As the automotive industry gears up to go fully electric, our columnist SJ visited the MTC, a UK research facility experimenting with tech that gives them a license to thrill car engineers and enthusiasts alike
Have you ever visited somewhere that made all your crazy movie fantasies feel just that little bit more realistic? Working in metal 3D printing, I thought I was already pushing the boundaries of reality. But my post-DEVELOP3D LIVE trip across Coventry to the Manufacturing Technology Centre (MTC) broke the proverbial third wall.
My favourite engineer in all of cinema history is Q, the quartermaster from James Bond. Q was a crafty genius, able to give critical equipment the appearance of simple, everyday objects.
This was very much the vibe at the MTC, too. It’s a place in the business of creating high-tech applications that look likely to have huge real-world impact within the current decade and beyond.
Established in 2010 as an independent technology research facility, with the goal of bridging the gap between academia and industry, the MTC’s brief today covers advanced manufacturing, factory design and training. It’s also home to the UK’s National Centre of Additive Manufacturing. This range of interests and specialisms allows MTC researchers to piece together the latest technologies to build brilliant advanced solutions for industries like aerospace, manufacturing and automotive.
Car chase
While there was no Aston Martin on hand, complete with bulletproof windshields, passenger ejector seat and revolving number plates, what my visit made clear is that researchers at MTC are doing a ton of equally innovative work across automotive.
The MTC aims to have a positive impact on the success of the UK’s zero-emission vehicle mandate — an ambitious plan for 80% of new cars and 70% of new vans sold in the UK to be electric vehicles (EVs) by 2030. And by 2035, the total is expected to rise to 100%.
The massive overhaul required to shift from manufacturing vehicles based on the internal combustion engine (ICE) to those powered by electricity is forcing the industry to navigate a challenging journey.
We’re in an economic period where many companies would prefer to pursue short-term growth and profits rather than chase longer term rewards, but the changes required to restructure automotive manufacturing will demand at least 10 to 15 years of hard work and investment.
