Al Dean takes an in-depth look at the ZPrinter 650, which brings the most recent innovations in high-definition colour and integrated post processing to Z Corporation’s high-end 3D printing offering for the first time.
Recently, Z Corporation has expanded its 3D printing products to include both high-resolution colour capabilities and facilities for model post processing – such as powder removal, treatment/infiltration and recycling of unused powder.
While this started at the lower end, it has now been extended to the high end, larger build volume machines, which previously lacked one big USP, that of full colour. The release of the ZPrinter 650 now brings full colour capabilities to a large build volume for the first time. So let’s take a look at what it can do and how it does it.
How does it work?
The basics, as with all Z Corp 3D printing machines, are as follows. The 650 relies on the layer-based printing of binder onto powdered material. As each layer of between 0.089 and 0.102 mm is put down the layer form is solidified, and the next layer built on top of that.
As the model is encased in a block of powder, this means that the system can be utilised to the full by ‘stacking-out’ the build chamber (as can be done with most powder-based systems) and much of the ‘unused’ powder can be recycled for subsequent builds. The system uses standard inkjet print heads from Hewlett-Packard and this also gives the Z Corp machines their huge advantage: colour. By using separate colour binders, the system can print colour directly into each layer at its periphery where required, allowing full-colour, high-resolution models. So what’s new for the 650? The answer is in three parts.
Build chamber
Previous ZCorporation 3D printing machines used Cyan, Magenta and Yellow to make up black, so a lot of binder was used and it didn’t give the best colour match
Firstly, the build chamber is much bigger than any other machine Z Corp has had to date. While by no means the biggest in the industry, the chamber, measuring 254 x 381 x 203mm, is much bigger than most and with the ability to stack it out, gives you plenty of room to breathe. As you’ll see from the images accompanying this article, it’s big enough for most. The good news is that the build speed hasn’t been compromised and still retains the inch per hour tag that Z Corp is renowned for. With layer thickness anywhere between 0.089mm and .102mm, good, high quality models can be produced in a very short space of time.
Improved colour
While colour has been a revolutionary feature of the Z Corp machines for some time, the 650 steps things up a notch by introducing a black binder, in addition to the existing Cyan, Magenta, Yellow and Clear binders. Previous machines used the combination of colours to make up black, so a lot of binder was used and it didn’t give the best colour match. The addition of a black binder will make features much crisper and colours richer.
System integration
If there’s been a criticism levelled at the Z Corp machines since they came onto the market, it’s that they could be a little messy in those early days. After all, shovelling white plaster or, as was the case back then, starch, into a machine, then digging a model out of it a couple of hours later, was always going to be a messy business. With the ZPrinter 450 Z Corp addressed this by introducing powder cartridges that make loading the machine much easier as they simply click into place. There is also a chamber to the right of the build area where users can safely de-powder the models from the build chamber, use an air hose to blow off additional powder and carry out post-build infiltration (models require an infiltrant be painted over them to make them more sturdy).
Conclusion
There’s currently a transition happening in the Rapid Prototyping sector. Many vendors are looking to shift their businesses from simply providing prototypes to providing end-use components and rightly so. Personally, I’m not convinced that the demand is as big as many are expecting but there is huge potential there.
While the transition to rapid or direct manufacturing is going on, there’s also a huge re-emergence of pure rapid prototyping and some serious advances are going on for those looking to build prototypes for use in the design process. One of the leaders in that field is
Z Corporation, who, alongside players like Objet, has consistently shown that there is room for innovation in a market that some RP vendors seem to be abandoning.
Z Corp has been refreshing its product line since the introduction of the Spectrum 510 a few years back, and the 450 saw the entry colour models bring greater office friendliness with an integrated finishing station. This has now been followed up very nicely indeed with the 650. The bigger build chamber brings the ability to create a much larger model and this is going to appeal to a number of industry sectors – even if simply to remove the hassle of joining separate builds to create large models. But alongside the ability to create bigger parts, the expanded build chamber gives the user the ability to build larger numbers of prototypes in one go and this is key.
During those initial stages of design, particularly for consumer electronics, the ability to prototype a large number of design variants, for evaluation, test and research, can enable greater experimentation and help achieve a better end product.
The improvements in colour capability, along with the addition of a black binder, mean that parts are more consistent across different models (because the system isn’t mixing black) and should also give more accurate results in terms of colour matching.
