Direct energy deposition (DED) 3D printing is shaking off its niche roots and proving its value to designers with its scale, materials and speed of delivery. Stephen Holmes speaks to experts in the field of DED about why this technology should be on your radar
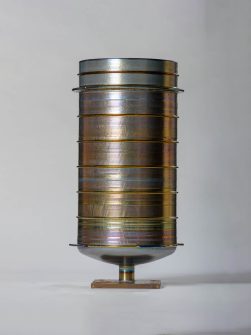
Despite relentless advances among the kinds of 3D printers we’re more used to seeing, a much bigger, hotter beast is promising to shake up the sector. Along the way, it could utterly transform how large parts and structures are designed and manufactured.
Direct energy deposition (DED) 3D printing involves a robotic arm, equipped with a heat source capable of melting either jetted powder or wire-fed or metal stock to form a solid bead of material that is built up into a close approximation of the required design. Being able to control the printhead across four, five or seven axes, it can create impressive geometries and angles without the need for support materials.
Typically, this process produces a near net-shape part, which can then be CNC-machined back, where necessary, to reach the exact final tolerances required.
Initially expensive and time-consuming, the process began as a niche means of repairing or replacing highcost or super-important parts faster than a casting could be produced or a replacement part shipped.
As the technology has evolved, however, the process has sharpened up. Vendors now offer more refined systems, software and materials. And, as a result, DED has transitioned over the past decade from a glorified automated welding solution to a genuine additive manufacturing (AM) process, capable of delivering tangible design, material and supply-chain benefits.
DED – rules of AM apply
The bigger the part and the more elements it includes, the more DED has to offer, says Robert Bowerman, a technical consultant at Autodesk and a former AM research engineer at the Manufacturing Technology Centre.
“The key value propositions of AM are unchanged from desktop to DED: efficient use of material, energy only consumed to create the material you need, and the toolless nature of the process enables manufacturing freedoms that in turn enable design freedoms for more optimised designs,” he says.
The process from digital design to final component involves far fewer steps than traditional manufacturing, and with part consolidation, can create more efficiency, adds Jeff Jaje, multi-axis AM product manager at Siemens Digital Industries Software.
Jaje says that cost and lead-time differentials between other manufacturing methods can be more pronounced, making a DED approach on large parts, “very attractive, especially when manufacturing with materials that can be difficult to manufacture otherwise, or if there can be a reduction in downstream processes.”
Much of this comes down to replacing traditional physical processes with digital, says Mathieu Pérennou, global business development director for AM at Hexagon’s Manufacturing Intelligence division. “Optimising deposition production processes may entail taking advantage of powerful simulation tools, state-of-the-art scanning technology, robust reverseengineering and analysis software, or a combination of all of these technologies to achieve the required quality and repeatability.”
3D printing parts to near net shape and CNC machining them back to exact tolerances not only has speed savings, but in terms of raw materials, the effect can be eye opening.
In a project for Thales Alenia Space, WAAM3D, Cranfield University and Glenalmond Technologies produced a full-size prototype of a titanium pressure vessel to be used in future manned missions for space exploration. The 1m tall, 8.5kg vessel was built using DED from titanium alloy Ti-6Al-4V. By using this AM method, the team used 30 times less raw material than if the vessel had been created via traditional processes.
Put another way, that’s more than 200kg of Ti-6Al-4V saved for each vessel produced.
DED – space for growth
The space and energy sectors have been fast to jump into DED. Their requirements for shorter supply chains, faster lead times and lower component cost, even on less noble materials such as steel, is playing a huge part, says WAAM3D CEO Dr Filomeno Martina.
The space sector is particularly excited by DED, with parts like fuel tanks taking full advantage of the design freedoms offered by 3D printing, allowing them to be optimised for volume, while simultaneously working within the packaging limitations of the vehicle.
“The business case here works well and the stories that can be told are inspirational, therefore the momentum has snowballed,” notes Bowerman, adding that take-up is spreading to verticals such as marine, defence, mining, and other heavy-industry sectors, as well as mould manufacture, “where the opportunities for AM are large and the route to qualify parts is (relatively) shorter.”
