As an aerospace supplier, RO-RA Aviation Systems GmbH is an expert in the production of complex, high-precision and difficult-to-machine components.
With around 190 employees, RO-RA has been developing and producing functional assemblies and precision parts primarily for the aviation industry since 2006, including both OEMs and their main suppliers, as well as contract CNC manufacturing. The products include rods, high-precision components and mechanisms used in civil aircraft, business jets, helicopters and their engines.
Based in Schörfling am Attersee, Austria, its customers demand maximum reliability for these key components, hence the its machining set-up needs to offer it the best possible performance.
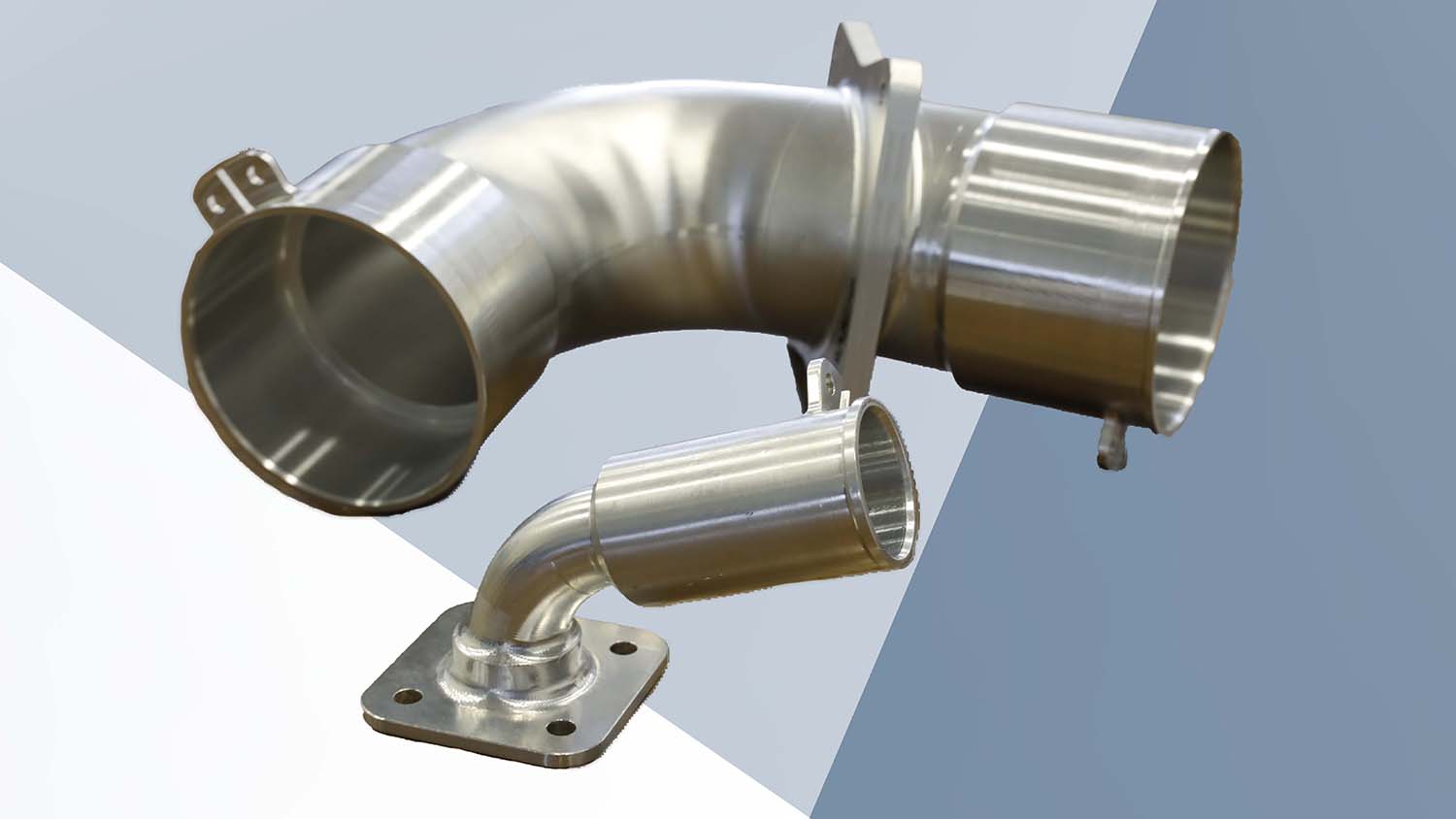
“Pre-development, calculation, design and qualification, as well as prototype production are essential components of our business model,” emphasises RO-RA managing director Helmut Wiesenberger. One success factor has been its digitalisation of development and manufacturing processes, optimising its years of machining know-how for light and often heat-resistant materials key to aviation product development.