We tested out the 650 with a standard SolidWorks dataset and one from Inventor and the results were highly impressive, with sharp details and vibrant colours. Even when working with scaled down parts or scaled up parts, the ability to see, to inspect and yes, to hold a product, while it’s still in a ‘digital non-realised’ form, is incredibly powerful and a real benefit to the design process.
Lorem ipsum dolor sit amet, consectetur adipiscing elit. Nunc ac enim leo.
Recently, Z Corporation has expanded its 3D printing products to include both high-resolution colour capabilities and facilities for model post processing – such as powder removal, treatment/infiltration and recycling of unused powder.
While this started at the lower end, it has now been extended to the high end, larger build volume machines, which previously lacked one big USP, that of full colour. The release of the ZPrinter 650 now brings full colour capabilities to a large build volume for the first time. So let’s take a look at what it can do and how it does it.
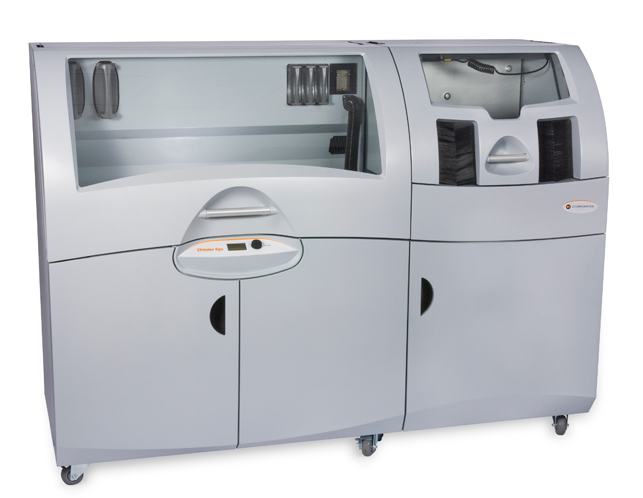
The ZPrinter 650 is nearly 2m wide and weighs over 300kg
How does it work?
The basics, as with all Z Corp 3D printing machines, are as follows. The 650 relies on the layer-based printing of binder onto powdered material. As each layer of between 0.089 and 0.102 mm is put down the layer form is solidified, and the next layer built on top of that.
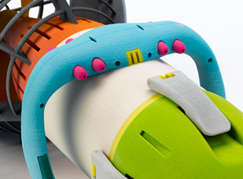
Modelled in SolidWorks, printed in one build
As the model is encased in a block of powder, this means that the system can be utilised to the full by ‘stacking-out’ the build chamber (as can be done with most powder-based systems) and much of the ‘unused’ powder can be recycled for subsequent builds. The system uses standard inkjet print heads from Hewlett-Packard and this also gives the Z Corp machines their huge advantage: colour. By using separate colour binders, the system can print colour directly into each layer at its periphery where required, allowing full-colour, high-resolution models. So what’s new for the 650? The answer is in three parts.
Build chamber
Previous ZCorporation 3D printing machines used Cyan, Magenta and Yellow to make up black, so a lot of binder was used and it didn’t give the best colour match
Firstly, the build chamber is much bigger than any other machine Z Corp has had to date. While by no means the biggest in the industry, the chamber, measuring 254 x 381 x 203mm, is much bigger than most and with the ability to stack it out, gives you plenty of room to breathe. As you’ll see from the images accompanying this article, it’s big enough for most. The good news is that the build speed hasn’t been compromised and still retains the inch per hour tag that Z Corp is renowned for. With layer thickness anywhere between 0.089mm and .102mm, good, high quality models can be produced in a very short space of time.
Improved colour
While colour has been a revolutionary feature of the Z Corp machines for some time, the 650 steps things up a notch by introducing a black binder, in addition to the existing Cyan, Magenta, Yellow and Clear binders. Previous machines used the combination of colours to make up black, so a lot of binder was used and it didn’t give the best colour match. The addition of a black binder will make features much crisper and colours richer.
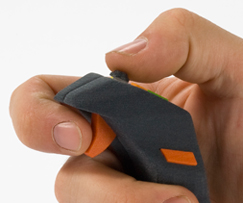
With a new black binder, features are more crisp and colours richer
System integration
If there’s been a criticism levelled at the Z Corp machines since they came onto the market, it’s that they could be a little messy in those early days. After all, shovelling white plaster or, as was the case back then, starch, into a machine, then digging a model out of it a couple of hours later, was always going to be a messy business. With the ZPrinter 450 Z Corp addressed this by introducing powder cartridges that make loading the machine much easier as they simply click into place. There is also a chamber to the right of the build area where users can safely de-powder the models from the build chamber, use an air hose to blow off additional powder and carry out post-build infiltration (models require an infiltrant be painted over them to make them more sturdy).
