Instead of a solution in search of a problem, additive manufacturing needs to become a technology that product development experts can depend on to deliver true mass manufacturing, writes Holo co-founder Arian Aghababaie
Whether we like to admit it or not, additive manufacturing (AM) is still a young, upstart industry when compared to the broader, more established manufacturing world. While that means we still have a lot to learn about scale, reliability and the applicability of our respective technologies, it also means that this is an incredibly dynamic and inventive space. It’s populated by many 3D printing start-ups, academic institutions and tinkerers who, together, are trying to break through the hurdles that companies in this industry face, from fierce competition for a potentially small overall user base to manufacturing economics that favour other approaches.
However, there is a downside to this dynamism. Sometimes, it can fuel a blind passion for developing technological solutions, rather than fostering a steady focus on what the world actually needs.
Starting with a solution is the easy way. It’s deciding, ‘I think this could work’, and then putting an experiment to the test and discovering you were right. It works!
A successful proof of concept is quickly followed by a flurry of other activities: filing a patent, starting a business, aiming to go viral on social media, and so on. That may sound like success – but it’s not, because it’s how you end up with a solution in search of a problem.
You go from, ‘I think this could work’ to, ‘I wonder what this could work for?’, which in reality is more of a thought experiment than a business plan.
Where to start?
Start with the problem. Start with the user base, with the people who might actually be in need of a solution and, more importantly, actively looking for one.
Listen to existing problems, instead of creating hypothetical solutions. Address real-world issues and listen to what they actually entail and require
Here’s where true brilliance lies and where a company might just build itself a foundation poised for success: Listen. Listen to existing problems instead of creating hypothetical solutions; address real-world issues and listen to what they actually entail and require.
When we started Holo, we took a technology familiar in 3D printing – digital light processing (DLP) stereolithography, known for being a high-throughput, high-resolution yet cost-effective process – to a sector mired with problems: metals.
DLP and metals hadn’t really intersected before, as users requiring finely detailed metal parts already knew of and had invested heavily in proven technologies that hit the specs, hit the parameters and hit the quality control that they need. In most cases, that points to precision processes, such as metal injection moulding (MIM), Swiss machining and 5-axis CNC.
And thus, in most cases, this has also meant accepting the limitations associated with these processes. These include identifying the few Swiss or precision 5-axis machine shops with available capacity, for example, and bearing with long lead times for parts. Or dealing with long wait times for MIM, while moulds are created, iterated and finalised, and weeks if not months are spent getting production lines ready.
In situations where you’re needing batches made up of millions of fine parts, these compromises might be worthwhile, as mass production would ultimately prove out its ROI. But when you’re dealing with limited or short-run production runs, batches comprising one or a few items, or you urgently require production-on-demand capabilities, then using these more traditional processes makes no sense, if it’s even possible.
Enter metal additive manufacturing as a new avenue. One or a few parts could be made relatively cost- and time-effectively. If those parts required substantial post-processing to hit tolerances, so be it: the ROI is still superior to traditional processes. Scaling that beyond one or few parts might be impossible, but how about combining the on-demand capabilities of 3D printing with the resolution of DLP and the necessary metal materials? That’s unheard of – or at least it was, until that particular intersection of needs was recognised as an issue in need of a solution.
