3D Systems has launched the Figure 4 135 3D printer for high mix, low volume (HMLV) manufacturing needs where a manufacturer is replacing or supplementing injection mould tooling.
The 5-watt, 2716 x 1528 resolution, with 50 μm pixel size can offer out-of-box accuracy and repeatability for production applications while having access to the Figure 4 advanced material line-up.
Developed in accordance with IEC-62443 cybersecurity standards, the Figure 4 135 also supports automated workflows, with built-in barcode scanner to support batch run capability and full production process traceability.
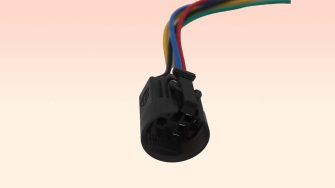
3D Systems lists electrical connectors as an example of traditionally manufactured plastic parts using injection moulding that requires tooling and long lead times.
By 3D printing the precision connectors, the parts can feature with high fidelity, high thermal stress resistance and cost-efficiency at high volumes. As part of this particular solution, 3D Systems is introducing Figure 4 Tough 75C FR Black. A tough, flame-retardant material is recognised by UL with a UL94 V0 rating at thin wall thickness (0.4mm) and a Relative Thermal Index (RTI) for long-term electrical of 150°C and mechanical use of 130°C.
This makes it suited for applications such as appliances, consumer electronics and automotive that require accuracy, heat resistance, durability, flexibility, and electrical safety.
The Figure 4 135 3D printer joins a growing Figure 4 family, including the Figure 4 Production, Figure 4 Modular, Figure 4 Standalone and specialist Figure 4 Jewelry [sic].
Elsewhere in its Stereolithography 3D printing portfolio, 3D Systems announced it is enhancing its 3D printed casting performance by making the QuickCast Diamond build style available with 3D Systems’ PSLA 270. This projector-based SLA 3D printer combines high-speed production and mechanical stability to deliver mid-size components. When using the QuickCast Diamond build style in 3D Systems’ 3D Sprint additive manufacturing software, users can rapidly design and create structured copies of parts to produce a tree.
QuickCast Diamond is up to 30 per cent lighter and has more consistent strength than previous QuickCast build styles with its internal diamond structure pattern providing a number of benefits including reduced internal mass resulting in cleaner burnout and less material usage.
Employing the QuickCast Diamond build style on the PSLA 270 should help foundries to reliably deliver large, high precision investment casting at a fraction of the time and cost of traditional tooling and with no limitation on geometric complexity.
“Innovation is in our DNA,” said 3D Systems CEO Dr. Jeffrey Graves. “Our historic R&D surge in 2024 yielded dozens of polymer and metal products, all driven by a rising demand to address an increasing number of applications using additive manufacturing. Now, we’re commercialising these advancements, such as the Figure 4 135, which dramatically reduces costs and boosts throughput for many high-mix, low-volume applications.
“These new product introductions underscore our unwavering commitment to delivering application-specific solutions that address our customers’ rapidly evolving needs. I’m looking forward to seeing the positive impact that these newest additions to our portfolio will have on our customers’ businesses.”