The sheet metal and fabrication industry requires a specific set of tools that are often only paid lip service by mainstream vendors. We take a look at the SigmaNest range from SigmaTek, which looks to address these particular needs
The sheet metal and fabrication industry is one that often meets with a slightly sniffy attitude from other companies in the manufacturing industry.
It simply doesn’t get the respect it deserves – from the use of the pejorative term ‘metal bashing’ or the media’s habit of cutting to someone working at a press brake when talking about the manufacturing skills gap.
The reality is that sheet metal design, production and fabrication is an advanced world, full of lasers, plasma cutters and some of the most interesting software you’ll find on the market today – handling everything from design and engineering, through to rapid quotation and stock and production management.
This is the world in which SigmaTek operates. Based in Cincinnati, Ohio, the company has been serving the sheet metal industry with a range of tools since 1993.
The company recently got a boost with its buy-out by Battery Ventures, a company that has also invested in companies including Vero Software, Edgecam, Alphacam and more.
While SigmaTek has been around for quite a while, it’s possible you’ve not come across it before, so our intent here is to provide an overview of what its solutions can do and how they can help those organisations looking to build a more intelligent workflow.
If there’s sufficient interest (do let us know!), then we’ll take a more in-depth look at the tools it offers in a future edition. So let’s begin with the first step in the process: creating quotes.
SigmaNest -Rapid quotes
Quote creation is particularly important in the sheet metal and fabrication industry, where subcontracting is king and speed of response to a request for quotation (RFQ) is a crucial factor in business success.
According to SigmaTek executives, the company’s most successful customers are those that are able to get an accurate quote in the hands of a customer in as fast a time as possible.
SigmaNest is the flagship product in SigmaTek’s range, and its capabilities are based on the use of advanced nesting algorithms.
This focus on nesting gives the software several advantages, many of which come into play in the earliest stage of the process.
Imagine receiving your customer’s RFQ and associated data. While the system can work with all manner of data, DXF or DWG are still the most common.
The first step, then, is to process that drawing data and extract as much useful information from it as possible.
This isn’t just about ensuring that you can strip out useful geometry and cross reference any associated dimensions to ensure it’s scaled and drawn correctly (which the system does).
It’s also about stripping back drawing title block geometry and retrieving other information such as part name, material requirements, thickness and more.
The system automates much of this, but clearly, some manual input might be needed to pick apart each individual customer’s naming conventions, layer use and such.
The good news is that, once you have done this, you can store that as a customer-specific template, which can be very quickly applied not only to other drawings in the same batch but also any subsequent RFQs that come in from that customer.
Now that you’ve got a set of drawings and associated parts, the system can work its magic, taking these specified parts, running them through its intelligent nesting algorithms and providing you with an accurate idea of costs associated with producing the parts required.
SigmaTek’s history in the nesting technology world is immediately evident.
All of your machine parameters are stored in a centralised location, in the form of a Microsoft SQL database.
Then, the system can very quickly rip through the nesting process, respecting any requirements per part, such as grain orientation, and evaluating the machine configurations available.
SigmaNest has been built to cover almost every machine capable of handling sheet metal, from CNC laser and plasma cutters and CNC punch machines, to CNC knife cutters typically used for composites and fabrics.
It will take your customer’s parts, build a set of sheets on the most appropriate machine and give you a fully nested weight for the job at hand, as well as a price, assuming you have your material prices linked in too.
SigmaTek’s product then takes this information and fully manages the quotation process, allowing secondary processes to be added.
These will give you the reports you need to ensure your quote is competitive and that you’re using your inhouse capabilities as efficiently as possible.
Once a deal is won, it’s then time to take that information into production – and this is where the SigmaTek production range really kicks things up a notch.
