Robotics company Wheel.Me hopes to transform how goods, equipment and objects are moved across factory floors. Stephen Holmes takes a look at the company’s latest product, the Genius 2, and learns what keeps its iterative design process rolling forward
Material handling is a big part of the activity on any factory floor. At facilities without conveyor lines, gantry systems or high-cost automated trolley set-ups, much of this movement must be carried out by (human) hand. That can be time-consuming, resource-intensive and risky for health and safety. And even forklifts and pickers require experienced operators and regular maintenance.
Norwegian robotics company Wheel.Me wants to solve these industry challenges and change the status quo of manufacturing. In 2018, it introduced Genius, the world’s first autonomous wheel. An updated version, Genius 2, has just hit the market.
With Genius, you can add wheels to just about anything, transforming that object into an autonomous mobile robot. The product combines robotic components, indoor navigation technology and data analytics, but also simplicity, since companies can add wheels to whatever they already have, such as racks, trolleys and carts. With Wheel.Me, these can run between points autonomously and without the need to make expensive infrastructure changes.
The market has responded with excitement, boosting Wheel.Me’s growth. In the last two years, the company has grown its employee base by more than 400% and opened offices in four cities across Europe and North America. Its internal departments – from production lines to customer support – have needed to scramble to keep pace.
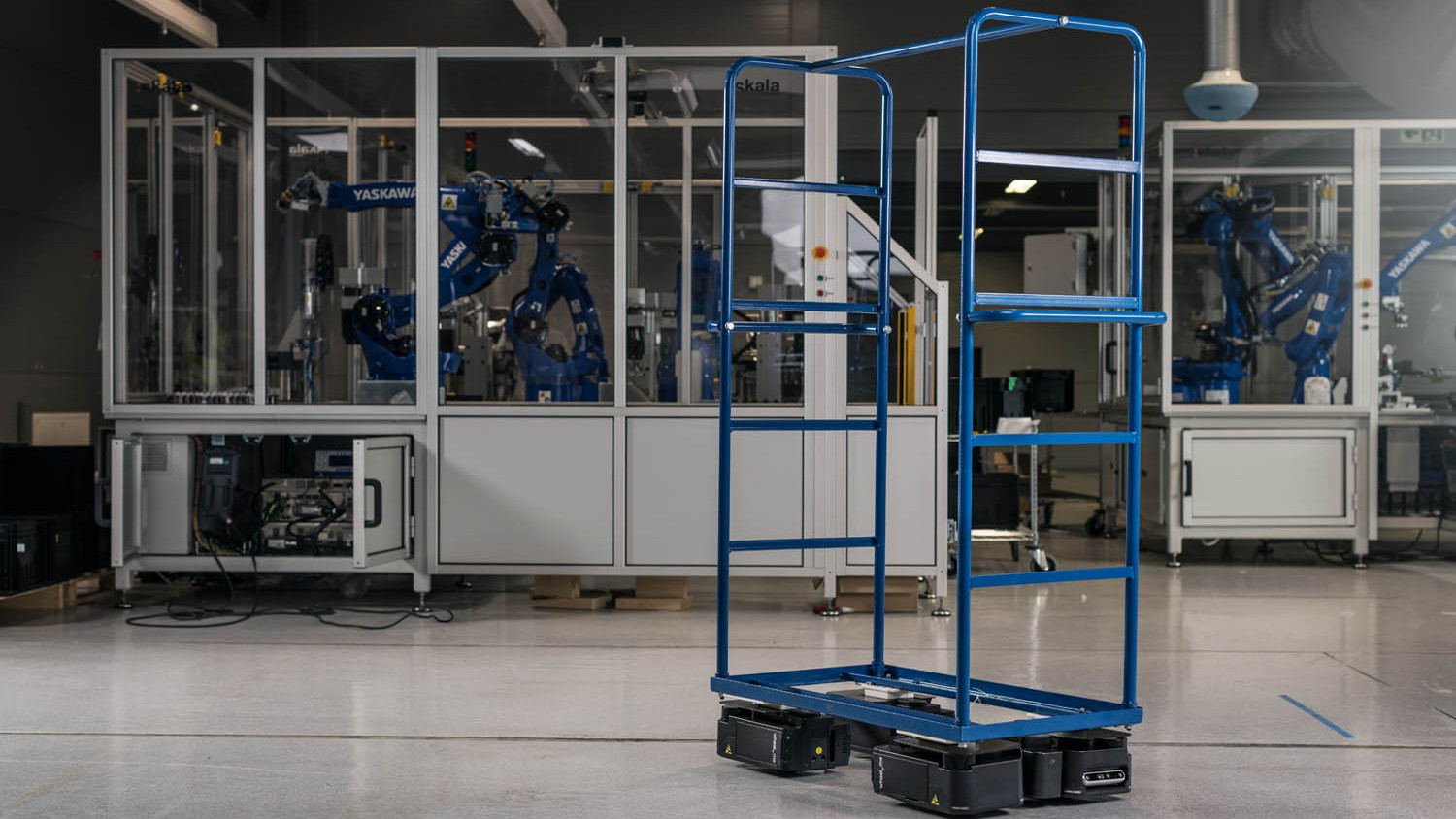
Wheel.Me // Choosing direction
In its early stages, a key challenge for Wheel.Me was to define its product and identify what would be needed to build the hardware. It was a process of trial, error and iteration, all conducted while moving at start-up pace to get the first product to market.
