The FX10 Metal Kit from Markforged adds to the 3D printer’s versatility, allowing it to print both metal filaments and composites with continuous fibre reinforcement.
The FX10 Metal Kit consists of a swappable print engine that includes a metal-specific print head, material feed tubes, routing back and dual pre-extruders.
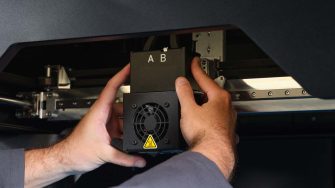
The 3D printer can be swapped between metal and composite as many times as needed, with each swap taking around 15 minutes.
The FX10, released in November 2023 as a composite only printer, was designed to be the most versatile tool on the factory floor with a modular architecture allowing for upgrades like the Metal Kit, letting users gain additional value from their system.
“Customers no longer have to choose between a metal and a composite printer,” said Markforged CEO Shai Terem.
“Years of R&D investment and field experience have come together to provide an all-in-one solution for 3D printing to provide immediate return on investment once installed on a factory floor.”
Terem goes on to say that the FX10 can “supercharge other equipment on the factory floor” to be better used and run more efficiently, increasing productivity and reducing potential line down events.
Markforged has also announced a new 316L stainless steel metal filament to be used with the FX10 Metal Kit. Users will also be able to print in 17-4PH with additional support for other Markforged metal filaments in the future.
“We designed the FX10 to be a modular platform, so that we are able to release new innovations and upgrades without customers having to purchase a new printer every year,” continued Terem. “Along with new software capabilities we release regularly, the FX10 Metal Kit is poised to provide continuously growing value on factory floors for years to come.”
Similar to its Metal X 3D printer, the metal prints are built from the metal filament and a ceramic release filament. The ceramic release is extruded as an interface between the part and supports for ease of separation and removal.
Once metal prints are complete, they must be washed and sintered in Markforged’s Wash-1 and Sinter-2 solutions. Eiger, Markforged’s slicer and print management software automates the process, including scaling parts to account for shrinkage during sinter.
Cut to fit: How Guhring use 3D printing for custom cutting tools