Spare parts produced by additive manufacturing open up a world of digital inventories and customer convenience. Stephen Holmes met with Replique, a start-up steering big brands through the potential pitfalls, and to discuss its recent work with Miele

In May 2020 domestic appliance manufacturer Miele started its 3D4U project to provide customers with free designs of 3D printable accessories, a bold step for the brand renowned for its commitment to reliable products.
Starting with three accessories available through its online shop – a coffee bag clip, and two specialist vacuum cleaner attachments – Miele was taking the first steps toward flexibly expanding its product portfolio.
However the immediate success of the project led to the Miele looking to enable greater access the designs for customers with no 3D printer.
“We have a beautiful maker community in Europe, but the number of people who don’t have a 3D printer is greater,” says Max Siebert, CEO of digital inventory start-up Replique from its base on BASF’s Chemovator incubator campus in Manneheim, Germany.
Immediately after the launch of the 3D4U project Siebert contacted Miele, to offer Replique’s expertise in additive technologies and materials, to safely scale production globally.
“We are working for various industries – transportation, agriculture, gardening – you see that all of those have the same issues at times, which is getting hold of spare parts,” says Siebert. The parts themselves might be simple components, but the volume requested is comparatively small scale, so additive manufacturing is very appealing.
Siebert adds: “It’s a new manufacturing technology that has really matured in the last years to become a very controlled industrial process, and I think this is now a good example of how people will start using this technology for certain niche applications and also to expand it.”
Yet for many companies, even with huge amounts of manufacturing expertise, 3D printing is still littered with unknowns, therefore partnering with a company that can make this process as smooth and pain free as possible offers huge benefits.
“They’re very happy to have somebody who has a very proficient knowledge in materials and can judge which material and technology route you should take, so there’s also a little consulting aspect here, because 3D Printing for end use parts is still very young – we’re not talking about prototypes.”
