With Autodesk Fusion Industry Cloud, Autodesk has big plans for data across the entire product lifecycle, writes Greg Corke
It must be hard to be a software company these days. If you’re not shouting about AI, you’re not part of the conversation. So, it was little surprise that Autodesk launched its ‘Autodesk AI’ brand at Autodesk University last month.
Given that there has been a sprinkling of AI capabilities in Autodesk products for several years, and AU didn’t deliver any major new AI capabilities, the branding is somewhat retrospective.
At this stage, the message is probably aimed more at shareholders than customers. Autodesk is essentially stating its intent to add more AI capabilities into the mix henceforth.
Much of the future AI developments will centre on Autodesk Fusion Industry Cloud, announced at AU last year. “It’s how we bring together data and workflows across the entire product lifecycle,” said Srinath Jonnalagadda, vice president, design and manufacturing industry strategy, Autodesk. “It unifies your data.”
The Autodesk Fusion Industry Cloud is built on the Autodesk Manufacturing Data Model (formerly known as Fusion Data), which is designed to provide a consistent method for accessing and sharing data. The idea is this can be done through any device,” as Jonnalagadda explained. “Whether you’re a business executive at a conference in Vegas, giving final design approval from your phone, or a production engineer heading to Shanghai, getting an alert about a change mid-flight on your laptop, or a machinist on the shop floor in Birmingham seeing from your tablet that tolerances have changed, you’re going to hear a lot about this – our vision for the future, the future we’re building with Fusion Industry Cloud.”
The Autodesk Manufacturing Data Model works by breaking up monolithic files into granular data that is stored in a unified database and can be accessed through APIs.
Instead of exchanging heavy files, the idea is that users can access the ‘right data at the right time’, without having to worry so much about version control. In addition, because the data is broken down into bits of information, subsets of data can be shared with collaborators.
According to Derrek Cooper, VP cloud data and PLM, Autodesk, this opens up new ways to exchange and extract information, like materials, cost, geometry and other things beyond that.
Storing all data in a unified database, instead hiding it away in individual files, presents a massive opportunity for AI. The idea is to set the Autodesk AI loose on the data and gain valuable insights. Quite what these insights will be remains to be seen.
Data doesn’t just have to come from Fusion, Inventor, or other Autodesk tools. In the future the plan is to extend it to data from third parties – CAD, CAM, CAE, PCB, data management (PLM, PDM), manufacturing execution systems (MES), or enterprise resource planning (ERP) are all up for grabs. In other words, data from across the entire product lifecycle.
AI: the here and now
While letting AI loose in the Autodesk Fusion Industry Cloud is certainly one for the future, Autodesk did announce one new AI capability that is coming to Fusion that will likely resonate with many of its manufacturing customers. Autodesk is using AI to automate drawing production.
According to Jeff Kinder, executive VP, design and manufacturing at Autodesk, this is a task that can suck up 60% of a skilled engineer’s time. “By the end of the year, we will launch automated drawings in Fusion to translate your 3D models into fully dimensioned drawings with a click of a button,” he said.
AI is also helping bring new efficiencies to toolpath generation, through a partnership with CloudNC, a UK firm in which Autodesk has a major investment. “Fusion has reduced programming times by up to 80% through AI-powered CNC toolpath analysis and automation,” said Kinder.
Stephen Hooper, VP design & manufacturing product development, Autodesk, continued, “You can upload a 3D model of any part and in one click automate toolpath creation, meaning you can spend time on the complex high-value projects that differentiate your shop’s capabilities.”
On a more creative level, Autodesk recently acquired BlankAI for conceptual design, a generative AI technology which augments the work of automotive / industrial designers, enabling them to create 3D concepts ‘in milliseconds’.
The AI lets users generate and edit proportional 3D models via semantic control. It even allows automotive firms to incorporate their own historic design DNA into the AI, so new concepts are consistent with styling cues. Autodesk has also integrated the software with Alias and VRED for a more ‘immersive, collaborative experience’.
