 points, beating the new Ford Fiesta into second place by the narrowest of margins and the Volkswagen Golf VI into third place.
An important contributing factor to winning this award was the high perceived quality of the Insignia. Perceived quality is a key component of brand identity. It describes the first impression a customer gets regarding the look-and-feel of a product, without regard to its functionality.
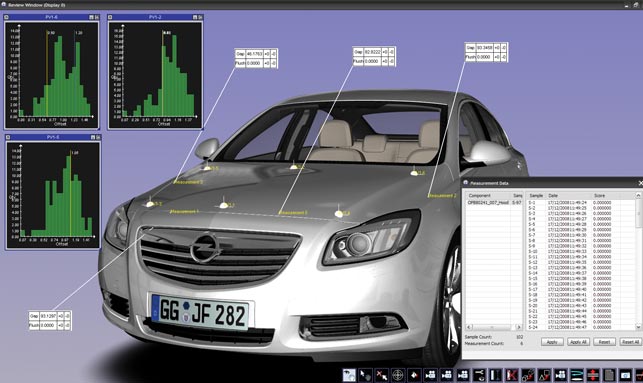
In the later design & validation phase of the development process attention was geared towards the calculated gap and flush dimensions
Key to GM Europe’s success with the Insignia was the use it made of advanced manufacturing variation simulation and visualisation software during the car’s development. Known as aesthetica and developed in the UK by Icona Solutions, the software was used from the early concept design stages of the project, enabling the various design, engineering and manufacturing disciplines involved in the project to understand the manufacturing constraints and to agree on gap and flush conditions and manufacturing tolerances as early as possible in the overall design and development process. This made it possible to achieve the highest possible perceived quality in the final vehicle without negatively impacting its development and manufacturing costs.
Dimensional management
Ten years ago, as part of its focus on quality, innovation and affordability, GM Europe created the dimensional management department at its International Technical Development Centre in Rüsselsheim, Germany.
The International Technical Development Centre is at the heart of engineering for GM Europe. Within it, the dimensional management department, led by Edgar Lossnitzer, who has defined the new perceived quality processes, is responsible for the management of tolerances over the entire vehicle development cycle.
“Dimensional quality is already defined at Opel at the start of a project in a tracking schedule known as the dimensional technical specification, or DTS,” says Lossnitzer. “Dimensional quality is tracked during the entire development cycle, all the way to production. In the DTS, all gaps and offsets visible to the customer along with their nominal values and allowable deviations are specified,” he explains.
“Nevertheless,” he adds, “one of the problems we faced was that too many gaps were falsely interpreted through the tolerance simulation. This often led to controversial discussions in the DTS setting meetings, as well as in follow-up meetings, until a physical model could be produced for review. This costly and time-intensive process resulted in agreements and decisions being made late in the process, with the result that there were often additional costs involved in implementing the required design changes.”
With a view to overcoming this problem, Lossnitzer and his team set out to fully investigate how, or if, 3D visualisation software could help in the dimensional management process for the Insignia programme. This brought them into contact with Icona Solutions, developer of the manufacturing variation simulation and visualisation software solution, aesthetica, and Icona’s business partner in Germany, Casolute.
Icona Solutions’ aesthetica software is unique in that it applies tolerances and component deformations directly to the product’s 3D CAD geometry. These 3D models can then be visualised, in real time, using different light sources, colours and materials. This is unlike traditional visualisation software, which can only visualise a virtual product in its perfect, as-designed nominal condition. With aesthetica, a realistic representation of the vehicle as it would appear at various points within the range of assigned tolerances can be produced at a very early stage of the vehicle development. This enables perceived quality reviews to be carried out, in which fit and finish problems can be spatially represented in real time and solved immediately.
Perceived quality studies
When Opel made the decision to implement aesthetica it was at the very early stage of the development of the Insignia. Superior design, vehicle dynamics, safety and comfort, as well as superior aerodynamics and appearance (gap and flush) were all expected from this vehicle.
With the introduction of aesthetica, design review meetings began to be routinely carried out in a virtual reality (VR) room in order to show the meeting participants the three dimensional model without it being necessary for any physical models to be built.
Aesthetica can be used in every phase of the development process to accurately and visually present the influence of tolerances on perceived quality. The parameters used for the simulations are based on the design and manufacturing data, including the material, fastening scheme and the tolerances. Complex deformation effects such as arching, bending and distorting are represented, thereby allowing the root cause of problem areas to be identified. These parameters can be changed freely to enable all possible solutions to be tested in order to achieve the highest possible quality in the final product.
