Hands-free access to documentation is a godsend for workers operating in awkward or high-risk environments. Stephen Holmes talks to RealWear, a company behind wearable technology that prioritises industrial needs and winning fans in work environments ranging from oil rigs to operating theatres
Put yourself in the steel-toe capped work boots of a lift maintenance engineer for a moment.
Responding to an issue, you put on your new head-mounted, mixed reality headset, which is going to show you how to identify and fix the problem through vivid, overlaid graphics. You stride towards the elevator in question – and whoosh. You failed to spot the edge of the lift shaft and down you plunge. It’s not just the cost and complex set-up associated with new head-mounted displays that are off-putting, says Noah Balmer. It’s also the risks they pose when a user has bright lights blasting both eyeballs.
“Yes, you can see through it – but it’s like when you see something in your peripheral vision, for example. You know, something’s there, but you have to actually look at it to see it. And when you’re looking at something, you have blind spots everywhere else.”
Balmer is director of product design at RealWear, a company that since 2016 has produced head-mounted displays that position a screen close to the wearer’s eye, but leaving their view unencumbered. Marketed as ‘assistive reality’, RealWear’s products are built solely with industrial use in mind.
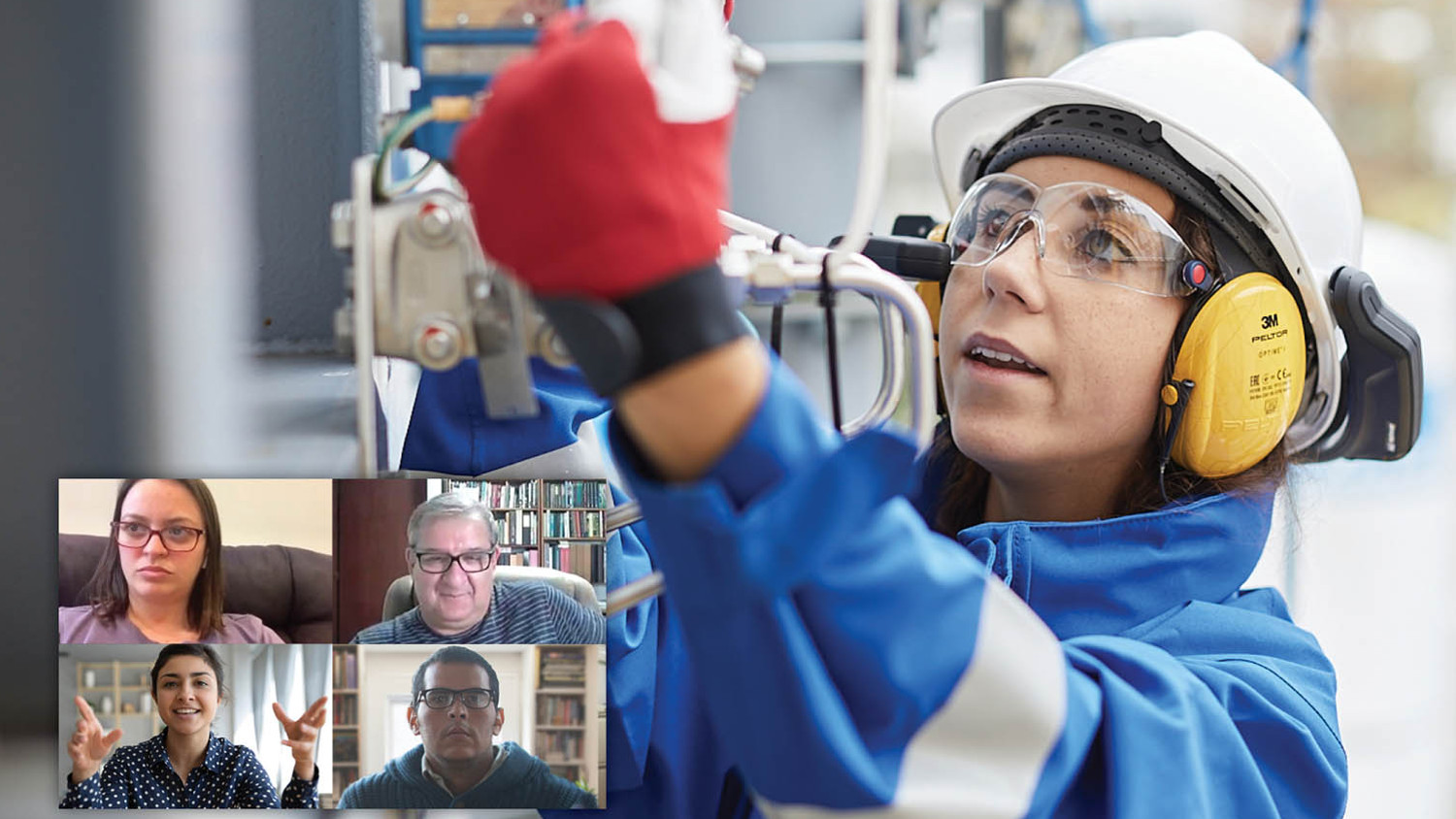
For most industrial maintenance workers, he says, the jump from laminated print-outs of work instructions, say, to hi-tech, mixed reality headsets is far greater than you might imagine.
