Industry leader Formlabs reveals its secret weapon for a smoother, faster, error-free product design phase: the cloud-native collaborative CAD and PLM platform Onshape
The past three years have forced us to drastically change the way we work and designers and engineers are no exception. But while for some jobs the transition from in-office to remote work was only a matter of providing employees with the same tools they’d previously use, for those working in the engineers field, who need to collaborate on complex projects with big teams of specialists spread all around the world, finding the right platforms it’s been more challenging.
To facilitate remote work, speed up the design and development process and reduce errors, the 3D printers manufacturer Formlabs relies on Onshape’s real-time collaboration platform.
Onshape doesn’t only allow engineers to concurrently work on a design rather than being forced into a serial workflow, but it also means that Formlabs teams no longer experience delays due to software crashes or corrupted files due to Onshape’s cloud-database architecture.
Formlabs said that Onshape’s built-in PDM system enables its teams, spread all around the world, to work with a single source of truth, eliminating version control issues during the collaboration process.
Before the adoption of Onshape, when multiple engineers were working on the same file-based CAD model, they were required to check their work in and out of a PDM vault to prevent version control issues, denying visibility to colleagues until they are finished editing.
File-based data management platforms are used to force serial workflows, requiring engineers to work one at a time instead of concurrently.
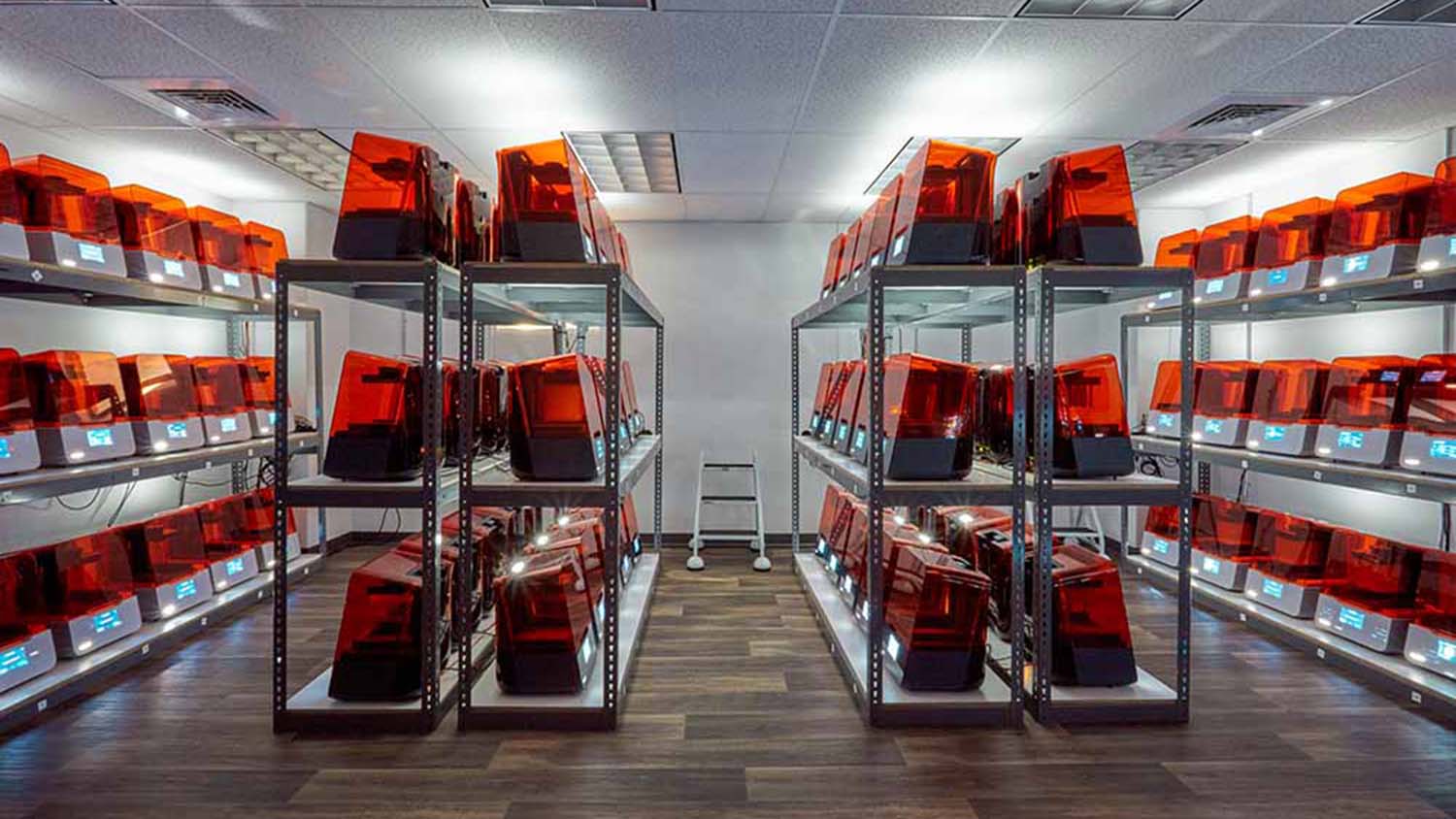
In contrast, cloud-native Onshape’s real-time data management allows multiple engineers to simultaneously work on the same product model, seeing each other’s design changes as they happen. A comprehensive ‘edit history’ tool tracks every design change, who made them and when, allowing the team to instantly revert to any earlier stage of the design if desired.
“It’s critical to reduce waste in any design process,” says Matt Lipsitz, head of sustaining engineering and quality at Formlabs.
“And one of the great ways to do that is to know that when you’re looking at something, you can trust it is the latest iteration. So any time you have to go back and rebuild a model or redesign something because it wasn’t saved correctly, that’s a waste. It’s hugely valuable for our engineers to know that what they’re looking at is the latest version.”
“In my current role, I need to collaborate with people globally. My colleagues or partners might be in the Far East, Europe or across the United States. So I need to be able to show them the latest CAD model in a matter of seconds – and it’s imperative that we’re all working from that same single source of truth,” he adds.
