Designed to haul goods and passengers over the waves between coastal locations, Regent’s seaglider blends flight and sailing in a way that reduces the time and costs of transit. Stephen Holmes hears how the vehicle could pioneer a new form of zero-emission transportation
With 40% of the world’s population living in coastal communities, Boston, Massachusetts-based company Regent believes that its concept for electric seagliders will offer low-cost, high-speed, zeroemission transport for passengers and freight.
Operating only a few metres over the water as an all-electric wing-in-ground (WIG) effect vehicle, the seaglider can travel in one of three modes: floating on its hull near the dock; foiling on its hydrofoils at up to 40 knots (kts) as it comes in and out of port; or flying above the waves at 160 kts while cruising to its destination.
When in flight, it relies on the ground effect phenomenon, flying on a cushion of air that allows it to combine the high speed and comfort of an aircraft with the low operating cost of an electric vehicle.
Regent’s design differs from past WIGs due to its hydrofoils, distributed electric propulsion and aerospace fly-by-wire controls. These elements enable safe harbour operations, increased wave tolerance and a comfortable passenger experience.
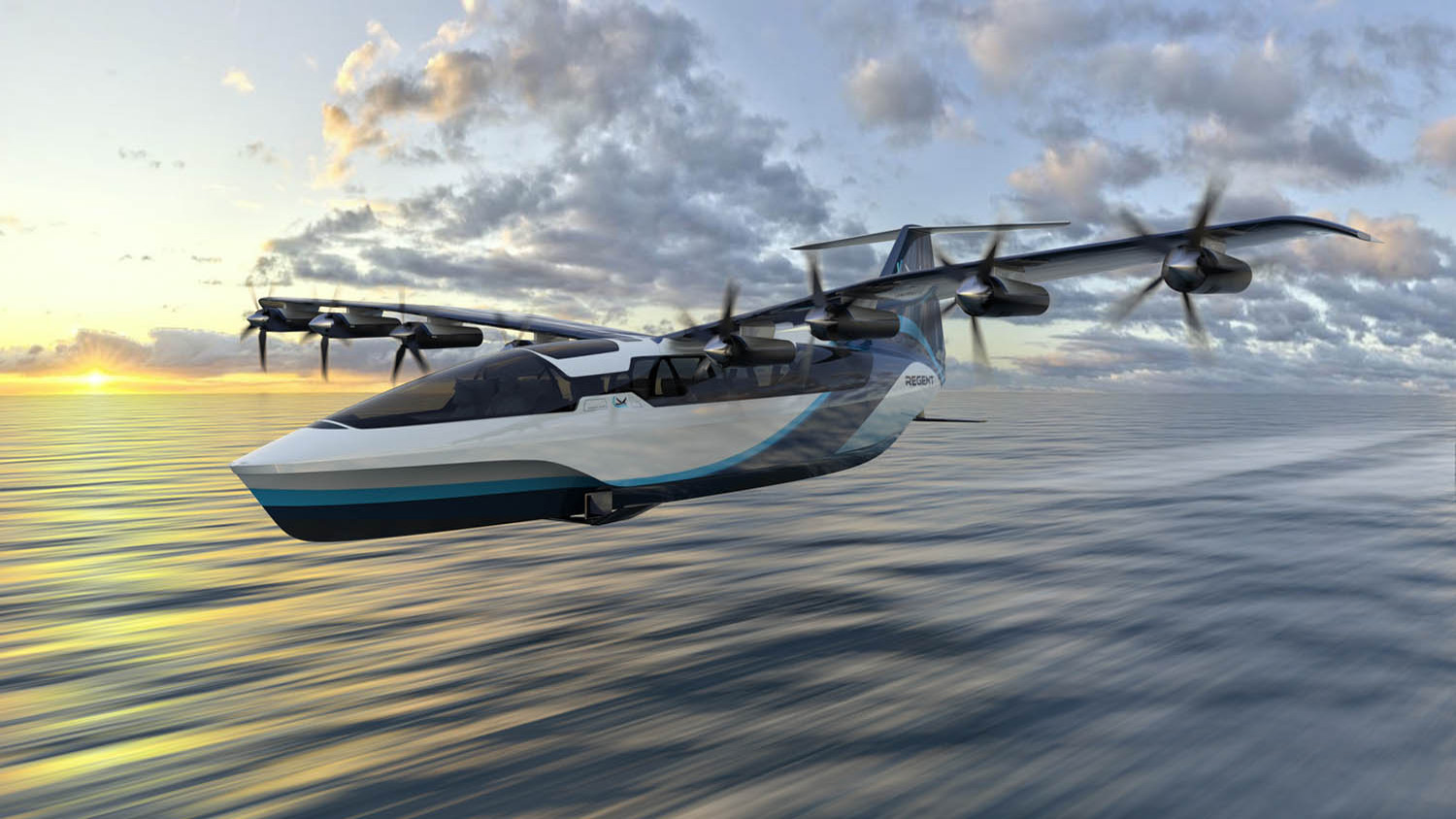
Going the distance
Regent’s flagship seaglider, the 12-passenger Viceroy, will be able to service routes up to 180 miles in distance with existing battery technology. It expects to cover routes of up to 500 miles in the near future thanks to nextgeneration batteries, all via existing dock infrastructure.
Additionally, its operation as a WIG effect vehicle above the water supports maritime testing and certification. This is an efficient pathway to entry into service, allowing customers to experience high-speed, zero-emission coastal mobility sooner than electric aviation options, while maintaining similar levels of safety. “
At Regent, we are focused on bringing a revolutionary new vehicle to the transportation market with the potential to change how both people and freight move over the water,” says Regent CTO and co-founder Mike Klinker.
“As our seagliders approach certification and full-scale commercial production, we need a robust, modern digital tools platform that supports the pace of our innovation cycles with the rigour to encompass a product as complex as ours.”
Klinker says that being a “digital-first start-up” led it to Siemens Xcelerator as a Service, when the company was choosing software to meet its design and engineering needs back in 2020.