Fortunately, the MTC’s Electrification Steering Committee is ready to step in with a plan to more rapidly overhaul engine architecture. One element of its proposals is an additively manufactured electric motor. Benefiting from increased power density, manufacturing efficiency and reduced part count, the casing for the motor uses liquid cooling channels to produce more power without overheating.
This idea would also support weight savings of 10% and a size reduction of 30%, leaving more space and weight available for other architectures such as the EV battery, controls, sensors and powertrain.
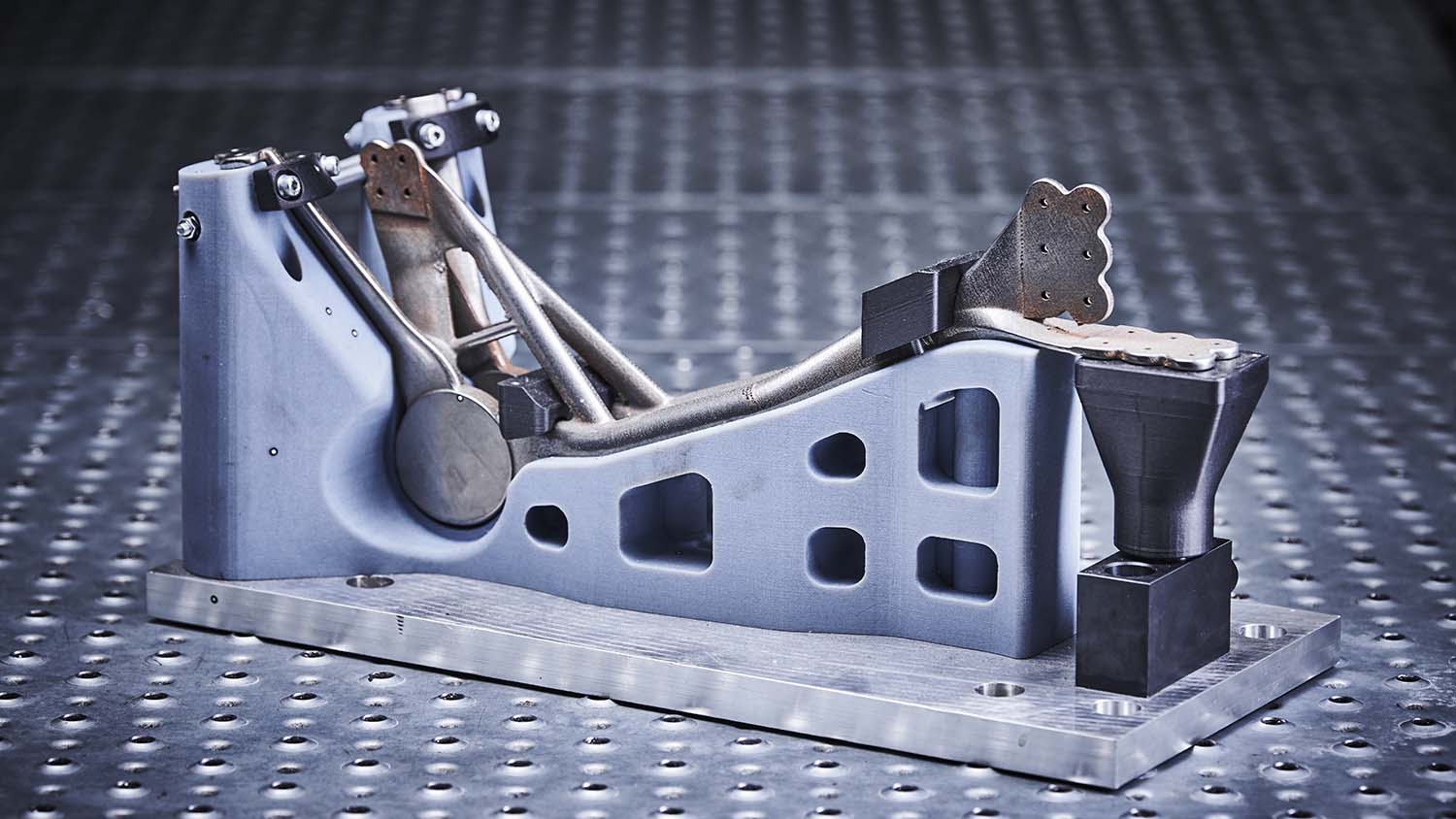
Ti(tanium) another day
Part of me dies a little every time a customer says they want a large, bulky part printed in titanium on our laser powder bed fusion system. Sure, titanium is one of the sexier, more exotic alloys, but it’s incredibly difficult to print. Fortunately, the MTC has been busy developing solutions and workflows for this very purpose.
Using a GE Arcam 3D printer, a smallscale particle accelerator fires electrons at the powder bed under vacuum, in order to melt metal material, instead of using a direct laser weld. Cost-effective, this approach produces parts with a coarser surface finish, but ones that are less prone to warping and thermal stress.
Using their fancy machine, the Qs in the MTC lab were able to print parts for the Oxford Brookes Formula Student racing team. The uprights that were printed delivered a 50% weight savings and enabled the gearbox to produce more than 300Nm of torque per wheel.
3D printing parts is great, but it’s sometimes only half the battle when better fixtures are needed to hold these new age parts during post processing. Enter the MTC’s large-format 3D printer for thermoplastics and composites. A hybrid additive and subtractive machine, its name makes it sound like a Bond villain’s henchman: the Ambit Xtrude.
The Ambit Xtrude, from US company Hybrid Manufacturing Technologies, takes a standard CNC machine tool and converts it into a hybrid machine with plug-and-play printheads for rapid additive layering.
Due to some hush-hush, MI6-style security, I can only tell you about a fraction of the incredible initiatives going on inside the MTC. I met brilliant engineers who, even from behind their safety glasses, made clear their sense of purpose and passion for technology and potential applications.
Even after a single visit, I’m fairly certain the MTC is well on its way to helping the UK achieve its EV goals for 2030 — bulletproof glass windows and machine gun nests not included, unless of course you have access to a Q of your own.