End-use parts are not the only sector to benefit, according to Terry Turner, DMG Mori UK business development manager for AM. He says that the tooling sector for traditional technologies such as injection moulding and die casting can hugely benefit industries like automotive, “whereby large-scale AM can be used to enable innovations in heat transfer and more effective repair or change for large and high value tooling components.”
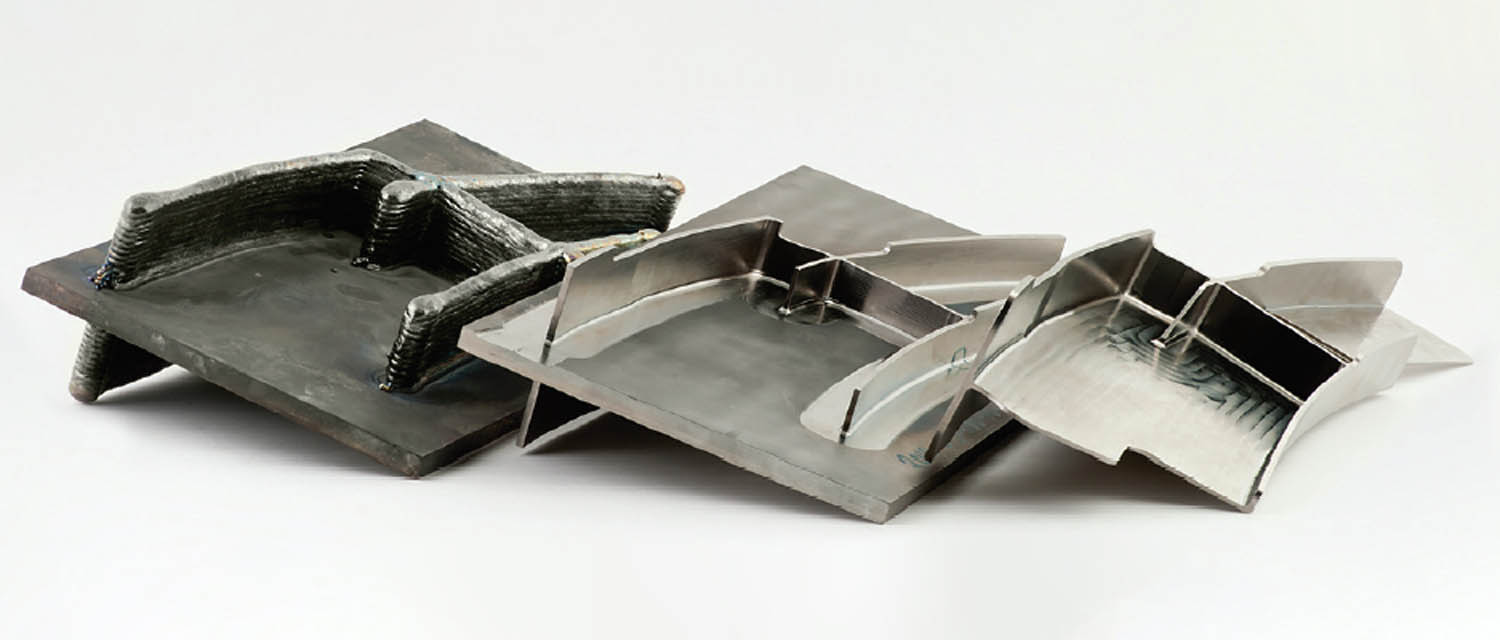
The ProM Facility in Trentino, Italy, is taking repairs to the next level using DED AM for high-value parts using a DMG Mori Lasertec 65 3D Hybrid system capable of both depositing metal and machining it back.
ProM AM engineer Matteo Perini explains that his team is able to combine different metal powders to obtain functionally graded materials with unique properties in order to upgrade existing parts.
“For example, cladding could be performed with wearresistant, heat-conductive or magnetic materials,” says Perini. “In our lab, the ProM Facility, we are now working with more than 20 different materials, and we continue to test additional materials and their combinations. Our machine allows us to mix powders, thus creating completely new alloys.”
