Desktop Metal has announced new software for its additive manufacturing systems, including new GPU-powered sinter-simulation technology Live Sinter, and new binder jetting support from Materialise.
Live Sinter simulation software corrects models for shrinkage and distortion inherent of the binder jet metal 3D printing process during the sintering process, helping minimise the trial and error.
Desktop Metal Live Sinter claims to achieve near-net shape parts post sintering, achieving tight shape and dimensional tolerances, while reducing the need for sintering supports.
“We believe Live Sinter will be a critical companion in continuing to drive forward the success of additive manufacturing,” said Desktop Metal CEO Ric Fulop.
“As manufacturers look to capitalise on the flexibility of volume production delivered through technologies such as binder jetting, Live Sinter is a first-of-its-kind solution that offers a path to predictable and repeatable outcomes by demystifying the sintering process.”
Live Sinter can be calibrated to a variety of alloys, predicting the shrinkage and distortion, creating ‘negative offset’ geometries that, once printed, will sinter to the original, intended design specifications.
These negative offsets are the result of a GPU-accelerated iterative process, in which the software proactively pre-deforms part geometries by precise amounts in specific directions, allowing them to achieve their intended shape as they sinter.
Desktop Metal states that the multi-physics engine’s dynamic simulation is refined using an integrated meshless finite element analysis, which computes stress, strain, and displacement across part geometries used to predict not only shrinkage and deformation, but also risks and failures, validating the feasibility of a part for sintering-based additive manufacturing before the build begins.
The software is claimed to calculate offset geometries in ‘as little as 15 minutes’, compared to more general-purpose simulation tools that can use complex meshes and require complex setups and hours to complete.
In addition to this, Materialise has announced the introduction of a Desktop Metal Build Processor, capable of translating 3D designs into machine-specific build files for Desktop Metal machines, as well as sintering support generation as part of Magics’ SG+ module, and metal Binder Jetting enhanced 3D nesting.
This integrated solution, compatible with Materialise’s software suite, aims to target companies looking to scale their metal 3D printing operations and add improved machine connectivity by offering manufacturers more insight into the production process.
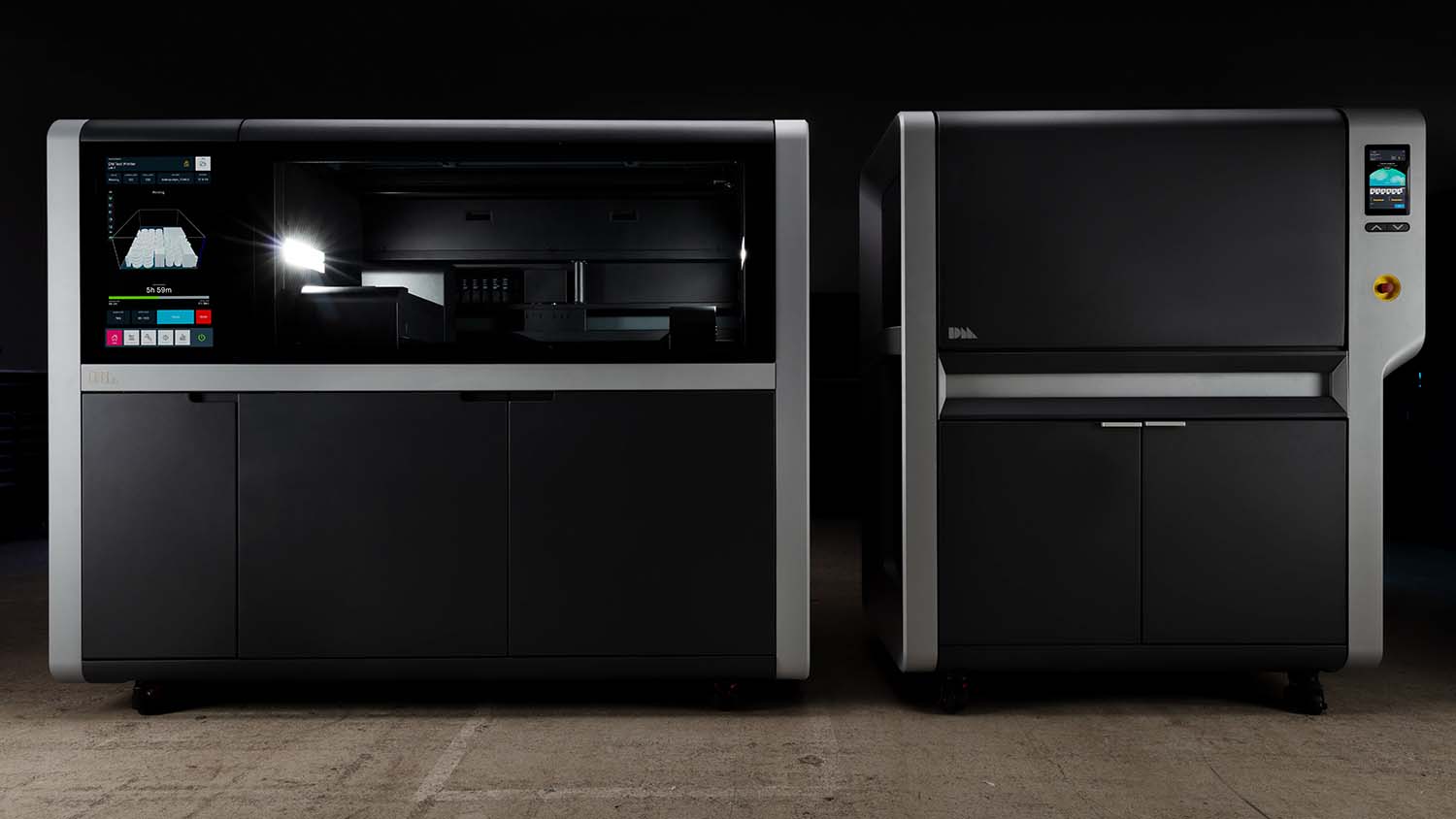
“Our partnership with Desktop Metal supports our next-generation Build Processor strategy to remove some of the remaining barriers to adoption of 3D printing as part of a connected, industrial manufacturing process,” said Materialise Software VP and MD Stefaan Motte.
“Removing barriers of speed, scale and cost requires a closer integration between software and machine.”
Desktop Metal will make the Build Processor available as an add-on software offering with its advanced metal 3D printing solutions, the Shop System for mid-volume manufacturing, and the Production System for high volume mass production.
“The combined strength of our metal 3D printing solutions with Materialise’s three decades of experience in 3D printing software and application development will help to accelerate the transformation of manufacturing with end-to-end metal 3D printing solutions,” said Arjun Aggarwal, VP of product and business development at Desktop Metal.
With the introduction of its Machine Connectivity Pack, as part of Materialise Streamics 8.2, Materialise appears to be paving the way towards a more open market model that can offer users further insights into their operations, and unlock the further potential by monitoring and analysing build data.
“We believe access to build data is crucial to advance our industry and usher in a new era of industrial scale additive manufacturing,” added Stefaan Motte.
“That’s why Materialise has always advocated open connectivity standards. I am excited that leading machine vendors such as Desktop Metal, share our beliefs and support machine connectivity through open standards such as MT Connect and OPC-UA.”