The team behind Glove80 speak to Claudia Schergna and explain how 3D printing and Fusion 360 helped them develop a split ergonomic keyboard, transposing a software development mindset into hardware design
Split into two halves, Glove80 is a wireless ergonomic keyboard that takes its name from the fact that it is designed to fit your hand like a glove and features 80 keys.
Fully customisable, it aims to introduce a healthier, more enjoyable way of typing, as its designers, MoErgo, looked for a solution to tackle repetitive strain injuries in the workplace.
Glove80’s two founders both suffer from damaged hands from over 20 years working as software engineers. “I ended up spending a lot of money buying keyboards and it turned out that none of the keyboards are really good!” says co-founder Stephen Cheng, over a web call from his base in Wellington, New Zealand.
Glove80 is split into two halves so that it can be regulated according to the width of the user’s shoulder, minimising ulnar deviation, which causes carpal tunnel syndrome.
It is designed to prevent wrists from bending outwards or upwards, which can cause serious injuries and prevent the blood from circulating to the hands properly. “Designing a keyboard is unlike anything else,” says Chris Andreae, the other co-founder, also on the line from his office in Tokyo, Japan, holding one of their latest prototypes of Glove80.
“Everything is functional. To make it work well with the human body, we had to create a whole new design process to make it work. When we talk about hundreds of prototypes, we are not joking at all!”
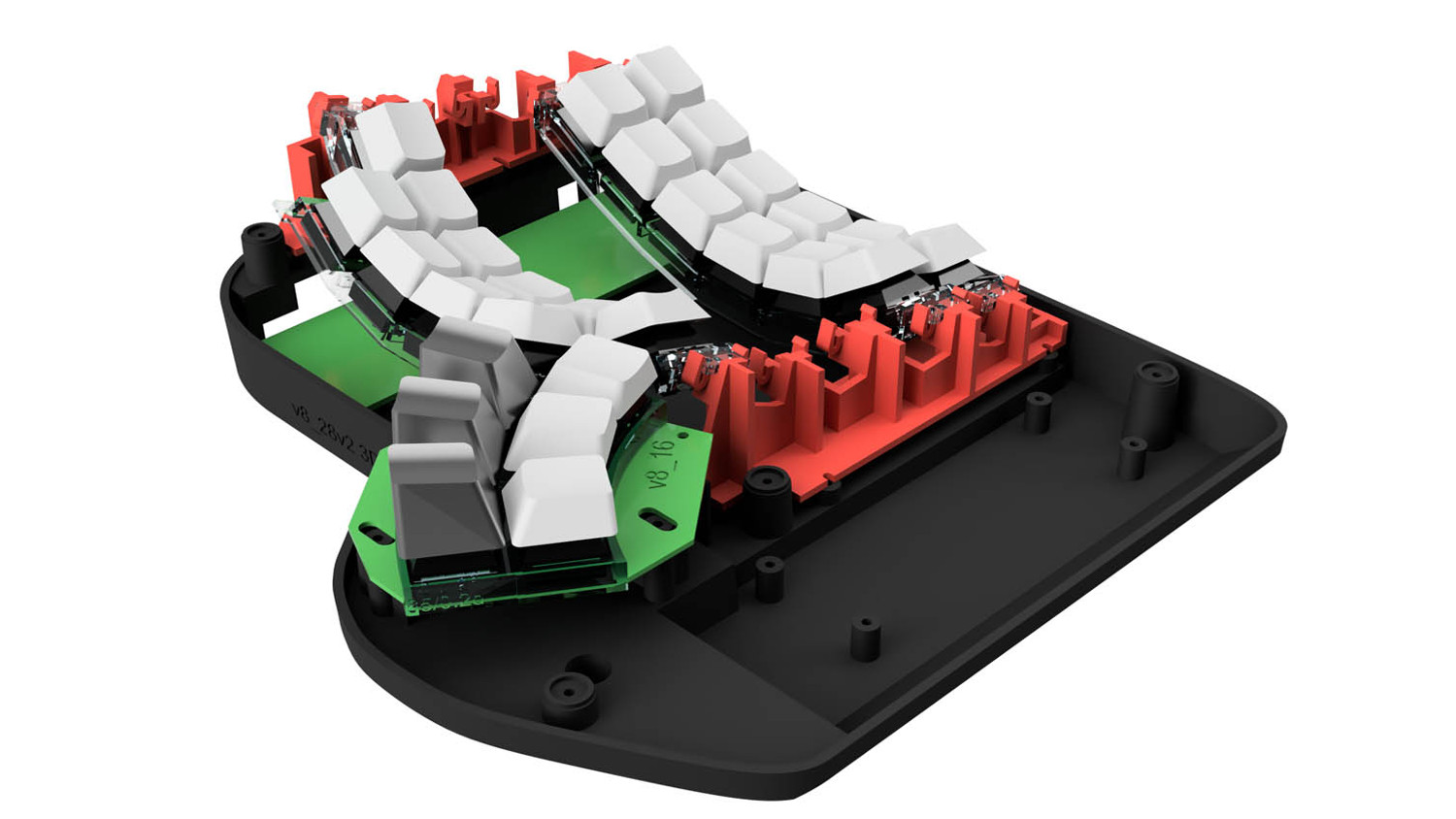
Going the distance
To find the best shape for each part of the keyboard, Cheng and Andreae 3D printed hundreds of prototypes on their Ultimaker 2 desktop 3D printers, allowing them to conduct A-B testing much as they would in software development.
To make this process easier and waste less material, they decided to adopt a modular system. “Without this kind of system, every single time you want to change, say, the ergonomics, you will end up having to print the whole thing again,” explains Cheng.
Andreae takes over: “The key element about our prototypes was that they were functional prototypes. At every step along the line, those keyboards where we would swap a different shape column or a different shape thumb panel, you could actually type on them. You could do your daily work and immediately get feedback.”
This process allowed the pair to coordinate their work, despite the distance and time zone difference. They send each other new STL files daily, developed with Autodesk Fusion360, which they then 3D print at their own home facility and test for a day or two.
“One of the things that we found out is how much everything is related to everything else,” explains Andreae. “When you change the palm rest angle without changing the corresponding key column angle, what it will cause you to do is twist your fingers as you press the keys. If you are sensitive to it and or have carpal tunnel or similar, it can get very painful even in a short period of time.”
Glove80 – big thumbs-up
Glove80 features six patented thumb keys, which are designed to redistribute the movement between all the fingers and engage the thumbs, which are our strongest fingers, but rarely involved in the typing process with straight keyboards.
Besides the ergonomic benefits, Glove80 also offers many technical customisable features, such as the possibility to rearrange the keys to QWERTY, Coleman, Dvorak or any other personalised layout, and the possibility for coders to add software features to the keyboard.
In the six years that Andreae and Cheng have worked on Glove80, they have performed around 500 ergonomics experiments to find the right angle and position for each key.
What they say makes their product special is the development process and the lack of anything similar on the market: “The existing keyboard vendors simply would not think about doing something like this: doing a 3D modelling, doing A-B testing, doing hundreds of experiments with the modular approach, doing the parametric sequencing.”
Although they extensively use 3D printing for prototyping, the manufacture of Glove80 will be done through traditional injection moulding.
The team has selected three factories in Shenzhen, China where the keyboard will be produced: one specialising in injection moulding, to make the plastic parts; one specialising in PCB; and a contract manufacturer to assemble the final product, putting it into the hands of end users.