The Commonwealth Games’ baton is currently on its 190,000km, 288 day journey around the 70 nations of the Commonwealth before its arrival in Glasgow on 23 July 2014 for the opening ceremony of the Games.
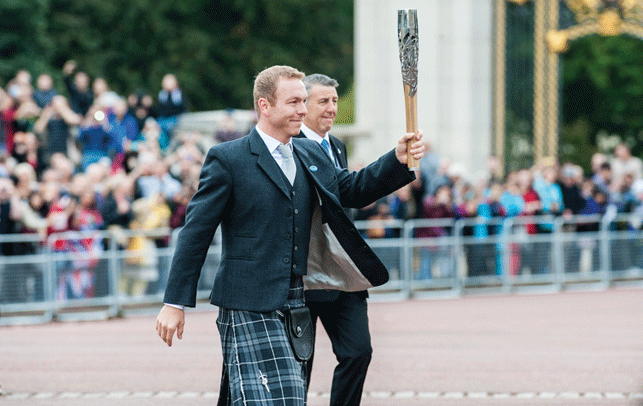
Scottish Olympian Chris Hoy carrying the baton at the launch of the Queen’s Baton Relay at Buckingham Palace on 9 October, 2013
However, getting the baton to Buckingham Palace for the launch of the relay on 9th October was no mean feat for Glasgow-based design engineering consultancy 4c Design, tasked with the design, development and manufacture of the baton in a very tight time frame.
The Games, which take place every four years, have since 1958 featured the Queen’s Baton Relay.
The Queen writes a message which is then placed inside the baton before it goes on its worldwide journey acting as a symbolic invitation to Commonwealth nations and territories to attend the Games.
The Queen will then remove the message from the baton at the Games’ opening ceremony and read it out.
4c, which won the tender set out by Glasgow 2014, the Commonwealth Games’ organising committee, knew it had to pull out all the stops especially as its client was essentially the Queen.
William Mitchell, 4c’s design director, led the project, and started out with brainstorming sessions with the design and engineering team looking at how they could unite the three aspects of Glaswegian culture, the Queen’s message and sport in one design.
Traditionally the Queen’s message has been rolled up inside the baton however, in recent models, the message has been housed electronically. 4c wanted to bring it back to its roots.
“We wanted to make the message reassuringly visible but also have this mystery and intrigue in that it shouldn’t be readable.
“We were brainstorming and playing around with different ideas in the office when we came up with the idea of the scrolled message lit up inside a latticework structure,” explains Robin Smith, 4c’s managing director, who, like Mitchell, graduated from the Glasgow School of Art but he has a mechanical engineering qualification as opposed to Mitchell’s product design degree.
Searching for inspiration
This latticework idea was inspired by a number of different objects including the ship building cranes on the River Clyde, the elegant silver filigree work by renowned Scottish designer and architect, Charles Rennie Mackintosh, and the Stevenson lighthouses, which were built by the Scottish civil engineer Robert Stevenson in the early 1800s.
“I particularly liked the lighthouse analogy – if you’re a ship and see a lighthouse beaming out in the distance, it guides you to safety,” says Smith.
Their concept featured a top half made of a double-layered titanium latticework frame with the Queen’s message held in a transparent cylinder within the inner layer, and a bottom half hand crafted from local Elm wood.
Having researched a number of different processes to produce the lattice, 4c chose the cutting edge technique of direct metal laser sintering (DMLS) offered by 3T RPD, a provider of additive manufacturing services in Berkshire.
Pattern maker
In the creation of the latticework, the designers used a computational form finding technique using Rhino and Grasshopper, a graphical algorithm editor within Rhino.
“We set out with a series of logic blocks and mathematical sums that form find – almost like it placed these parts but within the constraints of the overall geometry that we wanted. We ran it and the first view that came out, we all thought looked pretty amazing.
“We generated a few more iterations and then tweaked the one we liked manually using surfacing by eye to get it just right. We also added in the cross webs that connect the inner and outer lattice, which gives the whole thing its structure and strength,” describes Smith.
