When PTC unveiled its Digital Twin concept at the LiveWorx event in Boston earlier this year, it was the first time that the company had demonstrated a clear link between its new Internet of Things (IoT) line of business and its existing design package, Creo.
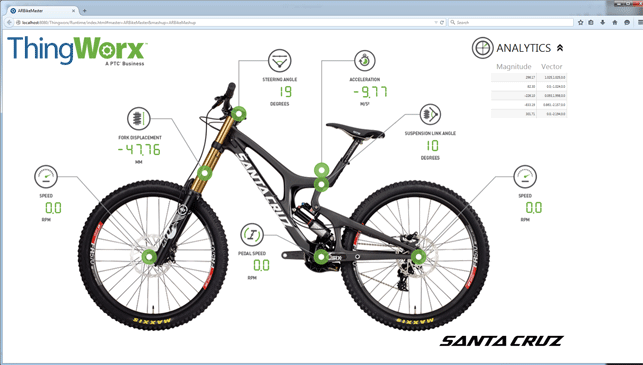
The Thingworx dashboard that shows the output from the sensors on the bike as it is ridden
The demonstration showed how a Santa Cruz mountain bike could be rigged with sensors that feed directly into a web-based interface, enabling the performance of the bike to be monitored in real time.
Then, taking things a step further, the information was streamed directly into a Creo model of the same bike. As the bike was ridden and its constituent parts moved, so did those on the ‘digital twin’ version on screen.
This got attendees’ minds racing, and one of the first things they wanted to know was, of course, “How much did that cost?”
The answer, provided by Brian Thompson, senior vice president of PTC Creo product management and part of the team that created the demonstration, came as a surprise to many in the audience.
“The total cost was $216 – at single unit volume prices and not exactly directly from the manufacturer. This, of course, doesn’t include duct tape or labour. We also 3D-printed some parts to make it easier to attach some of the tech to the bike,” he said.
The build process
There were three main steps involved in the development of this prototype. The first step was to rig up the bike with the components. Much of the hardware involved is widely available. Connecting it up, meanwhile, was pretty much a case of following the correct wiring diagrams, combined with a bit of background knowledge.
The second step was to create the communication links between these components and PTC’s Thingworx IoT platform. The data generated is pretty lightweight – just a small number of real values. The delay in the total communication loop was in the order of 0.5 seconds.
According to PTC, setting up these communication links took less than a day (not surprising considering the team’s knowledge of Thingworx).
The third step was to connect the Thingworx input into a dashboard-style interface. This took a couple of days to create and gives the user a real-time view of the data stream from the sensors, in the form of meaningful information on the bike’s performance.
For example, rather than displaying pure measurement data captured from the steering axis, users instead get more useful, real-time information on steering angles.
While this was one part of the demonstration, the next part showed how the same information could be linked directly to a model of the bike inside PTC’s Creo 3D design system.
Democratising telemetry
For now, this is just a demonstration –but it’s pretty clear that PTC’s plan is to productise this work and get it into the hands of customers. In order to do so, the company will need to work on integration, so that it becomes far easier for customers to create the links that transfer data between the sensors and the software.
As Thompson commented, “The [integration] between the PTC Creo simulation and Thingworx is new technology. We built some custom code to enable that, so it’s not possible [right now] for a customer to duplicate what we did with Thingworx, the sensors and the bike. Of course, we are working on making such connections possible for all of our customers.”
In time, he added, customers might be able to create such data links in a matter of minutes.
With its IoT focus, PTC clearly hopes to find new sales opportunities for its software products, among both new and existing customers. Many of the pitches for IoT in the manufacturing sector tend to focus on the use of sensors to measure a product’s performance in the field, to predict when it might need servicing, for example, or is experiencing some
Product design opportunities
For product developers, the ability to gain real-world insight into how a planned product might perform, long before it hits the market, could be invaluable.
Historically, this type of information has been difficult to capture at a reasonable cost and just as difficult to turn into meaningful insights that might usefully inform the design process.