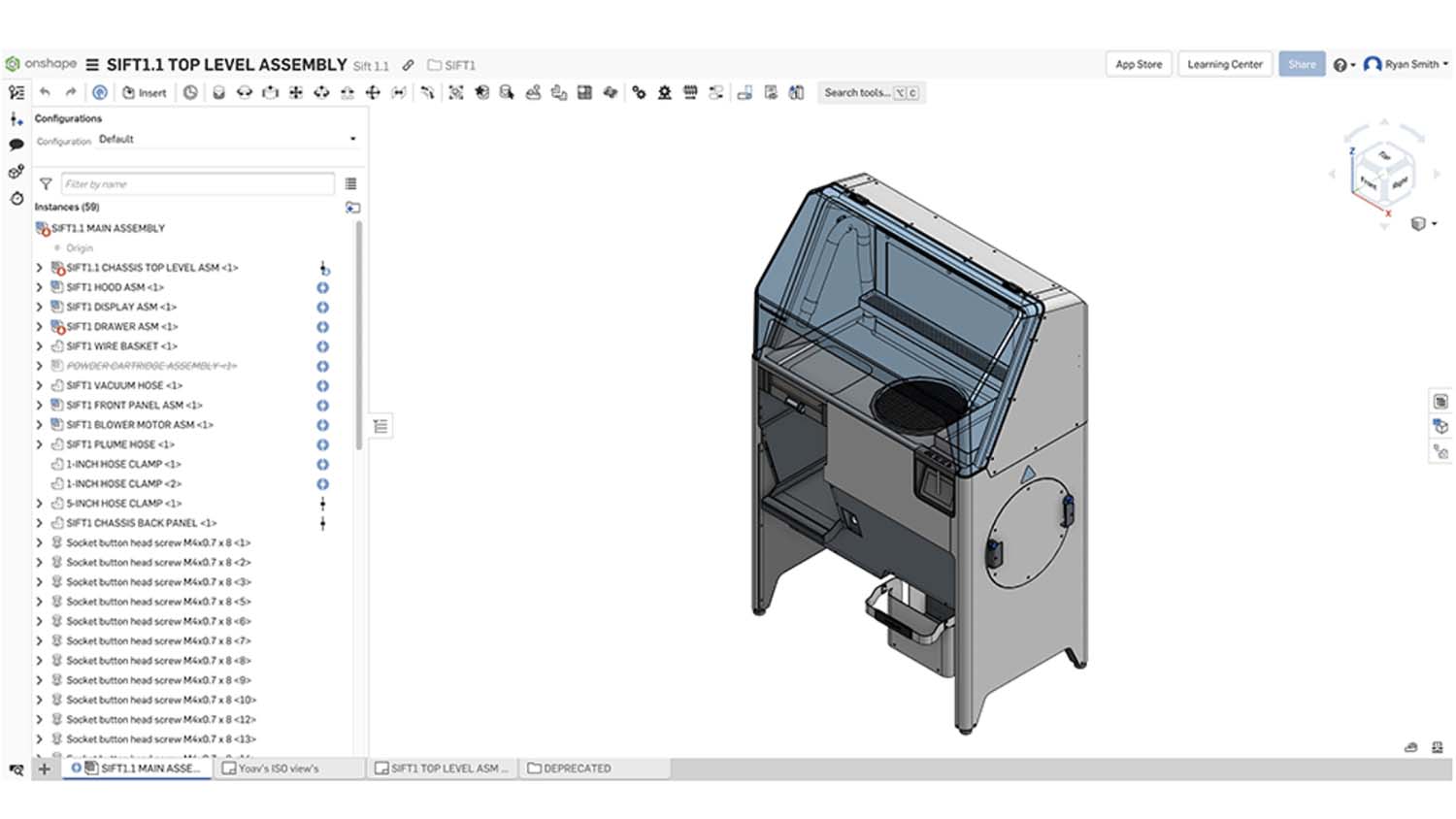
According to Lipsitz, another major benefit of cloud-native Onshape is the certainty that design work won’t be lost because of data corruption or computer crashes, issues common with on-premise, file-based systems.
“The way Onshape is designed, there is no need to remember to save our designs mid-workflow,” he says. “It’s always being backed up automatically. If a computer crashes, you can just move to another computer and continue right where you left off. The stability of the software has been a great boon to us.”
As a Software-as-a-Service (SaaS) platform, Onshape regularly releases updates in the cloud every three weeks, adding new features and functionalities requiring no downloads or installs.
“With Onshape, there’s always continuous improvement. Our engineers get excited to see what new features have come out in the last release and what features we may have requested that were recently deployed,” says Lipsitz. “That iterative cycle is refreshing. It feels like there’s always something new – as opposed to an on-premise system that may be updated only once a year.”
“Any time engineers are not actively working on design projects, they’re not adding value to the company. So we want to pursue any ways to eliminate downtime,” he adds. “And cloud-native software takes servers, maintenance and other IT tasks out of our hands, saving time and reducing the burden on our engineers.”