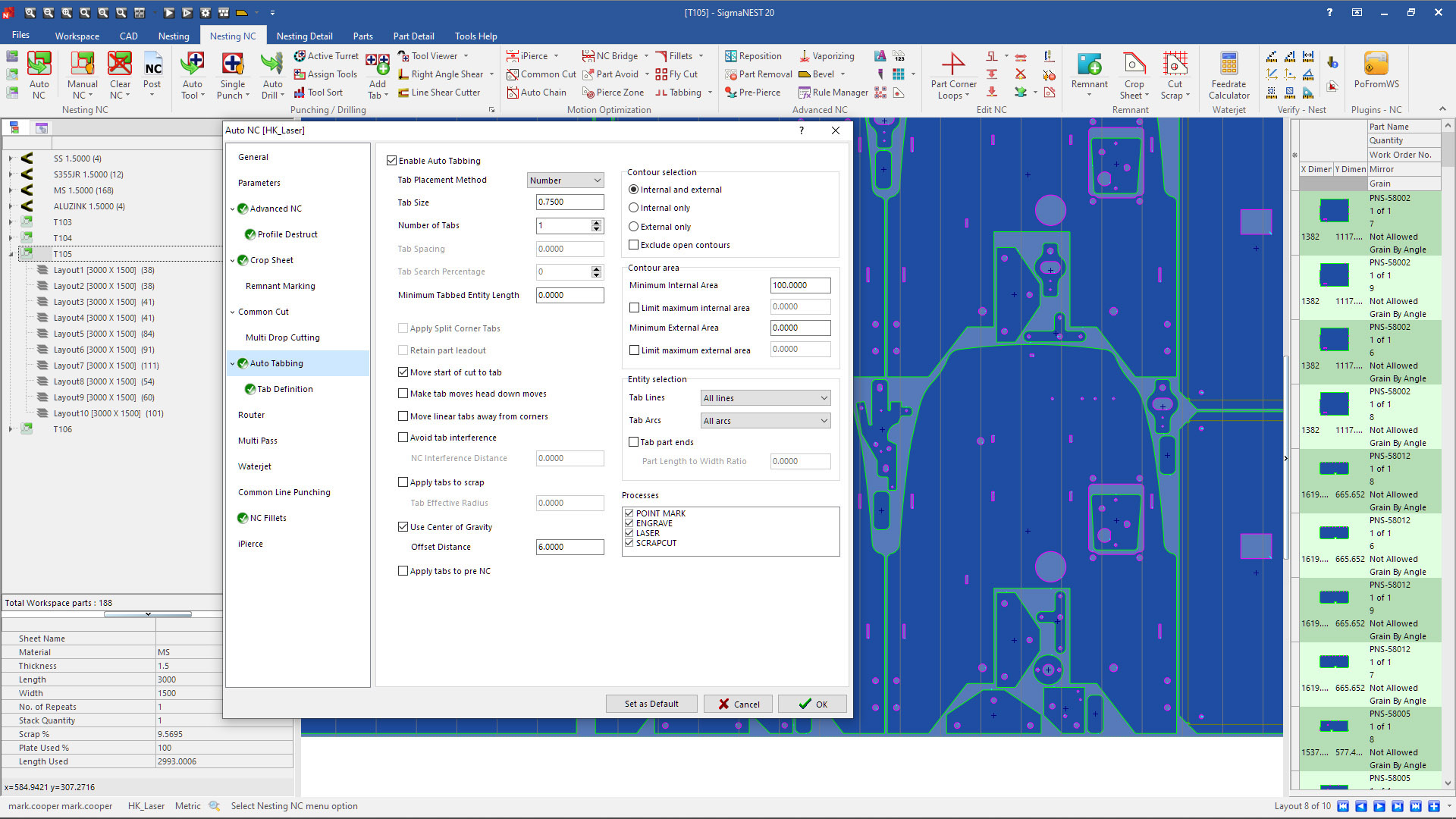
All systems go
Due to the breadth of SigmaNest’s capability, it’s difficult to give a complete overview of what it can do in just a few pages.
Instead, I’ll give you a few indications of how this product has been thought out and developed over time.
Consider nesting a set of parts on a laser or a plasma cutter: You would typically have a mix of large and small parts, nested together, all of which are cut from a large sheet, rested on a grid, through which the plasma or waterjet passes.
The issue here is that, if you have smaller parts that are not supported (for example, by two bars in the grid), they could tip and fall through and quite possibly never be seen again.
To resolve this issue, the system analyses the centre of gravity of each part and combines this information with previously defined knowledge of the grid that lies beneath the sheet.
When it identifies parts that are in danger of disappearing into the waste bin, it automatically adds the tabs that are needed to retain them.