“In addition to machining high-alloy steel, titanium and aluminium, we specialise in high-strength nickel-based alloys,” says RO-RA head of engineering Patrick Fellinger. “With our manufacturing technologies, we are able to produce highly complex geometries as well as gears very economically by means of skiving or hobbing.”
With more than 30 state-of-the-art machine tools and around 90 per cent automation, including 7 robot stations, workpieces up to a maximum diameter of 300 mm or 850 x 700 x 500 mm (X/Y/Z) can be machined almost around the clock.
Around 3,000 different designs, often having highly complex geometries, have been produced, all sharing the need to be highly accurate and have the best possible surfaces – a combination that makes cost-effective manufacturing extremely challenging. An example of this is the complex connectors made of aluminium for aircraft fuel lines, in which the machining rate is around 95 per cent. The component must also be non-conductive with perfectly processed surfaces.
Previously RO-RA experienced machine crashes despite its use of CAM simulation, resulting in costly downtimes and service calls. In order to avoid this and ultimately increase process reliability, RO-RA introduced CGTech’s Vericut simulation and optimisation software in 2018 after a selection process.
As Felling points out, CAM simulation only simulates the toolpaths and not the actual NC code. “With Vericut, we get a virtual machine and a machining digital twin. This means every travel path that we program is checked for 100 per cent process reliability,” he says, explaining the decision.
According to Fellinger, the software is also very easy to use, with RO-RA checking every milling program using Vericut for any errors before it is sent to the machine. “After all, only a production simulation of the NC data, i.e. the machine code, offers us sufficient security for all machining processes. The topic of crashes is definitely a thing of the past for us.”
Cutting down on errors
For a year now RO-RA has been using the Force module, in addition to Vericut, to further optimise its machining processes. Vericut Force is a physics-based software module for optimising NC programs – analysing the cutting conditions during the entire NC program operation.
In particular, the maximum reliable feed rate for a given cutting condition is determined based on the load on the cutting edge, spindle power and the maximum chip thickness. “So far, we have optimised 35 different components with Force and, depending on the material and complexity, have been able to reduce machining time by up to 25 per cent,” says Fellinger, summarising the results.
“We try to make the most of the production of our components in terms of program and tool technology – especially in the case of recurring parts. With Force, we now have another very simple lever with which we can further improve our competitiveness.”
Force is not about changing the milling strategies of existing programs or the toolpaths. Rather, everything is regulated by the feed to bring in additional advances. The geometries are not changed.
Force enables astonishing improvements, especially in the machining of materials that are difficult to machine and or complex multi-axis operations.
The head of engineering offers some insight into what it means to them when focusing on difficult-to-machine materials – CGTech on analysing an engine component for RO-RA was able to reduce the machining time by 18 per cent – reducing the time it takes from 12 to under 10 hours. RO-RA only had to provide CGTech with the Vericut project as well as additional information, such as the material, in this case Inconel 718, as well as certain limits, such as the maximum mean span thickness.
While the optimisation process, including the simulation, takes around two hours for a similar component – utilising a knowledge database with corresponding empirical values in the background – it also benefits from an improved cutting tool life, a claimed up to 40 per cent for Inconel or titanium.