In Formula 1 racing, engineering teams already place great stock in on-board and real-time telemetry that allows them to assess vehicle performance during tests and races – but relatively few organisations have at their disposal the budgets necessary for that kind of analysis.
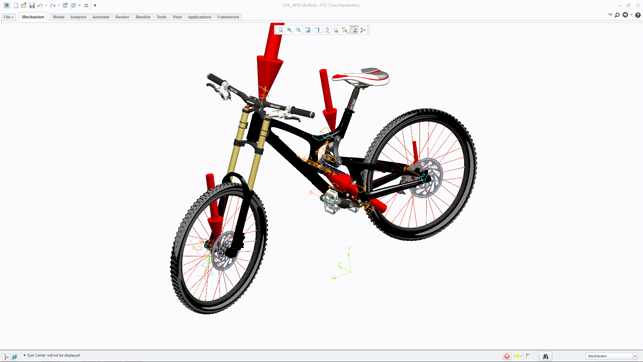
The Digital Twin. Connected to the real-world product via Thingworx, this Creo model updates to show how a product is performing
What this technology demonstration from PTC shows is that the combination of consumer electronics and the ‘maker scene’ that is springing up around open-source hardware is opening up IoT opportunities to a far wider audience. (In the PTC demonstration, for example, the Adafruit and Raspberry Pi technologies are all examples of open-source hardware. As of February this year, around five million Raspberry Pi units had been sold since the product was launched back in 2012).
The use of PTC’s Thingworx software is also interesting from a cost perspective. A software package like this is typically geared up for large-scale use and priced on a per-sensor basis. That suggests that users who are working on small-scale projects invollving fewer sensors may be able to take advantage of that pricing structure to keep costs low.
By contrast, the integrations that PTC is promising between Thingworx and Creo are unlikely to prove quite so inexpensive. On the other hand, there will be real value here for users, since these will save them the hassle of hard-coding integrations from scratch.
This kind of manual intervention can be time-consuming and typically requires coding expertise that isn’t necessarily part of the average design and engineering team’s skillset.
Instead, PTC executives are talking about offering a much more ‘plug-and-play’ approach, using packaged integrations that help customers get their own digital twins up and running in a matter of hours.
What’s not yet clear is how and when the digital twin concept will eventually be rolled out. The next year or so should provide some clues and there’s a good chance that further announcements will accompany the Creo 4 release, which is still some way out.
In summary, there’s huge potential for this kind of technology in the product design process. Imagine, for example, being able to rig up a prototype, gain real-world loading conditions and feed that back into simulation in order to perform fatigue analysis.
The good news is that this is now close to becoming an accessible reality for the many, rather than the few.
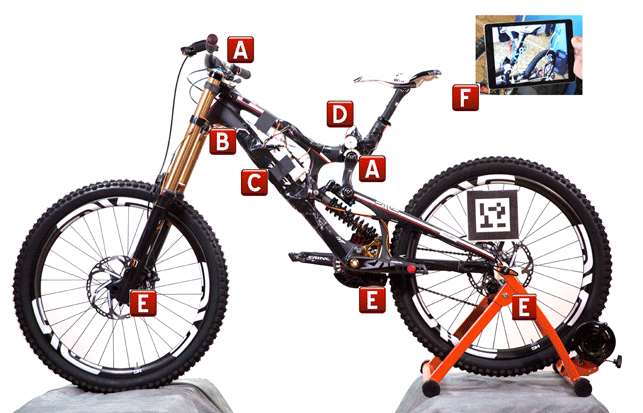
How it all works. See details below
A: Angle Sensor
An angle sensor is used to monitor steering angle as well as the movement of the rear suspension arrangement
B: Displacement Sensor
Displacement sensors are used in combination with the already-known K-factor of the forks to give reaction forces at the front shocks
C: Board + Power + WIFI
Powered by a portable battery, the whole rig is controlled by a Raspberry Pi 2, connected to the various sensors using a Pi-to-Arduino bridging component
D: Accelerometer
An accelerometer is fitted to a 3D-printed rig to assist with measuring the force placed on the seat of the bicycle, detecting movement changes in all directions
E: Speed sensor
Speed is monitored at the two axles as well as the crank axle to detect wheel and pedal rotations
F: AR target
A universal AR target is added to the bicycle to enable the iPad app to track the viewer’s position in relation to the bike and allow the overlaying of real-time sensor results
Digital Twin parts list:: $260 to build the same rig
Raspberryt PI 2
Supplier:: Rasberry Pi distributors
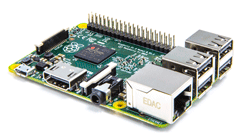
Use: A small computer the size of a tin of mints (albeit with less power than many are used to these days), the Raspberry Pi has changed the game for DIY computing.