Touch wood
In complete contrast, the wooden handle was constructed without a computer in sight. The GalGael Trust, a Glaswegian social enterprise, used a reclaimed tree from a local Glaswegian park utilising a technique called bird-mouthing, traditionally used to make masts for ships, to construct the hollow handle.
However, Glasgow 2014 had some reservations about a wooden handle. Would it be strong enough? How would it wear having thousands of hands on it? Would it stay clean?
4c came up with an ingenious way of testing just how the wood would wear. Three months before the delivery date of the final design, they replaced its office door handle with a handle made from a sample of the finished Elm handle.
“We did a quick poll and reckoned that our door gets opened 200 times a day, even the postman was one of our testers.
We have some pretty dirty hands coming in the office and in our eyes the handle was still looking great three months down the line,” says Smith.
The bayonet-style connection between the top and bottom halves was a challenging part of the design that took many hours to perfect. Having modelled this joint in CAD, a 3D print of both halves was made for testing. However, although the laser sintered lattice part could be millimetre tolerant, such tight tolerances couldn’t be guaranteed in a wooden handle that was constructed by hand.
“It’s a wrap around a 3D profile and so we couldn’t even supply a 2D drawing to GalGael to explain it. Instead we supplied them with a plastic 3D print of that connection part. They then used it as a jig,” explains Smith. “They could then manually chisel out little slivers and then marry them up with the 3D print slotting it together.”
The reason why 4c had to manage the project at such a level is because it had just five weeks to deliver the final product and all sections of the design were being worked on concurrently. In order to keep track of the controlling geometry, 4c’s production engineer utilised PDMWorks within SolidWorks to ensure that the links between files were accurate and reliable.
Puzzle over
The section of the design that did involve quite a lot of engineering was the puzzle mechanism at the top that releases a gemstone, which is then gifted to each of the Commonwealth nations the baton visits.
These gemstones are made of water-resistant granite sourced from Ailsa Craig and crafted by Kays of Scotland, makers of curling stones. Jewellers at Glasgow School of Art then embellished each of the 70 gemstones.
“Being mechanical engineers we enjoy beautiful mechanisms and that’s why our little indulgence on this project was the puzzle mechanism. We wanted to create an element of intrigue and a little bit of mechanical theatre,” says Smith.
Having researched various puzzle box designs, including some interesting Japanese ones, they took the principles behind a 2D sliding mechanism and converted it into a 3D rotary type actuation.
By twisting the top bezel one way, the four jaws are released in a linear movement and the gem is unlocked.
“We were looking for a spring damper that could lift the gemstone out of this mechanism. Having experimented with a few springs that boinged it out a bit like a jack in the box, I brought in a couple of IKEA soft close hinges I had left over from having redone my kitchen. I placed it inside the design, and it worked perfectly, lifting out the gemstone slowly before coming to a stop, in a very regal fashion.
“We figured that IKEA do a million cycle tests so why reinvent the wheel when somebody has spent forever engineering it. Although we have had to replace the hinge’s piston with a stainless steel one due to the baton being exposed to the elements.”
Growing the design
The most nerve wracking part of the whole project according to Smith was once 4c had sent the CAD files of the latticework to 3T RPD and waited with bated breath while it ‘grew’ over the weekend. It took 30 hours to build this part, which involves a laser fusing 4,000 layers of fine titanium powder together.
With all the elements together, the 4c team then had to assemble and finish the design. According to Smith it took about seven man days to achieve the high polish they were after. But that is just a fraction of the 4,000 hours that he reckons was spent on this project in total.
But all this hard work was worth it when the baton was launched to such high praise, especially from Alex Salmond, First Minister for Scotland, who said: “I think it’s an absolutely brilliant design, particularly the use of Ailsa Craig granite.
Congratulations to 4c and all those involved in producing such a wonderful work of art that will leave a permanent legacy of friendship between Scotland and the rest of the Commonwealth.”
4cdesign.co.uk | glasgow2014.com
The design and manufacture of the Queen’s Baton for the 2014 Commonwealth Games
Default