Turner agrees that this is one of the most exciting outlooks, “whereby a designer can choose to have one material in one location of a part, and have that gradually change to a different material in another location”. This, he explains, will enable new possibilities in thermal optimisation, mechanical performance, and not least production costs, whereby a part can have expensive material only where needed.
The next stage of DED is the evolution of its materials, but at present, much of this revolves around its key markets like aerospace.
Nickel-based alloys such as Inconel, or titanium alloys like titanium aluminide, can be very difficult to machine, making them particularly attractive for DED AM, says Jaje.
He explains that “significant” savings in programming and machining time can be gained using AM, leaving only the necessary areas to require machining, “versus machining the whole part from a solid block.”
Given that the feedstock can be in the form of wire or even powder, says Perini, the different DED AM processes can make it possible to process “difficult materials” such as tungsten carbide, Stellite or tool steels.
AM is of course very different from casting and forging in terms of thermal cycles and requires new chemistries that match the process, adds Martina, explaining that WAAM3D has looked to accommodate this with a range of aluminium-based alloys, including scandium and other niche elements that he says work extremely well with WAAM3D’s wire-arc process particularly.
For wire-fed DED, the process of making the wire itself has seen significant improvements, helping add geometric stability and improved surface characteristics, together with larger spools and more controlled packaging.
Building momentum
Taking all this into account it seems that for at least some industries the technology is ready to make an impact, but what is holding back it’s wider adoption?
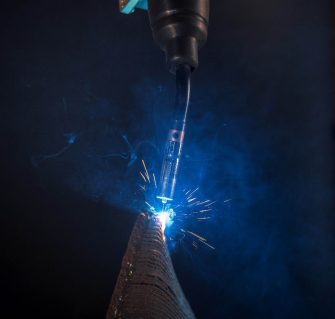
“In general, the technology is industry ready, and designers, engineers and system providers need to work together closely to ensure that genuine business cases for adoption can emerge from what is now available to us,” opines Turner.
Perini is convinced that in the future the technology will be widely used across a diverse swathe of industries, but that it’s “up to designers and engineers to imagine how things can be done and thought of in another way”.
He mentions the growing interest the technology is finding from the worlds of art and architecture, and how the construction of metal shapes simply unimaginable a few years ago look set to give designers new and surprising freedoms.
Martina suggests that other, more pragmatic reasons will aid adoption. “In AM properties and geometries are created at the same time,” he says. “Therefore, we have moved away from more traditional part-based qualification and are focusing on advanced process monitoring and control, especially around fundamental variables such as thermal field and real-time defect analysis and characterisation.
“By looking at the process as a whole, the validation process is quicker, unlocking the potential for continuous design improvements (as there are potentially no retooling costs) as well as mass customisation.”
Software matters
Additionally, software tools have become better at handling fully integrated design and manufacturing, helping users to design for the production process. This is necessary for large parts, says Siemens’ Jaje, as often additive and subtractive operations are alternated as necessary during the creation of the part. “Multi-axis tools allow for creating more complex parts and provide features helpful to the DED process,” he says.
“At Autodesk, we are doing this through our Fusion 360 product, implementing a hybrid manufacturing workflow that sets a new bar for accessibility,” adds Bowerman of his company’s move to lower the barrier to adoption by putting capabilities in the hands of the design team and not just the engineers.
