Tired of automotive companies playing it safe with interior design, Formation Industries took a more audacious approach when it came to its striking new McLaren Senna seat. DEVELOP3D spoke with founder Chris McGee and his team about the project
Chris McGee, CEO of design and product development company Formation Industries, is baffled by the beautiful but dull interiors of many of the world’s most exclusive supercars.
“Why would you have this ridiculously expensive car, and when you get in, it’s incredibly uninspiring?” he asks. “Everyone else gets to appreciate the beauty outside, but you’re just sat in there.”
In response, he’s been working on his idea for a complex and multifaceted automotive interior for over five years. The end result is a perfectly smooth seat, its geometric pattern a full-frontal visual assault limited only by the colours of the material.
Formation Industries has carried out many projects in the automotive interiors world, but shackled by non-disclosure agreements and hampered by manufacturers’ guidelines, the company decided to really break out with its latest project and push back the boundaries of what was possible.
In collaboration with D-Class Automotive, a company specialising in crafting bespoke car interiors, McGee and his team set about creating a car seat that would showcase what they believe represents the future of luxury car interior surfaces.
The idea was to create not just a concept design, but also an entire process for a quality product that can quickly be incorporated into production. “There are so many concept car interiors. You can look at them, but you can’t actually live with them – and we wanted to ask where is the future going with materials, textures and things like that,” McGee explains.
“But I’m not a textile designer by any means, or a trimmer – so we butchered engineering and engineering tools into our design process to make it happen.”
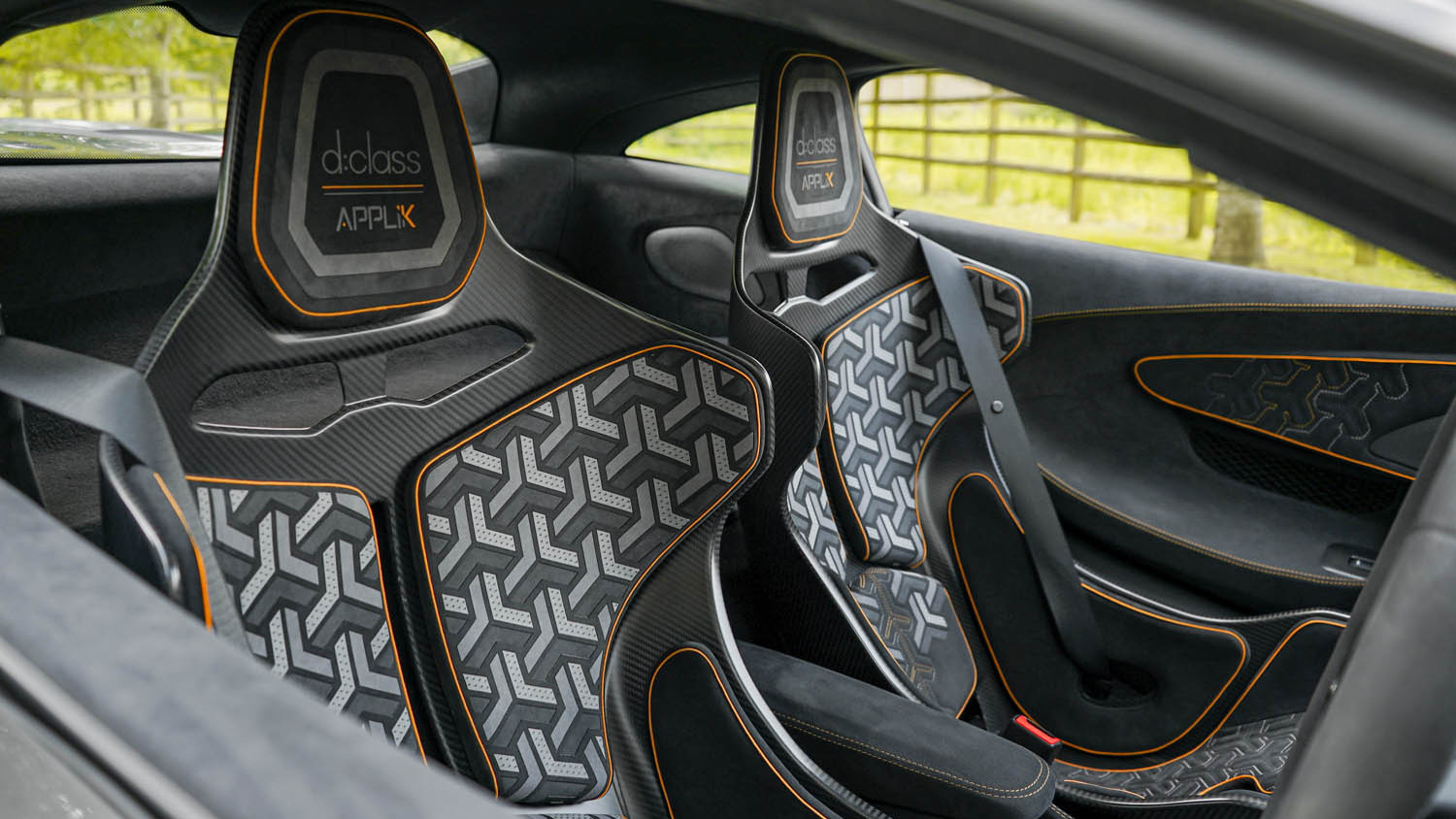
Take a seat
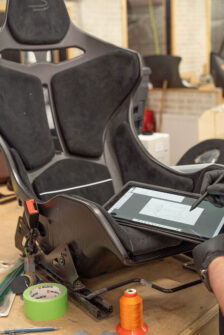
First off, a seat had to be sourced. With no manufacturer willing to release CAD data, the project team had to get creative. D-Class dug deep and bought a McLaren 600LT supercar, affording Formation Industries a brief window of time to spend examining the car’s carbon fibre bucket seat and its sparse padding.
