Global toy company Mattel is on a mission to empower the next generation with toys built to the highest standards of modernity, safety and accessibility, designed with the aid of innovative digital tools
If product design is about creating objects to make people’s lives easier, and more efficient or enjoyable, being a toy designer is about creating dreams. And not just for the children.
Aware of the power that toys hold to inspire, stimulate, and empower future generations, the international toy manufacturing company Mattel is investing in the latest design technologies on the market, to make sure its products are designed at the highest standards of efficiency and modernity.
Jack Peach, the lead innovation engineer at Mattel, has been working to help kids and families explore the joys of childhood and make the most of their toys, for the past 15 years.
Throughout the process, Peach and his team employ a mix of CAD, modelling, and simulation software, namely Creo and Solidworks for the manufacturable solid modelling and engineering tasks and Z-brush, Maya and Blender for the surface styling.
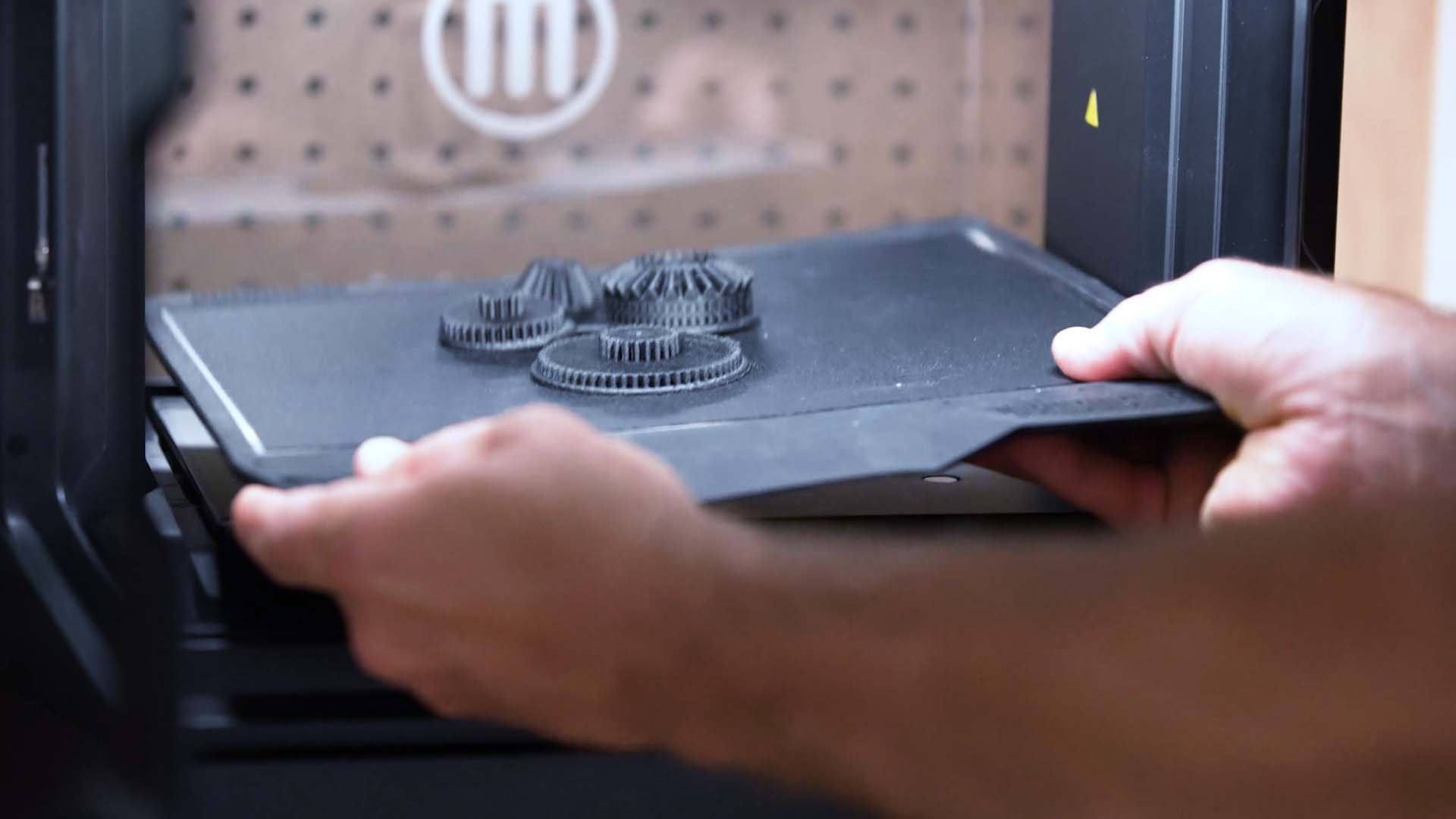
Flexible workflow
While working on one of his latest projects, the Sooth and Glow Rainbow sound machine by Mattel’s subsidiary Fisher-Price, Peach said, AM really upped the game.