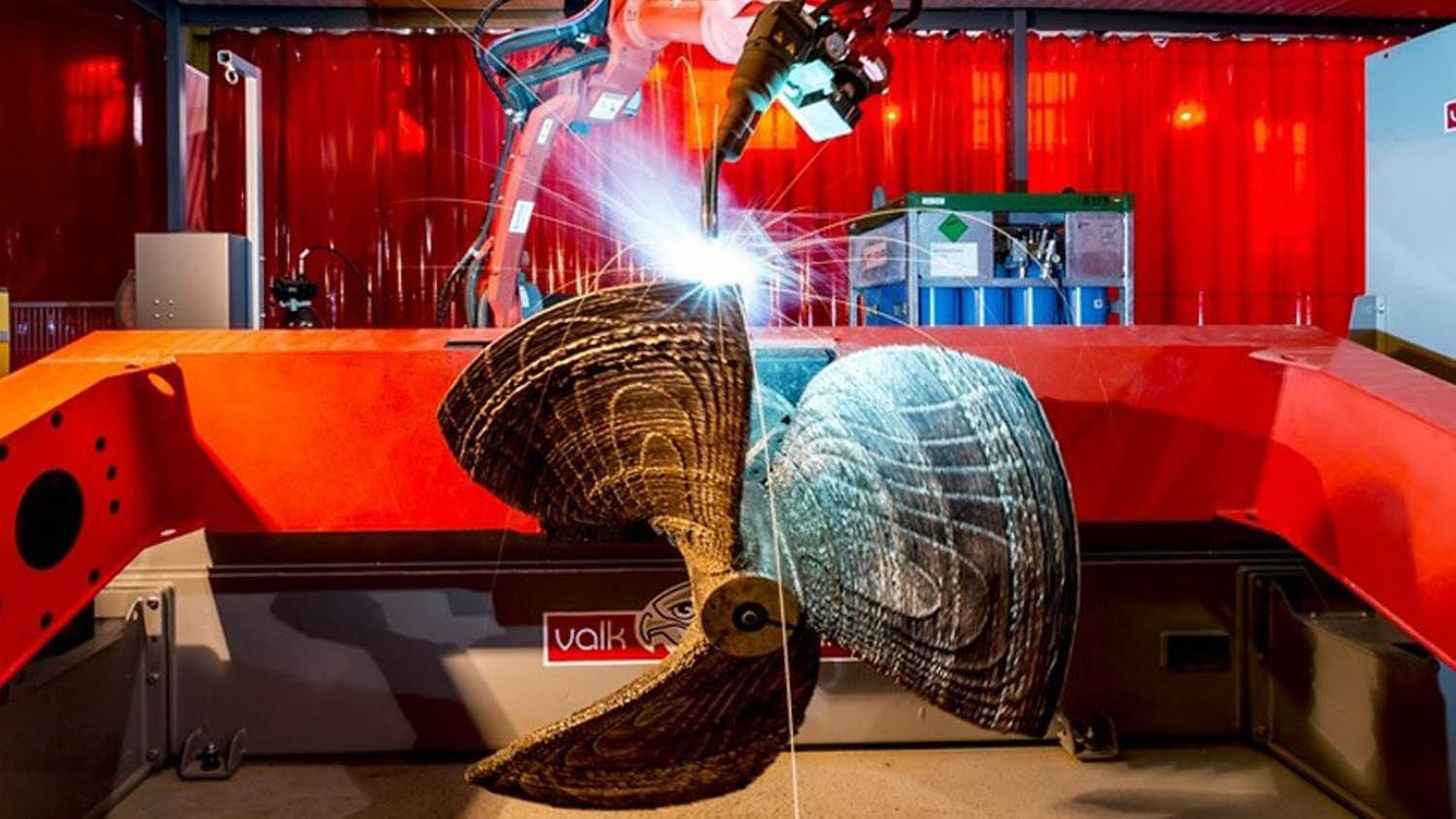
Bowerman concludes that more “thought-provoking capstone projects” are needed to showcase the technology and the genuine impact it can have when compared to more conventional alternatives.
Perini is already hard at work on such projects, where he says cost is nearly always the key driver for change. He cites a project from 2021 where a rollercoaster developer wanted to investigate optimising the seat support of its 31m tall, pendulum-like ride.
The cost of producing the optimised DED part was double the amount of the traditional technology. “But then, we managed to decrease the seat weight by approximately 74%, from 65kg to 17kg. Multiply this by 32, the number of seats in that particular rollercoaster, and it becomes obvious how this allowed the client to realise a huge reduction of the cost of other parts of the rollercoaster!”
As more designers begin to understand its potential, DED looks ready to add new possibilities and disrupt old manufacturing supply chains on a grand scale.