Having drawn up several initial concept sketches, it quickly dawned on them that the concept on paper wouldn’t be enough to enable clients to fully grasp the complexity and benefits of what they had planned, because of the complex curves of the seat and the patterns involved. “That’s when we realised we would have to 3D-model the seat,” says McGee. “All we had was access to the actual seat for a 12- hour window, and at that time we had no 3D scanner.”
In the end, McGee and the team had to paper-pattern the unpicked seat pads and take countless photos from every angle.
This process of transferring the 2D patterns into a 3D model, to then retract them for further 2D cutting and layout, proved a long one. Measurements and geometries drawn up in CorelDraw and Illustrator were imported into Fusion 360. Around 70 hours were spent modelling the seat in 3D from photographs and measurements across five revisions.
“Surfacing in Fusion is still not really ideal, but I’m a bit entrenched now – nearly 24 years deep in Autodesk software,” McGee admits.
“I’m not even sure what the ideal software would have been, but once we had this model, we were able to build it up in such a way that we were taking our initial flat panel concept designs and skinning them onto the seat pads, then producing the renders.”
Fusion 360 impressed with its ability to take the 2D cloth-cut files and wrap them around the 3D form of the seat to produce a convincing visualisation. With the chosen Alcantara material costing nearly £100 per metre, the 3D visualisations saved the development thousands of pounds.
This allowed the team to produce more than 10 interior designs in under three weeks, before then presenting them to their collaborators.
Once a single final design was agreed on, the next stage was equally tasking: building a physical prototype. “We had been wondering why we had not seen many cars out there with cut Alcantara bonded to Alcantara with no stitching. As much of what it is bonded to seems to be other nonalcantara substrate materials with a wet glue process, which just isn’t suitable for the production process we envisaged for the level of detail we wanted to achieve” McGee explains.
Formation Industries had spent nearly a year researching various adhesives and bonding methods for the low surface energy material. To make matters worse, Alcantara stretches in a very tricky one-and-a-half directions and has a very low melting point. The team needed to find a way that would allow detailed laser-cut pieces of the material to be inlaid, seamlessly joining with others. Stitching was not an option, according to McGee.
