Buttons, eyelets and rivets are just some of the detailed metal parts designed and manufactured for the fashion industry by Eurominuterie. Claudia Schergna spoke to the team to find out how digital tools help deliver those final flourishes for a garment
The devil is in the details. In the fashion world, the interior finish of a dress or the design of a tiny button can transform an everyday garment into one that exudes high quality and luxury.
Headquartered in Padua, northern Italy, Eurominuterie produces billions of stamped small metal details for the fashion industry each year. Its output includes decorative elements, internal components, buttons, eyelets, rivets, rollers, hooks and lace feeders for footwear.
Although these components are generally small and simple, they are the result of a careful design study and a production process that involves several stages.
The process starts with a client request, typically for a new or customised design. Team members from the production department at Eurominuterie studies the brief and draws on the company’s catalogue, where they can find years’ worth of designs for previous projects.
They then make the necessary changes and add some new elements, to come up with something as similar as possible to the item requested by the client in terms of functionality and style. And finally, they work with the technical department to select the best technologies and materials to realise the project.
With over four decades in the industry, Eurominuterie is able to offer a wide choice of processing to enhance a finished product, while also helping guide clients with creative solutions for customisation, says CEO Alessandro Rigato.
For example, he says, “we have developed a refined painting technique that allows the items to maintain strength and aesthetic appearance without giving rise to oxidation or staining.”
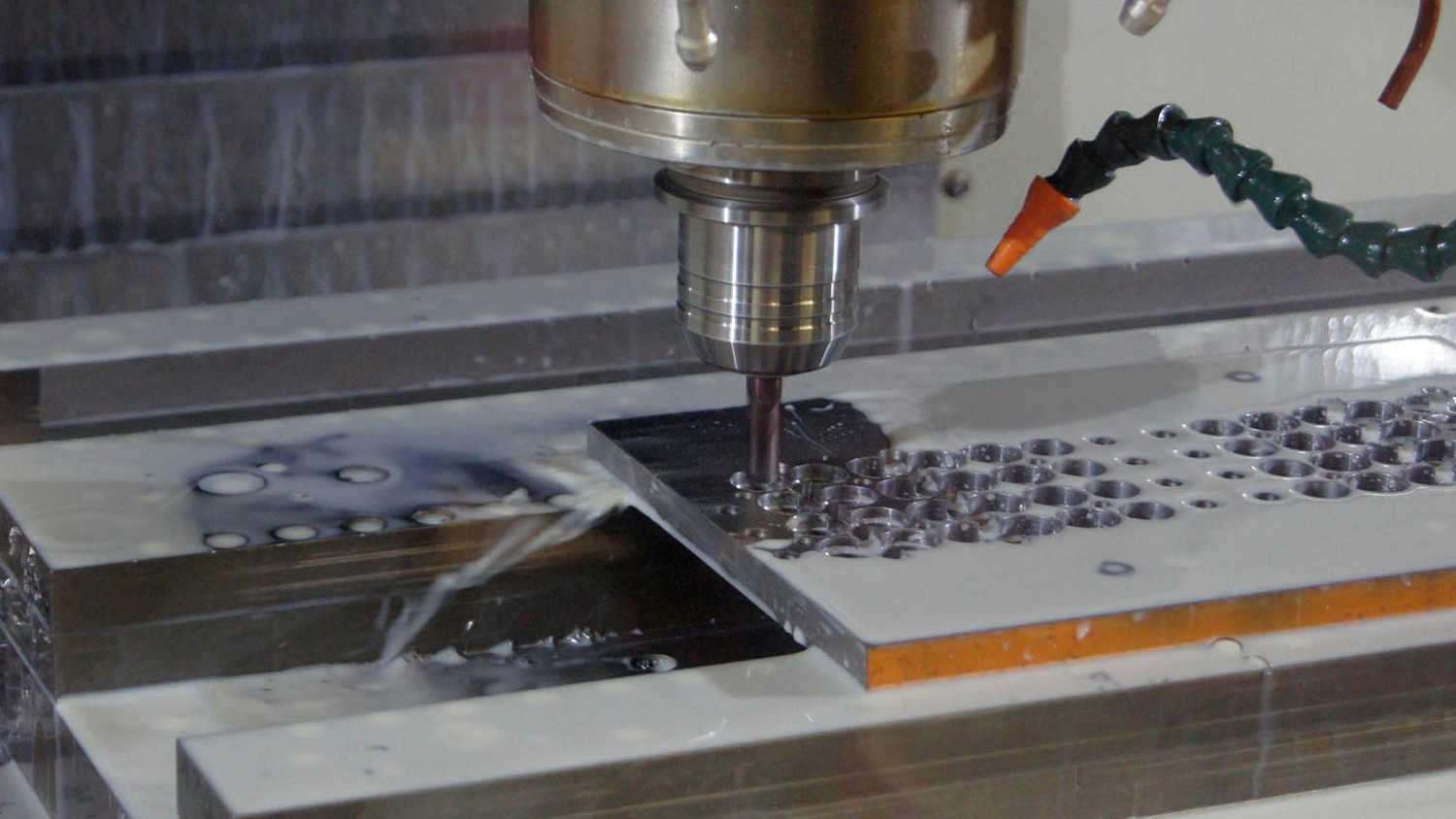
In-house moulds
As well as producing individual components, Eurominuterie also makes its own moulds in-house, giving it the flexibility to respond to customisation requests, while also reducing production costs, material waste and delivery times.
Moulds for each component are designed using Cambrio Cimatron, which allows the team to visualise the piece and estimate the quantity and cost of material needed. The pieces are stamped on sheets of metal using CNC machines, which are also programmed using Cimatron technology.