“With our device, it’s a lot easier for people to wrap their head around, or have it wrap around their head!” laughs Balmer. “We can just explain to them that this is a normal display. It doesn’t have holograms that dance around, you don’t need to develop new models, or digitise every schematic you have in your factory.”
RealWear’s products, such as the latest Navigator 500, offer a screen similar to a digital viewfinder on a camera. Once your eye is up against it, it looks like a big display. It’s often compared to a hands-free mobile phone display.
For someone needing to read page 132 of a PDF, while wearing gloves and goggles inside of a crawlspace, having to consult a document or a tablet is not ideal. A bunch of laminated papers is still the norm at many companies, according to Balmer. “They wake up in the morning, and they print out a bunch of crap. And then they laminate it. They’re all there fighting over the lamination machine!”
The Navigator 500 connects to WiFi or can be fitted with a modem. It can connect, for example, to a Microsoft Teams call, its camera capable of putting an expert on the other side of the world at eye level with the problem at hand. Or it can bring up video for a walk-through of how to conduct a repair via its screen.
While many new augmented and mixed reality (AR/ MR) headsets have been launched, few companies yet have detailed models for their service workers to use. “Most of the time, they’re printing out a PDF,” says Balmer, “There’s no way they’re gonna get to the next level of augmentation.”
Up top design
Before RealWear even started, its founders were already working in different companies, learning about optics and head-mounted devices. Using Human Factors and User-Centred Design principles, plus all they had learned about optics and how the human eye works, they began to build industrial headsets.
