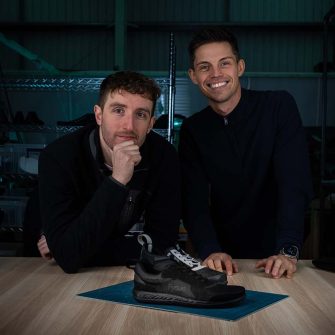
UK-based Fyous has announced the commercial launch of its Polymorphic Moulding technology, an alternative to 3D printing technology it claims is 20 times faster.
Polymorphic moulding is an automated pin tool moulding technology whereby a mould can be infinitely reconfigurable and reused in minutes, allowing Fyous to replicate mass manufacturing of custom parts economically or rapidly prototype new designs.
The patent-pending technology supports a wide array of materials and processes, including moulding, casting, vacuum forming and composite layup.
Fyous says that the pin tool shape shifts automatically in under 20 minutes using a provided 3D model, altering the 334 pins per square inch – the same surface area as a 50p coin, capable of holding 6 tonnes of pressure in its current configuration.
Stable at temperatures of 150’C and more, currently the max part size is 155 x 350 x 100 cm, with new moulds creating zero waste
“At Fyous, we believe in pushing the boundaries of what is possible in manufacturing,” said Joshua Shires, co-founder of Fyous. “Our new technology not only speeds up product development time, it removes the need for tooling making it much quicker and reducing time to market.
“This also means it is much cheaper than alternative options but also offers affordable customisation, which is crucial for applications that require interfacing with the human body from dental appliances to medical devices and sports equipment.”
Fyous has actively pushed the technology in the footwear sector, including custom shoes for diabetics patients to be quickly manufactured in more attractive styles, and is now actively seeking to establish partnerships across wider industry, including 3D printing companies and moulding and prototyping companies.
By collaborating with these technical partners, Fyous says it aims to further develop and deliver Polymorphic Moulding technology to market much faster, pushing the boundaries of manufacturing efficiency and customisation.
“We’re excited about potential partnerships that can help us scale and refine our technology,” said fellow co-founder Thomas Bloomfield. “By working with leading companies in the industry, we can accelerate the adoption of our technology and make a huge impact across various sectors.
“Polymorphic Moulding is a zero-waste technology where raw materials are conserved and moulds can be used again and again. We will remove not only the physical waste in the form of materials and tooling, but also remove wasted time by accelerating product development.”