Stamped parts then undergo a galvanic process to apply aesthetic and protective treatments by adding a thin layer of metal deposited by electrolysis onto surfaces. These can be more valuable metals like gold, silver, or nickel, giving the product the lustrous finishes desired by the client.
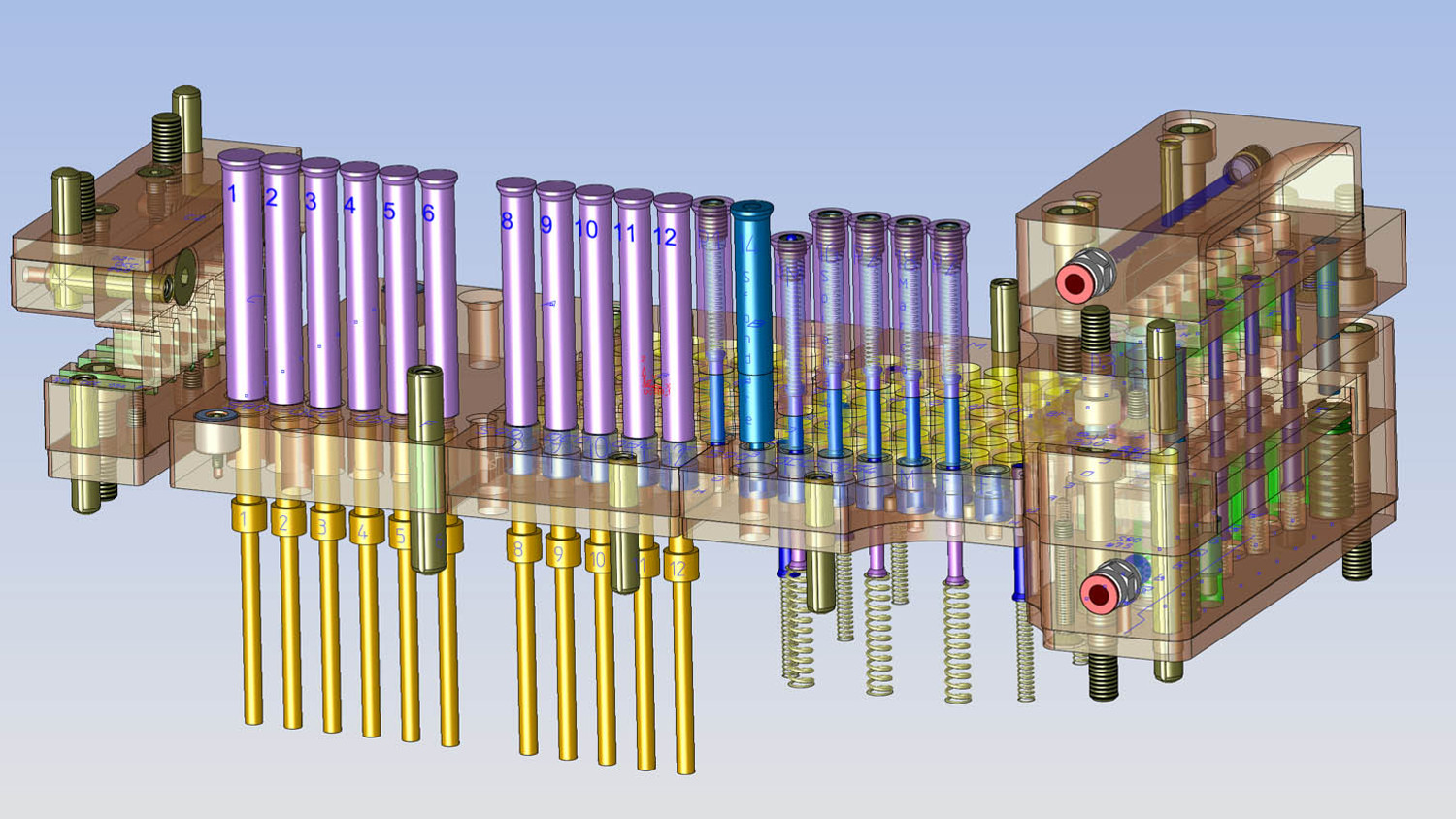
Parametric design
Eurominuterie’s digitalisation process began when the engineering team felt the need for CAM software to help programme its growing number of CNC machines. Once they saw how much the adoption of such technologies aided workflow and how it revolutionised production, they never went back.
Cimatron was chosen in part because of its capabilities with parametric design, explains Rigato, “a method that does not focus on individual results but describes the entire design process, allowing us to automatically, or almost automatically, infer many design variations, promising to increase our competitiveness and profitability.”
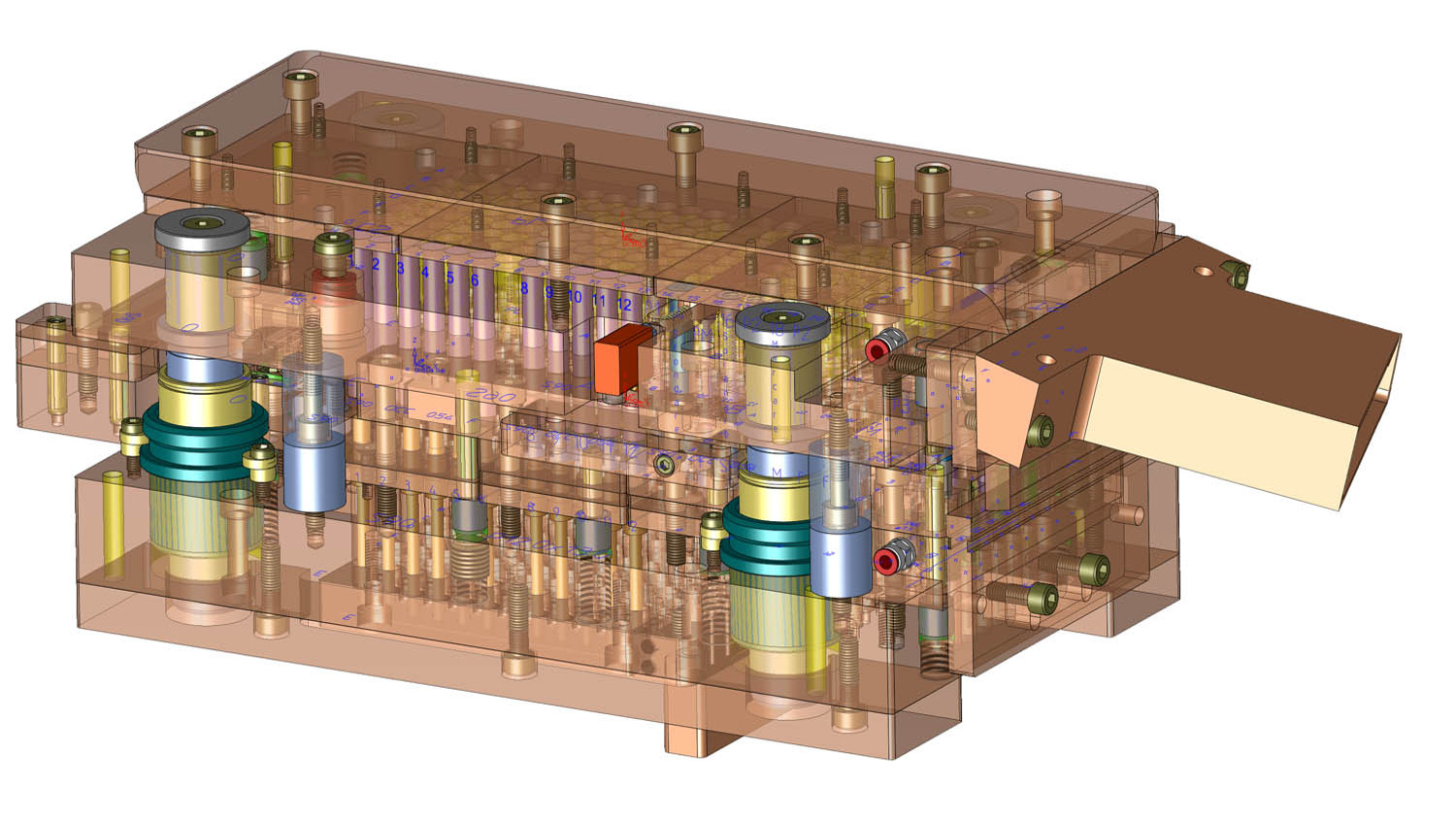
The ability to reuse data and develop it further from project to project enables changes to be made with greater ease, he says. Cimatron offers several modelling-to-analysis functions that help speed up delivery times and cut costs.
One of these is mould set-up, which allows the team to create 80% or more of the mould. Beyond that, only a few new parameters need to be entered to create a unique custom design.
“Over time, we have set up several basic mould structures in the company: those that are not needed in a new project are simply deleted, then we only need to modify other parts,” explains Rigato.
“The work is completed really quickly. In cutting and punching, the tools in the system from the earliest versions were already very advanced. Now, with the updates and upgrades that Cimatron regularly provides, even the deep-drawing strips can be designed very quickly and reliably. They have given us great advantages in these phases.”
Thanks to this feature, every change is updated in the drawing and all CAM procedures involved. In this way, the parallel design capability enables Eurominuterie engineers to start working on CAM programming even if a design process is just at the beginning stages.
Rigourous, logical and intuitive
Rigato points out that the team has developed its own control model for the designs, with a scheme to follow that is available to all technicians, which improves the quality and reduces errors substantially.
The system makes it possible to define precise rules according to a chosen operating standard with which everyone can comply. This might include positions, diameters, rank, applied technologies and tool combinations, for example.
