The Cobra Golf 3D printed putter is this week’s poster child for end-use parts built using additive manufacturing technology, but it’s not so much its ability on the greens that has caught our eye.
The King Supersport-35 putter is the first product to arrive from the collaboration between Cobra and the teams from HP and metallurgy experts Parmatech.
The club features a fully 3D printed 316 stainless steel body, with an optimised lattice internal to assist with weight distribution and deliver the highest-possible ‘MOI in a blade shape’ – more on that later.
As with most end-use consumer parts built using 3D printing, a golf club is that perfect mix of low volume and perceived value (even amateur golfers will pay a kings’s ransom to scratch a couple of points from their handicap).
The 3D printing process has provided a list of benefits, some more tangible than others: Golfers love a technology gimmick – so imagine the clamour in the clubhouse to learn more about Cobra’s ‘patented Descending Loft Technology (DLT) to create the most consistent and accurate roll on every putt’.
“HP’s 3D printing technology allows us to utilize a complex lattice structure to remove weight from the centre of the putterhead and push significant amounts of weight to the perimeter,” said Cobra’s marketing VP Jose Miraflor.
“The result is superior MOI levels and massively increased stability and forgiveness. So not only is the 3D production method more consistent but it also allows us to design products in a new and superior way.”
The fabled MOI – or Moment of Inertia – is a measurement of how much a club head twists if you connect with the golf ball off the centre of the club’s face. By packing the weight around the edge of the club head the theory is that the MOI is lowered and the ball is likely to go in the line that you want it to.
“I’ve had a lot of success over the years with my SIK putter and was really excited to work with Cobra to develop a new way to manufacture equipment and bring this new putter to market,” said 2020 US Open Champion and Cobra Golf ambassador Bryson DeChambeau – no doubt while pulling a fresh batch of putter heads from the HP Metal Jet de-powdering station.
While the actual benefits of how a club is manufactured (forged, cast, machined, or now 3D printed) are only of benefit to the person on the golf course, the process of additive manufacturing was one that gave Cobra’s team of designers and engineers quite a lot to be pleased about.
Using Metal Jet 3D printing to create an internal lattice structure within the body the designers were able to achieve the highest MOI without the need to attach additional fixed weights.
The near net shape part is post processed using CNC machining, while adding the all important cosmetic finishes (how else will a colleague know what club you’ve just spent a fortune on?).
The 3D printing process used allowed Cobra Golf and ‘the collaborative team’ to create and test 35 different design iterations over the King Supersport-35’s 8 month development.
“To do that, it’s critical to use the most effective manufacturing processes to design, develop, and achieve optimal results, and we’ve certainly done that with this new putter,” continued Miraflor.
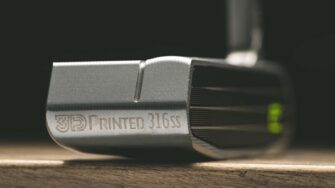
“During the development of the King Supersport-35 Putter, we saw immediate benefits from this process, including design freedom, rapid design iteration, and high-quality parts that meet our economic demands.
“3D printing is accelerating design innovation, and this breakthrough putter will help usher in a new era for the sporting equipment industry at large.”
The King Supersport-35 will be offered in very limited quantities online for $399. However, despite much being made of design freedoms and customisation levels of the process, it is only available in 34″ and for right-handed players.
In addition to this launch, the brands are already working together on a [deep breath] ‘strategic, multi-year product roadmap, that leverages the design and manufacturing benefits of HP’s additive technologies to deliver future golf equipment that raises performance and golfer satisfaction to new levels’.
This was just the first step – Cobra has plans to launch two additional products in 2021 that feature 3D printed technology.
While there’s no guarantee that the clubs will improve your game, additive manufacturing is still capable of creating new design avenues to be explored and exploited.