BlankAI will be debuting in Autodesk’s automotive design studio next year and while the main focus is currently on automotive, Hooper said there’s no reason it couldn’t be applied to other products, such as furniture or packaged goods.
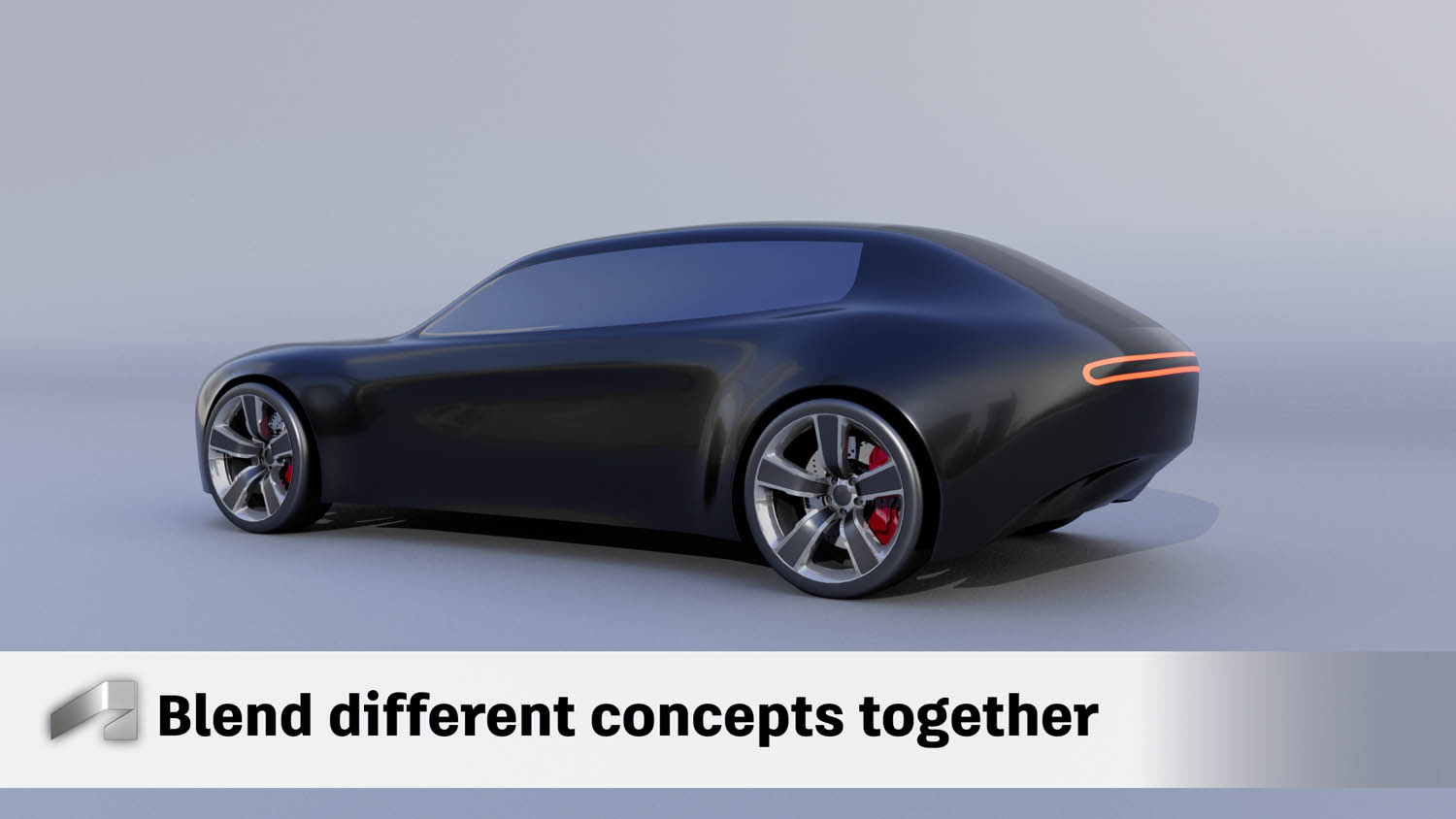
The role of Fusion 360
When Autodesk Fusion 360 launched in 2013, many presumed it would mark the death knell for Inventor. Ten years later and Inventor is still going strong. While people still talk of migration from Inventor to Fusion 360, Hooper sees better integration between the two CAD tools as being more about complementary workflows.
