As part of a UK’s effort to support the NHS in the fight against Covid-19, UK businesses from across the aerospace, automotive and medical sectors have joined forces to help produce more lifesaving ventilators needed for hospital intensive care units.
It’s the type of hands-on effort that’s hit the news headlines in recent weeks, but the task at hand has been explained in more detail by engineering experts Renishaw, members of the Ventilator Challenge Consortium.
Tens of thousands of these complex machines are needed in just a few weeks, and the reality of this is a stark prospect.
It’s a non-stop workload, concentrating on two proven ventilators, selected by the NHS and manufactured in the UK by Penlon and Smiths Medical.
Penlon and Smiths ordinarily have combined capacity of between 50 and 60 ventilators per week.
Using its extended resources, the consortium is aiming to push that figure to ‘at least 1,500 units a week’.
As part of this, Renishaw has dedicated a significant part of its manufacturing sites in Gloucestershire and South Wales to produce precision-machined components for the two different ventilators manufactured by consortium.
“When the government called, we scrambled to respond, and immediately realised the daunting scale of the challenge,” says Marc Saunders, director of group strategic development, who is leading Renishaw’s response.
“Ventilators are sophisticated medical devices and we felt that our capabilities would be best applied to helping scale up the production of designs with existing technologies.
“We soon realised that many other industrial companies were thinking the same way and that we would need our combined capacity and capabilities to achieve this enormous endeavour.”
Ventilators are intricate and highly complex pieces of medical equipment and the consortium maintains it vital that the twin imperatives of speed of delivery and absolute adherence to regulatory standards are needed to ensure patient safety.
This is a huge logistical operation – the mass-production of ventilators, each of which comprises hundreds of diverse components, requires millions of parts to come together for assembly, tricky at a time when measures must be in place to protect workers.
“We temporarily closed our UK manufacturing facilities last week to introduce additional measures to protect the welfare of our employees”, explains Gareth Hankins, director of group manufacturing services at Renishaw.
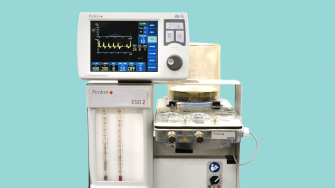
He continues, “We have reorganised our factories to increase spacing, as well as zoning areas to restrict movement around the sites.
“Hygiene regimes have also been enhanced to minimise the potential risk of the spread of infection.
“Our staff have responded magnificently to this challenging situation and it is wonderful to see the factories back up and running and for us to be playing our part in the national Ventilator Challenge.”
Marc Saunders reflects, “It has been an extraordinary few weeks, with so many companies from different fields aligning on a single goal and pulling together so effectively and so quickly.
“The consortium’s key message is that ‘Every ventilator produced is a life saved’ and Renishaw is proud to be playing its part in this vital endeavour.”