Most mainstream cutting programming tools only offer a tab on/off toggle, which means extra post-processing and hand finishing.
Another highlight is remnant management and cropping of sheets.
While some of this extends into stock management (which is covered by SigmaTek’s MRP system), it also plays heavily into the production programming process.
Most organisations that engage in this type of work are going to be looking to ensure that their machines are used in the most optimal ways possible – which is always going to mean mixing and matching customer jobs.
The product planning parts of SigmaTek’s range allow you to bring together your job list for a specified period of time and then run through automatic grouping, scheduling and nesting operations, to ensure your machines and material stock are used in an efficient manner.
This gives you not only the tools to assign that work, but also systems on the shop floor to assist operators in setting up and executing the cutting operations, and managing stock as it goes into the process, as well as palleting up the end results.
Now, what’s left at the end of that process? Nine times out of ten, there’ll be a remnant of some description.
Once upon a time, these were managed poorly, with larger parts held in the stock room and the smaller stuff thrown in the scrap bin.
When the price of material went nuts, however, we all realised that, with a judicious application of technology, remnants could still be a source of decent income.
So how does SigmaNest handle remnants? The answer is that it does so at a couple of different levels.
At the base level, the system is able to store your remnants in its stock database.
It doesn’t just record their very existence, but also their precise shape. What this means is that a remnant can easily be factored into any subsequent jobs, and perhaps even prioritised once overburdened remnant racks start to groan.
Then, at another, higher level, the system can also start to factor your remnant preferences into future nesting processes.
