In this workshop we go beyond the normal simulation approach of taking a potential design solution and seeing how it will perform against a set of objectives.
In the usual simulation process we look at how the design stacks up then, go with it, or modify it and see if it’s better or worse. But one of the key things a computer brings to the party is the ability to do lots of similar tasks in a repetitive manner.
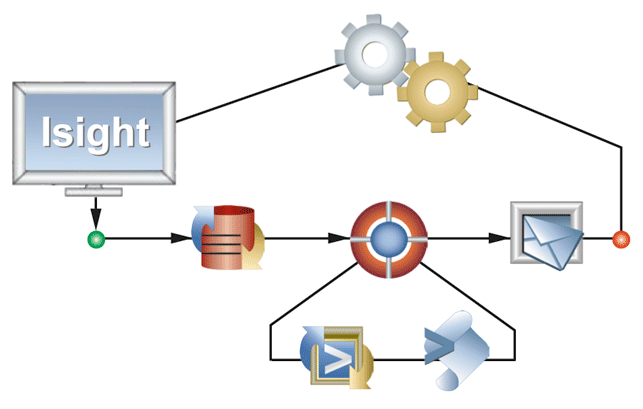
So coupling a simulation to a system that can vary the model and assess the impact of these changes is hardly a new departure (optimisation systems have been widely available for the whole of my simulation career). If there is one aspect of Computer Aided Engineering (CAE) that needs lots of computing power it’s optimisation; the adoption of this technology can only increase.
There are two distinct approaches to optimisation, one more intuitive than the other. The first approach is to create a CAD model (or a CAD like model in the FEA program), and allow the dimensions of the model to vary in response to the results of the simulation process.
So, a model may have several parameters that are allowed to vary such as thickness, fillet radius, length etc. These are varied to give the minimum weight under the constraint of a set stress limit. Other parameters, responses and constraints could be used, but this is the basic concept.
Parametric optimisation is a process similar to the way in which a human designer approaches the problem, and results in designs that are traditional in appearance. Programs like Isight use this approach.
Once we’ve established the link between the simulation and its CAE environment, the framework we use can be exploited to investigate design robustness and other effects of variability on performance. It can be argued that investigating design robustness is more important than extracting the last ounce of design efficiency, but perhaps that is a discussion for another day.
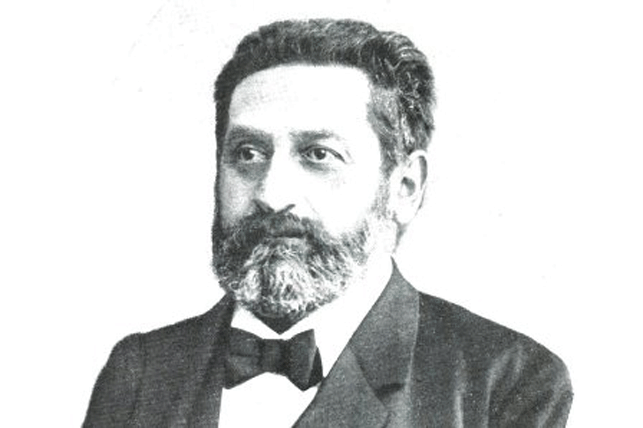
The second approach to optimisation is one based on topology. Topology optimisation starts with a much looser definition of the problem – the geometric starting point is often simply the space envelope that the part can take up. The optimisation process will then find the optimal distribution of material within that envelope to satisfy the goal. How the systems achieve this is a fascinating cross over between computing and biology.
Some time in the 19th Century a German surgeon by the name of Julius Wolff (1836 – 1902) was the first person to establish the link between the density of bones and the load applied to them, which he called ‘Wolff’s Law’. This discovery predated the most obvious illustration of it, that astronauts lose one per cent of their bone density for every month they spend in space.
So, the topology optimisation process mimics what happens in everyone’s skeleton in that where the stresses are high the local density and modulus increase and where they are low the modulus and density decrease. Mimicking this process in an engineering scenario reveals the optimal distribution of material within a design envelope.
So rather than coming up with traditional design solutions, topology optimisers generate organic looking geometries, which is hardly surprising given the biomimetic approach used to create them. The issue is that traditional design and manufacturing processes aren’t exactly used to working with organic geometries. You export the shapes readily enough using STL files, but there is generally a reasonable amount of work required to convert these into useful solid models. If there was an area in which R&D effort would be rewarding it is here.
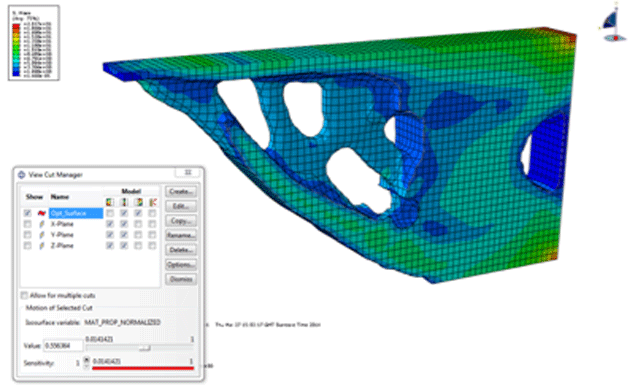
But if there is one area where the non-traditional approach to manufacturing isn’t a problem it’s 3D printing. Every time I tell people there isn’t anything to 3D printing somebody comes up with a more impressive application – but suffice to say there are many situations where a combination of topology optimisation and rapid manufacturing look like the future of efficient design.
Laurence Marks is the managing director of Strategic Simulation and Analysis Ltd, a company supplying the Simulia range of simulation software, training, implementation as well as consultancy services to a wide range of industries.