Conclusion
There’s currently a transition happening in the Rapid Prototyping sector. Many vendors are looking to shift their businesses from simply providing prototypes to providing end-use components and rightly so. Personally, I’m not convinced that the demand is as big as many are expecting but there is huge potential there.
While the transition to rapid or direct manufacturing is going on, there’s also a huge re-emergence of pure rapid prototyping and some serious advances are going on for those looking to build prototypes for use in the design process. One of the leaders in that field is
Z Corporation, who, alongside players like Objet, has consistently shown that there is room for innovation in a market that some RP vendors seem to be abandoning.
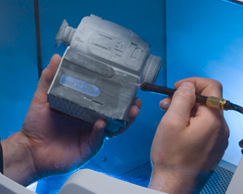
The ZPrinter 650 includes an integrated clean up and finishing station, which automatically recycles unused powder
Z Corp has been refreshing its product line since the introduction of the Spectrum 510 a few years back, and the 450 saw the entry colour models bring greater office friendliness with an integrated finishing station. This has now been followed up very nicely indeed with the 650. The bigger build chamber brings the ability to create a much larger model and this is going to appeal to a number of industry sectors – even if simply to remove the hassle of joining separate builds to create large models. But alongside the ability to create bigger parts, the expanded build chamber gives the user the ability to build larger numbers of prototypes in one go and this is key.
During those initial stages of design, particularly for consumer electronics, the ability to prototype a large number of design variants, for evaluation, test and research, can enable greater experimentation and help achieve a better end product.
The improvements in colour capability, along with the addition of a black binder, mean that parts are more consistent across different models (because the system isn’t mixing black) and should also give more accurate results in terms of colour matching.
We tested out the 650 with a standard SolidWorks dataset and one from Inventor and the results were highly impressive, with sharp details and vibrant colours. Even when working with scaled down parts or scaled up parts, the ability to see, to inspect and yes, to hold a product, while it’s still in a ‘digital non-realised’ form, is incredibly powerful and a real benefit to the design process.
Zprinter 650 Tech Specs
Machine dimensions (W x D x H) 188 x 74 x 145cm
Machine weight: 340kg
Build envelope: 254 x 381 x 203mm
Layer thickness: 0.089-0.102 mm (user selectable)
Build resolution: 600 x 540dpi
Build Speed: 2-4 layers per minute
{encode=”http://www.zcorp.com/en/home.aspx” title=”www.zcorp.com”}
From Solidworks model to full colour Prototype
The original CAD data is created within SolidWorks and then output to VRML (.wrl) file.
This is then read into Z Corp’s Zprint application, which provides users with a range of tools to set-up a build job.
As you can see the colours don’t match. This, we discovered, is down to a problem with SolidWorks’ VRML output that relates to whether appearances are assigned at the part or assembly level.
Assign it at an assembly level and the model looks right, but the VRML output references any colour or material assignments from the part level and overrides the assembly colour schemes.
We asked SolidWorks to explain this but we have yet to hear back. In the meantime, we had some suggestions from readers.
CADjunkie explained that “we need to apply colours only to Face in Solidworks. Painstaking, but ensures that the VRML captures the correct colours.”
Sotopia Concepts shared our pain and has the same problems when printing scale architectural models. They export the file in .stl and add the colours in the Zcorp printing software.
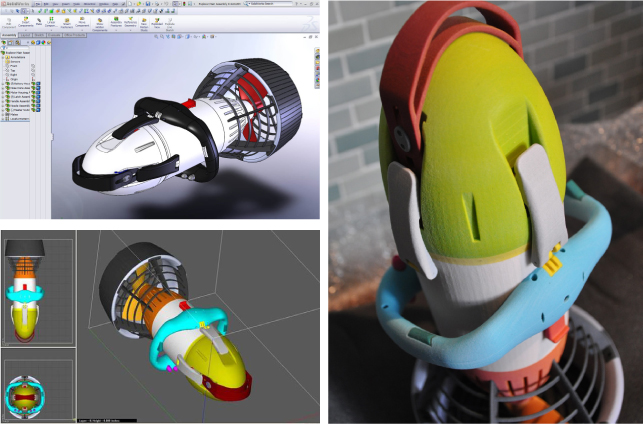
Product | ZPrinter 650 |
---|---|
Company name | Z Corporation |
Price | On application |