Rather than leaving you with an arbitrary (albeit optimised) sheet shape, the system can factor nice, orderly shaped and sized remnants into its nesting processes.
It can ‘crop’ these sheets into standard sizes, and the material can go back into the stock list as a full, but smaller, stock sheet.
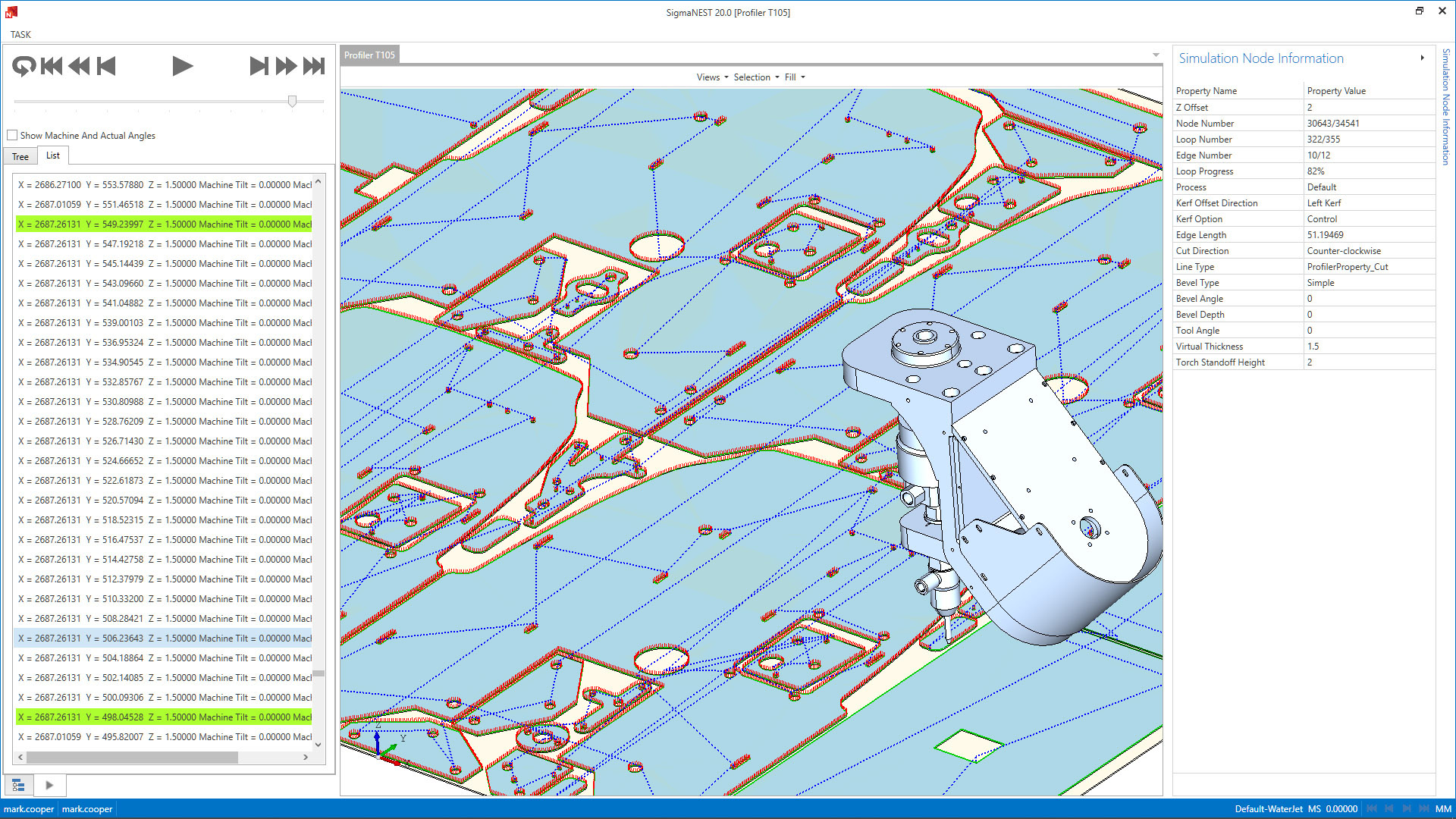
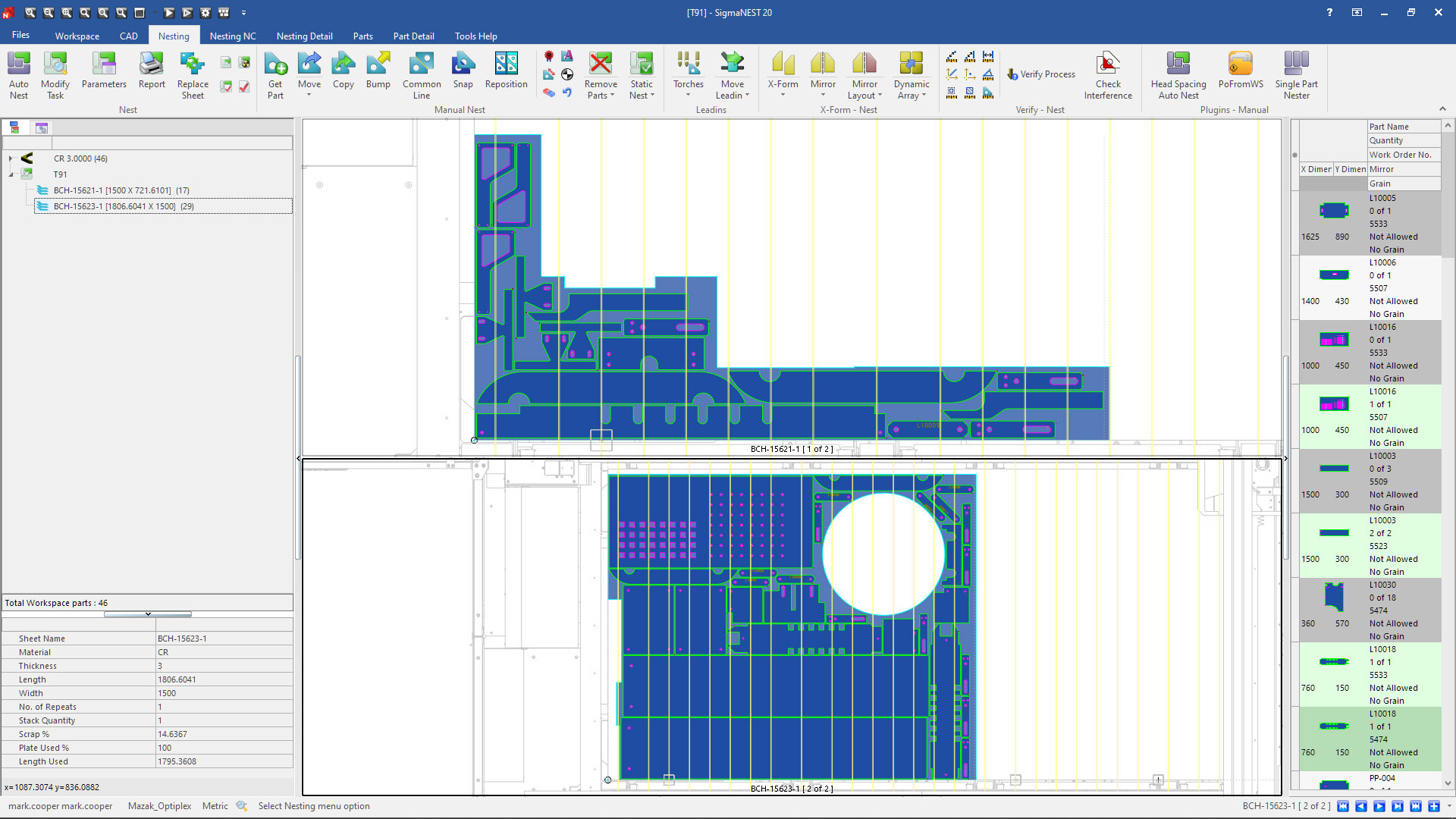
In conclusion
We’ve barely scratched the surface of what SigmaNest and its associated portfolio applications can do.
There really is something to handle everything you’d want to throw at it, from core sheet metal processing and programming tools, through work order and stock management, and into the realms of MRP and ERP integration.
If you’re in the sheet metal game, even if it’s a small element of a larger manufacturing and production enterprise, then there’s plenty to go at here.
And if you’re simply looking for a way to make more efficient use of your existing production facilities, the core parts of SigmaNest will pay some real dividends.
The nesting algorithms are first class and it’s clear that the team at SigmaTek has been working on this long enough to have built up a particularly interesting – and possibly unique – set of tools for squeezing every last bit of work out of your machines and your materials.
If you’re looking to take a more considered and efficient approach to your entire production process, then it’s very easy to see how the tools scale up to encompass additional areas of a manufacturing business – from quote creation to production planning, execution management, shop-floor feedback (this one is particularly impressive) and stock and scrap/remnant management.
We’ll come back to SigmaNest a little later on this year, but for now, if you’re involved in the sheet metal fabrication industry, it’s worth taking a look at what the company has to offer.
That’s particularly true if, up until now, you’ve relied on the tools available in mainstream 3D design and engineering systems. It’s entirely possible that you’ll never look at them in the same way again.
