Vestas Wind Systems, the Danish wind turbine company, keeps these vast installations spinning longer using a digital repository for faster, more accurate part production, as Stephen Holmes reports
Elegant and hypnotic, the whirling blades of wind turbines are one of the most common sustainable energy-generation technologies seen in the world today. But even the producers of such green tech – companies such as Vestas Wind Systems, for example – are looking to make their engineering and manufacturing processes more ecologically sound.
Having completed its first commercial design in 1979, Denmark-based Vestas has focused exclusively on turbine production since 1989. It has designed, manufactured, installed and serviced more wind turbines across the globe than any other company.
The scale and expense of wind turbines make it imperative they function reliably with minimal downtime, in order to be as effective as possible. And there’s no room for error when it comes to their production and installation, so Vestas depends on numerous inspection gauges at its manufacturing facilities and installation sites.
One example is the ‘top centre’ (TC) marking tool, used by Vestas to mark the root end of turbine blades to align pitch. Typically, this tool might take as much as five weeks to create and deliver using CNC machining. And, due to limits on machined designs, the Vestas team would have to order multiple versions of the marking tool, in order to fit a range of different blades.
Similar issues are found with the lightning tip receptors that are added to each wind turbine, to help reduce lightning-strike damage. These receptors are machined from aluminium and as a result might take up to 12 weeks to be delivered.
Vestas // Direct and digital
Vestas made the move to shorten this workflow in 2021, launching its direct digital manufacturing programme. This is designed to shift the company’s manufacturing processes away from a reliance on outside suppliers and to help build a knowledge base for better collaboration.
The programme includes over 2,000 Vestas parts, all of which are stored in a Markforged Eiger cloud-based digital repository.
From there, employees at any Vestas location – some with little to no additive manufacturing expertise – can quickly search for and then print out any number of fibre-reinforced composite parts on a local X7 printer and composite parts on Onyx One 3D printers. Jeremy Haight, principal engineer for additive manufacturing and advanced concepts at Vestas,
describes the new approach as “end-to-end”, enabling the company’s global sites and partners to 3D-print parts while maintaining central control over 3D models.
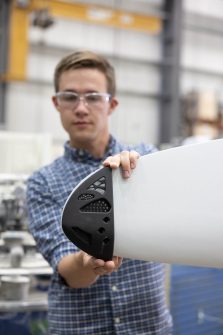
“We provide the physical article in near real time to a variety of places. It’s the closest thing to teleportation I think you can get!” he says.
Using the repository, teams at Vestas know they can get consistent, up-to-spec parts, at short notice, without the need for specialists at each of the company’s global facilities. This is helping to dramatically reduce shipping and freight costs, as well as manufacturing lead times.
The TC marking tool that previously took weeks to produce is now made in just a few days. And because the tool is printed using fibre-reinforced nylon Onyx, it now weighs 85% less than before.
For the lightning tip receptors, teams will be able to produce these in 3D-printed copper at the point of need. Company estimates suggest that it will take about two days to produce these receptors and get them directly into the hands of the assembly teams that need them.
Executives at Vestas see the company’s direct digital manufacturing plans as critical for new product development, as well as tool and end-use part availability.
In 2022, they hope to introduce on-demand gauge production at all manufacturing locations. The company has also partnered with Würth to build an additive ecosystem and manage an inventory of spare parts made with the Markforged Digital Forge platform to support maintenance, repair and operations (MRO) for local field support and other suppliers.
The company is making it easier for staff with the right permissions to scan a part code or search for a part in its EAM and ERP systems, and have it automatically sent to the required 3D printer. It is hoped that this centralised control, managed using its Blacksmith and Eiger Fleet, will produce high-quality, high-performing tools and end-use parts, keeping Vestas turbines turning and green energy flowing.