A lot of this is based around the shape of the human head, and the fact that what might be a perfect fit for one person may be huge or a tight squeeze on another, given their very different head dimensions. Eye dominance also plays a role, especially for a product that might be worn all day, hence RealWear’s display arms can be flipped to accommodate this.
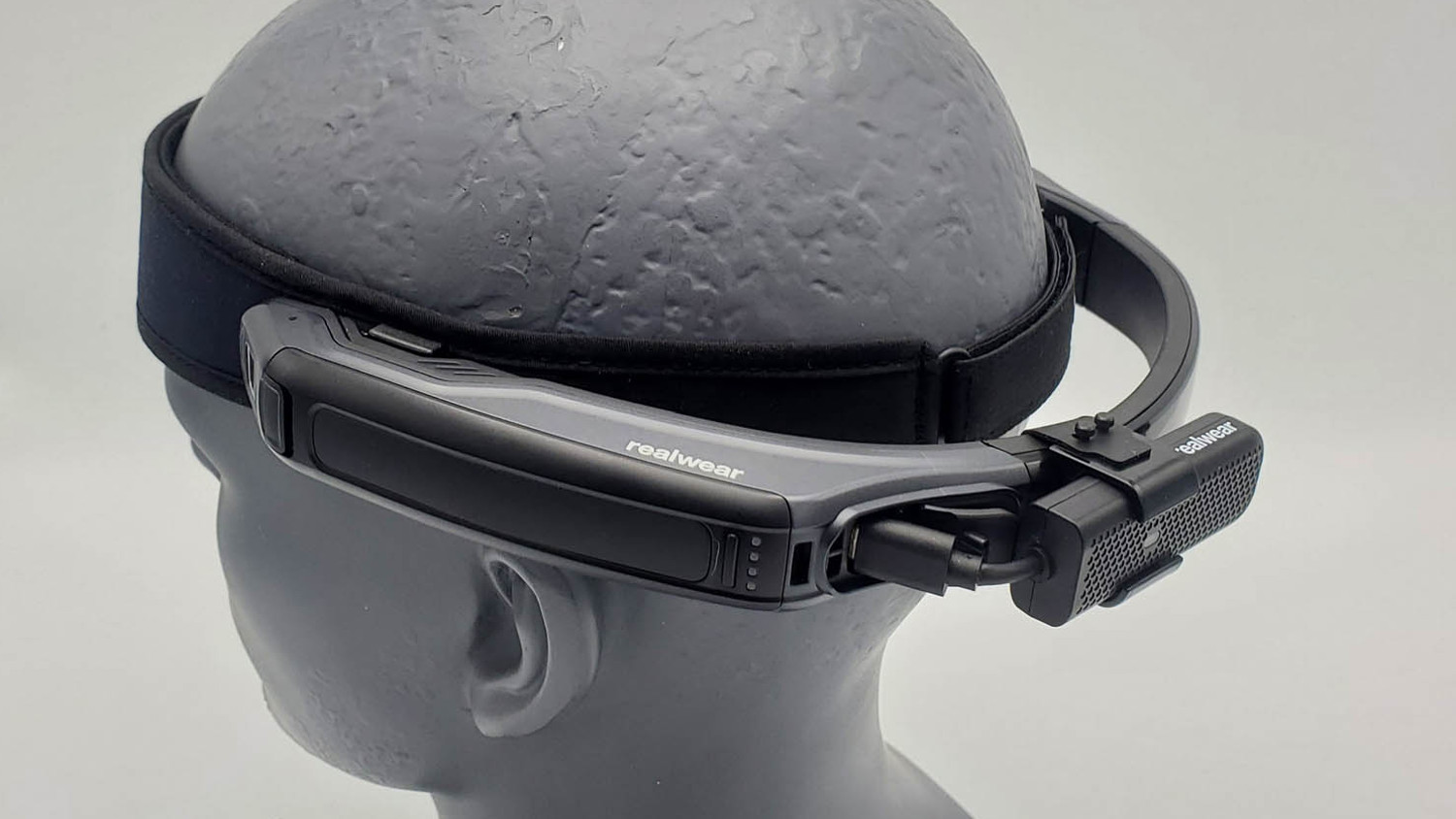
In an industrial space, there’s also the challenge of PPE – personal protective equipment. Many countries have different hard hat designs to meet varying safety certifications, so everything is slightly different. (RealWear offers around 50 different clip designs fordifferent hard hats.) And you can add to this mix a wide range of use cases. A wearer might need ear defenders, for example, but then they can’t wear the device under the brim. A lot of this product development work and identifying specific problems comes down to physical prototyping. At RealWear, much of this is down to the framework set out by Balmer’s predecessor.
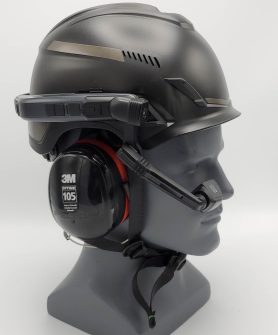
“The guy that I replaced, Stephen Pombo, was a pretty famous guy around this space. He was a model maker in the Bay Area for 30 years. He worked on original models for Apple computers and for Atari. He worked on some Star Wars assets for Industrial Light & Magic,” says Balmer.
“He hired me, and long story short, I realised that sketching models, scratch builds, these kinds of things, are way more important than people realise.”
The development process at RealWear begins with masses of brainstorming and consideration of specific customer requirements, but very quickly, moves into physical prototyping.
Balmer models most of the concept designs in Solidworks, and then 3D prints quick models for assessment on a desktop Prusa in his home office, in order to get an idea of how something might work or sit on the headset.
For presentation models, he steps up the design to the two workhorse Markforged Onyx 3D printers at RealWear’s design studio. “Those things just print every time. I’ve done like a 26-hour build lots of tiny parts – and it just works every time. It’s miraculous!” he says. These prototypes are vitally important, he says.
