Along with its best-known machine Henry, Numatic has been producing vacuum cleaners in the UK for over 30 years. We spoke to its toolroom team to find out how the ability to react quickly to tool repairs in-house is helping the company to expand beyond households and become a global professional cleaning powerhouse
Every week, Numatic produces more than 28,000 vacuum cleaners for household use, including Henry, the familiar, googly-eyed domestic machine with its red and black canister that has been the face of the brand for over 30 years.
But the Numatic brand extends well beyond the home, with some 4,000 commercial cleaning machines produced every week, too. These include both wet and dry vacuums and specialist cleaning units designed specifically for hotels and hospitals, for example.
Today, Numatic’s Chard, UK factory employs a workforce of over 1,000 people and runs 50 injection moulding machines – a far cry from humble beginnings as a team of six in a workshop.
The injection moulding machines on the production floor range from 40- to 1,400-tonne pressure machines, with the largest injection mould tool weighing in at 15 tonnes. Most components in the injection mould tools, meanwhile, are produced from pre-hardened 40HRc steel, which presents added challenges for the toolroom tasked with machining the components.
The toolroom at Numatic has a team of 11 staff and a selection of CNC machine tools from suppliers including XYZ, Hurco, HAAS, YMT and Sodick.
These are all utilised for machining inserts, punches and any other wear parts or components that may need repair or replacement.
Numatic – new components
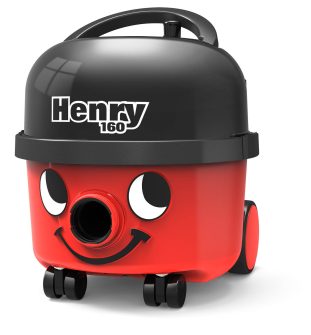
The company also has more than 2,100 injection mould tools on-site. At any point, the toolroom can be called upon to remove damaged or worn components from a mould tool, locate the drawing file and subsequently create a CAM file with Visi to machine a new component for the tool. Once this part has been precision-cut from metal, the tool can be returned to the production line.
“For the high-volume injection moulding machines, we always have a spare injection tool in place and ready to go,” explains Numatic’s toolroom supervisor, Scott Connett. “But for the lower volume parts, we have to leap into action and apply Visi to create a CAM file from the XT ParaSolid drawings that we have on our tool registry files.”
From here, Connett and the team generate the most productive machining strategy for the machine tools, in order to get the parts machined as quickly as possible and without error.
“As the material is difficult to machine, Visi helps us with our machining strategies to account for this,” continues Connett. “We would be completely lost without Visi, as it allows us to load particular programmes into our machines, and this gives us the versatility to have complete machine-tool availability.”
Always supported
Before adopting Visi, the team had no in-house 3D design experience, but as a useful resource and reassurance, Numatic has its own personalised portal. This means that if any issues arise and require support, a log can be raised with Hexagon, which results in the team getting a call back within the hour, “or two at the most”, laughs Connett. “This means that the support system is always there for us.”
With Numatic recently adding a third seat of Visi, Connett says the modular configuration is now perfect for his team’s requirements. The standard element system that Numatic uses includes the mould tool module and the electrode package for its EDM machine, but gives the company the option to explore other elements in the future, such as Visi flow for mould injection simulation.

As an integrated CAD/CAM package, Visi not only helps keep the team on top of external tooling designs and any in-house repairs, but it also allows its members to design and produce any jigs and fixtures for the mould tools.
Says Connett: “We have now been using Visi for 12 years and what initially attracted us was the CAD/CAM integration with it just being one system. This means we are not chopping and changing from one software suite to the next.” CAD
Visi enables the team to undertake machining and apply roughing strategies for complex parts in around 15 to 30 minutes, he adds. “That is an absolute saving for us. In most instances, our mould tools are manufactured externally, but having VISI means that we have the facility to design and manufacture some of our mould tools inhouse.”
This ability to amend and repair tooling in-house, while having the software to help quickly solve additional problems as they arise, is helping Numatic make a clean sweep of the market, both at home and further afield.