As he explains, it is key for the team that the design process is as flexible and iterative as possible from the very beginning: “Brainstorming and concept sketching is where it all starts. Minimal deco changes to last year’s products might be approved with visuals in the digital space. But if we’re trying to prove out a mechanical function and feature or appropriate sizing for a child, fabricating a model is essential.”
The prototype can, in fact, reveal unforeseen issues and or help the team come up with new features to elevate the product, that they wouldn’t have seen in CAD. In order to produce prototypes, the team has selected MakerBot Method and Method X 3D printers.
“With a 3D printer, you don’t have to re-fabricate the entire prototype by hand,” continues Peach. “You can make a few adjustments digitally, send it to the printer, and have a new part printed quickly. This process makes modifications, testing, and reviewing so much easier and quicker.”
Designed to calm the baby with soothing music, sounds and warm, soft glowing lights, the Sooth and Glow Rainbow machine is designed to be used by both adults and, as the babies grow into toddlers, to allow them to interact with it autonomously.
The rainbow-themed tabletop machine offers 15, 30 and 45 minutes of soothing nature sounds, white noise, and a specially designed Ready, Settle, Sleep playlist.
Mattel innovation team led by Peach was tasked with supporting the design and development of the initial prototype to explore the physical size and user interface. “When developing a prototype, we aim to get to the most effective representative solution as quickly as possible,” he says.