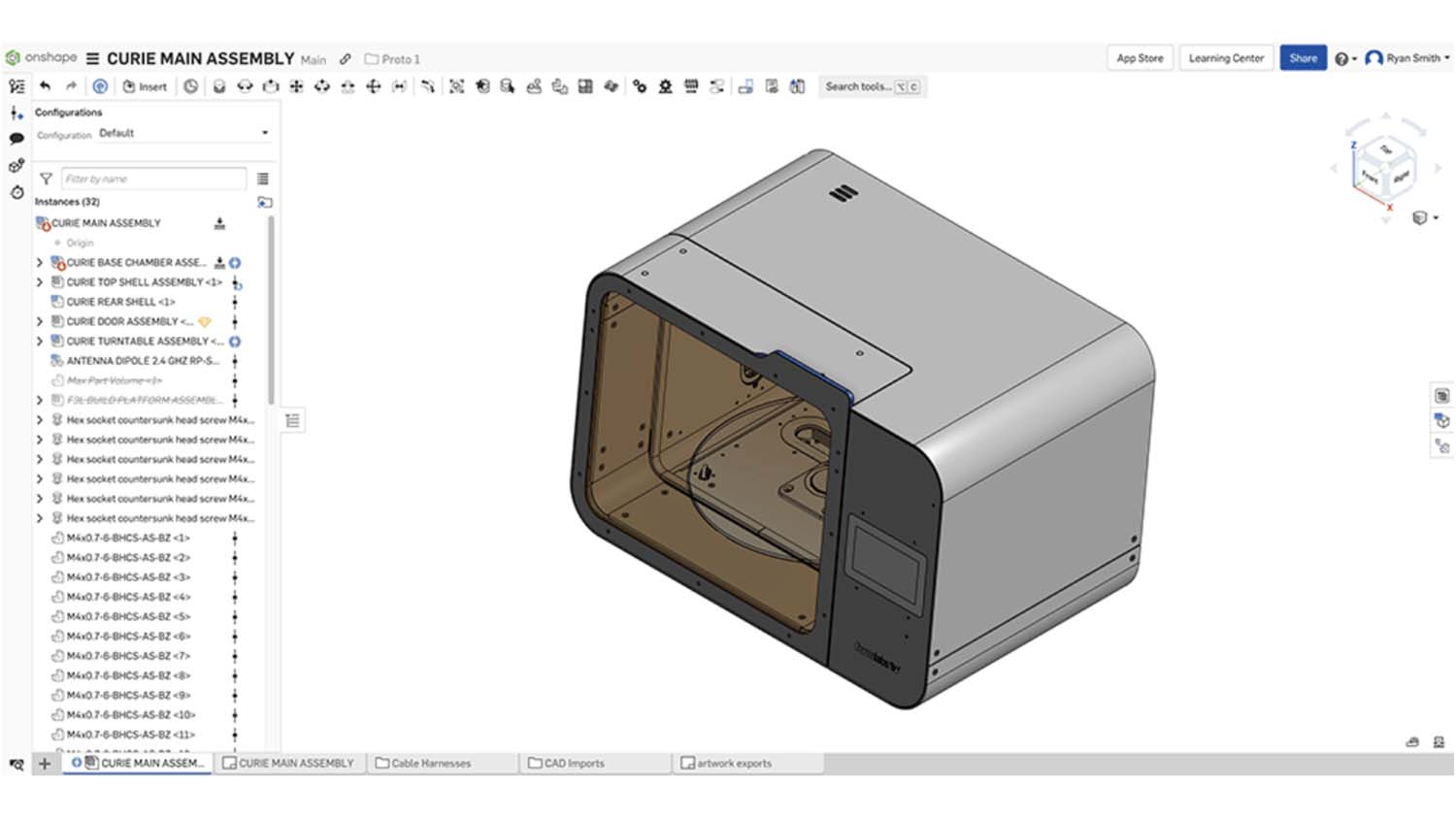
As Formlabs continues to develop new additive manufacturing technologies and expand to new applications, Lipsitz maintains that Onshape will remain especially valuable for helping to accelerate the onboarding process for new engineering hires.
When scaling up a project, Onshape users can grant immediate access to colleagues by simply entering their email addresses, versus waiting days or weeks to obtain additional CAD licenses with on-premise vendors and requiring assistance from IT.
“Onshape really reduces the barrier to onboarding engineers,” Lipsitz says. “The fact that it’s based in the cloud means that we don’t need to install any software, and we can add a new user with the click of a button, as opposed to having to install and link to a PDM system, and then teach somebody how to access it. Onshape runs right in your browser so somebody is good to go and can start designing parts right away.”
“We recently realized these same benefits on a project with an overseas supplier who was willing to adopt Onshape for joint engineering development of a new product. The ability to integrate an external partner into our engineering toolset shifted the traditional relationship from a transactional one to a collaborative one,” he concludes.
Onshape collaborative tool is helping Formlabs in its goal to allow “anyone to make anything” and its company mission, summarised in the analogy that sees Formlabs being “manufacturers’ Swiss Army knife”. Thanks to new generation tools, the Massachusetts-based 3D printing manufacturers are now looking to expand AM to the application that goes beyond R&D and prototyping and move from strictly automated manufacturing to mass customisation.