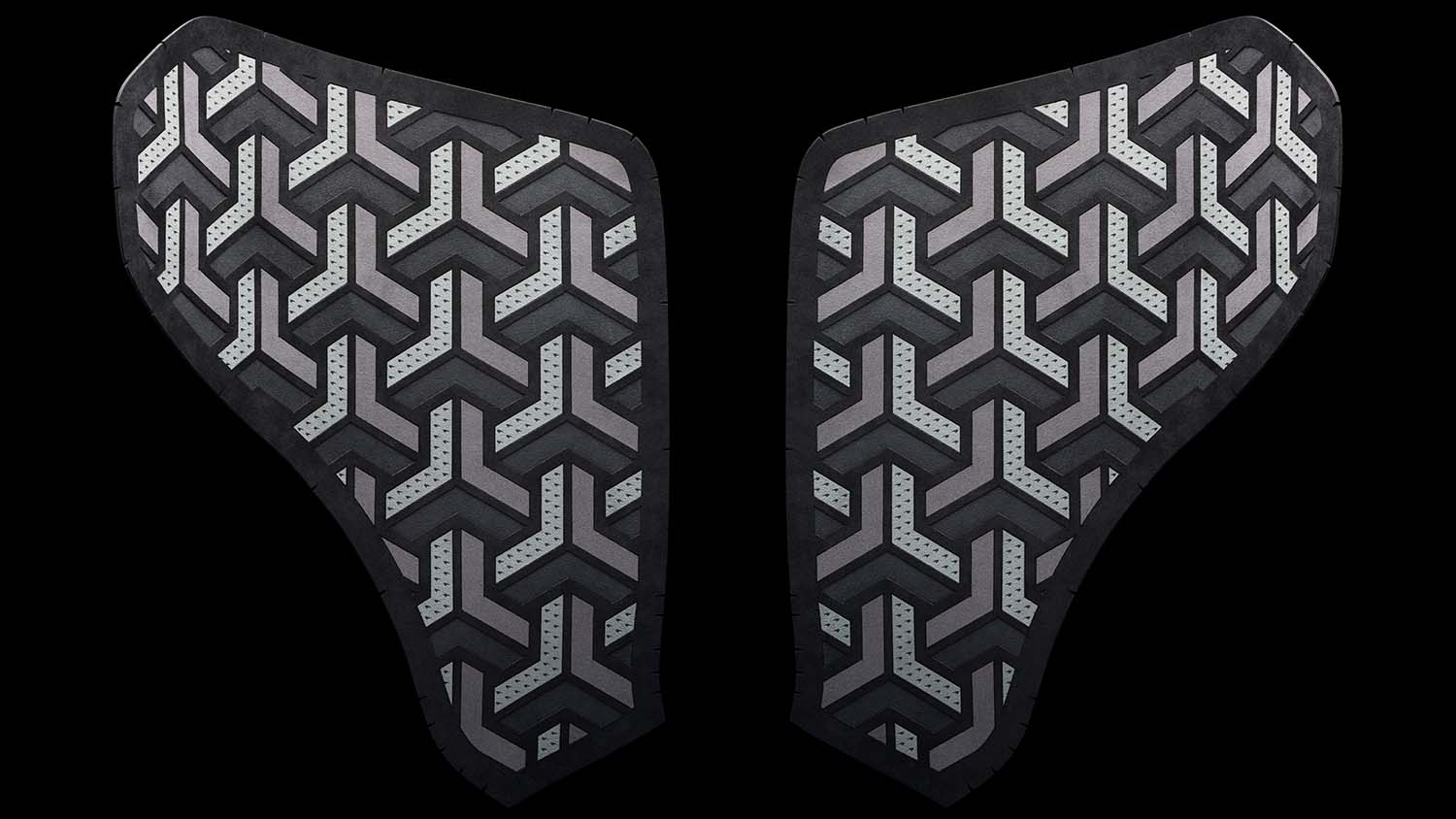
“Certain areas are higher-traffic – you move into them and slide across them, so you don’t really want something where you’ve got reliefs which you could keep catching the edge of,” he says. “With headrests, people have products in their hair, so things have to be cleaned differently, so we didn’t want to leave pockets.”
An additional hurdle was Alcantara’s nap. If you brush the surface in one direction, or rotate it by a 30-degree angle, it noticeably alters the shade of the colour. Says McGee: “It took three solid days of cutting and bonding to do the upper shoulder pads – it was that level of time-consuming. We had to consider every single part and its relationship to the final piece.”
However, the end result is like a classically tailored suit, he says: once unbuttoned, it reveals an extravagant and colourful lining. “That’s what I wanted for these interiors: to bring the pomp and ceremony of a suit, where we could both own the same suit, but the lining – our interiors – would start to define our personalities.”
The project has wowed the world of car interiors, but Formation Industries isn’t stopping there. McGee and his team reckon that even more materials can be added, but the next stage is streamlining the workflow.
An Einscan HX handheld 3D Scanner has since been purchased, reducing the 3D modelling from 70 hours down to two, and research has now moved on to how the cut slithers of material can be positioned to improve aspects of performance like grip and overall comfort.