What does it take to squeeze a left-hand heating, ventilation and air conditioning (HVAC) unit into the right-hand interior of a US-manufactured Chevrolet or GMC truck? The people to ask are the team at New Zealand-based product development company 3D Hub, because they recently solved this puzzle themselves, using a clever combination of reverse engineering, 3D scanning and printing and CAD modelling.
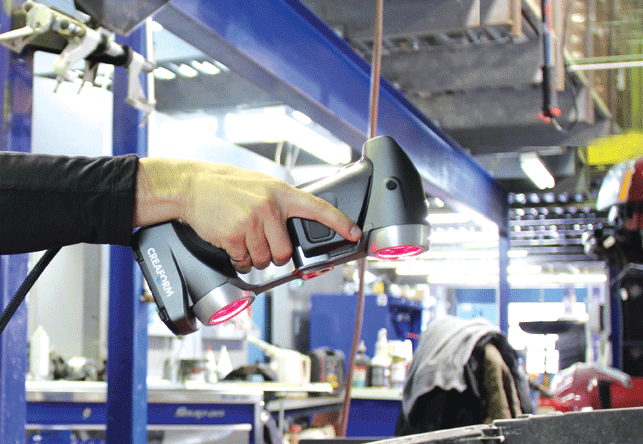
The HandySCAN 3D handheld scanner from Creaform in action
Adapting American vehicles for right-hand-side drivers is no easy feat. The main challenge in this project was its reverse engineering aspect: the team wanted to develop a right-hand HVAC unit by acquiring the 3D measurements of the existing left-hand components and integrating them within a CAD environment, so that the designs could be converted using the company’s 3D printing capability.
But it wasn’t just a simple left-to-right conversion. There was also a question of a dimensions to contend with, as Craig Russell, director and mechanical engineer at 3D Hub explains:
“All the complex functionalities had to fit into a right-hand space that was smaller than the original left-hand HVAC unit. Moreover, the reusable components, such as fans, sensors, servo motors, airflow flaps and so on had to be integrated in the CAD design.”
Then there was the fact that the HVAC unit was just one of a number of components that needed to be converted in the switch from left to right. Others included the dashboard, the steering column and the electrics.
Piece by piece
The first step was to disassemble the truck. The original dashboard was cut into critical sections (the glove box, the centre console and so on) and moved to their new positions with a right-hand-side alignment. These sections were mounted onto the dashboard support bar, removed as one from the vehicle, before being rejoined, hand-shaped and formed to create the final dashboard. From this final shape, a plug was made to create future fibreglass dashboards.
Meanwhile, the steering wheel and column were removed and repositioned to fit on the opposite side of the engine bay.
With the dash removed, the original HVAC unit could finally be removed and the firewall easily accessed for 3D scanning, using a hand-held, HandySCAN 3D scanner from
Creaform.
First, positioning targets (datum targets) were applied to the firewall surface. These would not be removed before the end of the project, because the 3D Hub team realised that they would be useful later for precise positioning and alignment work.
With the HVAC removed, it was finally ready for reverse engineering. The 3D Hub team began by 3D scanning the HVAC and the resulting data was used to lay out the new HVAC with its major components.
The recirculation unit was positioned in the vehicle to verify fit and final placement. Once it was in the final position, it was scanned relative to the original positioning targets on the firewall.
This data was then brought into the CAD environment in exactly the same place; no alignment was necessary, thanks to the retained positioning targets – a handy piece of forethought that significantly reduced processing time.
Once the reformed dashboard was completed and positioned in the vehicle, 3D scanning enabled operators to inspect the underside of the dashboard with the electronics and ducting in place. Again, the scanned data was aligned to the original target location on the firewall.
The HVAC unit could then be checked, in order to verify that it sat clear of critical components such as the dash bar and the glove box.
Time to print
The converted HVAC unit was now ready to be 3D printed in SLS nylon. The prototype was mounted and tested in the vehicle and, due to the accurate scanning data, only minor adjustments needed to be made before a final product could be manufactured, one that performed to the same high standards as the original manufacturer’s unit.
This reverse engineering project could have been carried out using 3D scanning technologies other than the HandySCAN 3D – but the team at 3D Hub believe this would have involved longer preparation times. The HandySCAN 3D’s flexibility, auto-positioning and fast, accurate localisation of the HVAC unit that the positioning targets enabled made it the best option for this project.
“The ability to scan anywhere, move the parts during the scanning process and split the job up over periods of time was what made us choose the HandySCAN 3D,” Russell explains.
“Scanning is now an integrated part of our design development process. This particular reverse engineering project and the outcome for the customer led to a referral to another company doing similar work in Australia.”
3dhub.co.nz
creaform3d.com
A complex HVAC conversion made simple with Creaform’s HandySCAN 3D handheld scanner
Default