“You can have bigwigs in a room talking, and you’re not gonna get anywhere until you put something on someone’s head and see if they like it or not see if it hurts their brain! Part of what I do here is make a ton of working models, and then test them on people. And that’s really, I think, the key to success for anything that goes on the human body, especially.”
A lot of Balmer’s role involves concepting, research and user studies. His design team, meanwhile, boasts plenty of CAD geniuses.
“I’m pretty good, but you know, there are those masters,” he says. “They’ve been doing it for 10,000 more hours than me, and I’m not going to catch up anytime soon while I read all these emails!”
A new display in a different form factor might begin life as a development circuit board hanging off a headset made of cardboard and 3D-printed parts. This, according to Balmer, is because he doesn’t want to be married to any single idea.
“If I make a model that takes two months, I’m really going to have to make it work, you know? But if I make it out of cardboard and I show it to people, they’re not worried that there’s a big investment. If I show it to the CEO, he’s not worried that we’re gonna lose hundreds of thousands of dollars, because we have to zigzag from this specific concept,” he explains.
“It doesn’t feel scary to them, because it’s just like, ‘Oh, it’s fun.’ It’s like a costume and it looks stupid and there’s wires hanging off it. They feel like they’re part of something.”
As the design progresses, and more models are tested, the design eventually transitions into PTC Creo for detailed mechanical engineering and production, with every element built in 3D CAD, right down to the last chip on the custom board. “In the beginning, it’s all about ‘fake it till you make it.’ Then you start getting into real mechanical and electrical engineering and it has to get more locked down,” says Balmer.
Loadbearing models are outsourced to Protolabs to be made using SLS 3D printing. CNC models are produced for final testing with all the electronics fitted in place.
The headsets feature a lot of metal components, in order to be able to stand up to industrial use. A ball joint for the display could be skimped on to save costs, says Balmer, but then you’re opening up the product to flaws. If it isn’t a ball joint, then it can’t be adjusted to achieve perfect horizontal levelling for the user.
“Why would that matter? It’s just a little bit, but I don’t know if you’ve ever mounted a TV to a wall one inch off [level] or something like that? It doesn’t feel good, like your brain has to somehow rotate five degrees. It takes more processing and brain power.” Such is the drive to achieve the best level of everyday comfort.
RealWear // Clever components
The industrial settings in which the headsets are designed to be worn add further levels of complexity. Drop-tests are rigorous, while the need to balance strength with weight reduction leads to a lot of FEA work to assess the best placement of internal ribs and screws. As a result, the latest model weighs, on average, only two-thirds what its predecessor weighed.
Modularity is another key factor. With a huge range of add-on components and features, the headsets can be customised for all kinds of roles.
“It makes sense in this world, because we’re using components from the smartphone industry. You get a camera from a smartphone, and in two years, they don’t even make that camera anymore. It’ll be some newer camera,” says Balmer.
“And so, for a business, it actually makes sense, because you can lengthen the lifespan of the overall product by offering accessory modules to make it more powerful.”
The latest model now offers a spring-loaded metal slide switch for the camera connector unit that allows the user to swap it for a different type of camera – such as specialised wide angled or thermal imaging kit – or for something else entirely, like a laser or a flashlight.