In the PTC demo, it handles the comms between the sensors and streams the data to the web.
Quantity: 1
Price: $43
ADAFRUIT 10-DOF IMU BREAKOUT – L3GD20H + LSM303 + BMP180
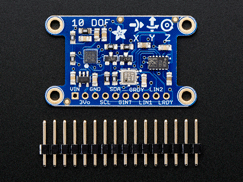
Supplier: Adafruit
Use: This inertial measurement unit (IMU) can give users all manner of data but in PTC’s case, it’s used to measure the vertical acceleration feed to scale/factor the loads. Static – at 1g – the occupant’s weight is known based on suspension reactions.
Quantity: 1
Price: $29.95
USB battery pack for Raspberry PI – 10000MAH – 2 x 5V
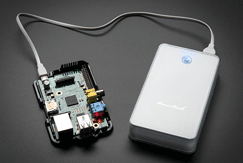
Supplier: Adafruit
Use: These are pretty bog standard USB charging devices, used to keep the whole system running and there’s more than a few options available in terms of size, capacity and power.
Quantity: 1
Price: $49.95
Sainsmart HC-SR04 Ranging Detector MOD Distance Sensor

Supplier: Sainsmart
Use: This is an ultrasonic sensor that measures distance by waves reflecting from a plate placed on top of the front wheel.
Quantity: 1
Price: $12
Arduberry for Raspberry PI
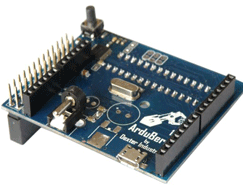
Supplier: Arduberry
Use: The Arduberry provides a hardware interface between the Raspberry Pi platform and the wealth of add-on modules available for the Arduino platform.
It’s pretty much plug and play.
Quantity: 1
Price: $25
Wire jumper and wiring
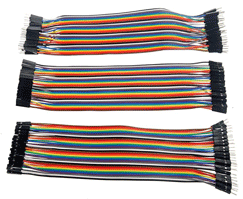
Supplier: Available from Amazon
Use: Of course, with all of the sensors placed all over the bike, they’ll need to be connected to the communications and computation devices.
Pre-cut packs of wires and reels are pretty commonplace and readily available.
Quantity: 2
Price: $31 each
Reflective IR sensor with 470 and 10K resistors
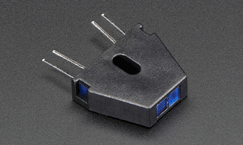
Supplier: Adafruit
Use: Reflective strips are placed on the bike’s rotating sprockets and this sensor triggers a signal every time a reflective strip passes it, forming a kind of encoder so that the rotation speed of the wheels and the pedals can be detected.
Quantity: 3
Price: $1.95 each
10K OHM 3 pins 6mm split shaft rotary potentiometers
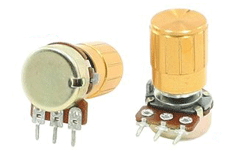
Supplier: Available from Amazon
Use:This is a potentiometer mounted in a way that the bottom is fixed to the frame, and the knob is fixed to the rotating part (fork in the front, and top suspensions link in the rear). That tells the angle of the moving part relatively to the frame.
Quantity: 2
Price: $8.60 (for 10)
Real-time Santa Cruz bike performance monitoring with PTC’s Digital Twin concept
Default