Shocking stuff
Designing a product for military, law enforcement and consumer use is a hard task, but when that technology can incapacitate a human, the process is much more than point and shoot.
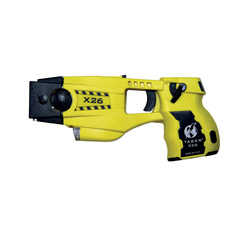
The X26 Electronic Control Device (ECD) from Taser International uses a cartridge of compressed nitrogen to deploy two probes that attach to the body of an assailant and transmit electrical pulses along its wires
The X26 Electronic Control Device (ECD) from Taser International uses a cartridge of compressed nitrogen to deploy two probes that attach to the body of an assailant and transmit electrical pulses along its wires. The pulses, which can penetrate up to one inch of clothing, affect the sensory and motor functions of the peripheral nervous system.
Variations of the X26 are being wielded on the front lines in Afghanistan, in police forces in town centres, and even legally in the hands of ordinary civilians across 43 states in the US.
All this makes its appearance, durability and the thought behind its mechanics an extremely interesting weapon.
“The unique aspect of the Taser X26 design was to maintain firearms mode of operation and features that officers are trained on [safety and trigger positions, sighting system] while designing an electronic control device product not to resemble any firearms in the market,” points out Steve Tuttle, VP of Communications for Taser International.
Most people will not have seen an X26 close-up but the dimensions are palm-sized, 60 per-cent smaller than the previous version, but still packed full of the complex electrical componentry. As Tuttle explains: “Generating and containing the necessary electrical energy and pulses required to achieve Neuro Muscular Incapacitation in a human safely and effectively,” was the hardest task to achieve.
The team works within AutoCAD and SolidWorks to transform original sketches and ergonomic foam models into 3D CAD data, with drop test simulation done inside Ansys and CosmosWorks. Parts are rapid prototyped in order to verify the design of specific components, such as the mechanism for the cartridge, before providing a pre-tooling release.
The diversity of its application, and its ability to resolve conflict with the greater reduction of death make this a truly modern weapon.
Hunting season
Bowhunting brings to mind images of Rambo stalking through the forest on the set of a Hollywood blockbuster, although the reality is much different.
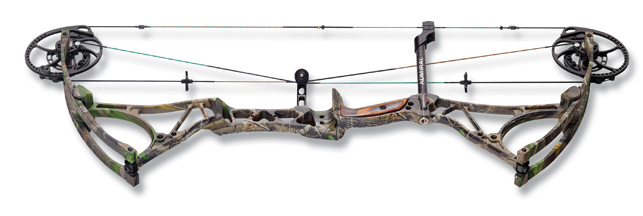
Bowtech uses non-linear solvers to simulate the behaviour of its high-deflection bows
The sport of hunting with a bow is incredibly popular in the US, where modern technology continues to advance the pastime. In contrast to a rifle hunter, who can shoot targets over 200 yards away, archers are restricted to taking shots from 20-30 yards, a distance that depends upon individual ability, the target, the bow setup, and the weather.
Bowtech’s latest bow, the Admiral, is a lightweight, durable weapon, reliant on cutting edge materials, dynamics, and ergonomics in order to operate at extremely high speeds in near silence.
Sketching was transferred into SolidWorks to layout the assembly of the model, incorporating modern technologies vital for a smooth draw-back motion, and the reduction of vibration and noise.
“Somewhat unique to our industry,” says Craig Yehle, head designer at Bowtech. “Is the bow’s limb, which is responsible for storing the strain energy used to propel an arrow at speeds well in excess of 300 feet per second.” Built from high-grade fibreglass they are analysed using DDS Simulation Premium with nonlinear solvers.
Non-linear solutions are required because of the high deflection values of the bow. “The trick here is to bend the limb in the software and optimise the stress distribution throughout the component,” explains Craig. “This, in turn, maximizes the strain energy that can be stored in the component without exceeding the material’s limits.”
Rotary club
Having ushered in a new way of fighting during the Vietnam War, the helicopter now plays a key role in wartime and peacekeeping operations, and the Agusta Westland Lynx is one of the most modern incarnations.
Its crew operates within one of the most advanced environments devised by engineers, and flying at over 200mph into direct conflict situations, search and rescue missions, and even anti-submarine warfare scenarios, it is vital to have essential controls at their fingertips.
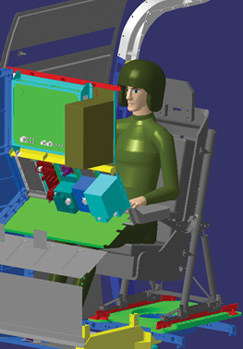
Digital manikins form an essential part of the cockpit design process at Westland Lynx
To help with the correct ergonomic positioning of the various equipment, switches and dials in the cockpit and crew areas, the design team makes great use of digital human manikins. Russell Bond, human factors engineer at Agusta Westland, points out that this is key to adapting to a more sophisticated working space as technology advances. “Using Delmia V5 Human we optimised the design taking into account the most frequently used apparatus in relation to minimising operator’s negative or extreme posture.”
This was done across a full range of body types and sizes, with vision assessment also key to the process. “The software allowed us to measure the relative efficiencies of various design layouts and to accurately assess body types that would prove unsuitable for the design,” says Russell.
“Using digital human manikins in conjunction with digital 3D Catia helicopter models it is possible to analyse the man-machine interface and assess human performance within the design. Questions of visibility, task performance, physical accessibility, maintainability and other factors are investigated.”
The end result has all the ergonomic benefits that allow a crew to operate with ease in the most pressured situations. “They can be sure, through analytical feedback, that their designs are on track and optimised allowing pilot and crew to function to their best capability,” concludes Russell.
The advanced design technology used in some of the most effective weapons