“At Regent, we are moving very quickly. We went from a blank sheet of paper to an 18-foot wingspan, 400lbs technology demonstrator on the water in 10 months,” says Bryan Baker, Regent’s chief engineer for vehicle physics.
Baker describes his background, in common with many others in the design and engineering team, as being grounded in professional racing and prototyping, whether that be in aerospace, motorsports or America’s Cup sailing.
“The team is very multidisciplinary. We pay special attention to critical design tasks, prioritising solutions with real-world application and delivered on time with the greatest chances of success. The success of the team relies on getting a working product from which we can iterate improving safety and performance throughout the entire architecture,” he says.
On-demand tools
Baker says that at different times, members of the team can have “bursts of software demands to follow the cadence of our design.”
This means they require specific software tools at varying frequency, which the cloud-based platform offers while reducing cost.
“I’ve been using cloud services for years now and the ability to scale compute resources like HPC, and matching that with different on-demand licences, is a very useful tool,” he says.
For aerodynamics, the team relies heavily on STARCCM+ and on NX for CAD modelling, as well as coupling Simcenter Structures for mechanical design and tolerancing.
“We use FEMAP as our mainstay for structural FEA, using it for both global and local modelling,” adds Baker.
“We are now getting into Fibresim to better model our material drops and hopefully leverage ply-cutting tools in future designs, as well as optimise material purchases.”
Teamcenter is being assessed for organising and tracking CAD and trade-study data, as well as best practices to develop a certification path with maritime authorities.
“As we continue to grow, I hope to leverage these tools both internally and with our ever-growing contractor and builder relationships, to ease the communication and reliability of our designs,” says Baker.
”The goal is getting from prototype to production while growing a world-class team able to transfer our knowledge without losing calendar and keeping costs down. We hope to do just this leveraging Siemens and a flexible cloud solution.”
While the craft won’t reach heights of more than a few metres from the water’s surface, this transformative mode of transport is definitely benefitting from the cloud.