“In this case, our prototype was made from hand-cut thin wall stock styrene, paper was used as a light diffuser and a length of serial RGB LEDs were controlled with a demo circuit board.”
After a few rounds of adjustments to the geometry and electronic design to meet value and cost targets, the designers and engineers in the team would finish developing the production geometry and a physical model would be printed for evaluation.
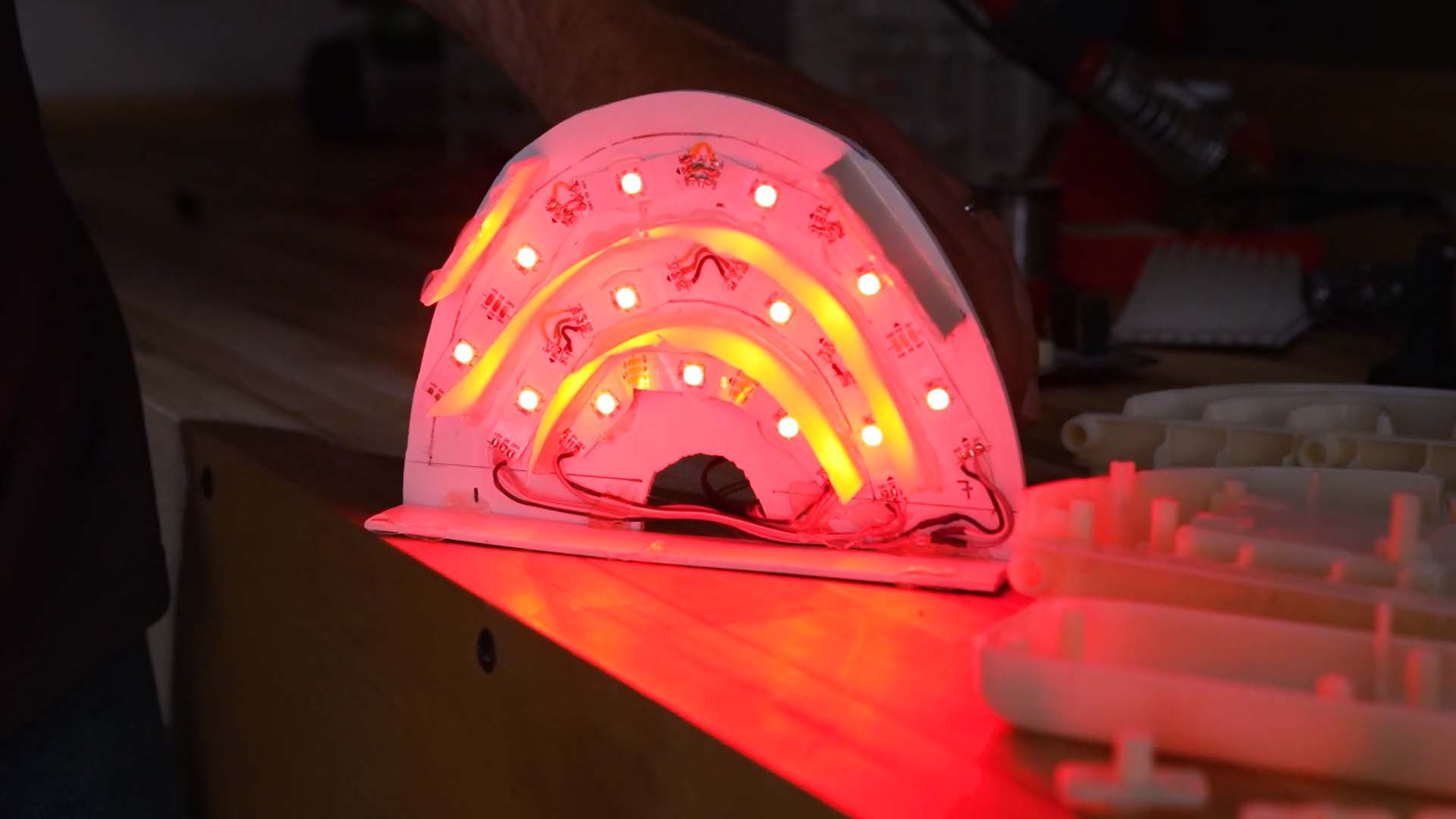
Game-changing tools
Before having the MakerBot 3D printers at his fingertips, Peach relied solely on the machine shop at the office for prototyping and, since the space would be shared with other teams, parts could take several days to be ready. Every iteration of the original design would cause massive delays, limiting both productivity and design freedom.
“Having a high-quality desktop 3D printer in-house opens new doors, allowing me to fabricate and test mechanical functions sooner, sometimes shaving off days,” says Peach.
“Complex parts and assemblies are often ready overnight, ready for review with a cup of coffee in the early hours of the morning.”
Since the MakerBot 3D printers are mostly used to print early prototype models to test electromechanical functions, Peach and his team selected materials that can withstand hundreds of cycles.
Recently, they started using ABS-R for housings and structural features due to the material’s high impact resistance and durability, and Nylon Carbon Fibre for gears.