SigmaNest 20: Four new features that impressed
SigmaNest – Bevel cut with simulation:
The use of multi-axis cutting heads is increasingly common in the plasma and waterjet cutting world, as manufacturers push to differentiate themselves in an increasingly crowded market.
The issue is that programming these can be time-consuming. SigmaNest allows you to bring in 3D CAD files, or programme off the basis of 2D data, in order to get your machine producing the forms that your customer needs. It’ll also help you simulate the job at hand for the safety-conscious user.
Tube cutting:
While the SigmaTube module isn’t new, there have been some significant updates for this release. It already handles generating nests and NC code for tube and pipe cutting on laser and plasma machines, but Version 20 adds support for new inventory profiles, and tab and notch enhancements.
These are key for ensuring not only that you can programme complex tube forms, but also that each individual part is optimised as part of the complete job, which means the process should be more efficient.
SigmaNest – Bending of 3D CAD files:
While SigmaNest has traditionally relied on the 2D file format, this is changing. You can now bring in a 3D CAD file that contains folded-up representations of parts, perhaps tube components or sheet forms.
SigmaNest can now automatically assign the tasks that you need to perform in order to manufacture those parts. If you’ve got folded-up parts, for example, the system can quickly work through an unfolding analysis and create a simulation sequence of that part being folded on a press brake.
Standard feature library:
While SigmaNest is primarily aimed at the production of 2D nested parts, there is also clearly a move underway to support more complex forms, as seen in the tubing tools.
Another good example here is the SigmaDevelop module, which is a design system for standard ducting and HVAC geometry. You simply punch in the parameters needed for a standard form and the system will give you back the production files to produce those geometrical forms.