A change of camera, sensor or chip could mean the beginning of a whole new testing cycle, and involve the design team working around the clock to make the new part fit.
Much of Wheel.Me’s innovative, custom-built hardware was defined by customer feedback. As Wheel.Me head of mechanical engineering, Casper Rødsrud, puts it: “Mechatronics is not just mechanics. It’s not just robotics. It is the intersection of everything. So I think the biggest challenge was to properly understand the requirements for the product.”
Some of that comes down to the environment in which the product will work. Here, it needs to be incredibly versatile, which adds to the complexity of designing it. Some factories are modern and spacious, with smooth floors almost like clean rooms. Others have been in operation for centuries, with cracked floors and other idiosyncrasies. Traffic flow is also an issue, depending on the number of forklifts and telehandlers moving from station to station.
Much of the Genius 2’s agility is enabled by its Mecanum wheel design – an independent, non-steering drive wheel with its own powertrain – which creates an omnidirectional platform so that a load can be manoeuvred precisely in tight spaces.
“In the beginning, it was a fully manual wheel,” explains Rødsrud. “It clicked in and clicked out, like a ballpoint pen. You lift a piece of furniture, and the wheel is out. You lift it again and the wheel is back in.” The team continued to experiment with new concepts: motorised wheels, self-stabilising wheels, and then finally, autonomous wheels.
While solving lots of problems, the Mecanum wheel also created new challenges for the design team. It needed angled external rollers for grip, for example, and axles that provided the right fit. Other issues for the design team to address included load weight, managing traction and powering the wheel while maintaining a small form factor.
Wheel.Me // Internal design
The majority of components are custom-built, and all designed in-house, even the Mecanum wheel with its integrated BLDC motor. “We’ve had assistance when designing these things,” explains Rødsrud. “We’ve talked to motor manufacturers, talked to gear manufacturers, and worked with real professionals. But, right now, we have created mass production tools for almost every single part that we have. So we have got to a point where it’s not that big of a headache anymore, but it for sure used to be!”
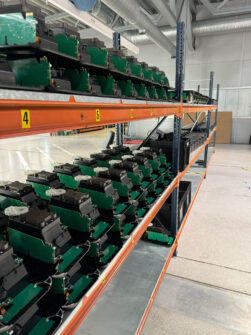
Getting to that point took a lot of time and effort, he says, but it was beneficial to have created most of the parts from scratch, as it offers the development team the control it needs to ensure that everything works in synergy.
“It’s an interesting question to ask yourself whether it would have taken less time if we actually had used a lot more off-the-shelf components. But on the other hand, it’s quite cool to sit here and say that everything you see in this product is designed in-house.”
Developing the 3D CAD model came with its own challenges, as the company found itself switching mid-stream between software packages. At first, it used Autodesk Fusion 360, then switched to Solidworks, before finally taking up the Siemens Mechanical Design package along with Teamcenter.
The need for larger complex assemblies and better collaboration between its mechanical design and electrical design teams saw it sometimes hampered by incompatible software. According to Rødsrud, “We realised that we needed more than just bits and pieces from different software suppliers, but better integrated solutions and somewhere where we could get the full picture.”
Solid Edge is predominantly used, with the package’s access to NX a distinct advantage. “It’s the flexibility that is key,” explains Rødsrud, “and knowing that we can do concept designs in Solid Edge, then move to NX during in-depth design was important for an agile team.”
According to the head mechanical engineer, the team especially appreciated the adaptability of the synchronous environment in Siemens, and the ability it gave the team to edit parts in assemblies. “It’s one of the things that I really think is super cool!”
The ability to work with multibody parts, and the capabilities in the product to do thermal analysis and structural simulations were also key advantages of the Siemens solution.
“Once we landed on the whole Siemens package, it also allowed us to implement a PLM system, Teamcenter, which allows us to do very, very thorough version control,” continues Rødsrud.
