Modern predictive models show that improvements in tennis rackets – which primarily focus on reduced mass and increased structural stiffness – allow a player to serve 17.5 per cent faster using modern equipment compared to what was available in 1870.
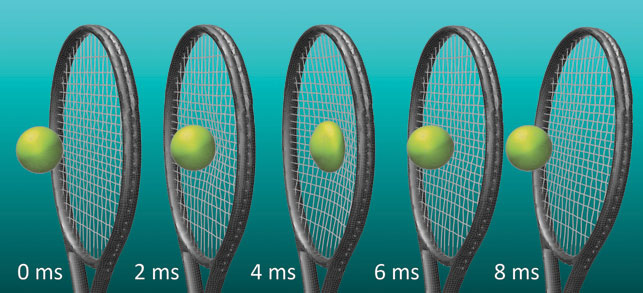
Image sequence showing a ball impacting perpendicular to the face of a freely suspended tennis racket
Making further improvements in rackets requires more complex and less obvious changes. This includes the coefficient of friction (COF) between the strings and the ball as well as the position of the racket’s balance point.
Search for a better racket
A team of sports engineering researchers at Sheffield Hallam University have developed models with ANSYS LS-DYNA software that accurately simulate ball-on-tennis racket impacts.
These models are being used to investigate the individual and combined effects of many different design variables and to develop insights for improving the design of tennis rackets produced by Prince Sports.
In simulating a tennis ball against a racket, conditions were designed based on an elite player’s typical topspin groundstroke.
The racket impact was assumed to be at the centre of the stringbed, because elite players typically hit the ball in this position.
The racket model had a mass of 0.348 kg, a balance point located 0.324m from the butt and a natural frequency of 135Hz, all representative of an International Tennis Federation-approved racket.
Researchers scanned a racket with a laser to produce a surface model that reflected the geometry of a real racket.
They used a linear elastic material model for the racket’s frame, which was meshed with 27,410 shell elements.
The racket model included an interwoven stringbed that had a linear elastic material model.
The ball model consisted of a felt cover and rubber core, with an airbag replicating internal pressure. Prior to generating the racket model, the ball model’s separate parts were independently validated against experimental data.
In the racket model, ball-to-stringbed contact was defined using the automatic surface-to-surface contact algorithm.
The research team evaluated the COF at 0.0, 0.2, 0.4, 0.5, 0.6, 0.7, 0.8 and 1. The simulation projected the tennis ball onto an initially stationary, freely suspended racket.
Comparing results
Engineers compared simulation results to the International Tennis Federation’s custom racket impact machine, designed to simulate nonspinning impacts between a tennis ball and a racket at a range of velocities and locations on the long axis of the stringbed.
Previous studies with a highspeed video camera demonstrated that this machine provides comparable results to a freely suspended racket.
The model was in good agreement with experimental data for a range of velocities and impact locations.
Once the model was validated, researchers used the results to gain a better understanding of the physics involved in the racket’s performance. Simulation provides far more insight and results than can be obtained from physical testing.
The analysis showed that a tennis ball typically goes through three separate phases during an oblique impact: sliding, overspinning and rolling.
Improving racket design
Researchers used simulation to investigate the effects of changing the COF between the strings and the balls. The results showed that with low rebound angles (relative to racket face normal), the COF did not have a major impact on the ball’s rebound characteristics.
Examination of simulation results showed that the ball was effectively rolling off the stringbed, so COF made little difference.
The COF has a larger impact if the ball is sliding or overspinning on the racket at the end of the impact.
The ball is less likely to roll during the impact if the inbound horizontal velocity or the backspin is increased. The ball is also less likely to go from overspinning to rolling during an impact if the COF is low.
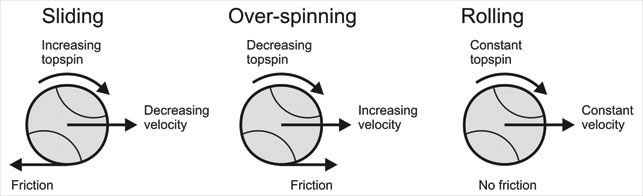
Three stages of tennis ball impact
The team conducted simulations with an impact angle of 40 degrees to determine the amount of topspin that the ball would rebound with when the COF was 0.2 and 0.6. The rebound topspin was 33 per cent higher when the COF was 0.2 because the horizontal force reversed direction approximately 1ms later in the impact.
This demonstrates that the ball is likely to rebound with more topspin from a low-friction stringbed than from a high-friction stringbed if the inbound velocity, angle and backspin are all large.
The ball will have the maximum possible rebound topspin if it rebounds from the stringbed at the instant at which it starts to overspin.
These results are significant because of the important role played by topspin in tennis. Topspin causes the ball to curve downward as it travels in the air, making it possible to hit the ball harder yet keep it inbounds.
Putting the results to use
The results of this and other studies of tennis rackets using ANSYS LS-DYNA have been employed by Prince Sports, which sponsored this research.
The tennis equipment manufacturer has begun making low-friction strings based on the results of this study.
The Centre for Sports Engineering Reserach is currently performing additional studies to evaluate other aspects of racket design.
For example, looking at the effect of racket design on a player’s potential to suffer from tennis elbow and other injuries. One of the causes of tennis elbow is believed to be a torque on the elbow generated by the racket; researchers will look at how the racket can be designed to reduce this torque.
Ansys.com | shu.ac.uk/research/cser
Tom Allen is a sports engineering researcher, Centre for Sports Engineering Research at Sheffield Hallam University
Simulation models developed with ANSYS LS-DYNA software improve tennis racket design
Default