There are now one click workflows that bring data from Inventor into Fusion associatively. If a model is changed in Inventor, it will automatically update in Fusion and vice versa.
“[Inventor users] can start to make use of things like generative design, some of the automated machine tools, and eventually things like automated drawings,” said Hooper.
Interoperability between the two tools goes beyond an associative link. It also extends to data management, as Cooper explains, “Customers that are managing their data on premise in [Autodesk] Vault, they also want to explore using Fusion, and we have a connection directly between Vault and Fusion, so you can have this coexistence.”
Autodesk is also looking to improve interoperability with third parties. In a move designed to enhance collaboration between mechanical and electronics design, Autodesk has formed a new partnership with Cadence, a specialist in electronics systems design tools. “Our partnership connects their sophisticated PCB design capabilities directly to Fusion, so changes made in either tool will automatically be reflected in the other,” said Kinder.
The storing of granular data in the Autodesk Data Model is also helping deliver new capabilities in Fusion. This includes the recently released ‘configurations’, which allow users to create multiple product variants during the development cycle without having to deal with multiple file versions.
“Each new configuration is not a massive new file, just recorded changes in a cloud database, which makes it faster to load, easier to navigate and easier to manage,” said Kinder.
Conclusion
Autodesk clearly has a long way to go before it delivers on its big vision for AI. At AU we got a good idea of how it intends to get there – via the Autodesk Fusion Industry Cloud with a unified database built around granular data from multiple sources across the entire product lifecycle – but there was very little information about what Autodesk’s AI will do with that data once it’s there.
In the meantime, we expect to see AI start to bring more tangible benefits to Autodesk users – automated drawing production and one-click machining strategies being cases in point. We’re also interested to see what role BlankAI might play beyond automotive.
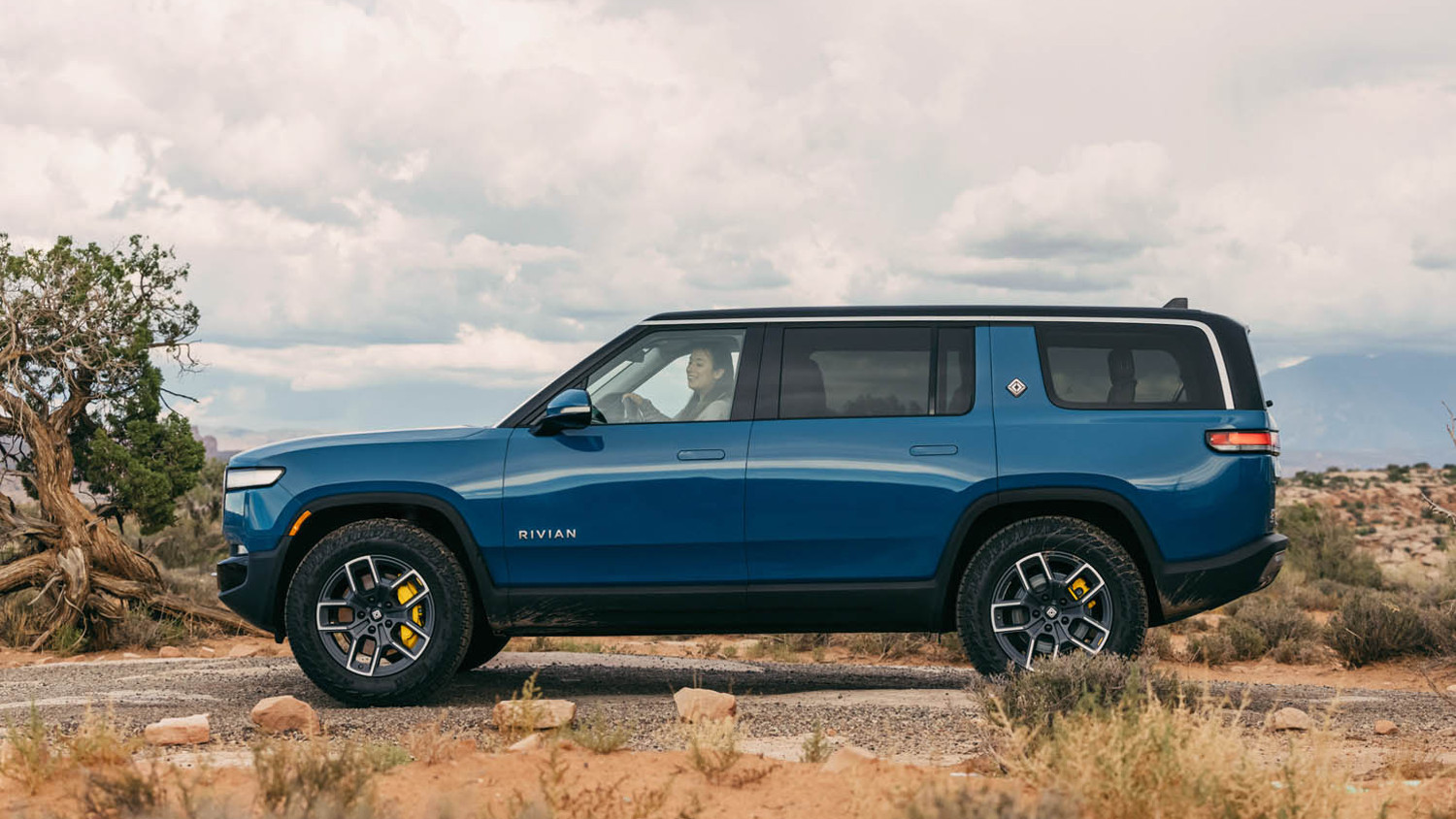
Electric dreams – Autodesk at Rivian