The first use of aesthetica on the Insignia project began at the early concept stage. As soon as the first styling data was released, the first aesthetica models for the interior and exterior were generated. From this point the digital model would be continuously updated to accommodate styling changes and/or the development progress. This process continued through the design & validation phase up to the final confirmation and improvement phase.
Considerable resources have been saved by eliminating the need for physical validation models
Early engineering used the digital models in order to visualise the effects of the different tolerances and if necessary, to kick off changes at a time when the cost of change was minimal. aesthetica made it possible for the calculated variations and their effects to be visualised in 3D. Alternatives could be brought directly into the aesthetica model and the effects of technical implementations could be shown immediately in the 3D representation.
For the interior the concentration was placed, above all, on the area visible to the driver and passenger in order to allocate the priorities for the tolerances in this area. This allowed areas that are difficult to see or aren’t seen at all to be used to compensate for build tolerances. Overall, additional attention was given to “forgiving design” in which design elements and their optimisations were evaluated in 3D in the VR room before being implemented in physical products.
In the concept phase of the new vehicle development process it was crucial to include key stake holders in meetings in order to present the new product, as well as all tolerances and the effects of those tolerances. As a result, very early in the development process the target specifications could be defined based on realistic images. Decisions were able to be released for product development simultaneously, thereby avoiding future surprises, because agreements were more quickly obtained.
In order for discussions in the VR rooms to be completed as efficiently as possible, a type script was generated beforehand. With this, the area of the vehicle, perspective, material combination and light sources for the visualisation were defined and stored in aesthetica. As a result, every condition could be quickly reconstructed. The new points and desired notes from the meeting could also be directly entered and stored in the same manner. This allowed new ideas to be discussed immediately and either pursued, or rejected, partially eliminating the need for physical models and resulting in cost and above all, time savings.
Depending on the phase of vehicle development, different goals were pursued in these meetings. Here the 3D visualisation capabilities of aesthetica were indispensable because, in the absence of a physical vehicle, no conclusions could have been reached otherwise.
This was especially so in areas of the vehicle in which many components interface with each other, for example on the boot lid and the front end of the vehicle, as well as the area where the dashboard and door trim meet. In the development of the Insignia Sports Tourer, this area was investigated with aesthetica and its “Gap- / Flush- Fitting tools”. Using this, different possibilities for gap and flush could be judged until an image representing an optimal combination could be found.
In the later design & validation phase of the development process attention was always geared towards the calculated gap and flush dimensions. The results of these calculations were based on the assembly processes, component geometry, component tolerances and assembly tolerances. For visualisation, separate interior and exterior models were required because the development phases started at different times.

Design elements and their optimisations were evaluated in 3D using VR on a powerwall
As a rule, only partial models were generated in the interior area. These models included the front door trim, instrument panel and the centre console. In order to observe these areas from the viewpoint of the driver and/or passenger, information from the RAMSIS human models was also used in these models. Additionally, within the aesthetica model, rotation points were set in the position of the eyes in order to evaluate the view in all directions.
With this, sensitive areas could be identified and the required focus could be applied to the resulting images. Moreover, this avoided a situation where certain areas were defined as problematic as a result of being evaluated from unrealistic views.
In the exterior area, the tolerance calculations that were categorised as critical were visualised on the Powerwall in the VR room using the “Gap- / Flush- Fitting Tools” of aesthetica and presented to the decision makers. This provided a great advantage because the meeting participants easily could see how large the adjusted gap dimensions were.
As the models became more advanced further attention could be applied to elements such as visible structural items like screws, rivets or ribs within the gap, clip connections of components within the visible area, visible sub-materials such as sealing foam or glue, and elements visible through transparent components such as headlamps. This all helped to improve the overall visual appearance, or perceived quality, of the final vehicle.
Real benefits
“As a business that has actively integrated dimensional engineering into the vehicle development process for more than ten years, Opel was looking for a tool to support decision making,” says Lossnitzer.
Icona Solutions’ aesthetica software was developed as a visualisation tool that enables vehicles – and other products – to be developed in a cost efficient and effective way. Although Lossnitzer acknowledges that some people were initially critical of the high investment needed for the software and 3D visualisation on a Powerwall, he points out that once it became clear how easily concrete decisions could be made, they were convinced of the value.
Summing up the benefits, Lossnitzer states, ”Since introducing aesthetica into Opel there have been no more long-winded and time-consuming discussions regarding a few tenths of a millimetre. Communication to management of necessary changes has improved, decisions are made faster and as a result, development costs are saved. Considerable resources have been saved by eliminating the need for physical validation models, which together with the time savings have more than compensated for the acquisition costs of the software.”
www.iconasolutions.com
Advanced manufacturing simulation and visualisation software proves rewarding for GM