Siebert explains that while many services produce prototypes, where speed is the main driver, the key to end-use parts is purely quality. Take for instance the coffee clip – the part needs to be built with the expectancy it will come into contact with foodstuffs.
For Replique this meant researching a full food-safe production process, beginning with materials. “There are really only a few food-safe certified materials, not just saying that it is ‘generally food-safe’ but that it is certified,” explains Siebert.
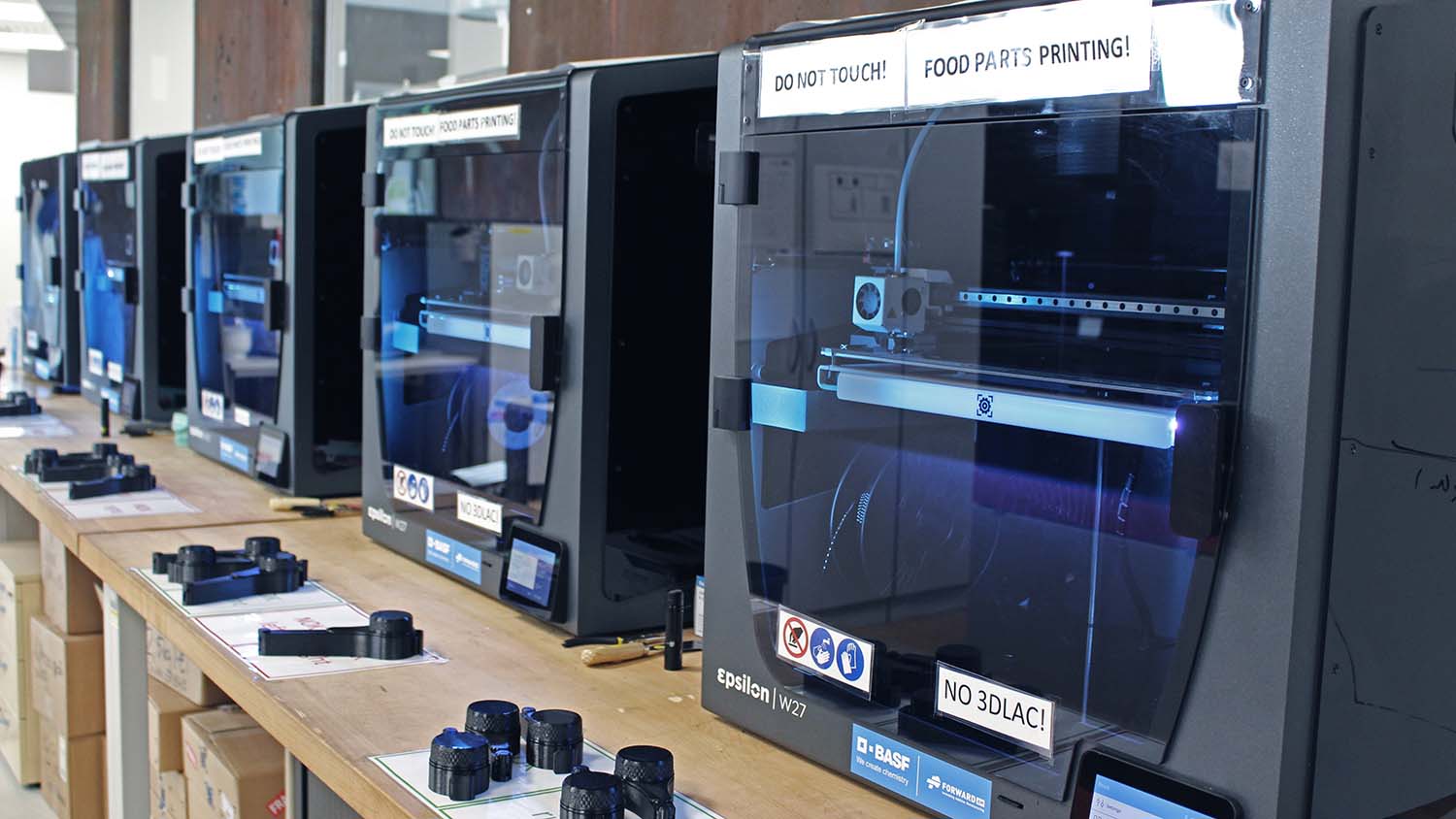
Replique does not produce the parts itself, instead it works with its vetted production partners that include BASF 3D Printing Solutions, making it technology, materials and process agnostic, as well as having a global reach.
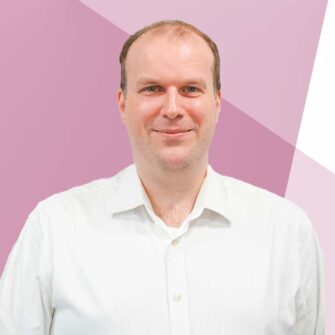
Siebert’s team are already working across various industries – in transportation, agriculture, and even gardening products, which all have similar problems.
“You see that all of those have the same issues at times, which is getting hold of spare parts.
“The parts might be simple,” he says, “but [the volume] requested is small scale, so they’re very happy to have somebody who has a very proficient knowledge in materials and which technology route to take.”
One client that produces powertools found that its long guarantees offered on products meant that requests for spare parts were still being received long after the original product had ceased production. In this case Replique was able to step in and help maintain supplies without the need for the long lost original tooling.
Having proficient 3D printed parts suppliers and a close partnership with the client means that Replique can also help offer design for AM advice, helping tweak or optimise parts to make them more robust or save material.
Siebert believes that more industries are further targeting this sort of process, either to produce spares on demand, or for assessing product demand for appliance accessories.
“In the past you only produced parts where you were sure that you [would have demand for] hundreds of thousands of those, but now you can produce way more parts because the complexity of managing those parts is not that high.”
With a quality assured system, consumers will be able to rest easy knowing that the products – ordered online and shipped direct to them – will have the same characteristics as the original, while manufacturers won’t be faced with a complex warehousing and supplier network.