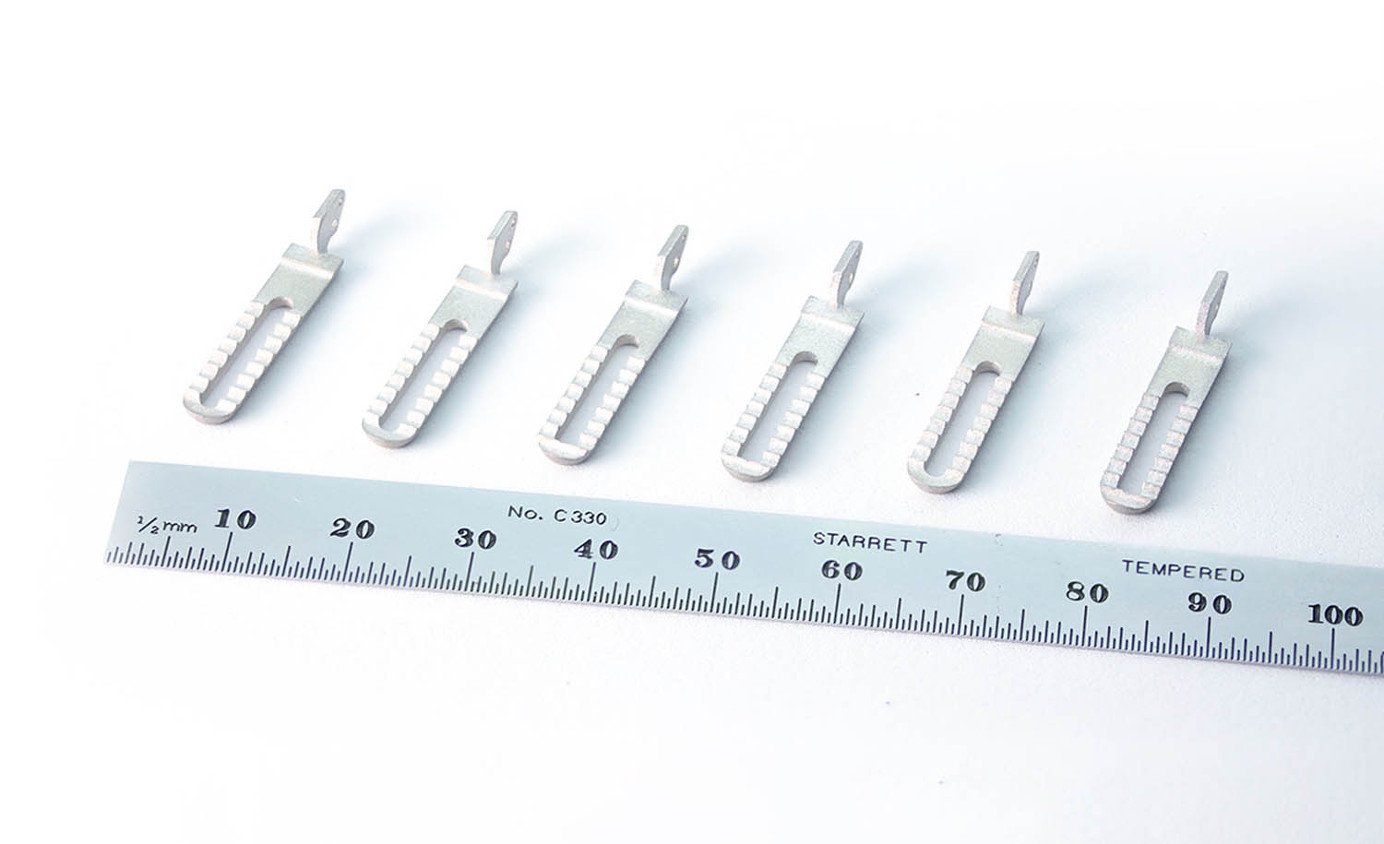
What does and doesn’t help
The first step is identification. For us, what end users needed was a precise, true-to-CAD, scalable production technology available on demand.
The next step is solving that problem. Excited inventors may not want to hear this, but it typically means focusing on the boring stuff, like accuracy and results.
From there, we move to refining – note that we’re not saying reinventing – the technology, taking it into high gear by moving beyond the boring stuff into creating realisable processes. In effect, the new technology should aspire to replicate the success of more traditional manufacturing processes.
Along the way, there are some important ‘Do Not Do This’ steps to observe:
• Do not push a 3D printer onto someone who doesn’t need it
• Do not ignore existing trusted supplier relationships
• Do not pretend that ‘traditional manufacturing’ means ‘out of date’, or worse, ‘obsolete’
It can be easy for those invested in AM to drink the industry Kool-Aid and throw out lattices as a solution for every problem. They help lightweight parts, right? Sure. But do they hit the necessary specs? Only sometimes.
At the end of the day, AM is a business. Business is about unique value propositions, sure, and it definitely helps when those are predicated upon patented offerings. But if everyone in, say, automotive reinvented the tyre for each new generation, we’d never get on the road. Let’s not reinvent the wheel. Let’s approach AM logically.
About the author:
Arian Aghababaie, PhD, is chief strategy officer, president and co-founder of Holo. With over 10 years in the AM industry, he has an extensive background in leading teams bringing new 3D printing technologies to market.
At Holo, he sets the vision for applying the company’s metal AM technology to production applications, creating value through the design freedom that Holo’s 3D printing enables.
This article first appeared in DEVELOP3D Magazine
DEVELOP3D is a publication dedicated to product design + development, from concept to manufacture and the technologies behind it all.
To receive the physical publication or digital issue free, as well as exclusive news and offers, subscribe to DEVELOP3D Magazine here