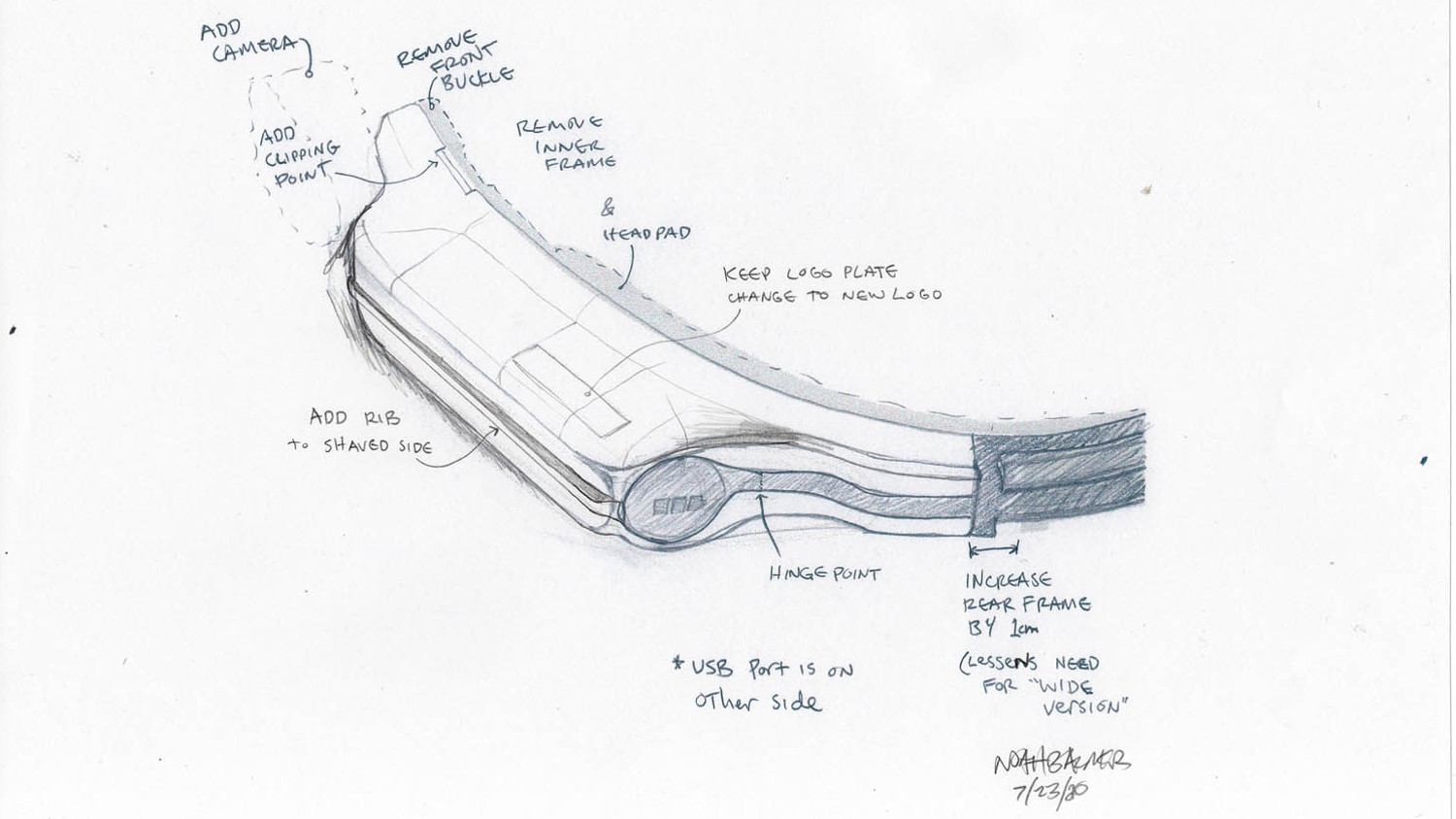
And if it turns out that a customer has a very specific requirement, then the headset proves far more versatile, and won’t require a full redesign to accommodate those needs.
Rugged aesthetics, such as overmoulded TPU bumpers, are designed with industrial use in mind, while Balmer suggests that other glasses companies have fallen into the trap of “trying to be a fashion brand.”
Donning a RealWear headset, he says “This looks pretty silly on me, but if I’m in a factory and I’ve got goggles and gloves on, it doesn’t matter that I don’t look like Blade or Vin Diesel or something!”
This versatility is a real strength, enabling RealWear to grab the attention of professionals in a wide range of sectors. Surgeons and cleanroom professionals love the devices. This widening market means that, over time, the design team will be looking to make products even more versatile.
As well as modularity, the latest model offers different head mounting options, including a lightweight, washable, soft headband option.
“For a medic performing surgeries, this is a much better design than a bump cap, or a hard hat, or some strappy thing,” explains Balmer. “[The Navigator 500] is kind of a chameleon, in that it can have different cameras, different sensors and different mounts on it for what you need in your industrial space or in your environment.”
RealWear is more accessible than many wearable devices, with its clever design allowing for a vast range of configurations and possibilities. That is enabling the company to plan clearly for the road ahead, spotting any proverbial lift shafts well before it steps into one.