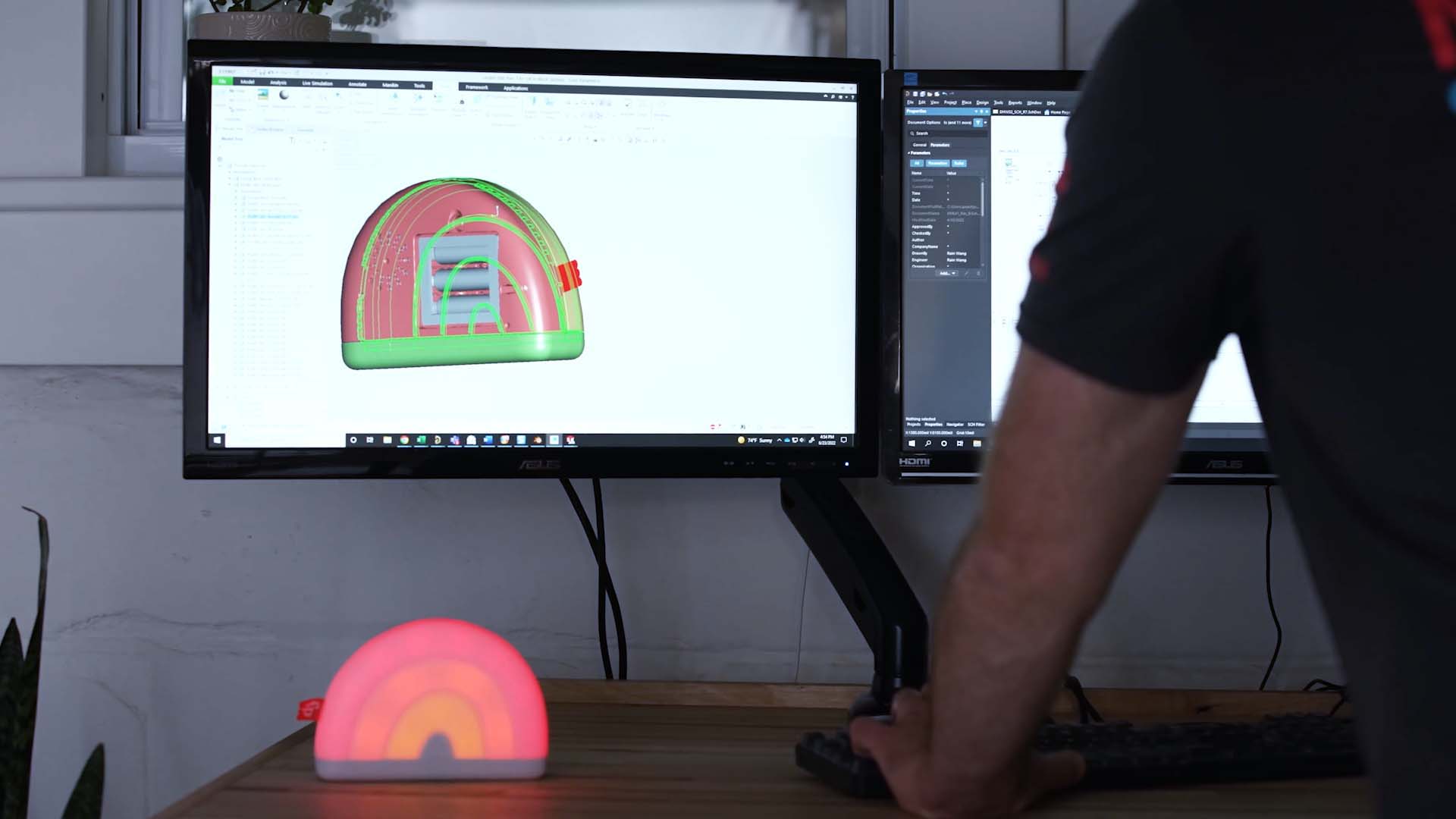
Physical prototyping is not the only technique Mattel’s innovation team employs to test a design. One of the most challenging elements to achieve, says Peach, was creating uniform lighting.
The innovation team at Mattel used Blender to realistically visualise the lighting effect. During the development process, they use its built-in LED light effect simulator to demonstrate the changing colour patterns of the LED.
Both simulation and AM helped Peach and the team reimagine the way they design for the toys and entertainment industry.
“Being an inventor, I’m most excited to see the sparkle in a kid’s eye when a toy does something unexpected, something magical. It’s a shared experience driving imagination at their level and mine, encompassing ‘What if? Why Not?’,” he says.
Those ‘Why Nots’ and ‘What Ifs’ are part of a new, innovative, more flexible workflow, which allows Peach and his team to visualise what the final product will be like in the early stages of production and imagine how children will interact, play and peacefully dream thanks to it.