Autodesk is no stranger to the automotive industry. Its Alias and VRED tools are used extensively by many global firms for surfacing and visualisation. Rivian, an electric vehicle (EV) startup that develops SUVs and pick-up trucks, is no different.
The company has been using VR in VRED to visualise the Rivian R1 EV from engineering to colour to materials and finishes. It’s an integral part of the design process, so its team can experience the design first hand.
“You can’t walk inside of a clay model,” says Jeff Hammoud, chief design officer, Rivian. “With VR we can open the door, explore the interior. How do things look and feel? Is there glare from the screen? What’s the view from the steering wheel?
While Rivian’s use of Alias and VRED is standard, its implementation of Autodesk Fusion 360 is not. The core of the design is done on an unnamed CAD system (we’re guessing Siemens NX or Catia) but the company’s special projects team that creates its prototypes has standardised on Autodesk’s CAD/CAM tool.
Fusion 360 is used to program Rivian’s 5-axis CAM machines for prototyping parts, jigs and fixtures. Components range from door hinges, motor covers and motor mounts to the sub frame and suspension system.
“We were able to swiftly create multiple iterations on our CNC machined suspension components,” said Hammoud. “Fusion enabled us to fine tune the geometry and the fit of these parts with remarkable efficiency.”
The decision to use Fusion 360 was driven by Rivian’s Jonathan Dankenbring, who now leads a team of machining and additive experts for prototyping at Rivian.
Dankenbring joined the automaker five years ago and was immediately tasked with building up its 5-axis capabilities. At the time, Fusion 360 was the only tool he was familiar with through his experience of programming hobbyist CNC machines. With only two weeks to prove out the process, he admits it was a steep learning curve. The rest is history, as they say. “We find it completely capable,” he told DEVELOP3D. “We’ve yet to find a part that we can’t make in Fusion 360.”
Of course, it’s faster and cheaper to 3D print prototype parts so until a stage is reached where testing for fit is required, parts can be made in plastic. Rivian uses a range of additive manufacturing technologies from Stratasys including FDM, SLA, DLP, Polyjet, and Powder Bed Fusion.