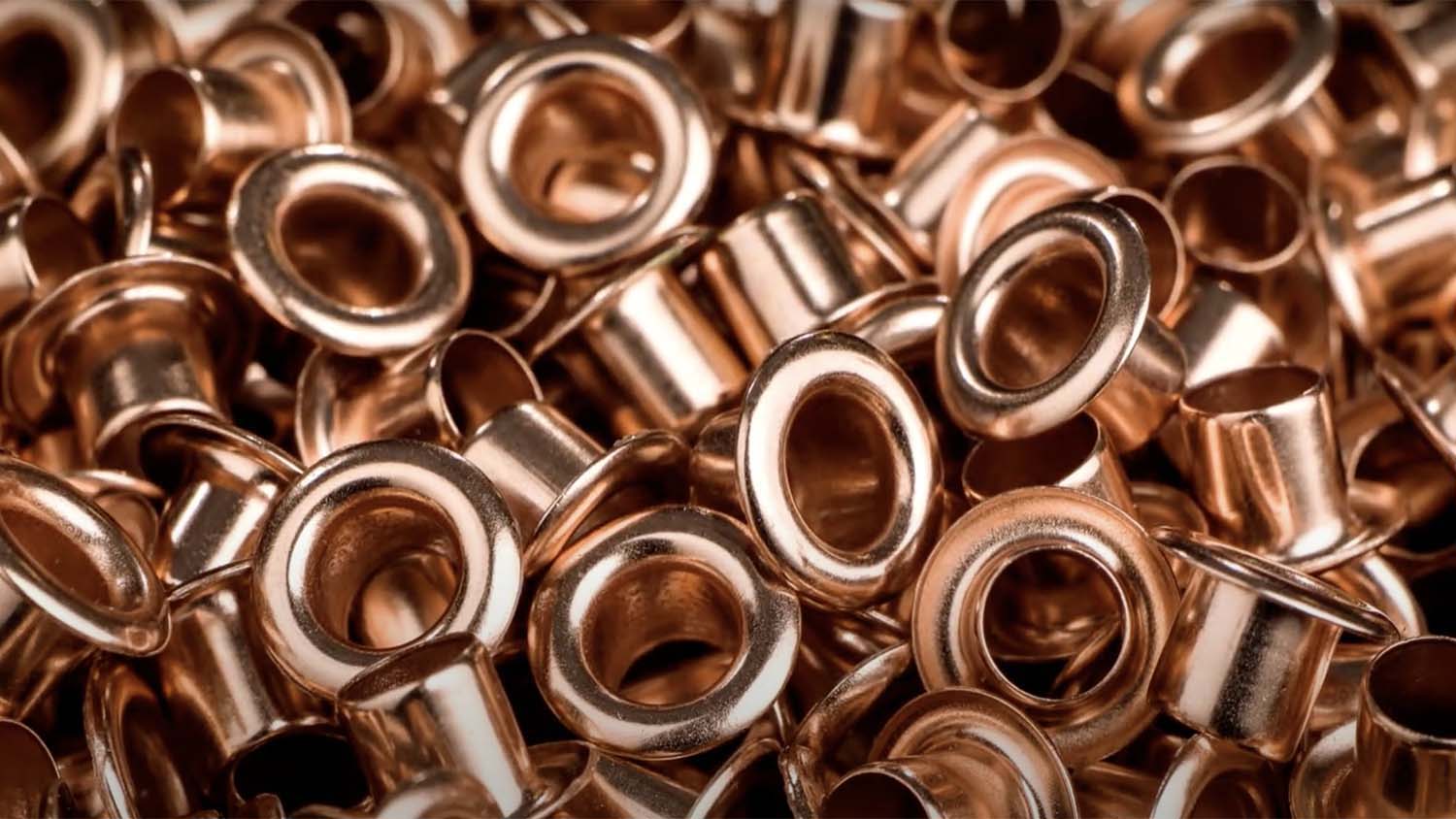
“In reality, the correct way to proceed is dictated by the system itself; the sequence of operations is rigorous, logical and intuitive,” says Rigato. “After constructing our reference formulas, the mould almost assembles itself.”
When it comes to CAM, although the steps at Eurominuterie are not particularly complex, the integration that Cimatron provides between design and machine tool programming makes the workflow smoother.
“The technology in our industry has not changed much on the method,” says Rigato, “but the way we build today allows us to save literally hundreds and hundreds of hours, not to mention labour. We could never go back from digitisation.”
The digitisation of the product development through manufacture has given Eurominuterie’s team more design freedom to deliver truly unique pieces, each of them capable of catching the eye.