“So right now, we’re building up workflows for both release and change management. All these processes are very focused at the moment, just to make sure that we know what changes we are making to the product, and why. And we also know how long they will take and how they will affect every other part.”
The biggest advantage with Teamcenter is its control over releasing datasets. “We can release one version to production, and then we can continue to work in parallel on the next iteration, where we can take into account some of the feedback that we’ve gotten along the way. And then we can schedule the next release for the physical product,” says Rødsrud.
Agile movement
Iteration has been key to the development of Genius 2. “You obviously have a lot of loops and a lot of iterations back and forth, up and down,” explains Rødsrud. “No development process is linear. Everything is agile.”
Rødsrud says that a lot of this comes down to taking the design off the screen and building physical prototypes.
“Building a physical product is never easy, because you realise a lot when you first have it in your hands. It’s not necessarily that easy to see all of the challenges and things you need to fix when you have it in your CAD programme or simulations or whatever. You really need to get it out as a prototype.”
The team has wheels rolling every single day, with in-house prototypes, beta models in the field and previous generation Genius robots being monitored by Wheel.Me’s deployment teams, who work closely with customers and get their feedback. This provides the development team with valuable information that must be swiftly analysed and then adopted into the new design.
“And sometimes, there are some hiccups, and we use those hiccups to also learn more about the product and what we need to improve,” says Rødsrud.
With an on-site machine shop at its disposal, the design and engineering team also runs a print farm in-house that is stacked with Bambu Labs X1E FDM 3D printers.
Additionally, the team has also just acquired a Formlabs Fuse SLS 3D printer. Hopefully, the company got a hefty discount on this machine, Rødsrud jokes, since Wheel.Me CEO Stefan Hollaender is a former EMEA managing director of Formlabs.
“That one is great,” says Rødsrud, praising the Fuse. “It allows us to create very detailed prototypes as well, so that we can actually test the interfaces and functions of things that we want to test. Instead of relying on simulations and calculations, we need to move fast. So instead we would rather make prototypes and test them in real life.”
A proficient in-house prototyping set-up means the team can build test rigs and jigs for the Genius 2, testing elements like material properties, robot loads and wheel endurance, right through to an end-of-line jig, which runs lots of tests consecutively on an end product to ensure everything works before it gets shipped to the customer.
The last 12 months at Wheel.Me have been about getting the Genius 2 into production. That’s seen the development team move away from prototyping methods and low-volume test units and embrace high-volume production. This means shifting from machined parts for the suspension system to casted parts and cutting injection moulding tools for all of the product’s plastic parts.
Wheel.Me’s factory and assembly plant is located just over an hour’s drive away from its headquarters in Oslo. The engineering team visits the plant at least once a week, helping its members see immediately what is working and what needs more work. Rødsrud adds that these visits help them get the perspective of the operators and build teams on how the robot could be designed better for easier assembly. This goes as far as inspiring new ideas for simple 3D-printed jigs and fixtures that may assist with the complex business of manufacturing, while also costing relatively little to produce.
The communication flow between the engineering and factory teams is great, he says, adding that any faulty parts are immediately flagged up to the designers, helping maintain the highest quality assurance.
Close control
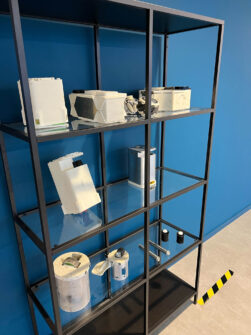
With overarching control of their product – from design through to engineering, software, prototyping, manufacture and assembly – this closed loop has helped Wheel.Me build a super-honed end product.
The complexity of maintaining this control may have added to its workload, but the team is adamant that agility is still the key driver in its process. “For us, it’s key to be quick as well,” says Rødsrud. “Because if we spent too long dwelling on one challenge, we would maybe lose our spot in the market and be overtaken by someone else. We need to be quick, we need to get our products out there and also be ready to do quick iterations when we get the proper feedback from the market.”
He predicts that the growth that the company is currently experiencing isn’t likely to let up soon, so scalability of both processes and infrastructure are critical. “The demand is just going to continue to blow up,” he says. “We have people knocking on our doors. They want wheels and they want to install wheels everywhere, on everything.”
The ability of the Genius 2 to move swiftly and manoeuvre with precision, no matter the load, is something reflected in the development team at Wheel.Me as it strives to progress manufacturing, one wheel at a time.
This article first appeared in DEVELOP3D Magazine
DEVELOP3D is a publication dedicated to product design + development, from concept to manufacture and the technologies behind it all.
To receive the physical publication or digital issue free, as well as exclusive news and offers, subscribe to DEVELOP3D Magazine here